Wälzschälen – eine neue Verzahnungsrealität
Das Wälzschälen ist heute ein in der Industrie weit verbreitetes Verfahren zur Herstellung von Zahnprofilen, das spezielle Werkzeuge und Bearbeitungsstrategien erfordert. Ein Werkzeugspezialist und ein internationaler Technologiekonzern haben das Verfahren in einem konkreten Anwendungsfall zur Perfektion weiterentwickelt.
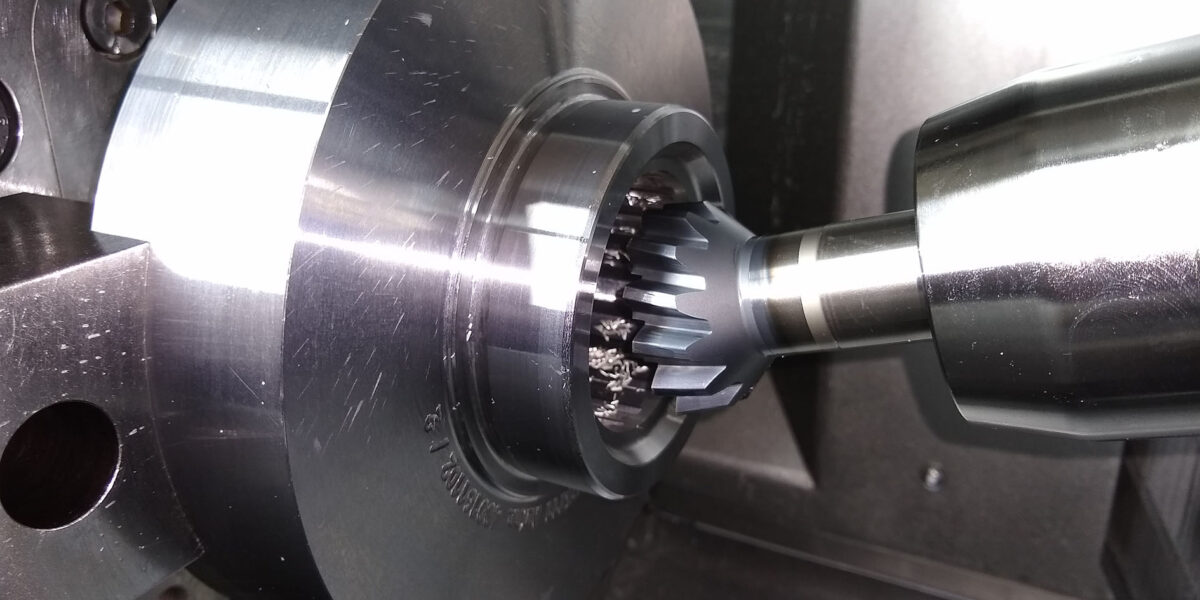
Wälzschälen: Ein „Power Skiving“-Werkzeug, gezeigt ist hier der „CoroMill 178B", und ein Werkstück in der Bearbeitungsmaschine.
Foto: Sandvik Coromant
Beim Wälzschälen handelt sich um ein hochproduktives, kontinuierliches Zerspanungsverfahren mit geometrisch bestimmter Schneide, das hauptsächlich zur Herstellung von Verzahnungsteilen eingesetzt wird. Durch Entwicklungen im Bereich der Schneidstoffe, der Maschinentechnik und des Prozessverständnisses, kann das Verfahren heute auch auf Universal-Bearbeitungsmaschinen angewendet und eingesetzt werden. Beispielsweise ermöglichen neue Schneidstoffe und Werkzeugdesigns die Bearbeitung von weichen und harten Bauteilen, wodurch diese Technologie ein großes Optimierungspotenzial bietet.
