Wie eine zentrale Datenplattform die Digitale Fabrik voranbringt
Der Begriff „Digitale Fabrik“ wird bereits seit über 20 Jahren am Markt verwendet. Doch was steckt eigentlich dahinter und wie kann der Mittelstand von dem Konzept profitieren?
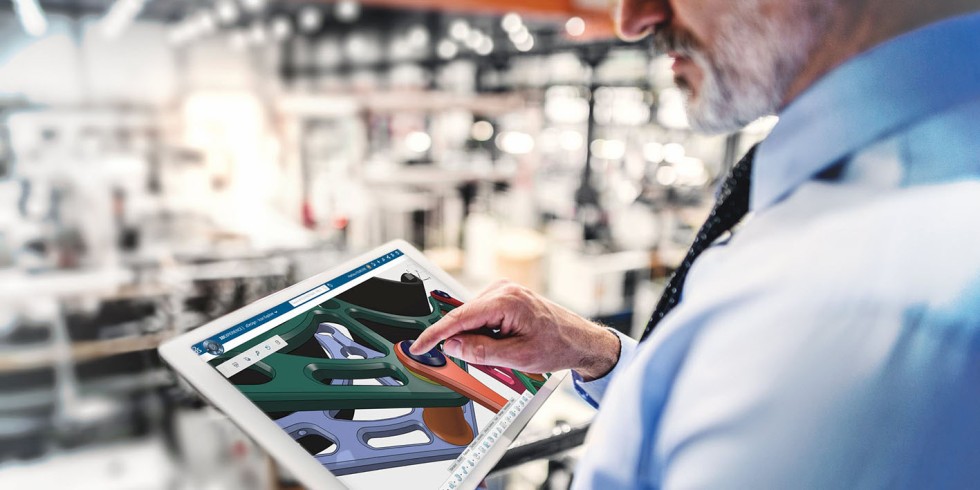
Im ersten Schritt eines Digitalisierungsprojekts geht es darum, Prozesse oder Bereiche zu definieren, mit denen man beginnen will.
Foto: Dassault Systèmes
Erläutert wird der aktuelle Stand der Digitalisierung bei Industrieunternehmen in Deutschland. Die Besonderheiten, auf die Betriebe bei einer erfolgreichen Umsetzung achten müssen, erklärt Björn Manderbach, Director DELMIA Industry Consulting bei Dassault Systèmes.
VDI-Z: Die Digitalisierung ist auch im beruflichen Alltag mittlerweile allgegenwärtig. Warum müssen sich Unternehmen jetzt mehr denn je für Digitalisierungsvorhaben öffnen?
Björn Manderbach: Zahlreiche wirtschaftliche und gesellschaftliche Faktoren sorgen dafür, dass digitale Prozesse in der heutigen globalisierten Welt unabdingbar sind. Dazu zählen beispielsweise eine zunehmend internationale Vernetzung, neue Arbeitsmodelle wie Remote Work, die steigende Relevanz von Nachhaltigkeitsaspekten, aber auch veränderte, individuelle Kundenbedürfnisse. Um nachhaltig Geschäftskontinuität und Resilienz sicherzustellen, wollen viele Mittelständler, insbesondere aus der Fertigungsbranche, die Digitalisierung jetzt verstärkt anpacken.
