Konstruktion und Herstellung eines Auslegers aus Aluminiumschaum-Sandwich unter Anwendung der Fräskanttechnik
Die Fräskanttechnik stellt ein Fertigungsverfahren dar, um aus plattenförmigen Materialien räumliche Strukturen auf einfache Weise herzustellen. In diesem Beitrag werden die praxisnahe Anwendbarkeit dieser Technik für ein Aluminiumschaum-Sandwich am Beispiel der Konstruktion und Herstellung eines Trägers aufgezeigt und für dieses Bauteil Gestaltungsregeln abgeleitet.
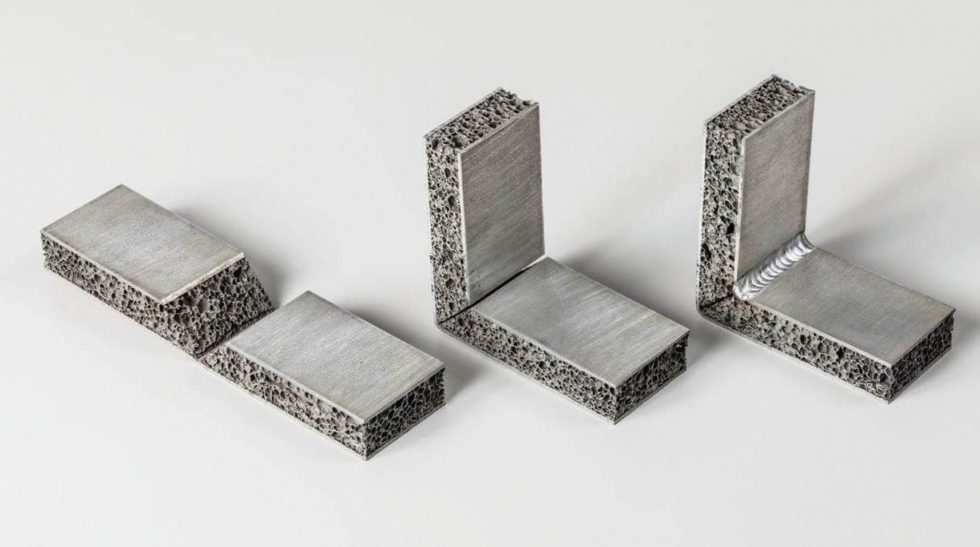
Bild 1: Dreistufiger Bearbeitungsprozess der Fräskanttechnik bei Aluminiumschaum-Sandwich (von links nach rechts: Fräsen – Umformen – Fügen, zum Beispiel durch Schweißnaht). Bild: Universität Stuttgart
1 Einleitung
Das Ziel im Maschinenbau, Produkte und Strukturen leichter zu gestalten, eröffnet den Verbundbauweisen ein breites Einsatzspektrum. Die Sandwichmaterialien stellen eine solche Bauweise mit breitem Anwendungsbereich dar. Das Sandwich besteht aus zwei Deckschichten, die durch einen zwischenliegenden Kern gestützt werden. Der Aufbau eignet sich besonders für biegebeanspruchte Bauteile, indem die Deckschichten aus festem Material die Zug- und Druckkräfte aus der Biegung aufnehmen. Der Kern, bestehend aus einem weichen Material mit möglichst geringer Dichte, nimmt die Querschubkräfte auf [1]. Neben verschiedenen Materialkombinationen hat sich das Aluminiumschaum-Sandwich (engl. AFS – Aluminium Foam Sandwich) etabliert, welches sowohl im Kern als auch in der Deckschicht aus Aluminium besteht. Der Kern ist bei diesem Verbund eine unter Hitze aufgeschäumte porenartige Struktur (Bild 1), die stoffschlüssig mit den Deckschichten verbunden ist. Neben der hohen spezifischen Biegesteifigkeit bietet AFS ebenfalls hohe Dämpfungseigenschaften, weshalb derartige Strukturen beispielsweise in crashrelevanten Bereichen im Automobilbau eingesetzt werden [2].
