Wie Messroboter die Qualitätssicherung autonom bewältigen
Der Trend zu mehr Modularität und höherer Variantenvielfalt in der Produktion erfordert nicht zuletzt eine flexiblere Qualitätssicherung. Wie Messroboter selbstständig den Weg zum Objekt finden und ihre Messpläne autonom abarbeiten, wird an einem Beispiel aus der Automobilindustrie beschrieben.
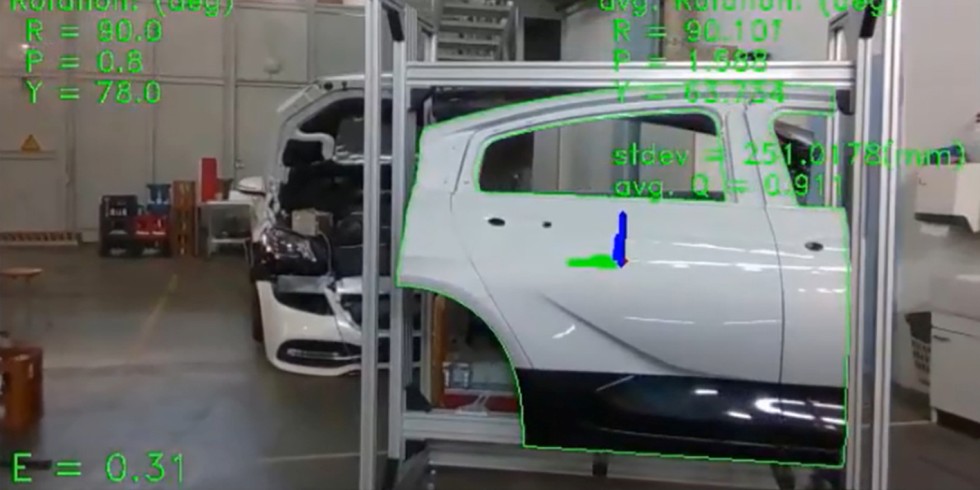
Diverse Aufgaben in der Automobilproduktion wie die Inspektion von Spaltmaßen und der Bündigkeit von unlackierten oder lackierten Karosserieteilen lassen sich jetzt ohne menschlichen Bediener bewältigen.
Foto: Zeiss
Ein Konsortium aus einen Messtechnikspezialisten, einem deutschen Automobilhersteller sowie zwei anerkannten deutschen Hochschulinstituten hat erfolgreich an einer zukunftsfähigen Lösung geforscht. Im beschriebenen Anwendungsbeispiel erledigen autonome Messroboter die Qualitätssicherung von Automobilkarosserien nun komplett eigenständig, quasi ohne den Eingriff eines menschlichen Bedieners. Damit fallen auch mögliche Fehlerquellen weg. Um die komplexe Aufgabe zu lösen, wurde unter anderem Know-how aus der Universität Ulm genutzt, das ansonsten bei Anwendungen zum autonomen Fahren zum Einsatz kommt.
Kompetente Kooperationspartner aus Wissenschaft und Industrie
Der Bereich Industrial Quality Solutions (IQS) von Zeiss gilt als tonangebend bei Lösungen für die Inline-Messtechnik. Mit der Innovation „AICell trace“ haben die Oberkochener Spezialisten es beispielsweise geschafft, die Echtzeit-Prozessüberwachung und metrologisch rückführbare Inline-Messtechnik in einer Zelle zu kombinieren. Basierend auf derartigen Projekten, liegt beim Anbieter großes Know-how durch den ständigen Austausch mit den Kunden sowie dem Wissen um deren Anforderungen und Strategien vor.
Mit Förderung vom Bundesministerium für Bildung und Forschung (BMBF) hat Zeiss in einem Konsortium mit den Partnern BMW, dem Institut für Mess-, Regel- und Mikrotechnik (MRM) sowie dem Institut für Lasertechnologien in der Medizin und Messtechnik (ILM) an der Universität Ulm als Antwort auf die aktuellen Entwicklungen das Konzept eines autonomen Messroboters (AuMeRo) erforscht und entwickelt. Ein vollständig funktionales Exemplar hat in diesem Jahr bereits beweisen können, dass sich damit diverse Aufgaben – wie etwa die Inspektion von Spaltmaßen und die Bündigkeit an unlackierten oder lackierten Karosserieteilen – in vollem Umfang bewältigen lassen.