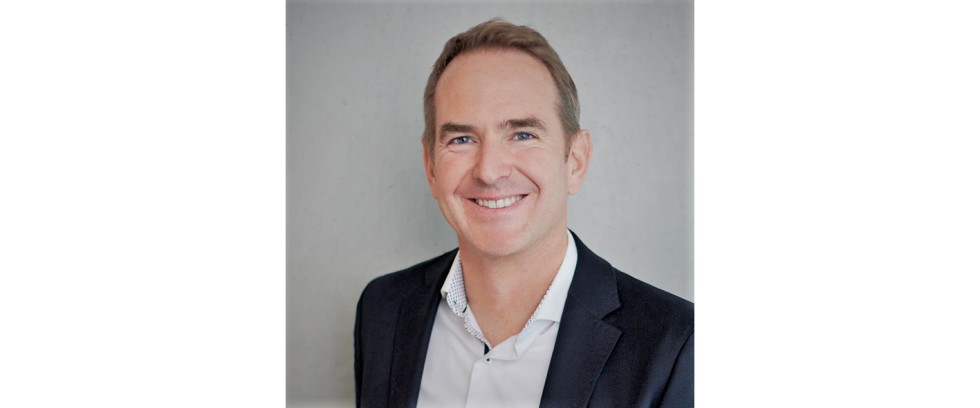
Björn Manderbach ist als „Director DELMIA Industry Consulting“ bei Dassault Systèmes ein ausgewiesener Digitalisierungsexperte.
Foto: Dassault Systèmes
Der Begriff „Digitale Fabrik“ existiert nun schon eine ganze Weile. Was genau bedeutet er denn und welcher Mehrwert entsteht für Unternehmen, die ihre Fabrik digitalisieren?
Das Verständnis einer digitalen Fabrik hat sich über die Zeit etwas gewandelt. Zu Beginn der Entwicklungen vor etwa 20 Jahren haben Unternehmen im Rahmen des Produktlebenszyklusmanagements (PLM) primär das Ziel verfolgt, digitale Produktinformationen für nachgelagerte Aktivitäten, wie beispielsweise die virtuelle Produktionsplanung, weiter zu verwenden. Heutzutage stehen jedoch ganze Abläufe im Fokus. In einer digitalen Fabrik geht es eigentlich darum, gesamte Prozesse – von der Planung über die Optimierung bis zur Ausführung – durch Softwarelösungen digital abzubilden und zu unterstützen.
Das bringt für produzierende Unternehmen enorme Vorteile mit sich: Basierend auf demselben Datenmodell, nutzen Mitarbeitende aus der Produktionsplanung die Informationen aus Konstruktion und Entwicklung, wodurch Veränderungen jederzeit für alle Beteiligten sichtbar und verfügbar sind. Die Ausführung der Produktion läuft somit auf stets aktuellen Informationen ab, während gleichzeitig der Datenrückfluss gewährleistet ist. Gemeint ist damit, dass kontinuierlich Echtzeitdaten aus den laufenden Prozessen mit den Daten aus der Planung verglichen werden können. Das macht Rückschlüsse darüber möglich, an welchen Stellschrauben gedreht werden kann.
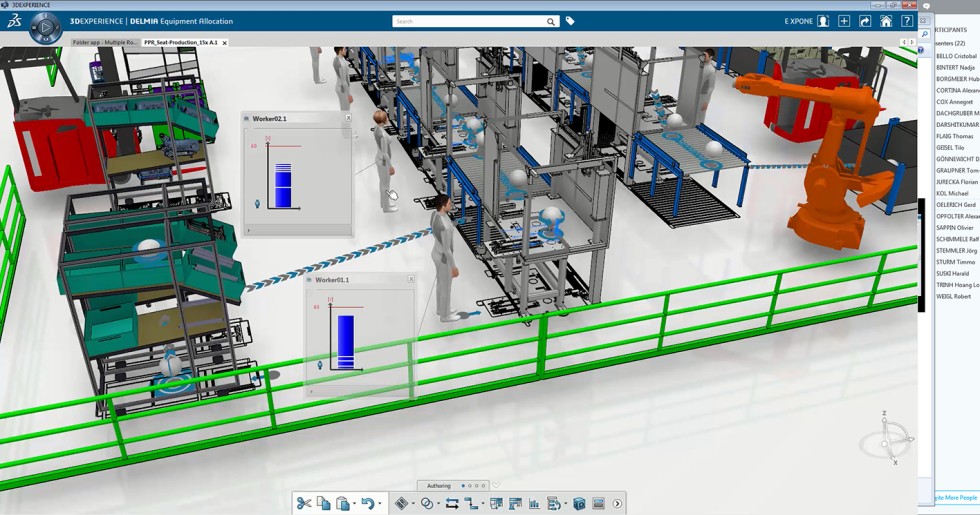
Architekten und Fabrikplaner können jetzt gemeinsam ganze Fertigungslinien in 3D planen und die Abläufe simulieren, bevor neue Maschinen in Realität angeschafft werden. Grafik: Dassault Systèmes
Welche Unternehmensbereiche bezieht die digitale Fabrik konkret mit ein?
