Thermisches Fügen von Stahl und Aluminium
Aufgrund moderner Leichtbaukonzepte in der Automobilindustrie hat das thermische Fügen von Stahl und Aluminium in den letzten Jahren zunehmend an Bedeutung gewonnen. In diesem Zusammenhang wurden vermehrt Prozessentwicklungen im Bereich des MSG-Schweißlötens in Kombination mit einem Aluminiumzusatzwerkstoff vorangetrieben.
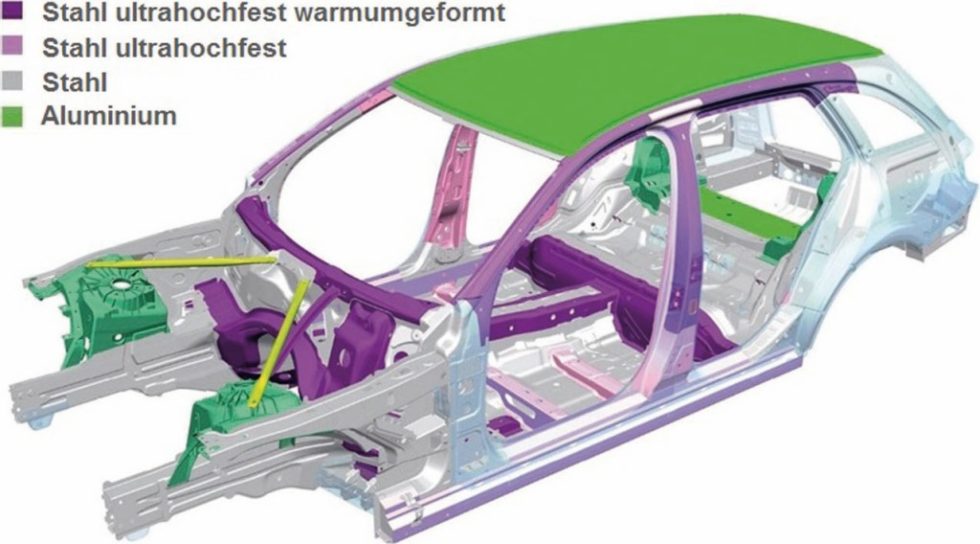
Innovative Hybridkarosserie am Beispiel der „C-Klasse“ von Mercedes-Benz. Bild: Daimler AG
Nachteilig bei dieser Fügestrategie ist die Bildung eines intermetallischen Phasensaums im Bereich der Fügezone aufgrund der sehr unterschiedlichen Werkstoffeigenschaften von Stahl und Aluminium. Dieser Saum ist sehr spröde und kann bei einer überkritischen Ausbildung zu einem frühzeitigen Versagen der Verbindung von Stahl und Aluminium führen.
Um den Herausforderungen beim Fügen zu begegnen, wurde bei der Forschungs- und Entwicklungsgesellschaft Fügetechnik GmbH (FEF) in Kooperation mit dem Institut für Schweißtechnik und Fügetechnik der RWTH Aachen (ISF) eine Fügestrategie entwickelt, welche gezielt die Bildung spröder intermetallischer Phasen im Bereich der Fügezone in Kauf nimmt, wobei deren negativer Einfluss auf die Festigkeitseigenschaften der Verbindung verringert wird. Um dies möglich zu machen, wurde ein niedrigenergetischer Kurzlichtbogenprozess mit einem niedrigschmelzenden Zinkbasislot verwendet.
Ausgangssituation
Aktuelle Leichtbaustrategien zeigen, dass Aluminiumwerkstoffe aufgrund ihres geringen spezifischen Gewichts immer häufiger in modernen Automobilkarosserien eingesetzt werden und somit konventionelle Stähle substituieren.
Beim thermischen Fügen von Werkstoff-Mischverbindungen werden in verschiedenen Anwendungsfällen Zusatzwerkstoffe eingesetzt, welche möglichst artgleich mit einem der beiden Fügepartner sind. In diesem Zusammenhang wird auch beim Fügen von Stahl-Aluminium-Mischverbindungen der Ansatz verfolgt, einen aluminiumbasierten Draht zu verwenden. Dabei wird der Aluminiumwerkstoff aufgeschmolzen, während der Stahlwerkstoff durch das Schmelzbad – ähnlich einer Lötung – lediglich benetzt wird.
