Maschinelles Lernen in der Prozessplanung
Formfehler aus der spanenden Bearbeitung können zu aufwendigen Nacharbeiten und sogar kostspieligem Ausschuss führen. Gezeigt wird, wie sich mit automatisiertem maschinellen Lernen der Verschleiß und die Formabweichungen vorhersagen lassen.
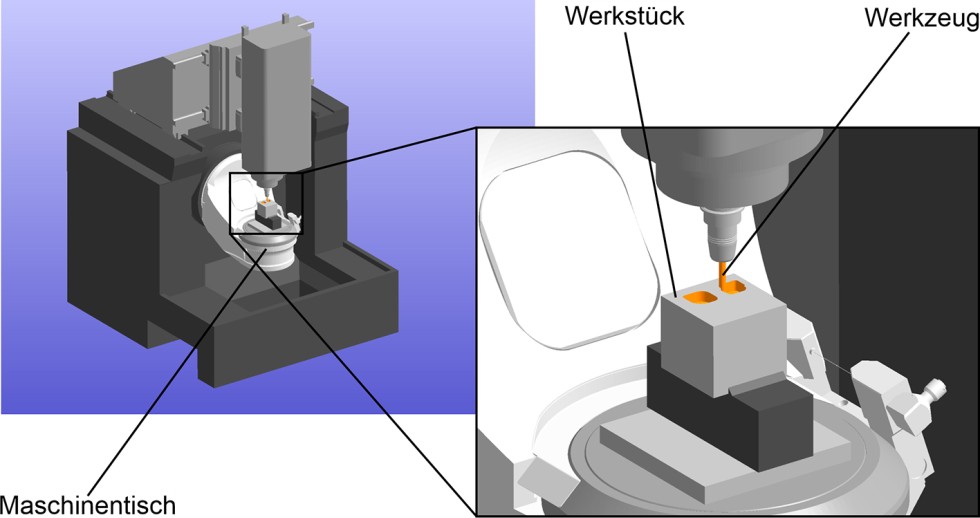
Simulation der Maschinenkinematik und der Eingriffsbedingungen: Prognosemodelle auf Basis maschinellen Lernens helfen, Fertigungsprozesse im sensiblen Werkzeug- und Formenbau zu optimieren. Grafik: IFW
Formfehler beschreiben ungewollte Konturabweichungen, die während der spanenden Bearbeitung auftreten. Diese Fehler sind als Abweichung der maximal tolerierten Sollkontur von der realen Kontur des gefertigten Bauteils definiert. Im Folgenden wird gezeigt, wie anwendungsfreundliches maschinelles Lernen (ML) die Formabweichungen – auch unter Berücksichtigung des Verschleißes – bereits vor der Prozessdurchführung vorhersagen kann. Als Beispielbranche dient der Formen- und Werkzeugbau aufgrund der Komplexität der dort gefertigten Bauteile.
Kostenintensive Bauteile im Werkzeug-/Formenbau wirtschaftlicher herstellen
Der Werkzeug- und Formenbau umfasst in der Regel eine Einzelteilfertigung von individuellen Bauteilen mit hochkomplexen Geometrien. Die dafür nötige spanende Bearbeitung der Werkstücke bedarf einer aufwendigen Prozessplanung und -durchführung, um den hohen Qualitätsansprüchen der Kunden gerecht zu werden. Darüber hinaus verbieten die hohen Kosten der Rohteile und Werkzeuge in der Regel einen Einfahrprozess für die jeweiligen Aufträge. Daher werden häufig konservative Prozessstellgrößen auf der Basis von Erfahrungswerten gewählt, um Fehler zu vermeiden. Hierbei werden Abstriche in der Produktivität bewusst in Kauf genommen.
Die Auswahl dynamischerer Prozessstellgrößen ist wirtschaftlicher, birgt jedoch ein erhöhtes Fehlerpotenzial bei unbekannten Wirkzusammenhängen. Daher ist eine möglichst genaue Modellierung des Prozessverhaltens erforderlich, um die Vorhersagbarkeit der Formabweichung auf Grundlage von Prozessstellgrößen wie zum Beispiel Schnittgeschwindigkeit, Vorschub, Schnitttiefe und Schnittbreite zu verbessern. Zu diesem Zweck werden in diesem Beispiel Methoden des maschinellen Lernens als Verfahren verwendet, da sie die komplexen Zusammenhänge aufwandsarm in ein vereinfachtes mathematisches Modell überführen können.
