Selbstfahrende Chassis in der Fahrzeug-Endmontage
Der Kundenwunsch nach mehr Individualisierungsmöglichkeiten sowie die unsicheren Stückzahlprognosen für Elektrofahrzeuge erfordern von der Automobilindustrie sehr flexible Produktionskonzepte. Klassische Montagestrukturen können diesen hohen Flexibilitätsgrad nicht gewährleisten und sind zusätzlich mit enormen Infrastruktur-Investitionen verbunden.
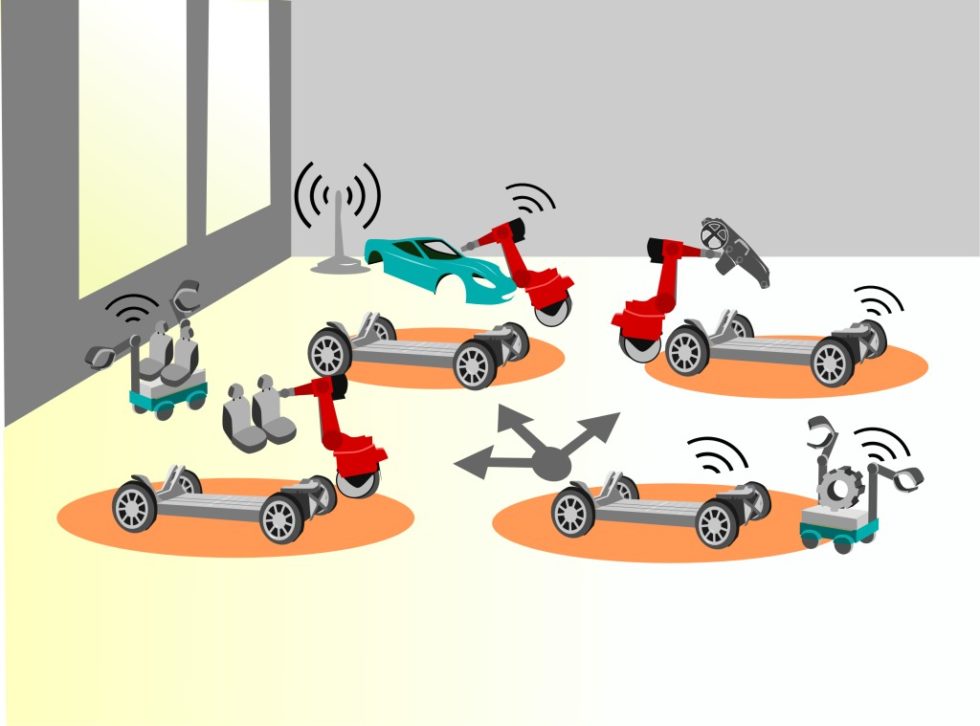
Autonom fahrende Fahrzeugchassis erlauben ein flexibles, skalierbares und investitionsarmes innerbetrieb‧liches Produktions‧netzwerk für die Endmontage von Elektrofahrzeugen. Bild: PEM, RWTH Aachen
Insbesondere bei der Auslegung der Produktionssystematik von Elektromobilen sind innovative und investitionsarme Montagekonzepte vonnöten. Eine Verlagerung der Transportfunktion von der Montageinfrastruktur in das Produkt selbst kann die notwendige Flexibilität bei gleichzeitiger Reduktion der Einmalaufwände herbeiführen.
Die globale Automobilbranche wird aktuell von einem Elektrifizierungstrend geprägt. Dieser Umschwung von klassischen verbrennungsmotorischen Fahrzeugantrieben zu teil- oder vollelektrischen Fahrzeugen macht sich auch in der Produktionstechnik bemerkbar. Dabei stecken diese neuen Mobilitätsträger im „Teufelskreis der Elektromobilproduktion“, Bild 1 [1].