Das Material ist seit einigen Jahren serienreif entwickelt [3] und wird in unterschiedlichsten Branchen eingesetzt. Durch den anisotropen Aufbau bestehen die Herausforderungen bei der Konstruktion mit dieser Verbundbauweise unter anderem in der Verbindungstechnik und der Krafteinleitung. So liegt das Sandwich als Ausgangsmaterial in der Regel plattenförmig vor, sodass dieses zunächst zugeschnitten und zu fügen ist, um räumliche Strukturen zu erzeugen. An dieser Stelle bietet die am Institut für Konstruktionstechnik und Technisches Design (IKTD) sowie am Fraunhofer Institut für Produktionstechnik und Automatisierung (IPA) untersuchte Fräskanttechnik (FKT) für AFS eine innovative Fertigungstechnologie, mit der Konstruktionen mit wenigen Bearbeitungsschritten umgesetzt werden können. Bei Anwendung der FKT wird eine Nut in V- oder U-Form in das AFS gefräst, um im Nutbereich die obere Deckschicht und das Kernmaterial zu entfernen. Diese eingebrachte Kerbe dient zur exakten Vorgabe der Biegekante für den sich anschließenden Biegeprozess, bei dem die Bereiche rechts und links der Nut bis zum Anschlag umgeformt werden. Die verbliebene Deckschicht dient hierbei als Festkörpergelenk. Dem Sandwich wird somit durch einen Fräs- und anschließenden Umformprozess eine neue Form gegeben, in der zwei Sandwichhälften – über eine durchgehende Deckschicht fest verbunden – in einem definierten Winkel zueinander gesetzt werden. In einem letzten Schritt wird die durchtrennte Deckschicht wieder verschweißt. Bild 1 visualisiert diesen dreistufigen Fertigungsprozess.
Ziel dieses Beitrags ist es, während der Entwicklung eines Auslegers aus AFS unter Einsatz der FKT die Herausforderungen entlang des Entwicklungs- und Bearbeitungsprozesses aus Konstruktionssicht aufzudecken und daraus Gestaltungsregeln für den Konstrukteur abzuleiten. Dafür werden zunächst bestehende Konstruktions- und Fügemöglichkeiten für AFS vorgestellt und mit der FKT verglichen. Anschließend werden prinzipielle Varianten des Fertigungsprozesses der FKT beschrieben und die Konstruktion am Beispiel des erwähnten Demonstrators erläutert. Der Beitrag schließt mit einem Ausblick auf weitere Forschungsaktivitäten.
2 Konstruieren mit AFS
Die vorhandenen Freiheiten bei der Konstruktion von Bauteilen aus AFS orientieren sich an den bisher vorhandenen Bearbeitungstechniken und -strategien. Literaturrecherchen und die Analyse von Anwendungsbeispielen haben ergeben, dass umgesetzte Konstruktionen auf folgenden Ansätzen aufbauen:
Zuschneiden der Sandwichplatte zur gewünschten Bauteilgeometrie durch Sägen, Fräsen, Laser- oder Wasserstahlschneiden mit anschließendem Fügen der Bauteile mittels Verschweißen der Deckschichten oder Verbinden der Platten durch Schrauben mit Hilfe von Inserts, Nieten und Kleben. [3]
Zusammenfügen geradlinig zugeschnittener Bauteile mit Verbindern zum Verklemmen oder Zusammenstecken. [4]
Zuschnitt bzw. Stanzen und Umformen (Tiefziehen oder Pressen) der Ausgangsbleche vor dem Aufschäumen. Beim anschließenden Aufschäumen in einem Formwerkzeug erhält das Bauteil die gewünschte stabilisierte Form, ein abschließendes warmes Nachpressen stellt die Endmaße sicher. [3, 5]