Grundsätzlich ist keine Abteilung ausgeschlossen. Welche Prozesse zuerst digitalisiert werden, ist aber von Unternehmen zu Unternehmen verschieden. Das kann dann sowohl das Projektmanagement, die Entwicklung, die Fertigung, oder auch die Zusammenarbeit mit Zulieferern sein – die gesamte Wertschöpfungskette also.
Meist geht es jedoch nicht darum, einen Bereich von Grund auf neu aufzuziehen. Viel häufiger ist, dass Industrieunternehmen eine bestehende Fabrik „smart“ machen möchten – und diese hierfür beispielsweise im ersten Schritt als 3D-Modell abbilden wollen, um virtuell ein neues Layout zu planen. Zunächst kann hierfür die Halle einmal komplett gescannt werden, um den Status Quo abzubilden. Das funktioniert mit speziellem Equipment, das per Laser und Kamera die nötigen Daten erfasst. Es entsteht sowohl eine digitale Punktewolke, als auch ein Modell aus hochauflösenden Bildern, in dem alle Parameter des aktuellen Fabriklayouts berücksichtigt sind: vom Grundriss, über Abmessungen der Maschinen und Freiräume, bis hin zur Position von Werkstoren und Fahrwegen.
Anhand dieses Modells können Architekten und Fabrikplaner nun zusammenarbeiten. Sie können beispielsweise ganze Fertigungslinien in 3D planen und die Abläufe simulieren, bevor neue Maschinen tatsächlich angeschafft werden. Das spart wertvolle Zeit und Ressourcen. Der Worst Case wäre ja, wenn eine neue, teure Maschine gar keinen Platz in der aktuellen Halle finden würde.
Daten sind das „A und O“ der digitalen Fabrik. Gibt es weitere essenzielle Bestandteile?
Daten sind tatsächlich die Grundlage für alles, was in der digitalen Welt passieren soll, um es schließlich in die reale Welt zu übertragen. Nur mit Daten können Unternehmen virtuelle Modelle erstellen, Auswertungen durchführen und dadurch ihre Prozesse optimieren. Dabei ist das Konzept der digitalen Fabrik weitaus vielschichtiger, als eine Checkliste abzuarbeiten und bei einer bestimmten Anzahl erledigter Punkte vom Endprodukt „Digitale Fabrik“ zu sprechen.
Auch wenn, wie bereits angesprochen, alle Unternehmensbereiche eine wichtige Rolle spielen, heißt das nicht, dass sie alle digitalisiert werden müssen – geschweige denn gleichzeitig. Der Fokus liegt auf der Digitalisierung von den Abläufen, die Unternehmen je nach Notwendigkeit individuell priorisieren und festlegen. Für Firma A kann das die Verzahnung von Konstruktion und Produktion sein, Firma B möchte die Lieferketten optimieren, während Firma C eine neue Fertigungslinie am 3D-Modell plant. Voraussetzung sind hier stets lückenlose Datensätze, die das Vorhaben in jedem Fall immens vereinfachen.