Herausforderungen bei der Produktion von Elektrofahrzeugen
Vor allem Privatkunden halten sich mit der Anschaffung eines Elektrofahrzeugs aufgrund einer vermeintlich unzureichenden Reichweite sowie der relativ hohen Anschaffungskosten zurück. Die dadurch sehr beschränkten Nachfragemengen erlauben es den Fahrzeugherstellern noch nicht, Skaleneffekte in der Produktion zu erzielen. Das führt im Vergleich mit hochvolumig produzierten klassischen Fahrzeugen zu höheren Produktionskosten, welche wieder ein Grund für die geringe Nachfrage an Elektrofahrzeugen sind.
Um dieses Dilemma zu durchbrechen, setzen die Fahrzeughersteller neben der Forderung nach einer staatlichen Subvention zur Steigerung der Attraktivität der Elektromobilität auch auf konsequente Produktarchitekturen und innovative Produktionsverfahren. Während bei „Conversion Design“-Fahrzeugen bestehende Fahrzeugplattformen und damit auch zumindest teilweise deren Produktionssystematik und –Infrastruktur übernommen werden kann, stellen „Purpose Design“-Elektrofahrzeuge komplette Neuentwicklungen mit eigenen Architekturen dar. Diese spiegeln sich wiederum in eigenen Anforderungen an das Produktionssystem wider.
Bei der Auslegung eines Produktionssystems für ein Purpose-Design-Elektromobil sind die aktuell noch geringen Nachfragemengen eine besondere Herausforderung. Die Investition in ein klassisches Transport- und Montagesystem zur Linienfertigung rentiert sich in vielen Fällen noch nicht. Gleichzeitig muss die Produktion jedoch auch für eine schnell wachsende Nachfrage gewappnet sein – die zum Beispiel durch die Einführung von staatlichen Subventionen für E-Fahrzeuge entstehen kann. Daher spielt die Skalierbarkeit bei der Konzeption von Produktionssystemen für Elektrofahrzeuge eine besondere Rolle. Dabei muss jedoch gewährleistet werden, dass die dafür notwendigen Investitionen so gering wie möglich gehalten werden und diese die Wirtschaftlichkeit der E-Mobil-Fertigung nicht zusätzlich negativ beeinflussen.
Zusätzlich wird die heutige Automobilindustrie generell durch schwankende Gesamtstückzahlen und einen Trend zur steigenden Kundenindividualisierung geprägt. Insbesondere die „mass customization“ führt zu sinkenden Stückzahlen für einzelne Varianten und einer steigenden Variantenvielfalt sowie Komplexität – insbesondere in der Endmontage. Die Gesamtheit der externen Einflüsse auf die Produktionssysteme für Elektrofahrzeuge führt zu einem gesteigerten Flexibilitätsbedarf in der Fahrzeugendmontage.
Flexibilität in Automobil- Produktionssystemen
Flexibilität lässt sich im Allgemeinen sowohl nach Fremerey [2] anhand eines Objektbereichs als auch nach Gottschalk [3] in eine zeitliche Perspektive unterteilen. Dadurch entsteht der in Bild 2 dargestellte Ordnungsrahmen der Flexibilität. Bereits existierende Flexibilitätsmaßnahmen können in diesen Ordnungsrahmen eingeordnet werden.
Kurzfristige organisatorische Flexibilität kann in der Fahrzeugendmontage durch eine Vielzahl von Maßnahmen erzielt werden. Beispielhaft lässt sich der Einsatz von „Springern“ sowie die Anpassung der Taktzeit erwähnen. Mittelfristige Flexibilität auf Organisationsebene kann durch eine Kapazitätsabstimmung („Line Balancing“) oder zusätzliche Mitarbeiter erreicht werden. Für eine langfristige organisatorische Flexibilität werden in Produktentwicklung und Montageplanung Methoden des Variantenmanagements oder des „Design for assembly“ angewandt [4].
Auf struktureller Ebene finden sich vor allem variantenabhängig verzweigte Produktionslinien (kurzfristig), die Inbetriebnahme von Leertakten und Parallellinien (mittelfristig) sowie die Restrukturierung des Montagesystems (langfristig). Insgesamt zeigt sich jedoch eine deutlich eingeschränkte Auswahl an Flexibilitätsmaßnahmen. Dies begründet sich vor allem in den starren Strukturen der verwendeten Transportsysteme in der Fahrzeugendmontage. Die in der Serienfertigung üblicherweise angewandten Transporttechniken – wie Elektrohängebahnen oder Plattenförderer – sind aufgrund ihrer fest installierten Infrastruktur nur sehr eingeschränkt für eine strukturelle Flexibilität geeignet.