Variantenvielfalt macht Modularisierung der Fertigung notwendig
„Eine starre Fertigungsstraße für ein Standardprodukt, auf der eine möglichst große Stückzahl produziert wird – dieses bislang gut etablierte Konzept könnte schon bald eine Technik von Gestern sein“, sagte Manuel Schmid, Produktmanager bei Zeiss IQS. Immer individuellere Kundenwünsche führen zu einer steigenden Variantenvielfalt bei Produkten und damit einer notwendigen Modularisierung bei deren Fertigung. Besonders davon betroffene Branchen wie der Automobilbau planen daher langfristig, sequenzielle Fertigungsprozesse mit hochspezialisierten Stationen in naher Zukunft aufzulösen und durch flexibel einsetzbare Fertigungsinseln zu ersetzen.
Der autonome Messroboter erkennt mit Hilfe von Kameras sein Ziel selbstständig und richtet sich an der Karosserie aus, um Spalt und Bündigkeit an den gewünschten Positionen ohne menschliche Interaktion zu inspizieren.
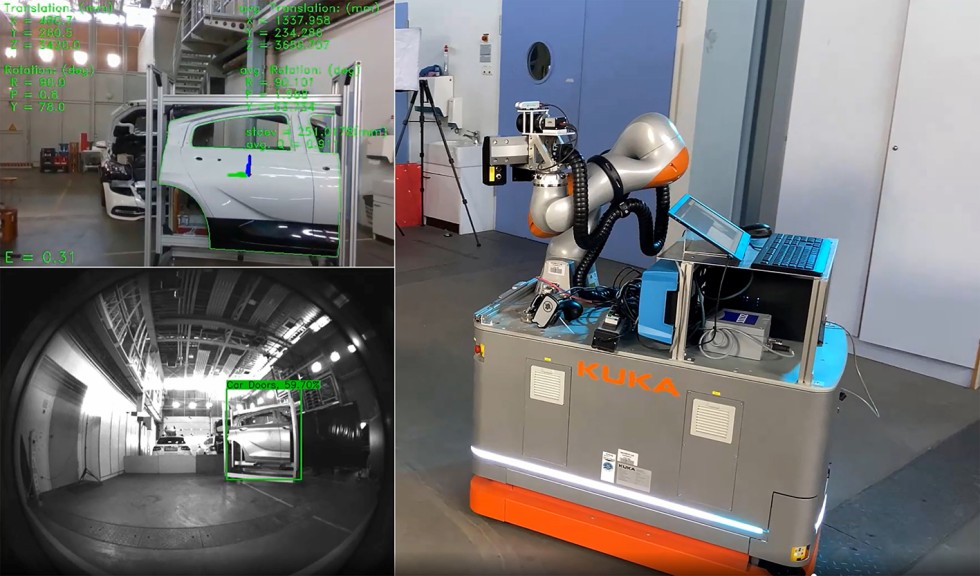
Der autonome Messroboter erkennt mit Hilfe von Kameras sein Ziel selbstständig und richtet sich an der Karosserie aus, um Spalt und Bündigkeit an den gewünschten Positionen ohne menschliche Interaktion zu inspizieren.
Foto: Zeiss
Kompetenzen für ein intelligentes, autonomes System kombiniert
Der AuMeRo ist eine rechteckige Plattform mit Rädern an der Unterseite und einem Roboterarm mitsamt einem optischen Mess-Sensor an der Oberseite. „Dieser Hardwareaspekt ist für sich natürlich noch nicht revolutionär“, erklärt Dr. Matthias Karl von der Konzernforschung der Gruppe. „Die wesentliche Aufgabe stellte sich uns auf Seiten der Software: Hier war es erforderlich, die nötige Intelligenz für die autonome Bewegung zum Objekt, dessen Vermessung und die Datenverarbeitung zu erschaffen.“ Um diese Herausforderung im Forschungsprojekt zu meistern, legten die Forschungspartner ihre jeweiligen Kompetenzschwerpunkte zusammen.
Das Institut für Mess-, Regel- und Mikrotechnik der Universität Ulm hat einen Fokus auf autonomes Fahren und arbeitet in diesem Bereich mit mehreren Automobilherstellern zusammen. Es erarbeitete und implementierte daher die Navigationslösung für die mobile Messplattform. Damit kann diese sich jetzt autonom zum Zielobjekt bewegen und dabei auch Hindernisse sicher umfahren.