Gemeinsames Projekt soll Prozessverständnis fördern
Aufgrund der komplexen Eingriffsbedingungen und deren Wechselwirkung mit den Prozessparametern und der Prozessführung ist ein tiefes Verständnis der zugrunde liegenden Prozesse die Voraussetzung für einen stabilen Bearbeitungsprozess sowie qualitativ hochwertige Bauteile beim Wälzschälen. Der Werkzeugspezialist Sandvik Coromant hat gemeinsam mit der Voith Group das Optimierungspotenzial des Wälzschälens an einem konkreten Anwendungsfall untersucht. Voith ist ein weltweit agierender Technologiekonzern mit einem breiten Portfolio an Anlagen, Produkten, Serviceleistungen und digitalen Anwendungen in den Märkten Energie, Papier, Rohstoffe sowie Transport & Automotive.
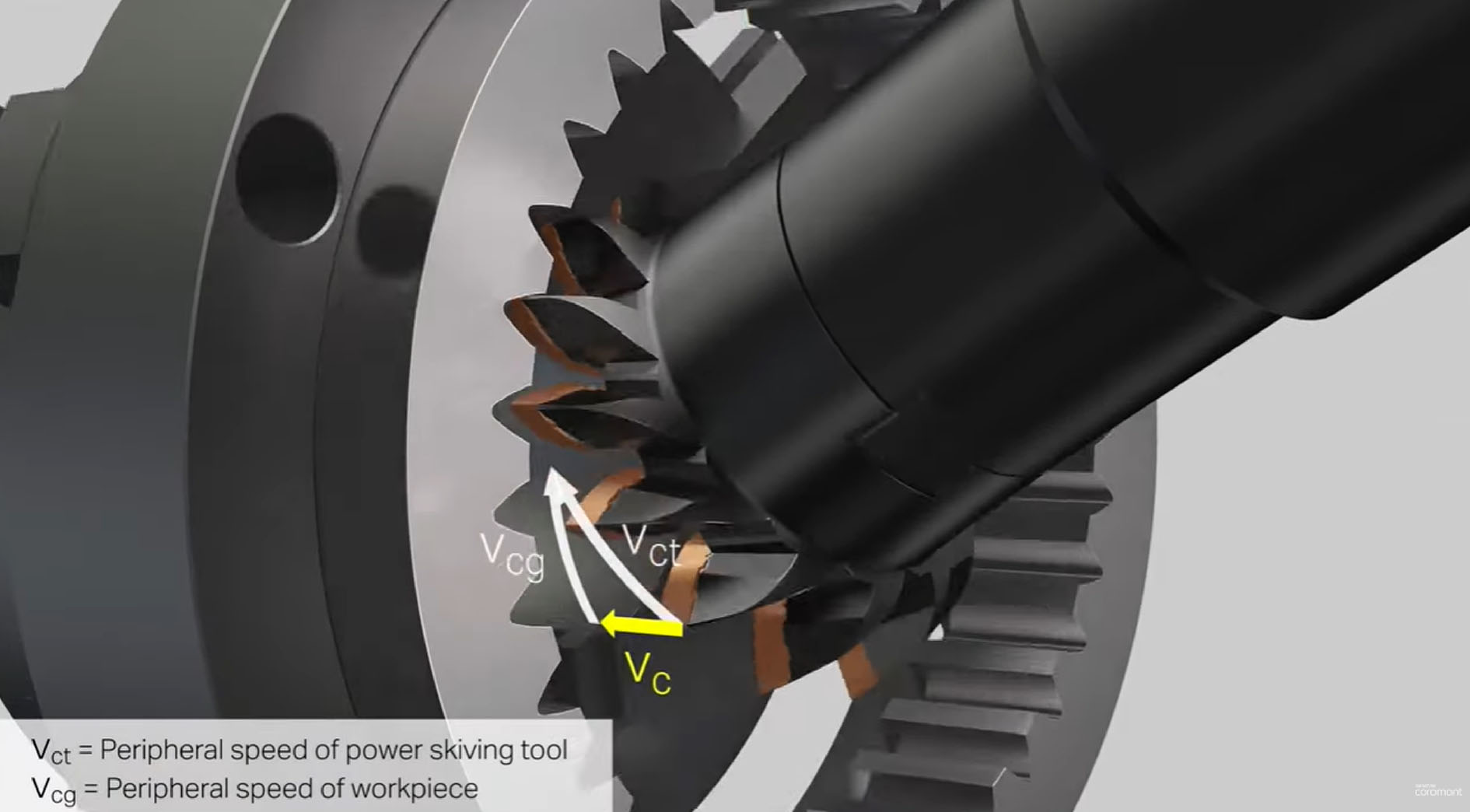
Bild 1. Beim Wälzschälen sind Werkzeug (hier „CoroMill 180“-Wendeschneidplattenfräser) und Werkstück im Eingriff und rotieren kontinuierlich und synchron nach Art eines Schneckengetriebes. Grafik: Sandvik Coromant
Beim Wälzschälen, auch „Power Skiving“ genannt, Bild 1, handelt es sich um ein kontinuierliches Zerspanungsverfahren, das heute auch auf Universalmaschinen eingesetzt werden kann. Somit lassen sich alle Bearbeitungsschritte in einer Aufspannung durchführen. Dabei sind Werkzeug und Werkstück im Eingriff und rotieren nach Art eines Schraubwälzgetriebes kontinuierlich und synchron. Die Werkzeugachse ist gegenüber der Werkstückachse um den Achskreuzwinkel Σ geneigt. Das am Werkstück zu erzeugende Profil entsteht durch den Wälzvorgang in Verbindung mit der Werkzeugform und der Relativbewegung von Werkzeug und Werkstück.