In der Praxis herrscht folglich ein Defizit vor allem an kurzfristigen, strukturellen Flexibilitätsmaßnahmen (Bild 2).
Verlagerung der Transportfunktion als Flexibilisierungsmaßnahme
Eine Möglichkeit, den beschriebenen Herausforderungen bei der Produktion von Elektrofahrzeugen zu begegnen und gleichzeitig das Praxisdefizit an kurzfristiger, struktureller Flexibilität zu schließen, ist die Verlagerung der Transportfunktion während der Endmontage vom Transportsystem in das Fahrzeug selber. Das Produkt Fahrzeug liefert nach diesem Ansatz selbst die Fähigkeit, sich ab einem bestimmten Entkopplungspunkt in der Montage selbständig durch diese zu bewegen.
Prinzipiell verfügen Elektromobile über alle notwendigen Antriebskomponenten (elektrischer Antriebstrang, Energiespeichersystem, elektronische Steuergeräte), um mithilfe des eigenen Antriebs eigenständig durch die Fahrzeugendmontage zu fahren. Wird der fahrzeugeigene Antrieb zur Fortbewegung verwendet, ist ein festinstalliertes Transportsystem nicht mehr notwendig. Ausgestattet mit einer geeigneten Informations- und Kommunikationstechnologie, wird das starre und lineare Transportsystem aufgebrochen und das flexible und echtzeitfähig gesteuerte Re-Routing jedes Fahrzeugchassis möglich.
Im Anschluss an die klassischen Fertigungsschritte des Karosseriebaus und der Lackierung werden in der Endmontage zum frühestmöglichen Zeitpunkt der elektrische Antriebsstrang sowie eine optionale Lenkvorrichtung installiert. Diese kann entweder nur eine temporäre Komponente oder die für das Fahrzeug vorgesehene elektrische Hilfskraftlenkung (zum Beispiel „Electric Power Steering“) sein. Mithilfe eines Fahrzeug-Steuergeräts, das die Informationsverarbeitung, Kommunikationsaufgaben und Steuerbefehle übernimmt, kann das Chassis sich nun selbständig durch die weitere Endmontage bewegen. Somit wird es möglich, dass sich jedes Fahrzeug in Abhängigkeit der jeweiligen Konfiguration und des aktuellen Zustands des Montagesystems einen individuellen Pfad für die noch anstehenden Montageschritte sucht.
Aufgrund der durchgängigen Vernetzung aller beteiligten Komponenten und einer echtzeitbasierten Prozesssteuerung findet eine Verschmelzung von Produkt und Produktionsanlage zu einem „Cyber-Physischen System“ (CPS) [5] statt. Eine Produktionssteuerung auf Basis dieses neuronalen Netzes erlaubt es, bei jeder neuen Informationslage die Route durch die Montage dynamisch neu zu planen. So kann vermieden werden, dass unnötige Wartezeiten an besetzen Stationen entstehen und nicht erforderliche Montagestationen angefahren werden.
Die Vorteile eines solchen Montagesystems liegen vor allem in der Fähigkeit, flexibel und schnell auf Veränderungen der Gesamtstückzahl und der Variantenvielfalt zu reagieren sowie sehr einfach neue Varianten in das Produktspektrum aufnehmen zu können. Des Weiteren profitiert das System von einer Reduzierung der notwendigen Einmalkosten in ein Transportsystem und der Verringerung des Zeit- und Investitionsaufwands bei strukturellen Änderungen am Produktionsablauf. Durch den nicht mehr starr verketteten Produktionsablauf ist es darüber hinaus robuster gegenüber Maschinenausfällen sowie bei Problemen in der Materialbereitstellung.