Das Institut für Lasertechnologien in der Medizin- und Messtechnik hat langjährige Erfahrungen in der optischen Messtechnik. Es erforschte und entwickelte eine Methode zur gleichzeitigen Vermessung von rohen, gefärbten und lackierten Karosserieteilen mit „nicht-kooperativen“ Oberflächen mit demselben Messgerät. Und Zeiss – als Verbundkoordinator – war mit seinem Bereich Industrial Quality Solutions und der Konzernforschung gleich mit zwei Fachabteilungen vertreten: IQS trug die anwendungsnahe optische Messtechnik dazu bei, während die Konzernforschung die Bewegung des Roboterarms, die Objekterkennung und die Messposen-Ansteuerung durch optische Bilderkennung in Verbindung mit maschinellem Lernen gewährleistete. Der Applikationspartner BMW als einer der führenden Premium-Automobilhersteller gab dem Projekt einen greifbaren Praxiskontext.
Ausgeklügelter Ablauf der autonomen Vermessung
„Der Anwender wählt via Software ein Objekt, zum Beispiel eine Fahrzeugtür, dessen groben Standort und danach den relevanten Messplan. Ab diesem Punkt agiert AuMeRo vollständig autonom“, erklärt Manuel Schmid. Die Objekterkennung folgt via Kamera und basiert auf einem digitalen Zwilling des Objekts. Für die eigentliche Messung wird die mobile Plattform mit zusätzlichen optischen Sensoren ausgestattet: Dazu wurde am ILM ein spezielles Messgerät mit Vorteilen für kurze Messzeiten und robuste Umgebungseinflüsse entwickelt, das Mehrwellenlängen-Digitalholografie nutzt. Auf diese Weise können innerhalb eines „Schnappschusses“ topografische Daten einer gesamten Fläche für diffus und/oder spiegelnd reflektierende Oberflächen gewonnen werden.
Nachdem die Plattform das Objekt gefunden und angefahren hat, bewegt der Roboterarm den Messkopf gemäß den Erfordernissen aus dem Messprogramm unter Berücksichtigung der aktuellen räumlichen Gegebenheiten. „Durch seine Fähigkeit zur autonomen Mobilität und Objekterkennung ist AuMeRo bereit für eine Zukunft, in der mobile, modulare Fertigungsinseln die Regel sind, und erlaubt eine Messung immer dort und dann, wo sie gerade nötig ist“, sagt Schmid. „Er kann aber für Hersteller schon jetzt seine Vorzüge vollständig ausspielen: Ein Beispiel dafür sind Produktaudits, in denen derzeit Messung und Dokumentation händisch im Messraum durchgeführt werden. Mit AuMeRo geht das viel effizienter – nämlich automatisiert und reproduzierbar mit konstant hoher Qualität und Aussagekraft der generierten Messergebnisse.“
Individuelle Aufgaben erfüllen und zugleich Effizienz steigern
„Wir haben mit dem Forschungsprojekt demonstrieren können, dass das Konzept ohne Einschränkung funktioniert. Und vor allem auch, dass es sich einfach auf neue Objekte und Messpläne adaptieren lässt. Damit sind die Türen für diese Technologie weit aufgestoßen“, sagt der Gesamtverbundkoordinator Dr. Matthias Karl. Und der industrielle Anwender – Jan-Klaus Dziergwa, Projektleiter Karosseriebau, Qualitätsmanagement BMW Group – ist von dem Ergebnis begeistert: „Bei BMW sind wir hoch interessiert daran, individuelle Kundenwünsche zu erfüllen und zugleich unsere Effizienz während der Produktion und Qualitätssicherung immer weiter zu steigern. Das erfordert innovative Methoden und Technologien. AuMeRo ist dafür ein hervorragendes Beispiel.“
Über die beteiligten Unternehmen und Institute
Zeiss entwickelt, produziert und vertreibt innovative Lösungen für die industrielle Messtechnik und Qualitätssicherung, Mikroskopielösungen für Lebenswissenschaften und Materialforschung sowie Medizintechniklösungen. In vier Sparten (Semiconductor Manufacturing Technology, Industrial Quality & Research, Medical Technology und Consumer Markets) wurde zuletzt einen Jahresumsatz von 6,3 Milliarden Euro erwirtschaftet (Stand: 30.9.2020). Der Bereich Industrial Quality Solutions gilt als führender Hersteller von Lösungen für die mehrdimensionale Messtechnik. Dazu zählen etwa Koordinatenmessmaschinen, optische und multisensorische Systeme, die 3D-Röntgenmessung, Mikroskopiesysteme für die industrielle Qualitätssicherung sowie auch Messtechniksoftware. Zu den belieferten Branchen zählen die Automobilindustrie, der Flugzeug- und Maschinenbau sowie die Kunststoffindustrie und die Medizintechnik.