Warmumformen der Sandwichplatte oder Verpressen der Ränder nach dem Aufschäumen. [3]
Die aufgeführten Ansätze zur Konstruktion von räumlichen Bauteilen – mit AFS in aufgeschäumter Form – basieren demzufolge entweder auf dem einfachen Zusammensetzen einzelner zugeschnittener Plattenelemente oder auf dem aufwendigen Umformen unter Wärmezufuhr des Ausgangsmaterials. Letzteres erfordert spezielle Fertigungseinrichtungen wie Pressen sowie Formwerkzeuge beim Aufschäumen. Die Fräskanttechnik (FKT) stellt eine einfache Alternative dar, um aus dem plattenförmigen Ausgangszustand räumliche Strukturen, ohne vorherige exakte Ausrichtung der zwei Bauteile, herzustellen, da durch die eingebrachte Nut mit definiertem Winkel zwischen den beiden Bauteilhälften nur ein Freiheitsgrad beim Umformprozess zu beachten ist. Die Nut lässt sich mit üblichen Universalfräsmaschinen oder händisch geführten Oberfräsen herstellen. Der Vorteil der FKT besteht in der gezielten Kombination der Fertigungstechniken Fräsen und Umformen bei AFS, die es erlaubt, den porösen Kern aus dem Umformprozess auszusparen, die verbleibende Deckschicht mit bekannten Blechumformprozessen zu gestalten und somit die Konstruktionsmöglichkeiten mit AFS zu erweitern.
3 Fräskanttechnik
Die Fräskanttechnik findet aufgrund vieler Vorteile bereits bei Plattenwerkstoffen im Fassadenbau Anwendung. Die dort zum Einsatz kommenden Verbundplatten weisen allerdings einen Kern aus Polymer mit mineralischen Anteilen und eine Gesamtdicke von nur wenigen Millimetern auf [6]. Nach dem Umformen ist gegebenenfalls ein Fixieren der Bauteilhälften mit einer Schweißnaht, einem Klebstoffeintrag oder mit Hilfsfügeteilen erforderlich. Der Bedarf des Fügens ist davon abhängig, ob ein auftretendes Lastkollektiv zu einer Rückbiegung führt. Mit Hilfe der Fräskanttechnik lassen sich je nach Kerbgeometrie verschiedene Winkel realisieren. Außerdem sind prinzipiell mehrere Nuttypen möglich, die in Tabelle 1 mit den jeweiligen Vor- und Nachteilen aufgeführt sind. Weitere Vorteile der Fräskanttechnik sind in der Aufzählung im Kastentext aufgelistet.

Tabelle 1: Gegenüberstellung von V- (links) und U-Nut (rechts) mit jeweiligen Vor- (+) und Nachteilen (–).
Foto: Universität Stuttgart
In der Literatur erwähnt Sviridov [7] unter dem Begriff „Gehrungsfügen“ eine erste Anwendbarkeit der Fräskanttechnik bei AFS und erläutert den zugrundeliegenden Fertigungsprozess. Am Beispiel einfacher Bauteile weist er nach, dass verschiedene Geometrien durch diese Technik umsetzbar sind. Eine tiefergehende Studie, die die Möglichkeiten und Grenzen der FKT untersucht, findet nicht statt.
In [8] greifen die Autoren die Vorteile der Anwendbarkeit der Fräskanttechnik bei Aluminiumschaum-Sandwich auf und führen experimentelle Untersuchungen an der gefrästen Kerbgeometrie durch. Der Beitrag beschreibt den Zusammenhang zwischen verschiedenen Kerbtiefen der Nut sowie den Kriterien Delamination, gemittelter Kerbradius sowie die Asymmetrie am umgebogenen Probekörper. Dieser Beitrag untersucht darauf aufbauend, wie sich die Fräskanttechnik auf die Konstruktion von Bauteilen aus AFS auswirkt und welche technologischen Besonderheiten dabei zu beachten sind.