Da es bei dieser „Schweißlötung“ dennoch zum Anschmelzen des Stahlblechs kommen kann und die Elemente Eisen und Aluminium bei Raumtemperatur nicht in Lösung gehen, entsteht ein intermetallischer Phasensaum (IMP). Im Fall des Phasensystems Fe-Al bestehen die IMP aus chemischen Verbindungen der Elemente Eisen und Aluminium. Die IMP unterscheiden sich aufgrund ihrer Bindungsarten von gewöhnlichen Metallen in ihren physikalischen und mechanischen Eigenschaften [1].
Die Bildung der IMP kann bei Lichtbogenprozessen nicht verhindert werden, da sie immer auftritt, sobald Fe und Al im schmelzflüssigen Zustand vorliegen, was beim Schweißlöten zu einem gewissen Anteil immer der Fall ist. Diese Phasen haben eine hohe Härte, was gleichzeitig eine geringe Zähigkeit zur Folge hat. Dies führt zu einer Verringerung der Festigkeitseigenschaften der Verbindung [2].
Intermetallische Phasen bilden sich vorwiegend als zusammenhängender Saum an der Oberseite des Stahlblechs. Aufgrund der spröden Struktur können sich Risse schnell entlang dieses Phasensaums verbreiten, sodass Stahl-Aluminium-Mischverbindungen beim Einsatz von Aluminiumzusatzwerkstoffen bereits unter geringen mechanischen Belastungen schlagartig versagen, Bild 1.
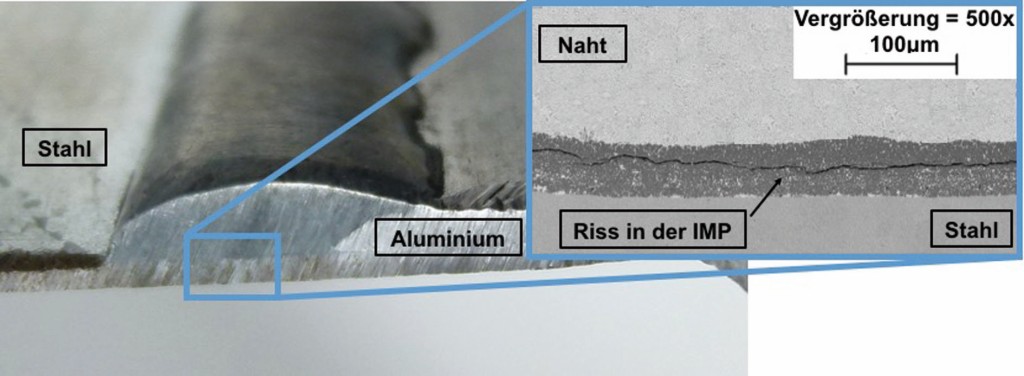
Bild 1. St-Al-Mischverbindung mit Aluminiumzusatzwerkstoff sowie Riss in der intermetallischen Phase. Bild: FEF
Um eine weniger spröde Stahl-Aluminium-Mischverbindung zu erzeugen, wird in [3] eine Phasensaumdicke unter 10 μm empfohlen, wobei der Grad der Ausbildung direkt von der Energieeinbringung durch das Fügeverfahren in die Prozesszone abhängt.
Zur Sicherstellung einer Phasensaumdicke kleiner 10 µm sind nach heutigem Stand der Technik nur zerstörende Prüfmethoden einsetzbar. So ist im Anschluss an das Fügen von Stahl-Aluminium-Mischverbindungen eine Vorhersage der möglichen mechanischen Belastbarkeit der Verbindung mit zerstörungsfreien Prüfmethoden nur mit einer großen Unsicherheit möglich. Diese vor allem die Qualitätssicherung betreffenden Herausforderungen erschweren einen industriellen Einsatz dieser Technologie.
Vorgehensweise und Ergebnisse
Um den negativen Einfluss der entstehenden intermetallischen Phasen auf die Festigkeitseigenschaften der Fügeverbindung zu verringern oder sogar zu eliminieren, wurde die Strategie verfolgt, beim thermischen Fügen von Stahl und Aluminium anstelle eines artgleichen Aluminiumzusatzwerkstoffs einen Draht auf Basis von Zink zu verwenden.