Aus der Relativbewegung und der Achslage ergibt sich die Schnittgeschwindigkeitskomponente vc. Die Vorschubbewegung des Werkzeugs erfolgt entlang der Werkstückachse, Bild 2. Die radiale Zustellung erfolgt meist in mehreren Schnitten, die durch unterschiedliche Aufteilungsstrategien an den jeweiligen Bearbeitungsfall angepasst werden können. Häufig ist es sinnvoll, zwischen Schrupp-, Vorschlicht- und Schlichtschnitten zu unterscheiden und die Prozessparameter entsprechend zu variieren.

Bild 2. Das Prinzip konischer (links) und zylindrischer (rechts) Werkzeuge am Beispiel des CoroMill 178. Grafik: Sandvik Coromant
Spezielle Werkzeuge erforderlich
Für das Wälzschälen werden verschiedene Werkzeugtypen verwendet. Man unterscheidet zwischen konischen und zylindrischen Werkzeugen. Bei konischen Werkzeugen ist der Freiwinkel konstruktiv im Werkzeug vorgesehen. Die Bearbeitung erfolgt in der Regel mittig. Das Nachschleifen von konischen Werkzeugen ist aufgrund des konstruktiven Freiwinkels nur bedingt profiltreu möglich.
Zylindrische Werkzeuge sind ohne konstruktiven Freiwinkel ausgeführt, so dass diese Werkzeuge häufiger profiltreu nachgeschliffen werden können. Aufgrund des fehlenden konstruktiven Freiwinkels wird ein kinematischer Freiwinkel durch eine exzentrische Werkzeuganstellung erzeugt. Die Werkzeuge werden in der Regel als Wendeschneidplatten (WSP)-, Vollhartmetall (VHM)- oder High Speed Steel (HSS)-Werkzeuge ausgeführt.