4 Konstruktion des Demonstrators
Zur Identifikation der Herausforderungen bei der Konstruktion von Bauteilen aus Aluminiumschaum-Sandwich unter Anwendung der Fräskanttechnik wird die Entwicklung eines Auslegers ausgewählt (Bild 2).
Als Herangehensweise während der Entwicklung dient das Vorgehen gemäß der VDI-Richtlinie 2221 [9], in dem insbesondere das methodische Entwerfen und Ausarbeiten bei der Grob- bzw. Feingestaltung des Trägers angewendet wurde. Der Ausleger verbindet in leichtbaurelevanten Anwendungsfällen beispielsweise ein Anbauelement mit einem Rahmenbauteil, wie dies etwa im Sonderfahrzeug- oder Anlagenbau mit dynamischen Massen zum Einsatz kommt.
Nach den erfolgreich durchgeführten und in [8] beschriebenen Erstversuchen mit Kantenlängen von 50 mm sollten mit dem Demonstratorbauteil erstmals auch längere Biegekanten unter Anwendung der FKT gefräst und umgeformt werden. Die Abmessungen (L x B x H) des Trägers wurden daher auf circa 400 x 200 x 200 mm festgelegt, womit durch die in Bild 2 rechts dargestellte Abwicklung eine circa 400 mm lange umzubiegende Kante resultiert. Der Ausleger soll eine möglichst leichte Alternative zu Konstruktionen aus umgeformten Blechteilen darstellen und die Vorteile der Fräskanttechnik veranschaulichen. Dazu gehört beispielsweise die Möglichkeit, die Abwicklung des Trägers aus einem Plattenelement herstellen zu können. Hinsichtlich der fertigungstechnischen Umsetzung sind einfache Fertigungsverfahren wie Sägen, Fräsen, Bohren sowie das Umbiegen zu berücksichtigen.
Bei der Gestaltung des Trägers wird auf eine kraftflussgerechte Formgebung geachtet. Das Bauteil hat jeweils an beiden Laschen sowie an der Unterseite zwei Bohrungen als Möglichkeit zur Anbindung an den Rahmen bzw. für das Anbauelement. Der Kraft- verlauf, der durch die beiden großen Bohrungen eingeleitet und durch die vier kleineren Bohrungen ausgeleitet wird, resultiert in einem rechtwinklig verlaufenden Beanspruchungsfluss durch die umgeformten außenliegenden Deckschichten bzw. die innenliegenden Deckschichten und zugehörigen Schweißnähte. Der Querschnitt der versteifenden Seitenwände nimmt über der auskragenden Länge ab.
Für die Abwicklung der Grobgestalt des Auslegers bzw. für den Kraftfluss zwischen den Bohrbildern an der Bauteilunter- sowie Rückseite bestehen zwei Möglichkeiten. Der Kraftfluss kann entweder direkt über die gemeinsame hintere Kante zwischen Rückwand und Bodenplatte oder über die Kanten zwischen der Rückwand und den Seitenwänden und anschließend über die Kanten der Seitenwände in die Bodenplatte geleitet werden (vgl. abgeleitete Gestaltungsregel „Lastpfad“ in Abschnitt 6 / Tabelle 2).
Die erste Variante erfordert jedoch an den Längskanten ein Fügen der Seitenwände. Bei der zweiten Variante sind neben der Fräskanttechnik keine weiteren Verbindungstechniken erforderlich, weshalb diese bevorzugt und umgesetzt wird. Durch die vorhandene Gestalt der Konstruktion wird einem Wiederaufbiegen der umgebogenen Nuten durch die entstehenden Beanspruchungen vorgebeugt, sodass je nach Belastung das Verschweißen der inneren Deckschichten nicht zwingend erforderlich ist.
