Fabrik-Layout mit virtuellen Methoden optimieren
Die Pandemie hat für einige Umbrüche in der Industrie gesorgt. Besuche der Verantwortlichen vor Ort in abgelegenen Produktionsstätten müssen zudem oft entfallen. Wie lassen sich Fabriken auf Basis intelligenter Daten dennoch zukunftsgerichtet planen?
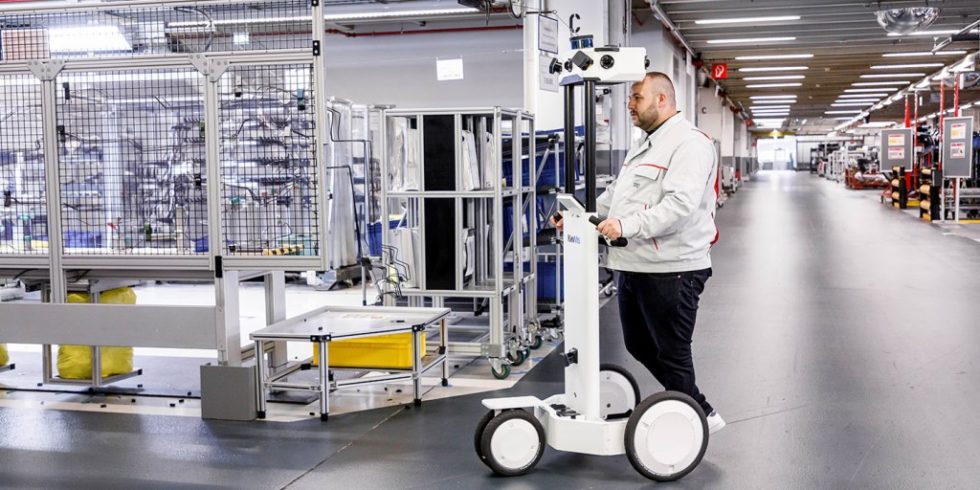
Erfassung intelligenter, aktueller Daten zur Fabrikplanung: Der "NavVIS M6" wird dazu durch den Standort geschoben.
Foto: Audi
„Die Digitalisierung der Produktion gewinnt durch Corona signifikant an Bedeutung“ – so lautet die Meinung von Finn Boysen, Chief Revenue Officer (CRO) von NavVis. Im Interview mit der VDI-Z äußert er sich zu Corona, Fabrikplanung und der Bedeutung des digitalen Zwillings.
Die Fabrikplanung genießt in der Industrie einen immer höheren Stellenwert …
Das stimmt! Dafür gibt es mehrere Gründe: Produkte müssen immer schneller auf den Markt gebracht werden, aber auch die Kosten fallen, trotz steigender Komplexität. Zudem kann ich gerade in Zeiten von Corona nicht mal schnell zu einer Fabrik nach Ungarn oder China fliegen und dort Messungen durchführen. Dann ist es von großem Vorteil, dass die Technologie von NavVis es möglich macht, in diese Fabrik virtuell hineinzusehen und mit den Leuten vor Ort über diese Daten zu kommunizieren. Hinzu kommt, dass im Zuge von „Continous Improvement“ permanent in den Fabriken verbessert und umgestellt wird – aber keiner pflegt dies in die Systeme ein. Da stellt sich natürlich die Frage, wie erhalte ich aktuelle Gebäudedaten, denen ich wirklich vertrauen kann?
An diesem Punkt kommt NavVis ins Spiel?
Genau, und wir sehen unsere Kernkompetenz in der Erfassung der „besten Daten“. Es folgt, diese „intelligent zu machen“ und den Nutzern zur Verfügung zu stellen. Unsere mehr als 200 Mitarbeiter betreuen mittlerweile über 400 Kunden in 40 Ländern. Diese kommen vor allem aus den Bereichen Automotive, Konsumgüter, Elektronik und der Prozessindustrie. Die Kunden schätzen an unserer Technologie vor allem die Geschwindigkeit und damit die geringeren Kosten, mit denen die Umsetzung abläuft. Ein weiterer wichtiger Aspekt ist natürlich die Aktualität sowie die Verfügbarkeit der Daten. Die mit unseren Laser Scannern gewonnenen Daten werden von der Fabrikplanung über Maintenance-Prozesse bis hin zu Continous-Improvement-Prozessen genutzt.