Alternativer Zusatzwerkstoff auf Zinkbasis
Zink hat einen deutlich tieferen Schmelzpunkt (circa 420 °C) als Stahl (1400 °C) und Aluminium (660 °C). Daraus folgt, dass für das thermische Fügen unter Verwendung von Zinkbasisloten geringere Prozesstemperaturen und somit auch eine geringere Energieeinbringung in die Fügezone nötig sind, sodass die Bildung von IMP reduziert wird. Zudem verbleibt der zinkbasierte Zusatzwerkstoff länger im flüssigen Zustand als die Aluminiumschmelze. So kommt es zu der Besonderheit, dass die bereits erstarrten Phasen von noch flüssiger Zinkschmelze durchdrungen und geteilt werden.
Zusätzlich haben die Phasen eine geringere Dichte als der flüssige Zinkwerkstoff, sodass diese – unterstützt durch die Fluiddynamik des Schmelzbads – von der Stahloberfläche abgelöst werden und im noch flüssigen Zinkwerkstoff aufschwimmen. Daraus resultiert, dass nach der vollständigen Erstarrung kleine Phaseinseln in einer duktileren Zinkmatrix eingelagert sind. Dieser Effekt führt dazu, dass das spröde Werkstoffverhalten von Stahl-Aluminium-Mischverbindungen reduziert wird.
Energiearmen Schweißprozess nutzen
Ein weiterer Aspekt der verfolgten Strategie zur Reduzierung der Energieeinbringung in die Fügezone ist die Verwendung eines energiearmen, digital geregelten Kurzlichtbogenschweißprozesses, in diesem Fall des CMT (Cold Metal Transfer)-Prozesses. Die Besonderheit dieses Prozesses liegt darin, dass die Stromquelle den Kurzschluss zwischen aufgeschmolzenem Zusatzwerkstoff und dem Schmelzbad erkennt und die Stromstärke entsprechend auf ein sehr niedriges Niveau reduziert. Somit entsteht ein vergleichsweise kalter Tropfen an der Drahtspitze. Der Materialübergang des Zusatzwerkstoffs in das Schmelzbad geschieht nahezu stromlos. Der Tropfenübergang wird zusätzlich von einer Rückbewegung des Drahtendes mechanisch unterstützt, welche durch einen Servomotor am Brenner möglich wird.
Um die Energiezufuhr in die zu fügenden Stahl- und Aluminiumbleche zum Teil unabhängig von der Drahtvorschubgeschwindigkeit des CMT-Prozesses zu gestalten, wurde ein WIG (Wolfram-Inertgas)-Brenner als zusätzliche Wärmequelle vor den CMT-Brenner geschaltet. Auf diese Weise war es möglich, verschiedene Energiebereiche und somit unterschiedliche zur vollständigen Erstarrung der Naht nötige Zeitintervalle für gleiche Drahtfördergeschwindigkeiten zu untersuchen, Bild 2.
Mit dieser Vorrichtung konnte auch ein gezielt längeres Halten der Schmelze in einem gewissen Temperaturintervall zur gewünschten Ausbildung der intermetallischen Phasen realisiert werden.
Geeignete Prozessführung
Der WIG-Brenner wurde ohne Zusatzwerkstoff eingesetzt und erlaubte durch Einstellung von niedrigen Stromstärken eine direkte Beeinflussung der in die Fügezone eingebrachten Energie. Basierend auf den gewonnenen Erkenntnissen unter Zuhilfenahme des WIG-Prozesses wurden im Anschluss mehrere Prozessparameter in der Programmierebene der Stromquellenkennlinie des CMT-Prozesses modifiziert. In diesem Zusammenhang ließen sich die Kennlinienparameter so anpassen, dass der CMT-Prozess ausreicht, um Stahl und Aluminium unter Verwendung von Zinkbasisloten prozesssicher zu fügen.
Mithilfe der entwickelten Fügestrategie konnten Stahl-Aluminium-Mischverbindungen mit Grundwerkstofffestigkeiten unter Verwendung eines zinkbasierten Zusatzwerkstoffs hergestellt werden. Für diese Materialkombination wurde der Einfluss der Prozessparameter auf das Fügeergebnis soweit analysiert und bewertet, dass sich die gewünschte Phasenablösung prozesssicher einstellen lässt. Die aus der Prozessführung resultierende Phasenverteilung in der Naht einer Stahl-Aluminium-Mischverbindung ist in Bild 3 dargestellt.
