Wie gelingt Energieeffizienz bei Fertigungsunternehmen?
Immer mehr Fertigungsbetriebe wollen oder müssen ihre CO2-Bilanz verbessern. Da der Großteil der Emissionen auf den Energieverbrauch entfällt, gilt es, hier anzusetzen. Die fundierte Analyse bringt noch weitere Verbesserungschancen ans Licht – wie an Beispielen gezeigt wird.

Der traditionsreiche Landmaschinenhersteller konnte mithilfe des Energiemanagementsystems seinen Energieverbrauch vom Produktionsanstieg entkoppeln.
Foto: AGCO/Fendt
Für eine gezielte und nachhaltige Reduktion des Energieverbrauchs brauchen Unternehmen Transparenz. Sonst laufen sie Gefahr, dass sie in (weitgehend) wirkungslose Maßnahmen investieren. Wer hingegen die Übersicht über die Energieflüsse und Verbräuche im Unternehmen hat, kann damit den Status Quo ermitteln, Effizienzmaßnahmen definieren und priorisieren sowie deren Auswirkungen nachvollziehen und klar beziffern. Viele Unternehmen nutzen die hier gewonnen Erkenntnisse zudem für die Optimierung der Produktion, für Investitionsentscheidungen oder eine optimierte Wartung.
Erste Schritte in Richtung Klimaschutz
„Wir hatten viele Daten, aber wenig Transparenz“, erklärt Markus Lihs, Umwelt- und Energiefachkraft bei Fendt. Gegründet 1930, gilt Fendt mit über 6100 Mitarbeitern (2020) als einer der führenden Hersteller für Landmaschinen und geht auf das gleichnamige bayerische Familienunternehmen aus Marktoberdorf zurück. Seit 1997 ist es im Besitz der amerikanischen AGCO. Am Standort Marktoberdorf werden die Traktoren entwickelt, produziert und vertrieben. Die Produktionsanlagen haben aktuell eine jährliche Kapazität von rund 20.000 Traktoren und 29.000 Vario-Getrieben. Nachhaltigkeit – sowohl in der Landwirtschaft als auch auch in der eigenen Fertigungskette – hat bei Fendt einen hohen Stellenwert, an dem sich das unternehmerische Handeln konsequent ausrichtet.
Das viele Daten erfasst werden, die aber nicht direkt für Transparenz sorgen, ist nicht unüblich. Denn die meisten Unternehmen haben bereits Messgeräte im Einsatz, viele lesen diese jedoch manuell ab und werten die Daten mit Hilfe von Excel oder ähnlichen Tools aus.
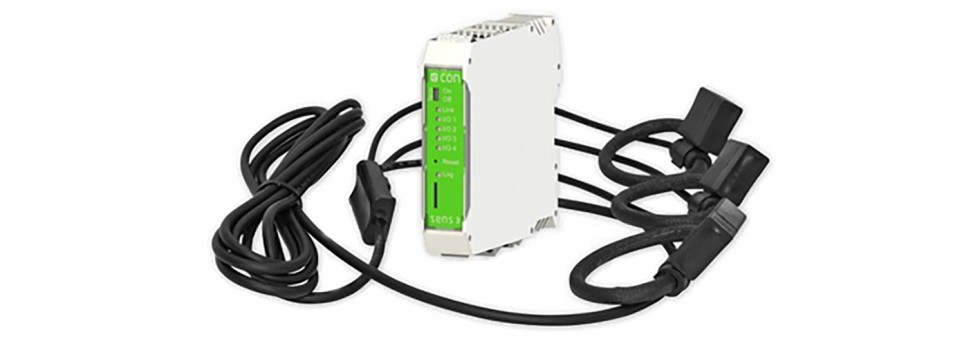
Messungen für die Erfassung von Daten sind die Basis für jedes Energiemanagement.
Foto: econ solutions
Für ein systematisches Energiemanagement reicht das nicht aus. Denn die Messintervalle sind in der Regel zu lang, die Datenqualität meist ungenügend und die Auswertungsmöglichkeiten sehr eingeschränkt. Gleichzeitig ist der Aufwand sehr hoch – in Zeiten von Industrie 4.0 ist das nicht mehr zeitgemäß.
