Inline-Überwachung: Wie klingt eine fehlerfreie Zerspanung?
Erfahrene Bediener von CNC-Fräszentren erkennen oft schon an Geräuschen, ob sich in der Zerspanung ein Problem ankündigt. Die Klangunterschiede im laufenden Bearbeitungsprozess nutzt ein Werkzeugspezialist für ein innovatives Expertensystem.
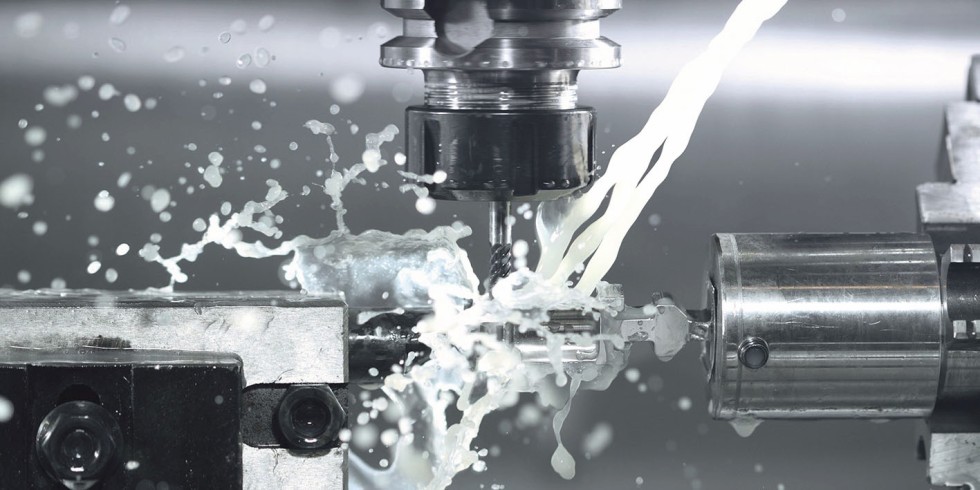
Jeder Aspekt einer Bearbeitungssituation lässt über eigene Frequenzbänder Rückschlüsse zu: Werkzeugzustand, Antrieb, Aufspannung und Frässtrategie zeigen durch Abweichungen in den Geräuschen an, wenn sich Bedingungen in der Zerspanung ändern.
Foto: PantherMedia
Unter der Bezeichnung „SonicShark“ ist jetzt eine neuartige Technik zur prozessbegleitenden Qualitätskontrolle in der zerspanenden Bearbeitung entstanden. Mit Hilfe von Körperschallsensoren und einer lernfähigen KI (Künstlichen Intelligenz) erkennt das System Anomalien in Produktionsprozessen, identifiziert Materialinhomogenitäten und „hört“ beginnenden Werkzeugverschleiß.
Was sind die Vorteile für den Anwender?
Durch die bearbeitungsbegleitende Inline-Kontrolle hilft das System, Zeit und Kosten in der Qualitätssicherung (QS) einzusparen. Es gestattet eine effizientere Werkzeugnutzung sowie eine vorausschauende Wartung. Dank der Prozessüberwachung ist es möglich, die Bauteilqualität zu verbessern, Prozesszeiten zu verkürzen, Maschinen länger auszulasten und Ressourcen wie Personen- und Maschinenzeit effizient zu nutzen.
Das System hat Hufschmied Zerspanungssysteme entwickelt. Das 1991 gegründete Unternehmen mit Hauptsitz in Bobingen bei Augsburg ist ein Hersteller prozessoptimierter Präzisionswerkzeuge für die zerspanende Fertigung sowie Systemlieferant renommierter Werkzeugmaschinenhersteller. Die Hochleistungswerkzeuge und die Fertigungsprozessberatung werden besonders in der Automobil- und Luftfahrtindustrie sowie in der Medizintechnik geschätzt. Das Unternehmen ist in zahlreichen Organisationen engagiert, darunter dem Composites United Deutschland e. V. Mit Hilfe einer vorangegangenen Forschungskooperation haben die Bobinger in die Neuentwicklung SonicShark auch die Expertise weiterer Spezialisten, zum Beispiel aus dem Digitalisierungsbereich, mit eingebracht.