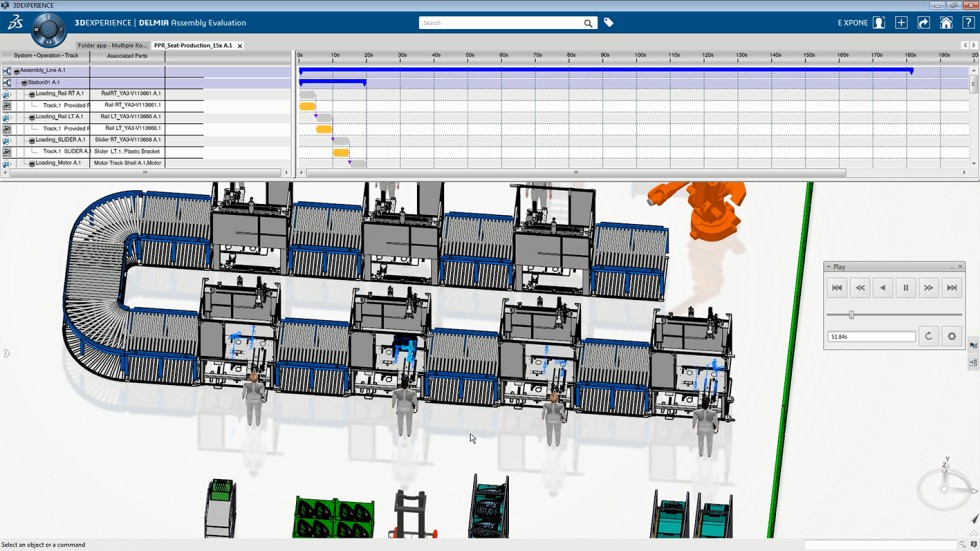
Die Prozessvisualisierung von Abläufen in der Fabrik zählt zu den Kernaufgaben. Grafik: Dassault Systèmes
Grundbestandteil einer digitalen Fabrik sollte daher auch eine zentrale Datenplattform wie beispielsweise die 3DExperience-Plattform von Dassault Systèmes sein. In Zeiten einer zunehmenden Globalisierung bietet sie auch den Vorteil, dass Mitarbeitende von überall aus und jederzeit auf die aktuellsten Daten zugreifen sowie in Teamarbeit an Produkten oder Projekten arbeiten können. Diese ortsunabhängige Kollaboration haben wir besonders in den vergangenen zwei Jahren der Pandemie zu schätzen gelernt, als wir erleben mussten, wie schnell unerwartete Ereignisse das Geschäft verlangsamen oder sogar lahmlegen können.
Wie sieht es in Deutschland aus, wie schätzen Sie den aktuellen Digitalisierungsfortschritt bei Industrieunternehmen ein?
Früher haben sich fast nur größere Konzerne an die digitale Fabrik gewagt, da die Umsetzung aufwendig und kostenintensiv war. Mittlerweile hat sich die Situation gewandelt: Auch KMUs (kleine und mittlere Unternehmen) haben verstanden, dass es nicht zwingend um die Digitalisierung des großen Ganzen geht, sondern dass man bei einzelnen Prozessen beginnen kann.
Grundsätzlich sind Unternehmen in Sachen Digitalisierung also relativ weit fortgeschritten. Sie haben über die Zeit oft verschiedene, kleine Lösungen implementiert oder selbst gebaut, die gewisse Facetten abdecken. Jetzt geht es darum, die einzelnen Puzzle-Teile zu verbinden, also Lösungen zu konsolidieren und zu einer einheitlichen Infrastruktur zusammenzufügen. Hier kommt erneut der Plattformgedanke zum Tragen, der ein wesentlicher Aspekt beim Thema „Digitale Fabrik“ ist. Aktuelle Umfragen ergeben zwar, dass sich viele Unternehmen in Sachen Industrie 4.0 eher als „Nachzügler“ einschätzen – die Bereitschaft, in Technologien der Digitalisierung zu investieren ist jedoch auch vorhanden. Das Potential der digitalen Fabrik ist bei deutschen Industrieunternehmen also noch lange nicht ausgeschöpft.