Sandvik Coromant, seit Jahrzehnten Partner von Voith, hat verschiedene Hochleistungswerkzeuge für das Wälzschälen entwickelt: „Mit dem CoroMill® 178 bieten wir Schneidräder in zwei Ausführungen an: aus pulvermetallurgischem Schnellstahl (PM-HSS) und aus VHM. Unser WSP-Fräser ,CoroMill 180‘ ist mit prismatischen Plattensitzen ausgestattet und für hervorragende und wiederholbare Genauigkeit ausgelegt. Alle Werkzeuge können hinsichtlich Steifigkeit, Auskraglänge, Kühlmittelzufuhr und maximaler Standzeit weiter optimiert werden. Damit ermöglichen sie eine reproduzierbare und prozesssichere Fertigung. Entscheidend für den Bearbeitungserfolg ist die auf den jeweiligen Bearbeitungsfall abgestimmte Werkzeugauswahl und die darauf abgestimmte Bearbeitungsstrategie“, führt Jochen Sapparth, Project & Sales Engineer bei Sandvik Coromant, aus.
Konkrete Anwendung vor Ort: von der sequentiellen zur optimierten Prozesskette
Neue Technologien wie das Wälzschälen können ein enormes Optimierungspotenzial bieten. Um dieses auszuschöpfen, ist es notwendig, bestehende Prozessketten zu analysieren und mögliche Ansatzpunkte zu identifizieren. Bei Voith Turbo – neben Voith Hydro und Voith Paper einer der drei Konzernbereiche von Voith – wurde ein Anwendungsfall identifiziert. Bei dem Unternehmen, das Antriebselemente herstellt, die weltweit in Industrieanlagen sowie auf Schiene, Straße und zu Wasser eingesetzt werden, gab es den nachfolgend beschriebenen Bearbeitungsprozess, die Herstellung einer innenverzahnten Kupplungsverzahnung für Triebwagen- und Lokomotivgetriebe nach DIN 5480.
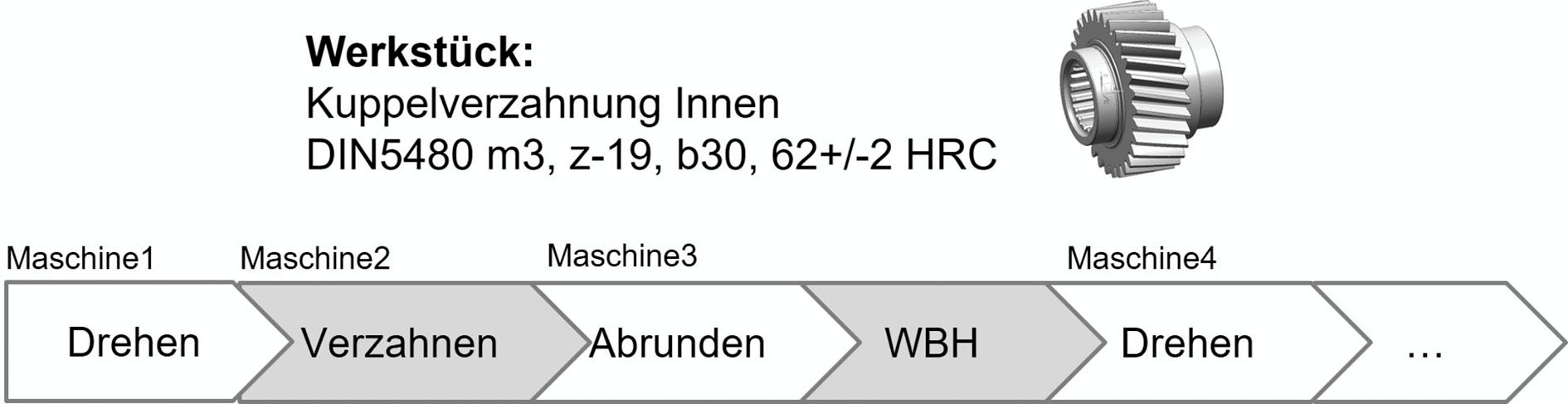
Bild 3. Der Ausgangspunkt der Untersuchungen ist eine sequentielle Prozesskette auf Einzweckmaschinen. Grafik: Sandvik Coromant
Die sequentielle Bearbeitung auf Einzweckmaschinen führte zu einer langen Prozesskette mit hohen Durchlaufzeiten. Die bisher üblichen Fertigungsverfahren für Innenverzahnungen wie Stoßen oder Räumen boten nur bedingt die Möglichkeit der Hartfeinbearbeitung. Durch das Fehlen eines Hartfeinbearbeitungsprozesses war es nicht möglich, die durch die Wärmebehandlung hervorgerufenen Form-, Lage- und Volumenänderungen der Verzahnung zu kompensieren. Darüber hinaus waren diese Geometrieänderungen aufgrund der Vielzahl von Einflussfaktoren nur sehr schwer bis gar nicht vorhersagbar, was eine stabile Vorhaltung extrem erschwerte. Durch die fehlende Hartfeinbearbeitung war die beschriebene Prozesskette qualitätskritisch und der Fertigungsprozess nicht stabil, Bild 3.