Mit dem System „NavVis M6“, welches geschoben wird, sowie dem tragbaren „VLX“ bieten wir auf der Hardware-Seite zwei Produkte an. Beide Systeme erlauben es, durch eine Fabrik zu gehen und dabei einen digitalen Zwilling des Gebäudes und der Maschinen (sowie von allem, was sonst noch da drinnen ist) aufzunehmen. Dies geschieht mit Kameras und den sogenannten Lidar-Sensoren, also die Laser, die kontinuierlich diese Daten in einer extrem hohen Auflösung aufnehmen. Den Nutzen unserer Technologie sehen wir auch und gerade darin, vorhandene Prozesse digitaler, nachhaltiger und genauer zu machen. Außerdem Kosten zu sparen, schneller eine Produktionslinie umzubauen sowie rascher ein Problem zu lösen – und damit zum Output der Fabrik beizutragen.
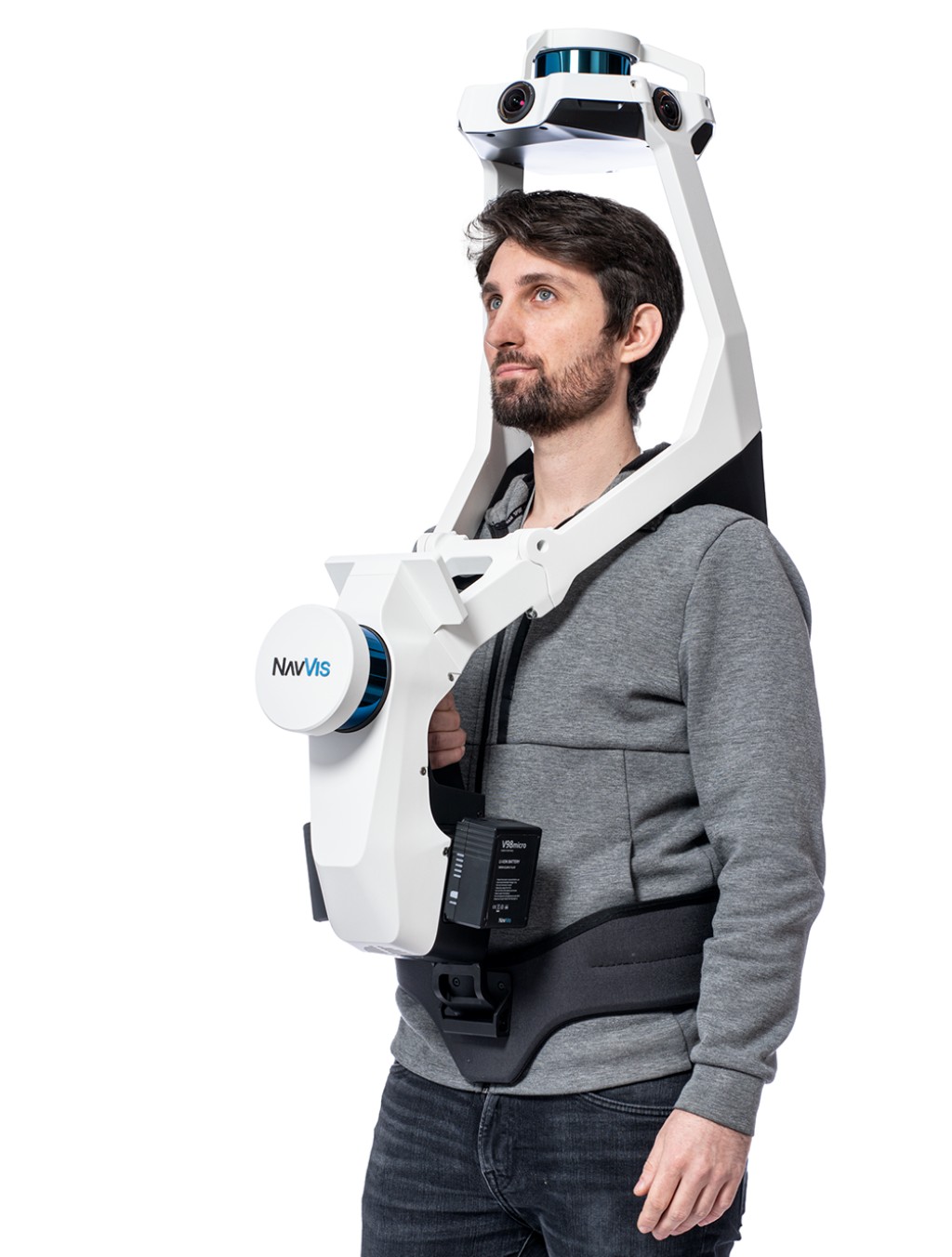
Der Laser Scanner „NavVis VLX“ kann beim Gang durch die Fabrik vom Mitarbeiter getragen werden.
Foto: NavVis
Welche Erfahrungen machten Sie und ihre Kunden während der Pandemie?