Als Material wurde das Aluminiumschaum-Sandwich der Firma pohltec metalfoam GmbH mit einer Sandwichdicke von 20 mm ausgewählt. Weitere technische Daten zum eingesetzten Plattenwerkstoff sind im Kastentext (vorige Seite, unten) zusammengefasst. Der Ausleger wurde für beide Nuttypen konstruiert und umgesetzt.
5 Fertigungstechnische Umsetzung
Nach dem Aussägen bzw. Ausfräsen der Abwicklung werden die Nuten auf einer Fräsmaschine gefertigt. Bei der Auslegervariante mit den V-Nuten wird ein mit polykristallinem Diamant besetzter Schaftfräser mit Hinterschnitt eingesetzt, der für diese Anwendung mit 45° gedrehter Vertikalachse durch die AFS Platte fräst. Die U-Nuten werden mit dem gleichen Fräsertyp aber entsprechend kleinerem Fräserdurchmesser in senkrechter Stellung eingebracht. Der Biegevorgang der V-Nut kann nach der Einspannung der vorbereiteten Platte händisch mit einer Biegehilfe (Hebel) umgebogen werden. Bei der Umsetzung der U-Nut muss eine Biegevorrichtung zur Sicherstellung des exakten Biegeverlaufs herangezogen werden. Nach der Durchführung von mehreren Tests mit Probengeometrien und dem Vergleich der beiden Nutformen wurde für die endgültige Umsetzung der FKT im Demonstrator die V-Nut ausgewählt. Die Vor- und Nachteile aus Tabelle 1 zugrundelegend, stellt sich insbesondere die nicht exakt definierte Biegekante bei der U-Nut und entsprechend erforderliche Nachbearbeitungsschritte als nachteilig heraus. Eine Validierung dieser Erkenntnisse durch die Umsetzung des Demonstrators mit U-Nut bestätigt diese Ergebnisse aus den Voruntersuchungen.
In Bild 3 ist eine Abbildung des umgeformten Auslegers mit V-Nut im nicht verschweißten Zustand dargestellt.
In der Abbildung ist erkennbar, dass aufgrund des elastischen Anteils des Biegevorgangs der hintere senkrechte Spalt zwischen den Laschen einen leicht geöffneten Winkel aufweist. Dieser wirkt sich je nach Fügestelle auf die Maßhaltigkeit in Form einer Abweichung zur Rechtwinkligkeit zwischen einem halben und einem Grad aus. Beim Verschweißen der Nut mit Arretierung kann die Maßhaltigkeit sichergestellt werden. Die dabei resultierenden Eigenspannungen sind zu berücksichtigen. An den Spaltmaßen der Nuten und den Biege- radien ist erkennbar, dass der Umformprozess gleichmäßig und entlang der gewünschten Biegekante erfolgt. Weitere Nachbearbeitungen sind nicht erforderlich. Nach dem Fräs- und Biegevorgang werden keine Auffälligkeiten bezüglich Delamination und Asymmetrie gemäß den Voruntersuchungen aus [8] festgestellt. Das Gewicht des Auslegers im abgebildeten Zustand beträgt 4,75 kg.