Das Bild zeigt, dass kein spröder zusammenhängender Phasensaum vorliegt, sondern eine statistische Verteilung von Phaseinseln – bis zu einem Abstand von 330 µm von der Stahloberfläche entfernt.
Fein verteilte Phase in duktilerer Zink-Matrix
Bei der sich während des Fügeprozesses ausgebildeten IMP wird ab einer kritischen Dicke eine Rissausbildung initiiert, welche zum Aufbrechen des Phasensaums führt. In die aufgerissenen Bereiche der Phase fließen Teile der Zinkschmelze aus dem Schweißzusatzwerkstoff ein, wodurch die IMP eine Phasenumwandlung hin zu Bereichen weniger kritischer beziehungsweise spröder Zusammensetzungen durchläuft. Durch die sich ergebende Dichteänderung bei dieser Phasenumwandlung erfährt die neue Phase eine Auftriebskraft und verteilt sich über die Höhe der Naht. Diese feine Verteilung der IMP führt dazu, dass die teilweise vorhandenen negativen Einflüsse der spröden IMP durch die Einbindung in die duktilere Zink-Matrix kompensiert werden können.
Erreicht wird dieses Ziel durch eine gezielt gesteuerte Temperaturführung während des Prozesses. Die gewünschte Verteilung der IMP über den gesamten Nahtbereich wird durch eine Ausdehnung des Abkühlintervalls der Schweißnaht im Bereich von 550 °C bis 380 °C erreicht. Für dieses Temperaturfenster wurde das Ablaufen der für eine Ablösung des intermetallischen Phasensaums vom Stahlblech relevanten Phasenumwandlungen identifiziert. Prozesstechnisch wird dieses Ziel durch eine gezielte Wärmeführung und eine geänderte Wärmeabfuhr aus dem Prozessbereich erreicht.
Um die Potentiale des energiearmen Fügens von Stahl und Aluminium unter Einsatz von Zinkbasisloten zu veranschaulichen und auf eine reale Anwendung zu übertragen, wurde ein Demonstratorbauteil hergestellt. Als möglicher Anwendungsbereich in der Automobilindustrie wurde die Verbindung einer Dachschiene aus einem hochfesten Stahlwerkstoff an ein Dachblech aus Aluminium identifiziert und in Form des Demonstrators realisiert, Bild 4.
Die Nahtoberflächen zeigen eine ansprechende Nahtoptik, welche auch für den Einsatz im Sichtbereich geeignet ist.
Fazit und Ausblick
Anhand der Untersuchungen und des gefertigten Demonstratorbauteils konnte gezeigt werden, dass Stahl-Aluminium-Mischverbindungen prozesssicher thermisch gefügt werden können. In Kooperation zwischen der FEF und dem ISF der RWTH Aachen wurde eine Fügestrategie entwickelt, welche eine statistische Verteilung von spröden intermetallischen Phaseinseln im Nahtquerschnitt erlaubt. Auf diese Weise wird der negative Einfluss von spröden IMP unter Verwendung eines Zinkbasiszusatzwerkstoffes entschärft. Weitere Untersuchungen sollen den Prozess für den industriellen Einsatz ertüchtigen.
Literatur:
[1] Gottstein, G.: Physikalische Grundlagen der Materialkunde. Heidelberg: Springer-Verlag, 2007.[2] Radscheit, C.R.: Laserstrahlfügen von Aluminium mit Stahl. Bremen: BIAS, 1997.[3] Schmid, D.: Rührreibschweißen von Aluminiumlegierungen mit Stählen für die Automobilindustrie. München: Herbert Utz Verlag, 2014.
Dipl.-Ing. Matthias Angerhausen, Jahrgang 1983, studierte Maschinenbau an der RWTH Aachen. Seit Januar 2017 ist er als Vertriebsleiter bei der Forschungs- und Entwicklungsgesellschaft Fügetechnik GmbH (FEF) in Aachen tätig. // Dipl.-Ing. Christoph Geffers, Jahrgang 1977, studierte Maschinenbau an der RWTH Aachen. Seit Oktober 2012 ist er als Leiter Industrial Services and Solutions bei der FEF tätig. // Dipl.-Ing. Alexandros Pipinikas, Jahrgang 1976, und Thorsten Twiehaus, M.Sc., Jahrgang 1991, studierten Maschinenbau an der RWTH Aachen. Beide sind als Projektleiter bei der FEF tätig.