Corona stellt natürlich auch für uns eine Herausforderung dar. Wir sind jedoch sehr früh ins Home-Office gewechselt, was auch sehr gut funktioniert. Wirtschaftlich konnten wir in 2020 ein über unseren Erwartungen liegendes hohes zweistelliges Wachstum erzielen. Denn es erwies sich für uns als Vorteil, dass immer mehr Unternehmen während der Pandemie den Wert eines digitalen Zwillings ihrer Fabriken zu schätzen lernten. Schließlich konnten wegen Corona selbst die Leute vor Ort nicht einfach rausgehen, um nachzumessen. Daher gewann die Digitalisierung der Produktion signifikant an Bedeutung.
Und im nächsten Schritt wurde sie auch bereits in Aktionen umgesetzt. Wir registrieren, dass wir heute mit vielen Kunden einen anderen, seriöseren Kontakt haben als noch vor der Corona-Krise. Hinzu kommt, dass wir auch mit großen, renommierten Unternehmen – vor allem international betrachtet mit Blick auf Fabriken u.a. in den USA, China und der Türkei – zusätzliche Umsätze gemacht haben, weil sie einen digitalen Zwilling brauchten.
Ihr Fabrikplanungsangebot umfasst sowohl Hardware als auch Dienstleistung …
Neben unseren Laser Scannern können die Kunden auch auf unser Netzwerk an weltweiten Partnern zurückgreifen. Sie gewinnen für sie die Daten und führen sie in einem globalen digitalen Zwilling zusammen, den wir als Komplettlösung in unserer Software zur Verfügung stellen. Es gibt übrigens nicht viele Firmen, die so einen weltweiten Scanauftrag organisieren können – wir gehören dazu.
Selbstverständlich können die Kunden die Scans aber auch selbst durchführen. Allerdings müssen sie über eine gewisse Kompetenz und Erfahrung im Thema verfügen. Zu berücksichtigen ist: Der entscheidende Punkt für den Kauf unserer Lösung ist nicht, dass ein Kunde den ersten digitalen Zwilling will, sondern ihn aktuell halten möchte. Hierzu braucht es eben den gekauften Laser Scanner und einen trainierten Mitarbeiter. Dies ist eine gleichermaßen kosteneffiziente wie schnelle Lösung, denn die Daten sind dann stets verfügbar und Up-to-date. Schließlich gibt es immer wieder Bereiche, in denen sich jede Woche etwas verändert.
Egal, ob mit der Hardware oder der Dienstleistung – wir wollen die Technologie mit den Menschen verbinden. Sie muss so einfach sein, dass sie jeder nutzen will. Das ist unser ultimatives Ziel – zumal mit einem verbesserten Prozess auch Produktivitätssteigerungen möglich sind.
Wie beurteilen Sie den IST-Stand bei der Fabrikplanung in der Industrie?
Wir sehen oft, dass keine Datengrundlage vorhanden ist und daher bezüglich des Fabrik-Layouts viele Fragen offen bleiben: Wo ist was in der Fabrik angeordnet? Wo steht die Säule und wo befinden sich die Rohre? Steht die Maschine hier am Platz oder ein paar Zentimeter weiter? Unabhängig davon, ob bei einem innovativen, bekannten Unternehmen oder bei einem mittelständischen: Der tatsächliche Stand in den Fabriken wird häufig nicht korrekt abgebildet. Wenn die Fabrik auf Basis falscher Daten geplant wird, sind zumeist enorme Probleme die Folge. Zum Beispiel, weil die Maschine zu groß ist und nicht mehr durch die Tür passt. Oder weil die Anschlüsse anders liegen als gedacht.
Ein Beispiel: Ein Kunde aus dem Automobil-Bereich stellte in seiner großen Fabrik in Osteuropa auf ein neues Modell um – auf der Grundlage falscher Daten. Acht Wochen vor der Umsetzung erkannte er, dass drei Zentimeter bei einer Maschine fehlen. Die Konsequenz ist dann zunächst eine gewisse Panik, anschließend muss eine angepasste Planung durchgeführt werden. Das kostet sehr viel Geld. Ich würde hier beinahe von gelebtem Alltag sprechen.
Das könnte Sie auch interessieren:
Agile Methoden revolutionieren die Fahrzeugproduktion
Komplexe Spritzgießwerkzeuge digital managen
Mit Smart-Safety-Agenten die Maschinensicherheit automatisch bewerten
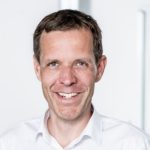
Finn Boysen, Chief Revenue Officer (CRO) von NavVis: „Wir registrieren, dass wir heute mit vielen Kunden einen anderen, seriöseren Kontakt haben als noch vor der Corona-Krise.“ Foto: NavVis