Wie funktioniert eine Inline-Qualitätskontrolle?
Die Inline-Qualitätskontrolle (auch gerne als „Qualitätssicherung 4.0“ bezeichnet) beschreibt die datenanalytische (Echtzeit-)Überwachung der Produktion hinsichtlich Abmaßen, Materialschwankungen, Fertigungsfehlern etc. Sie zeichnet sich dadurch aus, dass sie innerhalb des Prozesses vonstatten geht – und nicht wie sonst üblich nachgelagert. Mit Hilfe spezieller Software und KI sind teilweise auch Vorhersagen bezüglich der Qualität („Predictive Quality“) möglich.
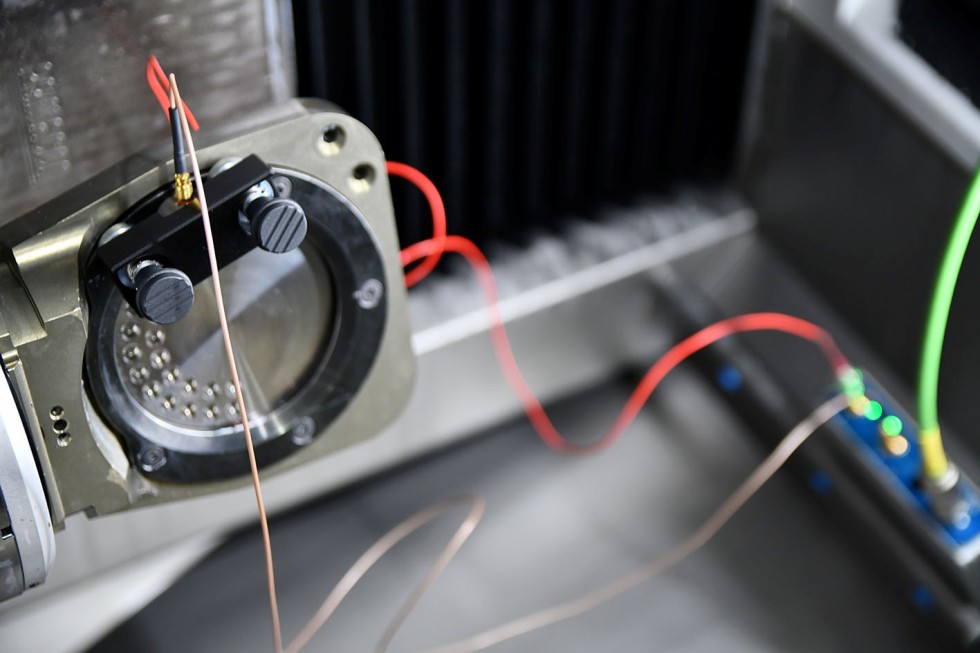
Magnetische Sensoranbringung an einem Schraubstock: „SonicShark“ erkennt den Klang fehlerfreier Zerspanung und „warnt“ bei Abweichungen.
Foto: Hufschmied
IIoT (Industrial Internet of Things)-Plattformen ermöglichen es zu jeder Zeit, Anlagen, Werkzeuge und Werkstücke der Produktion nachzuverfolgen. Dabei senden Sensorik und/oder Anlagen Messwerte an die Plattform. Über Körperschall, gemessene Leistung und weitere Kennzahlen erfasst das System alle möglichen Parameter – und damit auch Abweichungen. Ein Beispiel ist die IIoT-Plattform „CuttingEdge“ für die spanende Bearbeitung, die von der Firma inno-focus digital aus Berlin entwickelt wurde.
