Intelligente, digitale Restblecherfassung
Die Erfassung und Verwaltung von Restblechen findet heute überwiegend manuell, ohne geeignete Systemunterstützung statt. Weiterentwickelte Anlagen zur Blechverarbeitung oder ganzheitliche Softwarelösungen bieten integrierte Lösungen zur Ausgabe und Speicherung von Restgeometrien an. Aufgrund ihrer hohen Kosten sind sie jedoch insbesondere für kleine und mittelständische Unternehmen (KMU) unattraktiv.
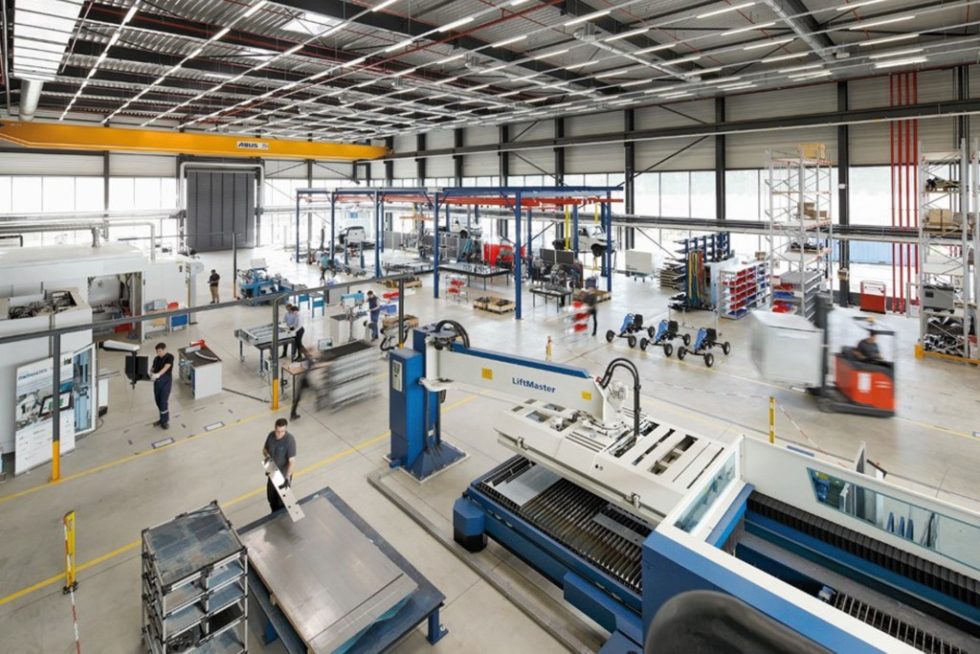
Bild 1. Die Produktionsumgebung der DFA Demonstrationsfabrik ‧Aachen bietet die Möglichkeiten, ‧Lösungen direkt in der Praxis ‧umzusetzen. Bild: WZL
Zwei in letzter Zeit entwickelte Lösungen stellen eine Alternative für die Erfassung und Wiederverwertung von Restblechen dar: Die eine verwendet eine kamerabasierte, die andere eine laserscannerbasierte Blecherfassung mit anschließender Bildverarbeitung. Die laserscannerbasierte Blecherfassung ist auf dem RWTH Aachen Campus bereits in Betrieb, Bild 1. Nachfolgend werden beide Lösungen bezüglich ihrer möglichen Anwendungsbereiche vorgestellt und ihre Einbettung in einen exemplarischen Prozess der Restblecherfassung und -verwaltung dargestellt.
Ausgangssituation
Falls Geometrien von Restblechen heute erfasst werden, geschieht dies oftmals manuell durch handschriftliche Skizzen auf Papier. Häufig wird dieser Aufwand gar nicht betrieben, sodass Restbleche entweder verschrottet oder ohne systemische Erfassung gelagert werden. Restbleche werden deshalb selten in ein Materialverwaltungssystem zurückgebucht, da diese Systeme häufig nicht die benötigten Funktionalitäten bieten. Durch die reine Eingabe einer Blechlänge und -breite können entscheidende Merkmale für die mögliche Wiederverwertung, beispielsweise Aussparungen, im System nicht abgebildet werden.
Die weitere Verwendung dieser Restbleche stellt eine Herausforderung dar, weil – bedingt durch die fehlenden Informationen im System – meist ein physischer Abgleich in der Produktionsumgebung stattfindet, ob die Restfläche eines Blechs für den nächsten Auftrag sinnvoll wiederverwertet werden kann. Häufig werden direkt neue Bleche verwendet.