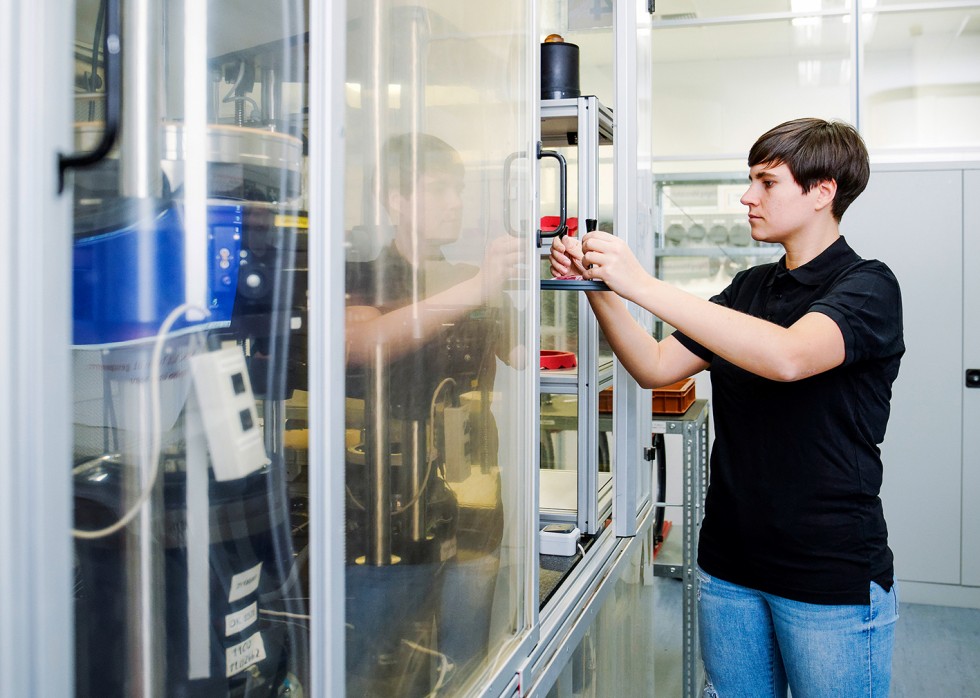
Forscherin bei Zeiss in Jena: Der Konzern blickt 2021 auf das 175-jährige Bestehen zurück und gilt als weltweit führendes Technologieunternehmen der optischen und optoelektronischen Industrie.
Foto: Zeiss
Die BMW Group ist mit ihren Marken ein weltweit führender Premium-Hersteller von Automobilen und Motorrädern sowie Anbieter von Finanz- und Mobilitätsdienstleistungen. Als internationaler Konzern betreibt das Unternehmen 31 Produktions- und Montagestätten in 14 Ländern sowie ein globales Vertriebsnetzwerk mit Vertretungen in über 140 Ländern.
Außerdem sind am Projekt noch zwei Institute der Universität Ulm beteiligt: Das Institut für Mess-, Regel- und Mikrotechnik (IRM) arbeitet seit mehr als 15 Jahren im Bereich der automatisierten Systeme mit Schwerpunkt des automatisierten Fahrens. Aktuell sind mehr als 15 Wissenschaftliche Mitarbeiterinnen und Mitarbeiter mit diesem Themenschwerpunkt befasst. Methodische Schwerpunkte liegen im Bereich der grundlegenden Sensorsignalverarbeitung von Video -, „Lidar“- und Radarsensoren, der Informationsfusion, dem Multi-Objekt-Tracking, der Umfeldmodellierung mit Situationsverstehen und der Handlungsplanung autonomer Systeme. Und last but not least: Das Institut für Lasertechnologien in der Medizin und Messtechnik (ILM), ein rechtlich eigenständiges An-Institut, forscht in ausgewählten Bereichen der Photonik / Optik und transferiert die erarbeiteten Technologien in die industrielle und medizinische Praxis. Die wichtigsten Anwendungsfelder umfassen Medizin und Dentaltechnologie, Produktionsmesstechnik, Prozessanalytik, Agrar- & Umweltsensorik sowie Sensorik für autonome Systeme.
Das könnte Sie auch interessieren:
Automobilbau: Qualitätsprüfung mit Augmented Reality
Best Fit in der Oberflächenmesstechnik
Elektronischer „Fingerabdruck“ für die technologische Souveränität