Schweißanweisungen softwaregestützt automatisiert erstellen
Für die Inbetriebnahme und Kontrolle von Roboterschweißanlagen sind hochqualitative Schweißanweisungen unabdingbar. Bisher ist hier der Erfahrungsschatz von Schweißexperten gefragt. Auf der Grundlage von standardisierten Prozessen wird es nun möglich, die Schweißparameterapplikation nachverfolgbar umzusetzen.
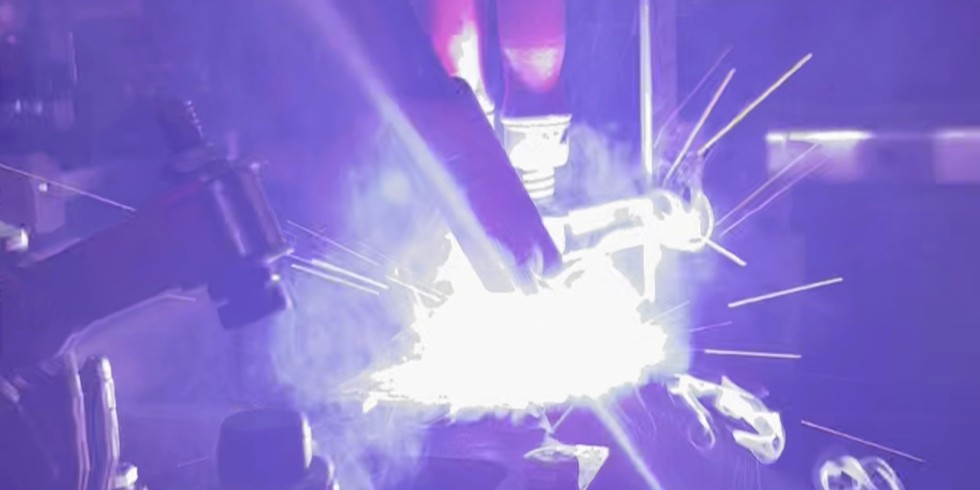
Die Ermittlung geeigneter Schweißparameter hängt bisher vom Erfahrungsschatz des Schweißexperten ab. Mit Hilfe einer programmierten Software wird die automatisierte Verarbeitung gesammelter Messwerte möglich – auch im zeitsensitiven Umfeld einer Maschineninbetriebnahme.
Foto: Strutz
Mit dem Inkrafttreten der DIN EN 1090 sind Hersteller von Stahl-, Edelstahl- und Aluminiumtragwerken forciert gefordert, werkseigene Produktionskontrollen durchzuführen und die damit verbundenen Schweißanweisungen (WPS – Welding Procedure Specifications) zu erstellen. Beim automatisieren Schweißen muss hierbei die Vorrichtung, der Roboter und die genauen Schweißparameter dokumentiert werden.
Insbesondere bei der Inbetriebnahme von komplexen Sondermaschinen führt dies zu mangelhaften und schlecht dokumentierten Optimierungsprozessen der Schweißparameter. Die Applikation dieser Daten findet meist im letzten Schritt der Inbetriebnahme statt und ist deshalb durch den Termindruck des Projekts geprägt. Das Evaluieren eines globalen Optimums wird hierdurch zumeist nur mangelhaft dokumentiert. Dieser Artikel widmet sich einer softwaregestützten Methodik zur Parameterapplikation mit automatischer Erstellung einer WPS.
Parametergenerierung
Für die Parametergenerierung werden der Drahtvorschub, die Schweißgeschwindigkeit und die Brennerposition bei leicht stechendem Brenneranstellwinkel variiert [1]. Hierfür wird das „Latin Hypercube Sampling“ (LHS) verwendet, um die Versuchspunkte gleichmäßiger zu verteilen als bei einer rein zufällig gewählten Verteilung. Der gesamte Wertebereich jeder Eingangsvariablen wird in Intervalle unterteilt und aus jedem Parameterbereich wird zufällig der Wert einer Eingangsvariablen ausgewählt – es entsteht ein Parametersatz ohne Zusammenhang der einzelnen Eingangsvariablen. Das Ergebnis ist eine Normalverteilung über alle Eingangsvariablen, wodurch Optima schneller gefunden werden als beim klassischen Design of Experiments [2; 3]. Zudem erhält jede Probe eine eindeutige ID, welche das Bauteil durch den gesamten Prozess begleitet.
Schweißvorgang und Parameterapplikation
Der Anschluss des Roboters erfolgt über eine Profinet-Schnittstelle (oder Ähnliches), sodass die Schweißparameter für den Roboter zugänglich sind. Da es sich um eine große Parametervariation handelt, wird die LHS-Matrix in eine ASCII-Datei exportiert und an die Robotersteuerung übertragen.