Deshalb bieten einerseits neuere Laserschneid- oder Wasserstrahlschneidanlagen zur Blechverarbeitung die Möglichkeit, die Restgeometrie direkt auszugeben und sie somit direkt digital weiter zu verwerten, beispielsweise als einzulagernde Restgeometrie. Andererseits existieren bereits ganzheitliche Softwarelösungen, die den Prozess – von der Einlagerung einzelner Bleche über das Schachteln bis hin zur Blechverwaltung – abbilden. Insbesondere für KMU stellen jedoch weder die Anschaffung neuer Maschinen noch die Implementierung einer neuen Software zur Optimierung der Restblechverwaltung ein realistisches Szenario dar. Der Aufwand und die Kosten stehen häufig nicht im Verhältnis zum erwarteten Nutzenpotential.
Um dennoch eine Lösung für einen effizienteren Umgang mit Restblechen möglich zu machen, bieten zwei Lösungen eine kostengünstige Alternative. Die eine stellt eine kamerabasierte, die andere eine laserscannerbasierte Blecherfassung mit anschließender Bildverarbeitung dar. Im Weiteren werden diese beiden Lösungen detailliert vorgestellt.
Kamerabasierte Erfassung von Restblechen
Mithilfe einer Kamera wird das Restblech zunächst optisch erfasst, Bild 2.
Die Kamera wird dabei in ausreichender Höhe angebracht, sodass das gesamte Restblech im Erfassungsbereich liegt. Hierfür eignen sich beispielsweise eine Anbringung über dem Schneidtisch oder vor dem Lagerbereich. Wenn es sich um ein Lager mit Schubladen handelt, könnte beim Beladeprozess der Schublade ein Foto aufgenommen werden. Es ist darauf zu achten, dass die Kamera während der Aufnahme nicht durch Kräne oder Ähnliches verdeckt wird. Zudem sollte eine Schattenbildung weitestgehend verhindert werden, um optimale Ergebnisse erzielen zu können.
Das Kamerasignal wird über Kabel oder Funk zu einem zentralen Auswerterechner übertragen. Dort wird mithilfe der Softwarelösung von BKE Ingenieurbüro Dr. Brake die Restblechkontur ermittelt und diese im DXF-Format ausgegeben. Diese Datei kann anschließend an einen beliebigen Speicherort abgelegt oder an eine Schachtel- und Blechverwaltungssoftware übergeben werden [1].
Scannerbasierte Erfassung von Restblechen
In einem gemeinsamen Projekt zwischen dem Werkzeugmaschinenlabor (WZL) der RWTH Aachen [2], dem Center Connected Industry [3] und Sick [4] wurde ein Verfahren zur Restblecherfassung entwickelt. Ein Prototyp für die scannerbasierte Restblecherfassung steht in der DFA Demonstrationsfabrik Aachen. Dieser Prototyp lässt sich an beliebigen Stellen im Fertigungsprozess integrieren.
Er ist folgendermaßen aufgebaut, Bild 3: Von einem Bearbeitungstisch wird das zu erfassende Restblech auf eine nahestehende rollengeführte Vorrichtung bewegt.
Bild 3. Prinzipskizze der Restblecherkennung durch einen Laserscanner in der DFA Demonstrationsfabrik Aachen. Bild: WZL
Alternativ zur Bewegung des Restblechs wäre auch eine bewegliche Sensorvorrichtung über ein ruhendes Restblech möglich. Hierbei ist jedoch auf Kollisionen mit Verfahrensbewegungen der Bearbeitungsmaschine oder Kränen zu achten.
Bei ruhender Sensorvorrichtung und beweglichem Restblech passiert dieses zunächst eine Lichtschranke, welche die weiteren Sensoren aktiviert und den Erfassungsvorgang einleitet. Ein Laserscanner erfasst zeilenweise das Restblech in seiner Breite und gibt diese Daten an die Sensor Integration Machine („SIM4000“), eine zentralen Datenerfassungs- und Datenvernetzungseinheit weiter. Über einen Drehgeber an der Führungsrolle wird die Relativbewegung des Restblechs zum Zeilenscanner bestimmt, um eine korrekte Abmessung in der Restblechlänge sicherzustellen. Neben der Lichtschranke befinden sich ein induktiver Sensor und ein zweiteiliger Abstandssensor. Der induktive Sensor bestimmt das Material des Restblechs, beispielsweise Stahl oder Aluminium; der Abstandssensor erfasst die gleichbleibende Dicke des Restblechs.
Alle Daten der Sensoren werden in der leistungsfähigen SIM4000 zusammengeführt, welche die Punktwolken aus dem Laserscan und die Materialinformationen in Echtzeit auswertet. Aus der Punktewolke wird die größtmögliche rechteckige Fläche ermittelt, welche wiederverwendet werden kann. Das Abbild des Restbleches kann über geeignete Schnittstellen an das betriebseigene Materialverwaltungssystem und den Schachtelprogrammen der Bearbeitungsmaschinen weitergeleitet werden, Bild 4.
Umfangreiche Daten sind verfügbar
Neben den fertigungsrelevanten Informationen können über die SIM4000 und einem webbasierten Dashboard auch Informationen für die Arbeitsvorbereitung abgerufen werden, Bild 5.