Anwendungsbeispiel bewährt sich als Prognosemodell
Als Anwendungsbeispiel aus dem Werkzeug- und Formenbau wurde am Institut für Fertigungstechnik und Werkzeugmaschinen (IFW) der Leibniz Universität Hannover ein repräsentatives Bauteil mit Taschen gefertigt, welches sich durch wechselnde Eingriffsbedingungen im Zerspanungsprozess auszeichnet. In diesen Taschen wurde an verschiedenen Stellen der Formfehler als Zielgröße durch den maschinenintegrierten Messtaster aufgenommen. Im weiteren Verlauf soll gezeigt werden, dass der Formfehler durch das hier vorgestellte Modell bereits in der Prozessplanung prognostiziert werden kann. Mittels dieser Prognosen können im Rahmen der Fertigungsplanung Anpassungen der Stellgrößen zur Vermeidung von Formabweichungen erfolgen.
Das Prognosemodell benötigt Trainingsdaten, durch die es angelernt und daraufhin zur Vorhersage von neuen Daten verwendet werden kann. Da die Prozesskräfte von komplexen Eingriffsbedingungen abhängig sind, wird der Zerspanungsprozess mittels einer Materialabtragssimulation in der Software IFW CutS [1] abgebildet. Mit der NC-Simulation können, wie in Abbildung 1 erkennbar, ortsaufgelöst Eingriffsbedingungen berechnet werden. Zu diesen gehören zum Beispiel die Schnitttiefe, die Schnittbreite und das Zeitspanvolumen. Zusammen mit den gemessenen Formfehlern aus der Qualitätssicherung kann so ein Datensatz erstellt werden, mit welchem das Modell durch maschinelles Lernen trainiert wird.
Die Machine-Learning-Pipeline
Obwohl mit dem Einsatz des maschinellen Lernens eine aufwendige analytische Modellierung oder eine rechenintensive numerische Simulation umgangen werden kann, ist das Erstellen des Prognosemodells mit anderen Herausforderungen verbunden. Das Vorgehen von der Datengenerierung bis zum fertigen Prognosemodell wird in der „Machine-Learning-Pipeline“ zusammengefasst (siehe Abbildung 2).
Zunächst werden die generierten Datensätze, die meist in verschiedenen Dateiformaten vorliegen und aus unterschiedlichen Quellen stammen, aufbereitet. Dabei werden zum Beispiel unvollständige Daten entfernt, die später bei der Modellgenerierung zu Problemen führen können. Zur Vorverarbeitung gehören darüber hinaus noch weitere Schritte, wie zum Beispiel die Normierung der Daten.
Mittels der üblicherweise manuell durchgeführten Merkmalsextraktion wird untersucht, welche Merkmale (in diesem Kontext z. B. Schnittgeschwindigkeit oder Zahnvorschub) einen hohen Einfluss auf die Zielgröße haben. Dies kann zum Beispiel durch eine entsprechende Korrelationsanalyse oder eine Hauptkomponentenanalyse durchgeführt werden. Das Ziel ist es, nur entscheidende Merkmale für die Modellerstellung zu verwenden, um den Rechenaufwand zu minimieren.
Letztendlich wird das Modell trainiert und dann gegebenenfalls im Rahmen der Nachbearbeitung mit anderen Modellen zur Verbesserung der Prognosegüte kombiniert (Ensembling). All diese Schritte benötigen jeweils Erfahrung und Wissen, sowohl in den Bereichen der Informatik, als auch hinsichtlich der zugrunde liegenden fertigungstechnischen Sachverhalte des Anwendungsfalls. Zur Umsetzung in Unternehmen fehlen häufig die Kenntnisse über die effiziente Implementierung der vorgestellten manuellen Machine-Learning-Pipeline. Daher bietet sich automatisiertes maschinelles Lernen (AutoML) an, um die beschriebene Anwendungsentwicklung zu unterstützen und zu automatisieren [2]. Dies soll es auch Anwendern ohne tiefgründiges Wissen im Bereich des maschinellen Lernens ermöglichen, dieses anzuwenden und die Qualität der Vorhersagen zu verbessern.
Automatisiertes maschinelles Lernen entlastet den Anwender
Um nun festzustellen, wie gut das Modell den Formfehler in der Zerspanung vorhersagt, wurde das Analogiebauteil wiederholt gefertigt und gemessen. So konnte der tatsächlich vorliegende Formfehler mit den Prognosen des Modells verglichen werden, um den Prognosefehler zu bestimmen (siehe Abbildung 3). Die einzelnen Fehlerwerte werden dann zur Berechnung der globalen Prognosegüte verwendet. Dabei ist der „Root-Mean-Square Error“ (RMSE) eine gängige Metrik zur Quantifizierung der Prognosegüte, wobei ein geringer RMSE eine hohe Prognosegüte darstellt.