„Aufgrund der heutigen Kunden- und Marktanforderungen ist eine kontinuierliche Prozessverbesserung hinsichtlich Kosten, Durchlaufzeit und Qualität unabdingbar. Im dargestellten Beispiel konnten wir durch die Implementierung des Wälzschälens und der damit verbundenen Prozessintegration auf einer Universal-Bearbeitungsmaschine die Prozesskette sowie die Durchlaufzeit deutlich reduzieren, Bild 4“, erklärt Dr. Thomas Glaser, Betriebsingenieur bei Voith Turbo. „Durch die Prozesscharakteristik, geringe Spandicken und hohe Schnittgeschwindigkeiten sowie Hochleistungsschneidstoffe und -beschichtungen, ermöglicht das Wälzschälen zudem eine Hartfeinbearbeitung nach der Wärmebehandlung, wodurch die Bauteilqualität nachhaltig verbessert werden konnte.“
Der neue Bearbeitungsprozess
Entscheidend für einen stabilen Wälzschälprozess ist die Werkzeug- und Prozessauslegung. Im betrachteten Fall wurde ein Wälzschälwerkzeug (CoroMill 178B) für die Vorbearbeitung im weichen Zustand sowie für die Hartfeinbearbeitung im harten Zustand ausgelegt. Für die Vorbearbeitung wurde ein Flankenaufmaß im Werkzeug vorgesehen, die