Produktivitätssteigerung in der Carbonfaserherstellung
Trotz des herausragenden Leichtbaupotentials werden Carbonfasern heutzutage kaum in Massenanwendungen eingesetzt. Die Hauptursache hierfür ist der hohe Preis von 15 – 25 Euro/kg, der im energie- und damit kostenintensiven Produktionsprozess begründet ist [1]. Ein Hauptkostentreiber ist der Prozess der Stabilisierung mit langen Verweilzeiten bei hohen Temperaturen.
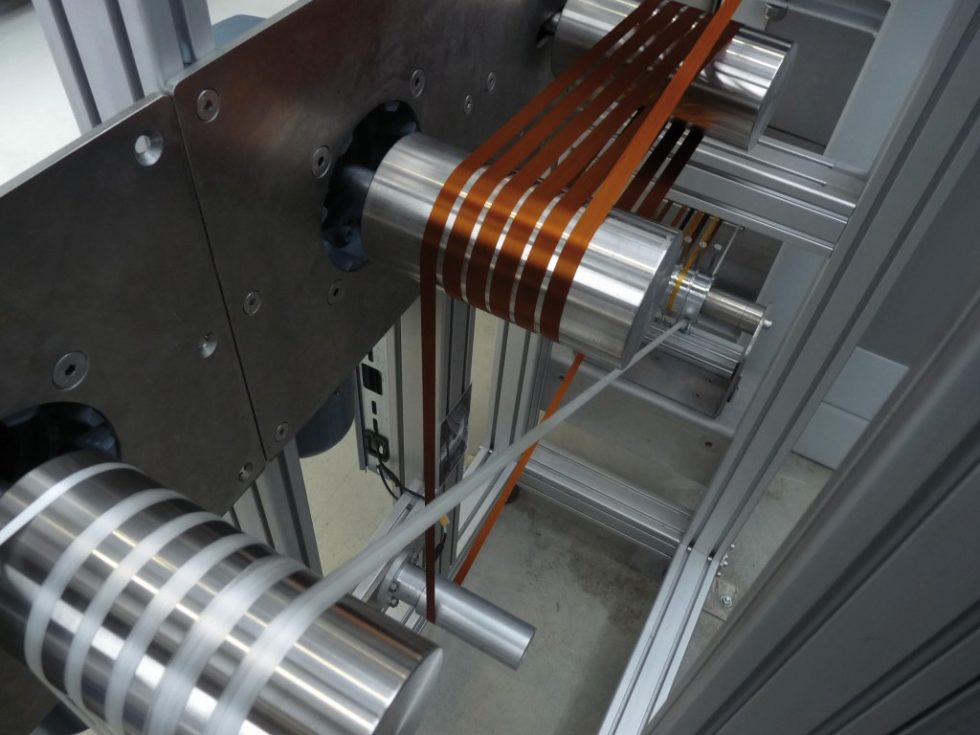
Farbveränderung der Ausgangsfasern während der Carbonfaserproduktion: Eine Reduk‧tion der Zykluszeiten trägt ‧signifikant zur Kosteneinsparung und ‧damit zur besseren ‧Wirtschaftlichkeit von CFK (kohlenstofffaserverstärker Kunststoff)-Bauteilen bei. Bild: ITA, RWTH Aachen
Die Verweilzeiten liegen zwischen 60 min bis 100 min bei Temperaturen bis 280 °C [2;3]. Ein Lösungsansatz zur Verkürzung der Zeiten ist die Entwicklung von Prozessprofilen, die auf die chemischen Eigenschaften des Ausgangsmaterials angepasst sind. Am Institut für Textiltechnik (ITA) der RWTH Aachen ist so auf kontinuierlichen Technikumsanlagen eine Stabilisierungszeit von 22 min realisiert worden. Die mechanischen Eigenschaften der Carbonfasern sind dabei vergleichbar zu industriellen Standard-Modul-Carbonfasern (Zugfestigkeit: 4100 MPa, E-Modul: 220 GPa).