In Abbildung 4 sind verschiedene gängige Verfahren des maschinellen Lernens hinsichtlich ihrer Prognosegüte abgebildet. Zudem sind für jede ML-Methode drei verschiedene Merkmalszusammensetzungen gewählt worden, welche wie folgt aufgebaut sind:
- Ohne Berücksichtigung des Verschleißes: Es wurden lediglich die simulierten Eingriffsbedingungen, wie Schnitttiefe, Schnittbreite, Zeitspanvolumen, Geschwindigkeit und Beschleunigung des Werkzeuges sowie der Umschlingungswinkel des Werkzeugeingriffes berücksichtigt.
- Berücksichtigung des Verschleißes mittels Simulationsdaten: Zu der oben genannten Merkmalszusammensetzung wurde das vom Werkzeug zerspante Volumen zum Zeitpunkt des jeweiligen Simulationsschrittes als zeitabhängige Ersatzgröße des Verschleißes ergänzt.
- Berücksichtigung des Verschleißes mittels Verschleißmessung: Als Ergänzung der ersten Merkmalszusammensetzung wurde der Verschleiß nicht als Ersatzgröße, sondern als lichtmikroskopisch bestimmte Verschleißmarkenbreite der Freifläche berücksichtigt.
Grundsätzlich ist festzustellen, dass unabhängig von der verwendeten Merkmalszusammensetzung eine erhebliche Verbesserung der Prognosegüte durch die Verwendung von AutoML feststellbar ist. Als Referenz wurde dabei eine nicht optimierte „Support-Vector-Machine“ (SVM) verwendet, die zum Vergleich zudem einer Hyperparameteroptimierung (HPO) und einer Datenvorverarbeitung (HPO & prepro) unterzogen wurde, welche die Ergebnisse bereits erheblich verbesserten. Eine weitere Steigerung der Prognosegüte ist durch den Einsatz von AutoML sowohl mit als auch ohne anschließendes Ensembling festzustellen.
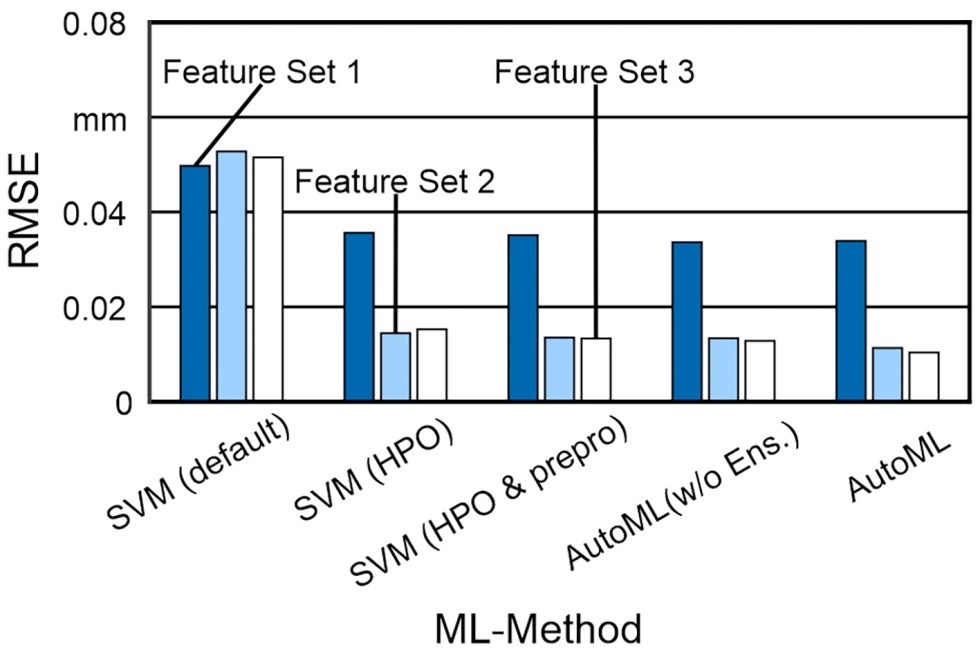
Prognosegüte der Methoden des maschinellen Lernens mit jeweiliger Variation der verwendeten Vorhersagemerkmale. Grafik: IFW
Ergebnis: Machine-Learning-Methoden bieten große Chancen
Hinsichtlich der zugrunde liegenden Merkmale ist in Abbildung 4 zu erkennen, dass die Berücksichtigung des Verschleißes allein durch zeitabhängige Simulationsdaten, wie dem Spanvolumen möglich ist. Hieraus resultiert eine erhebliche Optimierung der Vorhersagegüte, die sich auch nicht signifikant durch die Berücksichtigung von empirisch gemessenen Verschleißwerten verbessern lässt. Hiermit konnte gezeigt werden, dass AutoML, sowohl die Vorteile einer verbesserten Vorhersagegüte, als auch eine vereinfachte Anwendung von ML-Methoden zulässt und daher ein hohes Potential bezüglich der industriellen Anwendung birgt.