Über insgesamt drei Jahre wurde der Prototyp und Vorläufer des heutigen Portals CuttingEdge in einem Forschungsprojekt geprüft. Im Vorhaben „Inline Produktions- und Qualitätskontrolle bei der Fräsbearbeitung von metallischen und CFK-Produkten“ erarbeiteten die Partner aus Industrie und universitären Einrichtungen, wie die Qualität in Fräsprozessen durch den unternehmensübergreifenden Austausch von Daten verbessert werden kann. Auch Hufschmied war daran beteiligt. Ziele wie die Reduktion des Aufwands in der Qualitätssicherung, Effizienzsteigerungen, ein sparsamerer Einsatz von Ressourcen, ein dezentraler Einsatz von Fachkräften und viele weitere wurden erfolgreich realisiert. Um die Potenziale von Industrie 4.0 für die Zerspanung noch stärker zu nutzen, wird CuttingEdge als unternehmensübergreifendes Ökosystem kontinuierlich weiterentwickelt und ausgebaut.
Das Expertensystem vom Werkzeugspezialisten
Doch zurück zur Entstehungsgeschichte von SonicShark: Sehr erfahrene Maschinenbediener erkennen bereits an Geräuschen, ob in der Zerspanung alles rund läuft oder ein Problem vorliegt. Doch diese Experten werden immer seltener. Die Klangunterschiede in der laufenden Zerspanung nutzt Hufschmied daher nun für sein Expertensystem. Dieses detektiert akustische Abweichungen vom Sollzustand und weist frühzeitig auf Mängel im Fertigungsprozess hin. Für die Inline-Qualitätskontrolle werden je nach Größe des Werkstücks ein oder mehrere Körperschallsensoren am Werkstück angebracht. Ein kleiner Computer neben der CNC-Maschine sammelt die Sensordaten. Das System wird auf die Referenzakustik einer Zerspanung unter optimalen Bedingungen trainiert – für die eigenen Werkzeuge liefert Hersteller Sensor-Soll-Signale künftig als Referenz mit.
Die Software legt eine Sensordatenbank an und vergleicht die Soll-Daten mit den Ist-Daten. Auf einem Bildschirm wird das Ergebnis des Vergleichs angezeigt und der Maschinenbediener gewarnt, wenn sich in den Frequenzen Abweichungen über oder unter festgelegten Schwellwerten ergeben.
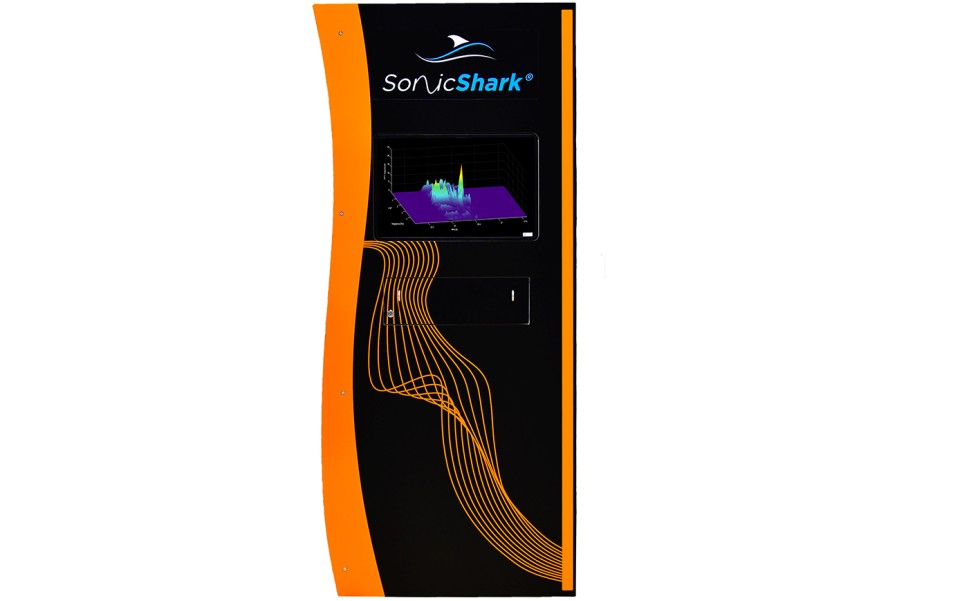
Ein Expertensystem detektiert akustische Abweichungen vom Sollzustand und weist frühzeitig auf Mängel im Fertigungsprozess hin. Grafik: Hufschmied
Verschleiß besser einschätzen, Werkzeugkosten senken
In der Erforschung des „Lärms“ hat die Entwicklungsabteilung von Hufschmied festgestellt, dass jeder Aspekt der Bearbeitungssituation über eigene Frequenzbänder Rückschlüsse zulässt: Werkzeugzustand, Antrieb, Aufspannung und Frässtrategie melden durch Abweichungen in den Geräuschen, wenn sich Bedingungen ändern.