Bedeutung von CFK für den Leichtbau
Die Reduktion von CO2-Emissionen mittels Leichtbau ist eine zentrale Entwicklungsrichtung der heutigen Zeit. Daher werden vermehrt carbonfaserverstärkte Kunststoffe (CFK) als Substitutionsmaterial von klassischen Metallen eingesetzt. Im Vergleich zu klassischen Metallen wie Aluminium bieten CFK ein um 10-fach erhöhtes Festigkeits-Gewichtsverhältnis, was es für Leichtbauanwendungen prädestiniert.
Im Vergleich zu hochfesten Stählen, die häufig im Automobilbereich eingesetzt werden, ist das Preis-Festigkeitsverhältnis von CFK ebenfalls 10-mal höher. CFK werden bislang in Nischenanwendungen mit Fokus auf Gewichtsreduktion eingesetzt. Ein Hauptkostentreiber ist der hohe Carbonfaserpreis, der aufgrund des energie- und zeitintensiven Produktionsprozesses zustande kommt[2].
Bild 1 stellt den historischen und den prognostizierten weltweiten Bedarf an Carbonfasern von 2008 bis 2020 dar [4].
Möglichkeiten zur Kostensenkung
Eine der günstigsten Carbonfasern wird momentan von der Firma Zoltek (Bridgeton/USA) zu einem Preis von 14 Euro/kg vertrieben [6]. Der geringe Preis wird allerdings durch den Einsatz von großvolumigen „Heavy Tows“ (50k) mit geringen mechanischen Eigenschaften und geringer Faserqualität erzielt.
In der Carbonfaserherstellung ist die thermische Stabilisierung mit langsamen Prozesszeiten bis zu 100 Minuten bei Temperaturen bis 280 °C limitierend [3]. Der Hauptgrund für die langen Prozesszeiten sind diffusionsgetriebene exotherme Reaktionen, die über den Faserquerschnitt ablaufen [2]. Wie in Bild 2 dargestellt, entfallen nahezu 50 % der Energiekosten der thermischen Konvertierung auf die Stabilisierung [7].
- deutlich nachteiliges Preis-Leistungsverhältnis von CFK im Vergleich zu hochfesten Stählen oder Aluminium sowie glasfaserverstärkten Kunststoffen,
- kein Masseneinsatz von Carbonfasern – offenliegendes Leichtbaupotential,
- Kostentreiber ist die thermische Stabilisierung aufgrund langer Prozesszeiten.
Ein zentrales Ziel der Carbonfaserforschung am ITA ist die Reduktion der Prozesszeit der Stabilisierung, um hierdurch den Carbonfaserpreis zu reduzieren. Bei industrieller Umsetzung wird das Preis-Leistungsverhältnis von CFK gegenüber anderen Verstärkungswerkstoffen verbessert und somit ein Masseneinsatz von Carbonfasern für Leichtbauanwendungen möglich.
Stand der Technik bei der Carbonfaserherstellung
Im industriellen Standard werden Carbonfasern aus dem Polymer Polyacrylnitril (PAN) hergestellt. Das PAN wird zunächst im Lösungsmittelspinnverfahren zu „Precursoren“ ausgesponnen. Dabei werden tausend einzelne Filamente zu einem Faserbündel zusammengefasst. Anschließend folgt die thermische Konvertierung (Stabilisierung und Carbonisierung) der PAN-Precursoren zu Carbonfasern.
In der Stabilisierung werden die PAN-Precursoren durch eine Umstrukturierung der Molekülketten zu einer Pyridin-Ringstruktur unbrennbar und unschmelzbar gemacht. Hierdurch werden die Precursoren auf die folgende Carbonisierung vorbereitet. In der Carbonisierung wird der Kohlenstoffanteil sukzessive auf mehr als 90 % erhöht. Dabei wird die charakteristische hexagonale Ringstruktur der Kohlenstoffatome ausgebildet, die zu den hohen mechanischen Eigenschaften der Carbonfasern führt.
Abschließend erfahren die Carbonfasern eine Nachbehandlung mit einem Sizing-Auftrag. Das Sizing maximiert die Haftung und entsprechend die Kraftübertragung zwischen Matrixkunststoff und Carbonfasern. Es schützt die Fasern vor Abrasion bei der Herstellung textiler Flächen. Prozesstechnisch ist das Lösungsmittelspinnen von der thermischen Konvertierung aufgrund von deutlich unterschiedlichen Produktionsgeschwindigkeiten getrennt. Stabilisierung, Carbonisierung und Nachbehandlung laufen direkt nacheinander ab. Bild 3 stellt die verschiedenen Produktionsschritte schematisch dar [1–3].