Zudem wurde gezeigt, dass sich die Auswirkungen des Werkzeugverschleißes auf den Formfehler bereits vor der Prozessdurchführung in der Prozessplanung berücksichtigen lassen. Insbesondere im Formen- und Werkzeugbau und in Bereichen der Einzelteilfertigung, bei denen kein Einfahrprozess möglich ist, kann dieses Vorgehen zur Vermeidung von Ausschuss und Qualitätsabweichungen verwendet werden. Zudem können Werkzeuge durch die Simulation der Einsatzbedingungen, bis zu ihrem qualitätsspezifischen Standzeitende genutzt werden und müssen nicht schon zuvor aus Sicherheitsgründen ausgetauscht werden.
Positives Fazit – gute Zukunftsperspektiven
Zusammenfassend kann also gesagt werden, dass die Anwendungsexpertise für die Merkmalsauswahl in Kombination mit effizientem automatisiertem maschinellen Lernen (AutoML) zu einer substantiellen Verbesserung der Vorhersage von Formfehlern im Zerspanungsprozess führt. Diese Vorhersagen können genutzt werden, um Qualitätsabweichungen im Prozess zu vermeiden und die Wirtschaftlichkeit der Produktion zu steigern.
Mit Hinblick auf eine Umfrage der WGP (Wissenschaftlichen Gesellschaft Produktionstechnik) bezüglich des „Industriearbeitsplatzes 2025“ gewinnen diese Ergebnisse an Bedeutung. So ergab die Umfrage unter 120 Unternehmen, dass ca. 70 Prozent der Befragten die Adaption von Prozessparametern anhand von Maschinen- und Bauteildaten als eine zukünftige Anforderung an die Maschinenbediener/-innen sieht. Eine Automatisierung dieser Aufgabe könnte Unternehmen zukünftig helfen, diese Herausforderung zu meistern [3].
Literatur
- Böß, V., Denkena, B., Breidenstein, B., Dittrich, M.-A., Nguyen, H. N.: Improving technological machining simulation by tailored workpiece models and kinematics. Procedia CIRP 82 (2019), S. 224–230
- Feurer, M., Eggensperger, K., Falkner, S., Lindauer, M., Hutter, F.: Auto-Sklearn 2.0: The Next Generation, 2020, http://arxiv.org/pdf/2007.04074v1
- Behrens, B.-A., Groche, P., Krüger, J.,Wulfsberg, J. P.: WGP-Standpunkt Industriearbeitsplatz 2025, 2018, https://wgp.de/wp-content/uploads/FINAL_WGP_Standpunkt_2025.pdf
Das könnte Sie auch interessieren:
Werkzeuge werden produktiver und nachhaltiger
Virtuelle Inbetriebnahme steigert Verfügbarkeit von Werkzeugmaschinen
Nachhaltige Automation im Werkzeugmaschinenbau
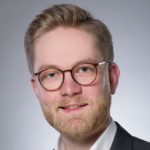
Lukas Stürenburg, M. Eng. studierte Verbundwerkstoffe an der Privaten Hochschule Göttingen und Maschinenbau an der Jade Hochschule Wilhelmshaven und ist seit 2020 wissenschaftlicher Mitarbeiter am Institut für Fertigungstechnik und Werkzeugmaschinen (IFW) am Produktionstechnischen Zentrum der Leibniz Universität Hannover. Foto: IFW
Berend Denkena, Prof. Dr.-Ing., leitet seit 2001 das IFW.
Marius Lindauer, Prof. Dr. rer. nat., ist seit 2019 Professor für Maschinelles Lernen am Institut für Informationsverarbeitung (TNT) der Leibniz Universität Hannover.
Marcel Wichmann, M. Sc. studierte Maschinenbau an der Hochschule Emden/Leer sowie Produktion und Logistik an der Leibniz Universität Hannover und ist seit Juli 2021 Bereichsleiter für Produktionssysteme am IFW.