Bisher werden Werkzeuge meist in Standzeittests qualifiziert und zur Sicherheit unabhängig von ihrem tatsächlichen Zustand nach einer festgelegten Zeit ausgetauscht. Werden diese starren, vielfach übervorsichtigen Vorgaben durch die Inline-Qualitätskontrolle ersetzt, spart das nicht nur Werkzeugkosten, sondern auch Zeiten für Werkzeugwechsel und Platz im Magazin für Schwesterwerkzeuge. Zudem verringert die Echtzeitüberwachung Ausschuss, der durch die Bearbeitung mit einem vorzeitig verschlissenen Werkzeug produziert wird.
Materialfehler und Maschinenverschleiß erkennen
Schätzungsweise 25 bis 30 Prozent der Herstellungskosten entstehen in der Qualitätssicherung und -prüfung. Das innovative Expertensystem eröffnet auch hier große Einsparpotenziale. Durch die Kombination verschiedener Sensordatenbanken mit Maschinendaten und einer optischen Qualitätskontrolle ist es möglich, Fehlstellen oder Defekte im Bauteil < 1 mm zu detektieren und an die QS-Abteilung mit den entsprechenden Koordinaten zu übergeben.
Die Analyse der Geräusche lässt zudem Rückschlüsse auf den Zustand der verwendeten Werkzeugmaschine zu. Die SonicShark-Sensorik kann deshalb als Basis für Predictive Maintenance sowie für digitale Prozessanalyse und Prozessoptimierung genutzt werden.
Inline-QS mit weiteren Experten in Leichtbauprojekten getestet
Die von Hufschmied entwickelte akustische Inline-Qualitätskontrolle kam zwischenzeitlich in zwei Kooperationsprojekten von MAI Carbon aus Augsburg zum Einsatz: In Zusammenarbeit mit der BMW Group, der Universität Augsburg, der Alexander Thamm GmbH, der inno-focus business consulting gmbh und VisCheck GmbH wurden im Projekt „MAI ILQ2020“ Möglichkeiten zur unternehmensübergreifenden Prozesskontrolle ermittelt. Die Inline-Qualitätskontrolle war zudem ein zentraler Aspekt im Projekt „MAI FastMove“ zur Förderung der HSC (High Speed Cutting)-Bearbeitung in der Zerspanung von CFK (kohlenstofffaserverstärkten Kunststoffen). Dem Spitzencluster MAI Carbon des Composites United e.V. (CU) gehören über 130 Teilnehmer an. Bayernweit wird darin das Ziel verfolgt, Leichtbautechnologien großindustriell für verschiedene Anwenderbranchen zu implementieren.
Das könnte Sie auch interessieren:
Zuverlässiges Messen in Drehbearbeitungszentren
Wie reagieren Kunststoffe unter mehraxialen Zugbelastungen?
Sechs Tipps für digitales Produktionsmanagement in der Industrie