Bild 3. Schematische Darstellung der Prozesskette zur Carbonfaserherstellung. Bild: ITA, RWTH Aachen
Großtechnisch wird die Stabilisierung bislang durch vier bis zwölf Öfen abgebildet, welche jeweils ein isothermes Temperaturprofil haben. Die Temperatur steigt vom ersten bis zum letzten Ofen mit konstanten Sprüngen an, wobei die Verweilzeit in den Öfen jeweils konstant gehalten wird.
Ein zentraler Sicherheitsaspekt der Stabilisierung ist die Entstehung von toxischer Blausäure, die mit einem Abgassystem abgeführt und verbrannt werden muss. Weiterhin sind die Stabilisierungsreaktionen sehr exotherm. Um eine hohe Prozessstabilität und -sicherheit zu gewährleisten, muss die exotherme Reaktionsenergie kontrolliert und abgeführt werden. Die minimal mögliche Stabilisierungszeit bestimmt sich aus dem für den Prozess notwendigen Stabilisierungsgrad der Fasern sowie der Betriebssicherheit der Anlage [1;2].
Neben verschiedenen Anlagenparametern sind die folgenden drei Prozessparameter maßgeblich relevant für die Prozessführung der Stabilisierung:
- Temperatur,
- Verweilzeit,
- Verstreckung.
Im industriellen Stand der Technik ist die Verweilzeit in den verschiedenen Temperaturstufen (verschiedenen Öfen) identisch. Industriell wird derzeit eine gesamte Stabilisierungszeit von circa 60 min bis 100 min realisiert, abhängig vom jeweiligen Hersteller und vorhandenem Know-how.
Zielsetzung und Lösungsansatz zur Kostenreduktion
Ziel der Forschungsarbeit ist die Reduktion der Prozesszeit, die zur Stabilisierung benötigt wird. Somit soll eine Kostenreduktion bei der Herstellung von CFK angestrebt werden. Dabei wird davon ausgegangen, dass aufgrund der Verweilzeitreduktion die mechanischen Fasereigenschaften reduziert werden. Um eine industrielle Anwendung der Ergebnisse zu erreichen, ist es maßgeblich, eine bestimmte Faserqualität zu erreichen.
Als Zielsetzung für die mechanischen Eigenschaften gilt eine Faser des Typs „T300“ des japanischen Herstellers Toray Industries, Inc. mit einer Zugfestigkeit von 3,5 GPa bei einem E-Modul von 230 GPa und einer Bruchdehnung von 1,5 %. Diese Faser ist eine der kostengünstigsten, am Markt erhältlichen Carbonfasern mit akzeptablen Eigenschaften. Sie wird in Sekundärstrukturbauteilen in Flugzeugen, im Automobilsektor sowie im Sport- und Freizeitsektor intensiv eingesetzt.
Im gewählten Lösungsansatz wird die Verweilzeit in den verschiedenen Temperaturstufen getrennt voneinander eingestellt. Konkret werden die Prozessparameter Temperatur, Verweilzeit und Verstreckung auf den Reaktionsablauf und die chemischen und thermischen Eigenschaften des Precursors in den verschiedenen Temperaturzonen angepasst. Da die Eigenschaften verschiedener Precursoren sehr unterschiedlich sind, wurde am ITA eine methodische Vorgehensweise entwickelt, auf Basis derer die Prozessparameter für einen vorliegenden Precursor entwickelt werden können.
Eine Erhöhung der Produktionsgeschwindigkeit der Stabilisierung geht mit einer höheren Produktionsgeschwindigkeit der Carbonisierung einher. Somit reduziert sich mit dem gewählten Lösungsansatz ebenfalls die Verweilzeit der Carbonisierung. Daher berücksichtigt die Vorgehensweise ebenfalls die Entwicklung von Prozessparametern für die folgende Carbonisierung, die Abhängig von der jeweiligen Prozessführung der Stabilisierung sind.