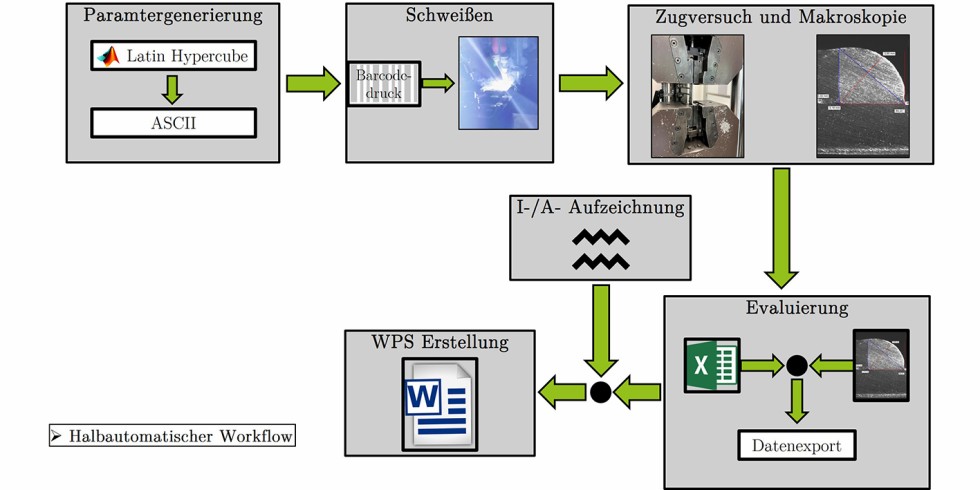
Abbildung 1: Darstellung des grafischen User-Interfaces und des Ablaufs für die softwaregestützte WPS (Welding Procedure Specifications)-Erstellung. Grafik: Strutz
Jede Probe erhält vor dem Einlegen in die Schweißvorrichtung ein Etikett mit den zugehörigen Schweißparametern in Klartext. Zusätzlich ist auf dem Etikett ein Barcode aufgebracht. Ziel ist es, die Bewertung jeder einzelnen Probe verwechslungssicher durchzuführen und vor der Evaluierung einzuscannen. Die Benutzeroberfläche und der Workflow sind in Abbildung 1 dargestellt.
Da es sich in den in den nachfolgenden Messungen um zerstörende Prüfungen handelt, ist das Anfertigen von mehreren Proben (mit jeweils eigener ID) unerlässlich.
Makroskopische Untersuchung
Im ersten Schritt findet das Trennen der Proben wie im gewohnten Ablauf statt. Vor dem Einlegen wird der Barcode der Probe gescannt, wodurch der Dateiname des makroskopischen Untersuchungsbildes mit „ID_ WireFeed_Pos_Speed“ benannt wird. Die Platzhalter werden entsprechend der ASCII-Tabelle mit den jeweiligen Parametern ersetzt.
Die Messung wird mit Hilfe einer automatischen Kantenerkennung nach dem „Canny-Algorithmus“ ausgewertet.
In Abbildung 2 ist die makroskopische Untersuchung einer Kehlnaht dargestellt. Hierbei ist das Ergebnis der Kantendetektion auf der linken Seite zu sehen. Anschließend wird die Auswertung mit Hilfe der Hough-Transformation durchgeführt. Dies ist ein Algorithmus zur Erkennung von geometrischen Formen. Auf der rechten Seite von Abbildung 2 ist die fertige makroskopische Untersuchung mit den drei Kenngrößen a-maß, Spalt zwischen den Blechen und Überwölbung der Kehlnaht dargestellt.
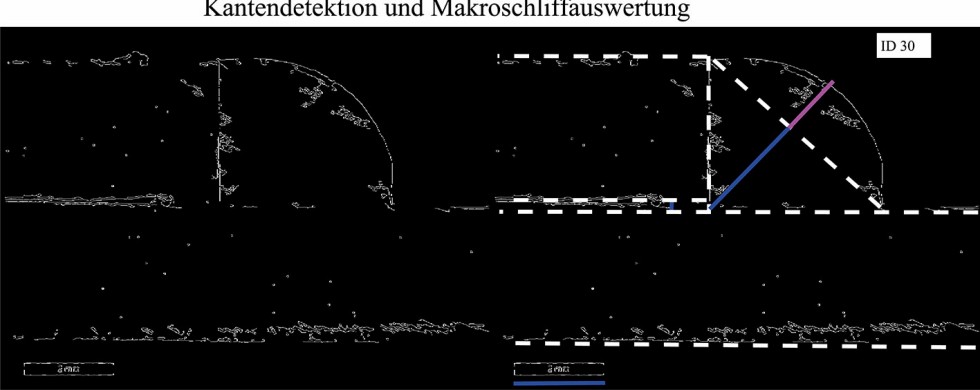
Abbildung 2: Makroschliffauswertung. Links ist die unbearbeitete Kantenerkennung und rechts die Auswertung zu sehen. Grafik: Strutz.