So ist es einerseits möglich, sich die Historie der gescannten Restbleche anzeigen zu lassen. Andererseits sind Informationen zum Sensorstatus – wie Signalstärke und Betriebsdauer – oder allgemeine Kennzahlen zu erfassten und genutzten Restfläche abrufbar. Zukünftig ist besonders die Visualisierung der vergangenheitsbasierten Wiederverwendbarkeit von Restblechen bestimmter Geometrien, bestimmter Dicke und eines bestimmten Materials interessant.
Auf Basis dieser gesammelten Vergangenheitswerte sollen zukünftig Prognosen für die Wiederverwendbarkeit der Restbleche gestellt werden. So kann nach der Erfassung eines Restblechs eine Aussage darüber getroffen werden, ob die Einlagerung dieses Blechs kosten- und fertigungstechnisch sinnvoll ist, oder ob es besser umgehend verschrottet werden sollte, da die Wahrscheinlichkeit der Wiederverwendung zu gering ist.
Vergleich der Lösungen
Beide vorgestellten Verfahren eignen sich für die kostengünstige Erfassung von Restblechen, Bild 6.
Sie unterscheiden sich primär in dem Ort der Anbringung und der Art der Aufnahme. Die kamerabasierte Lösung erfordert einen möglichst großen Abstand zum Blech, damit es vollständig erfasst werden kann. Es handelt sich dabei um eine statische Aufnahme, bei dem weder das Blech noch die Kamera bewegt werden muss. Die laserscannerbasierte Lösung erfordert dagegen einen möglichst geringen Abstand zum Blech. Um dennoch das gesamt Blech erfassen zu können, muss jedoch entweder das Blech oder der Laserscanner bewegt werden.
Ausblick
In den vorgestellten Lösungen werden die Restblecherfassung und -verwaltung zunächst einzeln adressiert. Langfristig ist es das Ziel, eine Einbindung in den gesamten Prozess möglich zu machen. Der Zielzustand ist, dass nach dem Erfassen des Blechs eine Entscheidung über die Verschrottung oder Wiedereinlagerung getroffen wird.
Die in einer Datenbank hinterlegten Restbleche geben dem Anwender einen einfachen Überblick über den aktuellen Bestand inklusive der jeweiligen Geometrien. Hierdurch hat der Anwender die Möglichkeit schnell herausfinden, welches der Bleche am besten für den nächsten Auftrag geeignet ist. Damit steigt die Wiederverwertbarkeit von bereits genutztem Material und letztendlich sinkt der Bedarf an neuen Blechen. Zudem kann auf Basis der bislang wiederverwerteten Belche eine Abschätzung stattfinden, wann es sich lohnt, ein bestimmtes Material in einer bestimmten Materialdicke und -größe aufzuheben.
Beim Schachteln eines neuen Auftrags wird dann im vorhanden Lagerbestand das bestmögliche Blech ausgesucht. Ein relevantes Kriterium ist beispielsweise die Auswahl nach dem geringsten Verschnitt für eine zu schachtelnde Geometrie. Langfristig soll so der Materialverbrauch gesenkt und eine höhere Transparenz in der Blechverwaltung erreicht werden.
AutorenProf. Dr.-Ing. Dipl.-Wirt. Ing. Günther Schuh, Jahrgang 1958, ist Mitglied des Direktoriums am Werkzeugmaschinenlabor (WZL) der RWTH Aachen, des Fraunhofer-Instituts für Produktionstechnologie IPT sowie Direktor des Forschungsinstituts für Rationalisierung e. V. (FIR) an der RWTH Aachen. Dr.-Ing. Jan-Philipp Prote, Jahrgang 1986, studierte Wirtschaftsingenieurwesen mit der Fachrichtung Maschinenbau an der RWTH Aachen sowie Industrial Engineering an der Tsinghua University in Peking. Er ist Oberingenieur am WZL und leitet seit Ende 2016 die Abteilung Produktionsmanagement.Marco Molitor, M. Sc., Jahrgang 1987, studierte Wirtschaftsingenieurwesen an der Hochschule Mannheim. Er ist wissenschaftlicher Mitarbeiter am WZL und leitet seit Anfang 2018 die Gruppe Prozessmanagement in der Abteilung Produktionsmanagement.Pia Walendzik, M. Sc. RWTH, Jahrgang 1990, studierte Maschinenbau mit der Vertiefung Produktionstechnik an der RWTH Aachen. Sie ist wissenschaftliche Mitarbeiterin am WZL in der Gruppe Prozessmanagement, Abteilung Produktionsmanagement.Dipl.-Phys. Dipl.-Wirt.Phys. Christian Maasem, Jahrgang 1983, studierte Physik und BWL an der RWTH Aachen und der Université d’Orléans. Am FIR leitete er von 2015 bis 2016 die Fachgruppe Informationstechnologiemanagement sowie von 2014 bis 2016 das Smart Systems Innovation Lab. Seit 2016 ist er Leiter des Centers Connected Industry.