Beim Vergleich mit ähnlich flexiblen Transportvarianten auf Basis fahrerloser Transportsysteme (FTS) zeichnet sich das dargestellte System vor allem durch die Selbst-Skalierung aus. Bei steigendem Produktionsvolumen sind keine weiteren Investitionen notwendig, während bei FTS immer ausreichend „Skids“ für die Skalierung vorgehalten werden müssen.
Das System bietet eine Umsetzung der Konzepte von Industrie 4.0 auf die E-Mobil-Produktion. Auf Basis der vernetzten CPS und dem „Internet der Dinge“ lassen sich die Individualisierung von Kundenwünschen, die Flexibilisierung der Produktionstechnologie, eine optimierte Entscheidungsfindung sowie die Ressourcenproduktivität und -effizienz verbessern [6].
Herausforderungen in der Umsetzung
Bei der Realisierung eines Produktionssystems auf Basis selbstfahrender Fahrzeugchassis stellen sich vielfältige Herausforderungen. Als Voraussetzung für ein solches Produktionssystem muss die Montagereihenfolge des Fahrzeugkonzepts so gestaltet werden, dass eine frühzeitige Inbetriebnahme des Antriebsstrangs möglich ist. Dabei muss die Zugänglichkeit aller notwendigen Fahrzeugbereiche auch nach der Installation der Antriebskomponenten gewährleistet sein. Gegebenenfalls müssen geeignete Montagehilfen, zum Beispiel Hebebühnen oder Rampen, durch die Montageinfrastruktur vorgesehen werden.
Aus Kostengründen sollten bereits für die innerbetriebliche Fortbewegung die für die spätere Nutzung vorgesehenen Antriebskomponenten verwendet werden. Mit Blick auf die häufig verwendeten Hochvolt-Energiespeicher sind dabei besondere Arbeitsschutzvorkehrungen zu treffen. Vorstellbar wäre es, zum Beispiel nur einzelne Module des Batteriepacks zu benutzen und so einen Low-Volt-Betrieb möglich zu machen. Hieraus ergeben sich erweiterte Leistungsanforderungen an den Elektromotor und den Inverter. Bild 3 stellt einen Ausschnitt der prinzipiell anwendbaren Lösungsmöglichkeiten für die Kernkomponenten Antrieb sowie Energieversorgung, Lenkung und Ortung dar.
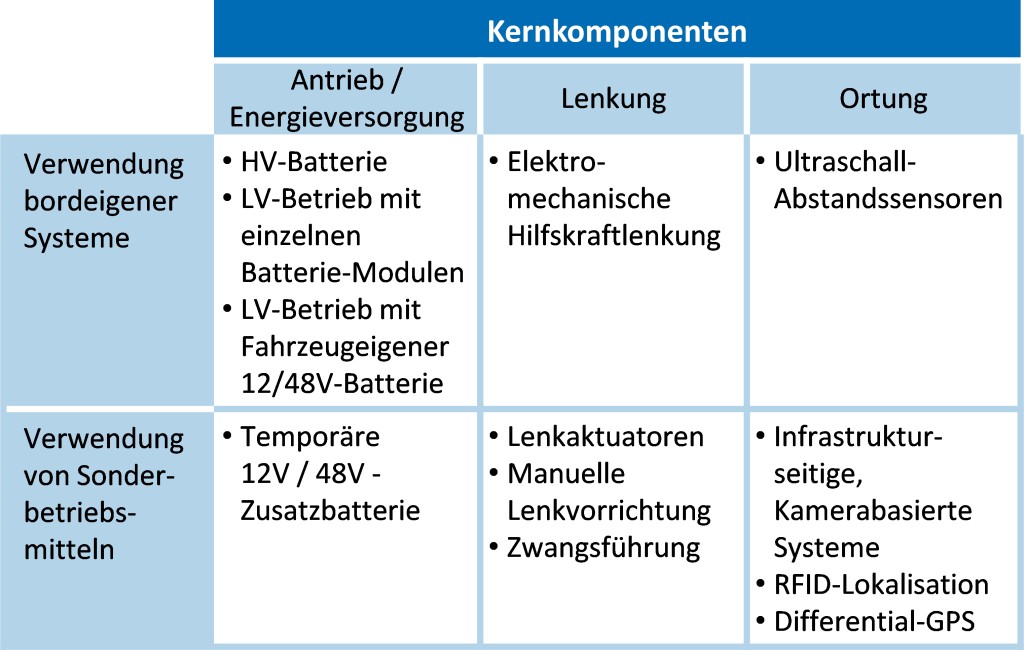
Bild 3. Beispielhafter Lösungsraum für die Umsetzung der autonomen Fortbewegung in der Endmontage. Bild: PEM, RWTH Aachen
Auch die autonome Fortbewegung der Chassis an sich stellt eine Herausforderung für den Arbeitsschutz der beteiligten Montagemitarbeiter dar. Durch eine geeignete Umgebungserkennung muss sichergestellt sein, dass Kollisionen zwischen selbstfahrenden Chassis und Mitarbeitern oder Maschinen verhindert werden. Hier ergeben sich Anknüpfungspunkte an aktuelle Forschungen aus dem Bereich des autonomen Fahrens.