Essenziell: ein systematisches Energiemanagement
Ein Energiemanagementsystem automatisiert diesen Prozess: Die Messdaten fließen in eine Software, welche die stets aktuellen Daten durch vielfältige Auswertungen und Berichte visualisiert. Bei Überschreitung von einstellbaren Grenzwerten werden Alarmmeldungen direkt an die verantwortliche Stelle automatisch versendet. Damit springen Effizienzpotenziale sofort ins Auge. Der Aufwand reduziert sich erheblich und die Verantwortlichen können sich drauf konzentrieren, die Effizienz zu steigern, anstatt Daten zusammenzutragen und Berechnungen durchzuführen.
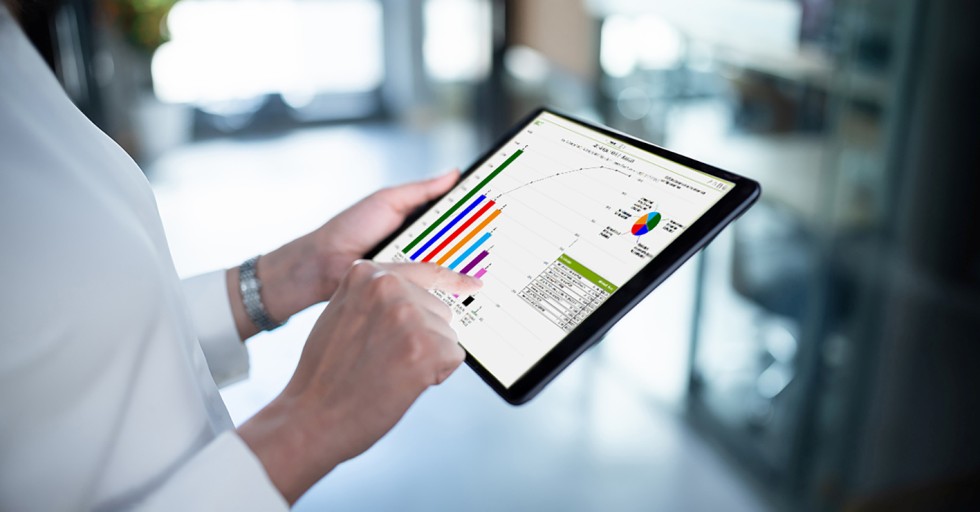
Die ABC-Analyse zeigt die größten Verbraucher auf einen Blick – und das sind oft andere als vermutet. Eine Energiemanagement-Software sollte dabei intuitiv nutzbar sein, damit der Umgang Spaß macht,
Foto: econ solutions/GettyImages
Ein solches System nutzt auch Fendt: In Sachen Messtechnik hat der Landmaschinenhersteller zuerst die steuerrelevanten Zähler in das System integriert, inzwischen erfasst das Unternehmen den gesamten Energieverbrauch an zwei Standorten. Neben dem Umfang wurde auch die Messtiefe sukzessive erweitert. Zähler und Sensoren, die bereits vorhanden waren, kommen weiterhin zum Einsatz, für neu geschaffene Messstellen nutzt Fendt das Energie- und Leistungsmessgerät „econ sens3“ von econ solutions. Es ist klein und dank mehrerer Schnittstellen auch in bestehende Systeme schnell und unterbrechungsfrei eingebaut.
Welche Fördermittel gibt es?
Eine solche Messtechnik kann mit hohen Kosten verbunden sein. Doch auch der Staat hat den Nutzen eines betrieblichen Energiemanagements erkannt und hat verschiedene Förderprogramme aufgelegt. Eines der wichtigsten ist die Bundesförderung für Energie- und Ressourceneffizienz in der Wirtschaft (EEW) des BAFA (Bundesamt für Wirtschaft und Ausfuhrkontrolle). Mit dem „Modul 3: Mess-, Steuer- und Regelungstechnik (MSR), Sensorik und Energiemanagement-Software“ werden sowohl deren Erwerb als auch Installation und Schulungen mit bis zu 40 % gefördert.