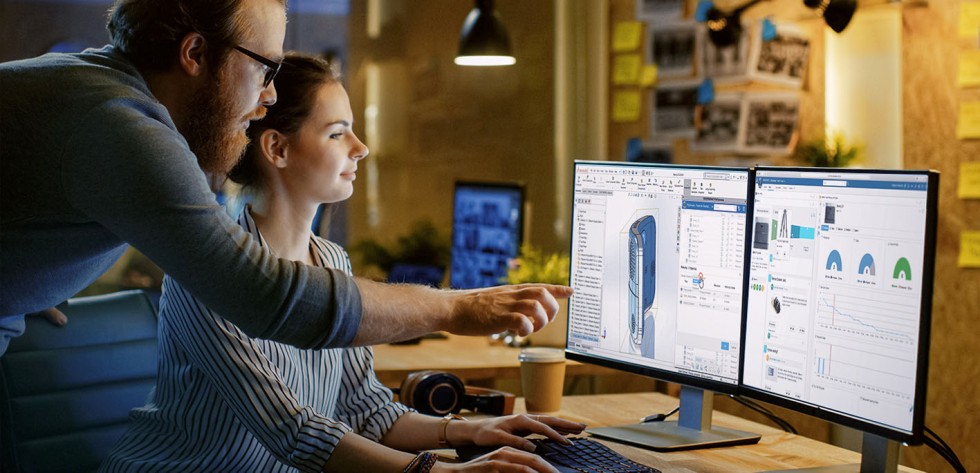
Während früher das Product Lifecycle Management im Vordergrund stand, so wird heute vor allem das Ziel verfolgt, ganze Abläufe in Fabriken zu digitalisieren.
Foto: Dassault Systèmes
Die Digitalisierung der Fertigung ist hierzulande auf einem guten Weg. Dennoch bleibt es ein langfristiges Vorhaben. Welche Ratschläge können Sie KMUs mit auf den Weg geben, die gerade ganz am Beginn des Projekts „Digitale Fabrik“ stehen?
Die wichtigste Botschaft aus meiner Sicht ist: Es gibt nicht den einen Startpunkt. Unternehmen müssen sich von dem Gedanken lösen, sofort die gesamte Fabrik zu digitalisieren. Das schreckt nicht nur ab, sondern ist schlichtweg ineffizient. Im ersten Schritt gilt es also, Prozesse oder Bereiche zu definieren, mit denen man beginnen will. Dabei sollte klar festgesetzt werden: Was ist das verfolgte Ziel und welcher Mehrwert entsteht durch die Maßnahmen? Sind diese ersten Projekte erfolgreich umgesetzt, können die nächsten Bereiche angegangen werden.
Jedes Digitalisierungsprojekt bringt große Veränderungen bei unternehmensinternen Abläufen für die Belegschaft mit sich, weshalb das „Change Management“ nicht zu vergessen ist. Die Kommunikation mit den Mitarbeitenden ist für ein Gelingen von großer Bedeutung, sie müssen frühzeitig eingebunden und „auf die Reise mitgenommen werden“. Das sind aber nicht die einzigen Erfolgsfaktoren. Projekte zur digitalen Fabrik sind vor allem dann gewinnbringend, wenn der virtuelle Aspekt mit dem realen Aspekt kombiniert wird. Daten müssen also nicht nur gesammelt, sondern auch genutzt werden, um Rückschlüsse aus dem laufenden Betrieb zu ziehen oder Entscheidungen bezüglich Investitionen zu treffen.
Zum Schluss bleibt der Appell: Wagen Sie den Schritt in die Digitalisierung. Auch wenn aller Anfang schwer ist, die Vorteile einer vernetzten Produktion überwiegen letztendlich. Mit gründlicher Planung, einem klaren Ziel vor Augen und dem richtigen Partner können Unternehmen von der digitalen Fabrik nur profitieren.
Das könnte Sie auch interessieren:
Wie Künstliche Intelligenz Einzug in den Fertigungsprozess hält
Umsetzungsstrategie bei Digitalisierungsprojekten: Zug um Zug in die Zukunft
In fünf Etappen zum Geschäftsmodell von morgen