Um die erkannten Kanten auf die gewünschten Geraden zu beschränken, werden zwei weitere Filter angewendet: Erstens wird die Position für die zu erkennenden Kanten begrenzt. Für jeden Teil des Bildes gibt es einen Bereich von Interesse (ROI), in dem nach der erwarteten geraden Linie gesucht werden soll. Dies ist nur möglich durch die festen Anschläge am Mikroskop und an der Trennmaschine. Andererseits ist der Wert des Linienwinkels begrenzt. In Abbildung 3 kann der Effekt an Abbildung 2 bewertet werden. Die Farbe stellt dabei die Kantenintensität dar.
Härteverlaufsmessung
Die Härteverlaufsmessung bei einer WPS dient der Überprüfung von Gefügeveränderung durch die schroffe Abkühlung der erhitzten Bereiche um die Schweißnaht – die sogenannte Wärmeeinflusszone. Für eine valide Härteverlaufsmessung müssen mindestens zehn gleichmäßig verteilte Messungen durchgeführt werden. Dabei müssen in den fünf Teilbereichen mindestens je zwei Messpunkte liegen, namentlich: Grundwerkstoff 1, Wärmeeinflusszone 1, Schweißnaht, Wärmeeinflusszone 2 und Grundwerkstoff 2. Mit Hilfe des grafischen User-Interface folgt die Eintragung der Messwerte ebenfalls ID-bezogen, da auch hier der Barcode vor der Messwerteintragung gescannt werden muss.
Zugversuch
Bei der Zugprüfung werden die Schweißverbindungen einer quasi-statischen Belastung ausgesetzt, um die Verbindung auf ihre mechanische Festigkeit zu prüfen.
Eine gängige Zugprüfmaschine eignet sich durch den in der Regel verwendeten Computer ideal für ein Makro zur Auswertung der Ergebnisse. Aufgrund der Kennzeichnung mittels Barcode müssen die Proben nicht in der richtigen Reihenfolge geprüft werden. Die ermittelten Werte aus dem Zugversuch werden dann chronologisch in einer csv-Datei gespeichert und in die Software eingelesen.
Fazit
Die Ermittlung von geeigneten Schweißparametern ist in den meisten Fällen durch den Erfahrungsschatz des Schweißexperten geprägt. Mit Hilfe der programmierten Software ist es möglich, die gesammelten Messwerte prozess- und verwechslungssicher zu verarbeiten und das globale Optimum der Prozessparameter zu eruieren – auch im zeitsensitiven Umfeld einer Maschineninbetriebnahme. Abschließend folgt die Erstellung einer normgerechten WPS „auf Knopfdruck“ in der übersichtlichen Benutzeroberfläche in einer Word Datei.
Literatur
- Cho, Y. H. et al. Effect of torch angle and position on bead geometry and joint strength during arc brazing of thin-gauge dual-phase steel. The International Journal of Advanced Manufacturing Technology 121.1, S. 543–557.
- Mckay, M; Beckman, R; Conover, W: A Comparison of Three Methods for Selecting Vales of Input Variables in the Analysis of Output From a Computer Code. Technometrics 21, S 239–245.
- Aistleitner, C; Hofer, M; Tichy, R: A central limit theorem for Latin hypercube sampling with dependence and application to exotic basket option pricing. International Journal of Theoretical and Applied Finance 15.
Das könnte Sie auch interessieren:
Maschinelles Lernen in der Prozessplanung
Wie funktioniert „Sandstrahlen“ mit Licht?
Ultraschallschweißen unterstützt Innovationen in der Automobilindustrie
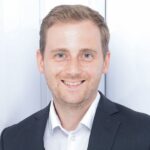
Josip Florian Strutz, M.Eng., ist seit 2020 Doktorand an der Josip Juraj Strossmayer Universität in Slavonski Brod (Kroatien) an der Fakultät für Maschinenbau. Foto: Autor
Ivan Samardžic, Prof. Dr. sc., ist Rektor an der Josip Juraj Strossmayer Universität in Slavonski Brod (Kroatien) an der Fakultät für Maschinenbau.