6 Abgeleitete Gestaltungsregeln
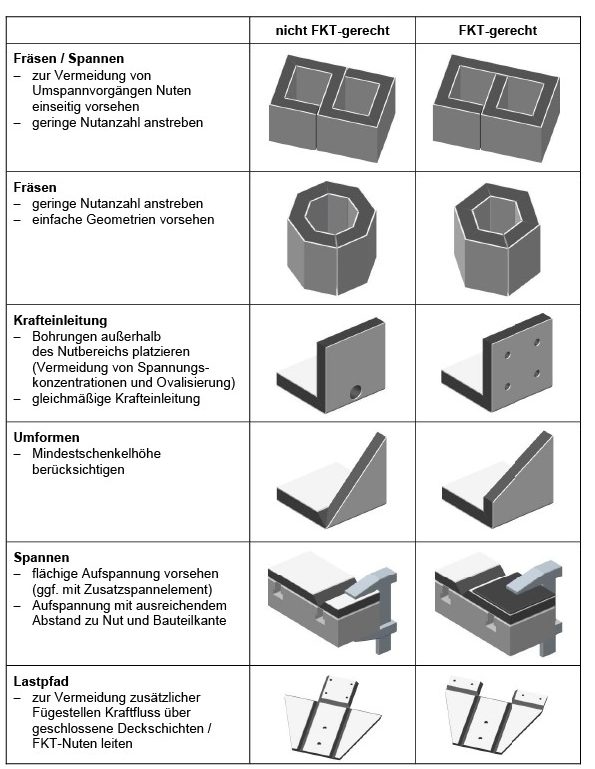
Tabelle 2: Abgeleitete Gestaltungsregeln für die Fräskanttechnik bei AFS.
Foto: Universität Stuttgart
Während der Entwicklungsschritte wurden Auffälligkeiten bezüglich fehlender Informationsstände festgehalten und hinsichtlich vorhandener Informationsquellen bzw. wissenschaftlicher Vorarbeiten recherchiert. Zusätzlich wurden bei der Fertigung Herausforderungen identifiziert, die sich bei der Umsetzung der einzelnen Bearbeitungsschritte ergeben. Die Ergebnisse sind in Tabelle 2 mit der Visualisierung eines „FKT-gerechten“ und „nicht FKT-gerechten“ Beispiels festgehalten und werden im Folgenden erläutert:
- Die Fertigungszeit von Bauteilen unter Anwendung der Fräskanttechnik wird insbesondere durch die einzubringende Nutanzahl beeinflusst. Demnach sind Konstruktionen bei gleicher Funktionalität mit so wenigen Nuten wie möglich umzusetzen. Es empfiehlt sich daher nicht, ein geschlossenes Profil durch ein Vieleck zu realisieren. Gleichmäßig runde bzw. ovale Außenkonturen sind mit der Fräskanttechnik nicht herstellbar.
- Das Spannen des Werkstücks hat in zweierlei Hinsicht Bedeutung. Erstens ist es auf Grund von zu vermeidenden Umspannvorgängen und der zugehörigen Bauteilausrichtung vorteilhaft, wenn alle Nuten für ein Bauteil auf einer Seite der Aluminiumschaumplatte eingebracht werden. Zweitens sind die Spannflächen so zu wählen, dass durch flächiges Spannen eine plas-tische Stauchung des Kerns ausgeschlossen wird.
- Um den porösen Kern beim Bearbeiten nicht durch eine ungünstige Bauteilgestalt zwischen den Sandwichdeckschichten spanend auszutragen, ist an offenen Rändern mit spitzen Winkeln eine Mindestschenkelhöhe vorzusehen.
- Aus der Blechkonstruktion abgeleitete Gestaltungsregeln betreffen insbesondere die Biegekante und deren Peripherie. In der Nähe der Biegekante eingebrachte Bohrungen neigen zu Ovalisierung und sind deshalb in einer Mindestentfernung vorzusehen.
- Wie bereits bei der Gestaltung des Auslegers im Abschnitt 4 erwähnt, ist die Biegekante als Lastübertragungsstelle zu bevorzugen. Zum einen kann so – abhängig vom Lastkollektiv – unter Umständen eine Schweißnaht gespart werden. Zum anderen wird der Kraftfluss über eine durchgängige Deckschicht ohne Unterbrechungen geleitet, was Spannungsspitzen vorbeugt.
7 Fazit und Ausblick
In diesem Beitrag wird die Anwendbarkeit der Fräskanttechnik am Beispiel der Entwicklung eines Auslegers aus Aluminiumschaum-Sandwich gezeigt und dabei die V-Nut- und U-Nutgeometrie erprobt. Entlang des Entwicklungs- und Bearbeitungsprozesses konnten verschiedene Gestaltungsregeln für die Fräskanttechnik identifiziert werden, die für Konstrukteure eine methodische Hilfestellung darstellen.