Bearbeitung erfolgte mit einer degressiven Zustell-Strategie in sieben Schnitten, wobei in den letzten beiden Schnitten die Schnittwerte für das Vorschlichten und Schlichten angepasst wurden.
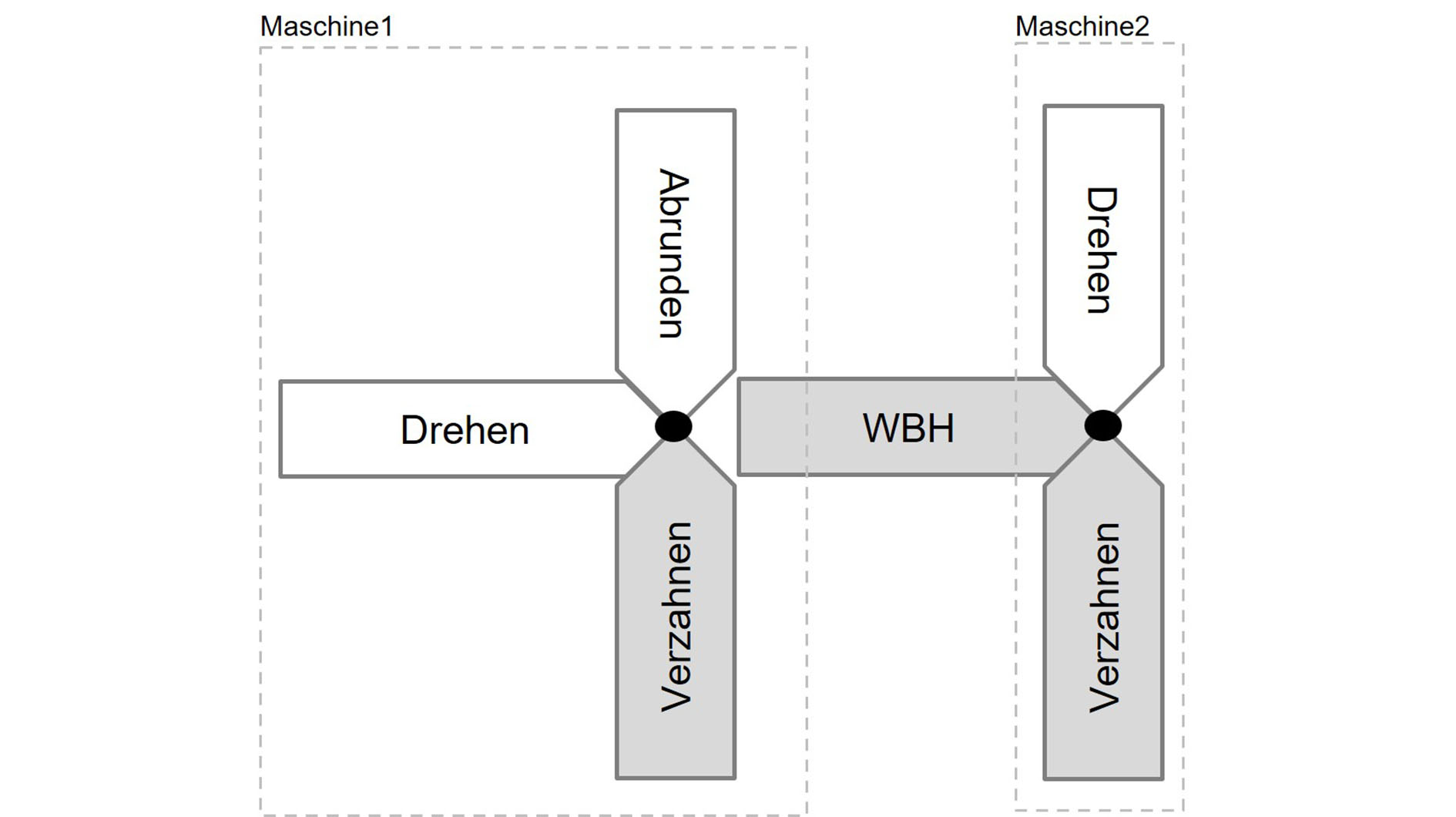
Bild 4. Optimierte kombinierte Prozesskette auf Universal-Bearbeitungsmaschinen. Grafik: Sandvik Coromant
Folgende Schnittwerte wurden verwendet:
- Vc = 100–200 m/min,
- F = 0,2–0,05 pro Werkstück-Umdrehung,
Bei der Hartfeinbearbeitung wurden die Zahnflanken im Einflankenschnitt bearbeitet. Die Bearbeitung wurde in zwei Schnitten durchgeführt, einem Egalisierschnitt und einem Schlichtschnitt. Die Zustellung erfolgte durch rotatives Zustellen des Werkstückes. Die Schnittwerte lagen bei:
- Flankenaufmaß = ~0,1 mm,
- Vc = 60–100 m/min,
- F = 0,025–0,08 pro Wst-Umdrehung.
Von zentraler Bedeutung für die Hartfeinbearbeitung ist die Bestimmung der Zahnlückenposition sowie die Kopplung und Synchronisation der Werkzeugschneidenlage mit dieser Position. Zur Bestimmung der Zahnlückenposition wurde von Voith ein Makro auf der Universal-Bearbeitungsmaschine implementiert, Bild 5.