Ein Bild sagt mehr als 1.000 Messdaten
Zur Visualisierung der Messdaten haben die Münchner Spezialisten die Energiemanagement-Software „econ4“ entwickelt. Neben allen Standardberichten, wie den Lastgang und die Verbräuche, liefert sie auch zahlreiche Management- und Spezialberichte. Dies reicht von der „ABC-Analyse“ über die Spektralanalyse bis zu Kosten- und CO2-Berichten. Die Software integriert herstellerunabhängig sämtliche Datenquellen und ist offen für alle Energiearten (Strom, Gas, Wasser, Wärme, Druckluft) sowie Zustandsdaten, z. B. Temperaturen.
Bei Fendt laufen zahlreiche Daten aus der Anlagen- und Gebäudeleittechnik in econ4, darunter Verbräuche von Bearbeitungsmaschinen und Prüfständen, die Temperatur in den Produktionshallen, die Feuchtigkeit in den Spritzkabinen, Beleuchtungszeiten sowie Stückzahlen. Aus diesen und den Werten der Messgeräte erstellt die Software zahlreiche Auswertungen sowie Kennzahlen – so auch die entscheidende Kennziffer, den Energieverbrauch pro gefertigten Traktor. Diese Kennziffer konnte Fendt durch eine Reihe an Effizienz-Maßnahmen bereits deutlich verbessern.
Maßnahmen in der Produktion umgesetzt
So ist durch die Auswertungen zum Beispiel aufgefallen, dass die regenerative Nachverbrennung für die Abgasnachbehandlung auch in den produktionsfreien Nachtstunden geheizt wurde. Die Heizzeiten konnte Fendt mühelos anpassen und damit Energie einsparen.
Zudem zeigte sich, dass eine Maschine für die Zahnradfertigung in der Stillstandzeit, also im Stand-by-Betrieb, noch 20 kW verbraucht. Sie lässt sich jedoch auch so abschalten, dass sie mit 3 kW auskommt, ohne dass dadurch irgendwelche Nachteile entstehen. Durch die Menge der Maschinen ergibt sich daraus ein nicht unwesentlicher Effizienzgewinn.
Ein anders Unternehmensbeispiel: Auch die Fried Kunststofftechnik war auf der Suche nach einem passenden Energiemanagementsystem. Durch die Auswertungen mithilfe der Lösung von von econ solutions wurde z. B. offensichtlich, dass beim automatischen Lackierprozess durch eine optimierte Einstellung von Regelparametern Energie eingespart werden kann – und das ohne Qualitätsverlust. Ähnlich war es bei der Druckluftanlage mit frequenzgeregelten Kompressoren: Hier konnte Fried mit den Analysen den mindestens nötigen Systemdruck ermitteln. „Dass wir an dieser Stelle unseren Energieverbrauch reduzieren können, wussten wir vorher gar nicht“, so Dr. Andreas Tewald, Energiemanagementbeauftragter und Leiter Arbeitsvorbereitung, Facility Management, Wartung/Instandhaltung bei Fried.
Bedarfsgerechte Wartung und Basis für Managemententscheidungen
Beim Blick auf die Berichte lassen sich manchmal auch Erkenntnisse gewinnen, die gar nicht vorrangig mit Energieeffizienz zu tun haben. So war es bei Fried, als der Energieverbrauch der Lackieranlage überproportional anstieg. Die Suche nach der Ursache führte zu einem verschmutzten Filter. Diese Tatsache nutzt Fried nun, um die Filter anhand der Messdaten bedarfsgerecht auszutauschen. Zweimal jährlich nutzt das Unternehmen die Auswertungen aus econ, um die Gemeinkosten für die Produktionsmaschinen zu ermitteln und ggf. anzupassen.