Der Ausleger wurde bisher nicht mit verschweißten Nuten hinsichtlich der Belastungsarten und deren Grenzen analysiert. In einem folgenden Schritt ist daher dessen theoretische Tragfähigkeit analytisch zu bestimmen und anschließend in einem experimentellen Versuch zu validieren. Dabei soll die Konstruktion auch mit einer konventionellen Konstruktion aus umgeformtem Blech verglichen und das Leichtbaupotential des eingesetzten Werkstoffs identifiziert werden. Eine Herausforderung stellt dabei noch die analytische Auslegung des Nutbereichs dar.
Literatur:
[1] Wiedemann, J.: Leichtbau Band 1. Elemente. – 2., neubearbeitete Auflage, Springer Verlag, Heidelberg, New York 1996
[2] Banhart, J.; Baumeister, J.; Weber, M.; Melzer, A.: Aluminiumschaum – Entwicklungen und Anwendungsmöglichkeiten, Bremen. In: Ingenieur-Werkstoffe 7, 43–45 1998
[3] Metalfoam GmbH: Broschüre zum Metallschaum weltweit einzigartig, zitiert nach: http://metalfoam.de/fileadmin/metalfoam/PDF/metalfoam_Broschuere_AFS_04032016_DE_Web.pdf (Stand: 07.08.2017)
[4] Kempf, A.: Entwicklung einer mechanischen Verbindungstechnik für Sandwichwerkstoffe, Dissertation RWTH Aachen, Aachen 2004
[5] Vieweger, B.; Sviridov, A.: Frontmodule für Schienenfahrzeuge aus Aluminiumschaumsandwich – Fertigungstechnologien zur Bauteilherstellung. In: Forum der Forschung 20/2007
[6] Alucobond: Products, Routing & Folding, zitiert nach: www.alucobond.com/plus-routing-folding.html (Stand: 20.03.2017)
[7] Sviridov, A.: Leichtbau mit Aluminiumschaumsandwich – Prozessketten zur Herstellung von Bauteilen, Dissertation Brandenburgische Technische Universität Cottbus, Cottbus 2011
[8] Bauernhansl, T.; Schuster, M.; Binz, H.; Honold, C.; Roth, D.: Fräskanttechnik bei Aluminiumschaum-Sandwichstrukturen – Analyse der Anwendbarkeit der Fräskanttechnik unter Variation der Nutgeometrie. In: wt Werkstatttechnik online, Jahrgang 107, Heft 9. Springer-VDI-Verlag, Düsseldorf 2017
[9] Verein Deutscher Ingenieure: VDI 2221: Methodik zum Entwickeln und Konstruieren technischer Systeme und Produkte, Beuth Verlag Berlin, Berlin 1993
Prof. Dr.-Ing. Hansgeorg Binz
Clemens Honold, M. Sc.
Felix Laufer, M. Sc.
Patrick Hommel, M. Sc.
Dipl.-Ing. Daniel Roth
alle: Institut für Konstruktionstechnik und Technisches Design, Universität Stuttgart, Pfaffenwaldring 9, 70569 Stuttgart
Tel.: 07 11 / 6 85-6 60 55 E-Mail: vorname.nachname@ iktd.uni-stuttgart.de www.iktd.uni-stuttgart.de
Prof. Dr.-Ing. Thomas Bauernhansl
Dipl.-Ing. Manuel Schuster
beide: Fraunhofer Institut für Produktionstechnik und Automatisierung IPA – Abteilung Leichtbau, Holzgartenstraße 17, 70174 Stuttgart
Tel.: 07 11 / 9 70-15 48 E-Mail: vorname.nachname@ipa.fraunhofer.de
www.ipa.fraunhofer.de