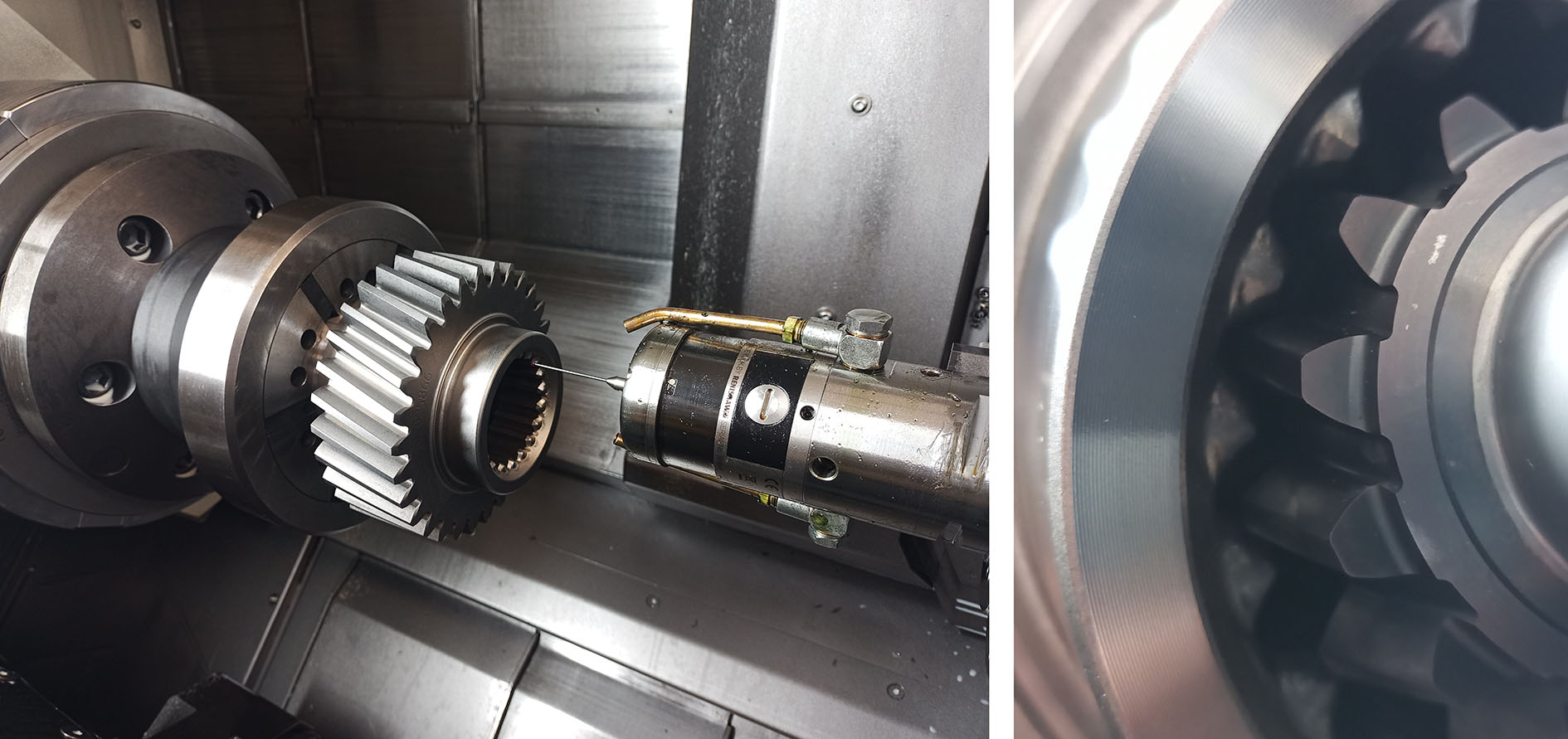
Bild 5. Einmittung auf der Bearbeitungsmaschine (links) und in die Zahnlücke eingemittete Werkzeugschneide (rechts).