Ergebnisse
Als Ergebnis wurde eine Stabilisierungszeit von 22 min bei Prozessstabilität und -sicherheit erreicht. Genutzt wurde hierzu ein industrieller Precursor der Firma Zhongfu Shenying Carbon Fiber Co.,Ltd. Bei einer Stabilisierungszeit von nur 15 min konnte ebenfalls ein Stabilisierungsgrad erzielt werden, mit dem eine Carbonisierung und damit eine Carbonfaserherstellung möglich sind. Allerdings kommt es bei derart geringen Verweilzeiten zur Entwicklung von hohen Mengen toxischer Gase in kurzer Zeit, sodass eine ausreichende Prozesssicherheit nicht sichergestellt werden kann.
Bei einer Verweilzeit von 22 min beträgt die erreichte Zugfestigkeit 4,1 GPa bei einem E-Modul von 220 GPa und einer Bruchdehnung von 1,8 %. Die erzielten mechanischen Eigenschaften liegen somit auf und über dem Niveau gängiger industrieller Carbonfasern (Beispiel Toray T300, Toho Tenax HTS 40). Großer Vorteil der entwickelten Vorgehensweise ist die Nutzung bestehender, konventioneller Anlagentechnik, wodurch die Übertragung der Methode auf industrielle Produktionslinien ohne zusätzliche Investitionskosten möglich ist.
Abhängig vom bisherigen Produktionsverfahren lässt sich eine Reduktion der Produktionskosten von 3 Euro/kgCF realisieren. Denkbar sind hierbei zwei verschiedene Varianten: Zum einen die Inbetriebnahme einer neuen Produktionslinie mit kleineren Öfen – und somit verringerten Investitionskosten. Zum anderen die Beschleunigung der Produktionsgeschwindigkeit von bestehenden Produktionslinien.
Fazit und Ausblick
In Bild 4 sind die erzielten Ergebnisse zusammengefasst.
Mit der entwickelten Vorgehensweise lässt sich eine Produktivitätssteigerung um mehr als 300 % bei einer marktüblichen Faserqualität realisieren. Die bisherigen Ergebnisse wurden auf einer Anlagengröße im Technikumsmaßstab erzielt. Als nächster Schritt steht daher der Ergebnistransfer beziehungsweise der Methodentransfer auf eine Anlagengröße im Pilotmaßstab an, um somit die industrielle Umsetzbarkeit zu bestätigen.
Literatur:
[1] Warnecke, M.; De Palmenaer, A.; Veit, D.; Seide, G.; Gries, T.: Faserstofftabelle Carbonfasern. Aachen: Shaker-Verlag, 2013.[2] Morgan, P.: Carbon Fibers and their Composites. Boca Raton: Taylor & Francis Group, 2005.[3] Heine, M.: Optimierung der Reaktionsbedingungen von thermoplastischen Polymer-Fasern zur Kohlenstoffaser-Herstellung am Beispiel von Polyacrylnitril. Dissertation, Universität Karlsruhe, 1988.[4] Witten, E.; Kühnel, M.: Composites-Marktbericht 2016. Industrievereinigung verstärkte Kunststoffe, Frankfurt/Main, 2016.[5] Technische Textilien als Treiber der europäischen Zukunft. Vortrag ITV Denkendorf, 7.5.2015. Gherzi Textil Organisation, Zürich/CH.[6] Zoltec Carbon Fibre: Zoltek PX35 Commercial Carbon Fibre Datenblatt, 2014.[7] Maghe, M.; Fox, B.L.; Byrne, N.; Huson, M.: Use of Ionic liquids as novel plasticizer for polyacrylonitrile carbon fibre precursor. Carbon Fibre – Future Directions Conference, Waurn Ponds, Australia, 2015.
Univ.-Prof. Thomas Gries, Jahrgang 1964, ist seit 2001 Direktor des Instituts für Textiltechnik (ITA) an der RWTH Aachen University. Er koordiniert die interdisziplinäre Forschung und ist als Gutachter und Berater tätig. Im März 2013 wurde ihm in Moskau die Ehrenprofessur der Lomonosov Moscow State University verliehen. // M.Sc. Franz Pursche, Jahrgang 1987, studierte Wirtschaftsingenieurswesen mit Fachrichtung Maschinenbau an der RWTH Aachen University. Seit 2014 ist er wissenschaftlicher Mitarbeiter in der Forschungsgruppe Carbonfasern am ITA in Aachen.