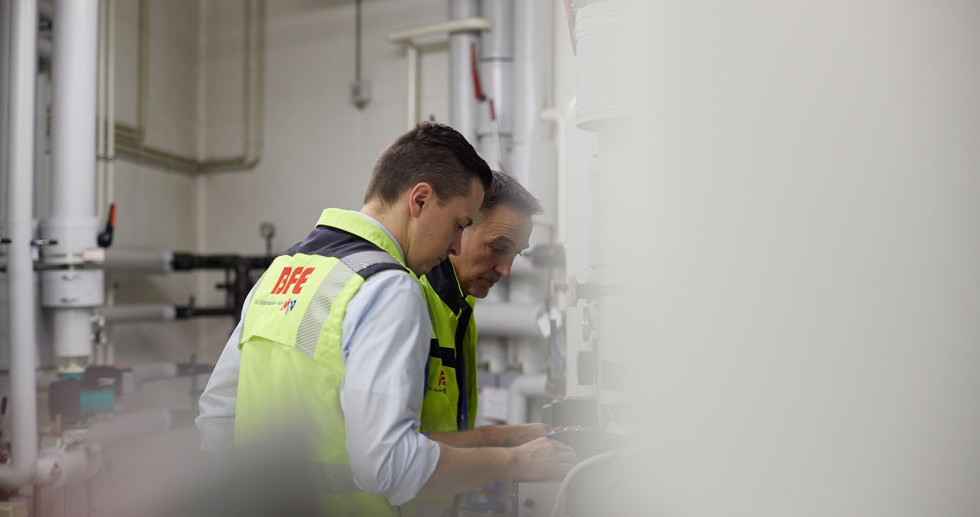
Die bedarfsgerechte Wartung von Maschinen und Anlagen erhöht die Energieeffizienz oft erheblich. Wann der richtige Zeitpunkt ist, lässt sich aus den Verbrauchsdaten ablesen.
Foto: BFE Institut für Energie und Umwelt
Weil die Menschen beim Energiemanagement eine zentrale Rolle spielen, hat bei Fendt die unternehmensweite Kommunikation zu den Energiethemen einen enormen Stellenwert. Monatliche Energiereports informieren über die entscheidenden Kennzahlen und Verbräuche, damit das Energieteam immer auf aktuelle Änderungen reagieren kann. „Solche Berichte haben wir von Anfang erstellt, aber inzwischen geht das erheblich schneller und einfacher. Es wäre wirklich schade, mit dem System nur Messtechnik zu betreiben!“, ergänzt Umwelt- und Energiefachkraft Markus Lihs.
Energiemanagement ist Klimaschutz
Mit verschiedenen Maßnahmen konnte Fendt allein im Jahr 2022 an den beiden Standorten Marktoberdorf und Asbach-Bäumenheim knapp 2.00.000 kWh Energie einsparen. Zudem ist es dem Unternehmen gelungen, den Energieverbrauch vom Produktionsanstieg zu entkoppeln. „Mit econ können wir die Einsparung detailliert nachweisen. Das System ist wie ein Navigationsgerät auf unserem Nachhaltigkeitsweg: Es zeigt, wie weit wir schon sind und auf welchem Weg wir am sinnvollsten weiter vorankommen“, beschreibt Markus Lihs.
Auch bei Fried Kunststofftechnik ist Energieeffizienz Teil der Dekarbonisierungsstrategie. Den Strombedarf, der nicht über die eigene PV-Anlage auf dem Werksgebäude gedeckt werden kann, bezieht Fried seit Juli 2021 ausschließlich als zertifizierten Ökostrom. Hinzu kommt Ökogas, sodass alle Produktionsprozesse vom Rohmaterialeingang bis zum Versand 100 % CO2-neutral sind. Im Rahmen des Energie- und Umweltmanagements lassen sich stetig weitere Maßnahmen durchführen, um immer effizienter und nachhaltiger zu werden.
Das könnte Sie auch interessieren:
ESG-Ratings – eine gute Basis für steigende Nachhaltigkeits-Anforderungen
Wie der Maschinenbau Lieferketten dank Risikomanagement absichert
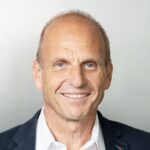
Rolf Wagner ist Prokurist und Leiter Vertrieb bei der econ solutions GmbH in München. Foto: econ