Foto: Sandvik Coromant
Überzeugende Ergebnisse
Mit dem eingesetzten Wälzschälverfahren ist Voith Turbo heute in der Lage, die innenverzahnten Kupplungsverzahnungen für die Getriebe von Triebwagen und Lokomotiven auf Universalmaschinen prozesssicher und mit einer sehr hohen Qualität zu fertigen, wie das Prüfprotokoll zeigt, Bild 6. Durch das Wälzschälen ist es auch möglich, die Innenverzahnung nach der Wärmebehandlung auf Endmaß zu fertigen, während bisher die Innenverzahnung vor der Wärmebehandlung fertiggestoßen werden musste, was den Prozess sehr instabil machte. Durch die Prozessintegration auf einer Maschine ergeben sich zudem Durchlaufzeit- und Kostenpotenziale.
„Die Umstellung der Prozesse von der sequentiellen Bearbeitung auf Einzweckmaschinen auf die kombinierte Bearbeitung auf Universal-Bearbeitungsmaschinen verkürzt die Prozesskette und damit die Durchlaufzeit um drei Wochen. Darüber hinaus konnten durch den Einsatz neuer Schneidstoffe und Technologien die Bearbeitungskosten für die Innenverzahnung um 30 bis 50 Prozent gesenkt werden“, bilanziert Dr. Glaser. Tobias Schneider, Werksleiter in Heidenheim, ergänzt: „Die neu eingeführte Hartfeinbearbeitung erhöht zusätzlich die Bauteilqualität und senkt die Qualitätskosten deutlich. Voraussetzung für die erfolgreiche Umsetzung der Wälzschältechnologie ist ein funktionsübergreifendes Prozessverständnis aller Prozessbeteiligten. Auch deshalb freuen wir uns, dass Sandvik Coromant uns auch in Zukunft bei allen Fragen rund um das Wälzschälen zur Seite steht und uns bei der Prozessoptimierung unterstützt.“
Über die Projektpartner
Gegründet 1867, ist die Voith Group heute mit rund 22.000 Mitarbeitenden, 5,5 Milliarden Euro Umsatz und Standorten in über 60 Ländern der Welt eines der großen Familienunternehmen Europas. Der Konzernbereich Voith Turbo ist Spezialist für intelligente Antriebstechnik, Systeme sowie maßgeschneiderte Serviceleistungen. Durch innovative und smarte Produkte bietet Voith beste Effizienz und Zuverlässigkeit. Kunden aus zahlreichen Branchen wie Öl und Gas, Energie, Bergbau und Maschinenbau, Schiffstechnik, Schienen- und Nutzfahrzeuge setzen auf die Spitzentechnologien und digitalen Lösungen.
Sandvik Coromant – Teil des globalen Maschinenbaukonzerns Sandvik – liefert Werkzeuglösungen für die weltweite Maschinenbauindustrie und möchte damit den Weg in eine nachhaltige Zukunft ebnen. Mehr als acht Jahrzehnte praktischer Erfahrung liefern dabei ein umfangreiches Fachwissen in der Zerspanung und Bearbeitung von Metall. Dieses Fachwissen verwandelt jede Herausforderung in eine Chance für Innovation, Zusammenarbeit und fortschrittliche Lösungen.
Das könnte Sie auch interessieren:
Wie Werkzeuge zu einer nachhaltigeren Produktion beitragen
Wie entstehen hochfeste Schrauben für die Endoprothetik?
Diamantschichten nach Maß für hochleistungsfähige Zerspanwerkzeuge
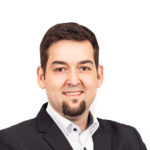
Dr.-Ing. Thomas Glaser ist Betriebsingenieur bei der J.M. Voith SE & CO. KG. Foto: Voith
Jochen Sapparth arbeitet als Project and Sales Engineer für „gear machining solutions“ bei Sandvik Coromant.