Dies gilt ebenso für die Entwicklung einer geeigneten Kommunikations-Infrastruktur. Um eine zielführende Produktionssteuerung zu erreichen, ist es notwendig, dass die Fahrzeuge untereinander und/oder mit einer zentralen Instanz ihre Daten austauschen. Erst so wird eine optimale Steuerung der Fahrzeugrouten und Montagereihenfolgen möglich. Auch hierbei werden möglichst vorhandene Systeme des finalen Fahrzeugs verwendet, um Investitionskosten einzusparen.
Für die bereits angesprochene Routenplanung der Fahrzeugchassis in der Montageumgebung ist zusätzlich ein Ortungssystem notwendig, das die genaue Positionsbestimmung der beweglichen Produkte sowie weiterer Komponenten – zum Beispiel autonomer Materialbereitstellungswagen – erlaubt. Hierfür bietet sich eine Vielzahl unterschiedlicher Systeme an, zum Beispiel „Indoor-GPS“, RFID (Radio Frequency Identification)-Technik oder die Nutzung von Kamerasystemen, wobei sowohl eine fahrzeugseitige Verbauung wie auch die Installation von Kamerasystemen in der Infrastruktur (Montagehalle) möglich ist.
Fazit
Die Verlagerung der Transportfunktion von einer Transportinfrastruktur in das Produkt selber stellt eine vielversprechende Flexibilitätsmaßnahme für die Fahrzeugendmontage bei gleichzeitiger Reduktion der Investitionskosten dar. Durch eine geeignete Vernetzung der Fahrzeuge untereinander sowie mit dem Montagesystem und der überlagerten Produktionssteuerung kann eine Verschmelzung von Produkt und Produktionssystem erreicht werden. Dabei ergeben sich jedoch vielfältige Herausforderungen an die Fahrzeugchassis, ihre Antriebskomponenten sowie die Produktionsinfrastruktur.
Um diese Konzepte zu validieren und die Vorteile einer flexiblen und investitionsarmen Montageinfrastruktur deutlich zu machen, wird im Aachener Zentrum für Elektromobilproduktion (ZEP) zusammen mit Partnern aus der Industrie ein Prototyp, bestehend aus selbstfahrenden Fahrzeugchassis, Bild 4, und entsprechender montageseitiger Infrastruktur aufgebaut, mit dem unterschiedliche Industrialisierungsszenarien des Konzepts untersucht werden.
Literatur:
Kampker, A.: Elektromobilproduktion. Aachen: Springer-Vieweg-Verlag, 2014.
Fremerey, F.: Erhöhung der Variantenflexibilität in Mehrmodell-Montagesystemen durch ein Verfahren zur Leistungsbestimmung. Berlin: Springer-Verlag, 1993.
Gottschalk, S. F.: Dedicated Flexibility. Komplexitätsoptimale Gestaltung manueller Serienmontage. Aachen: Shaker-Verlag, 2006.
Hu, S.; Zhu, X.; Wang, H.; Koren, Y.: Assembly system design and operations for product variety. CIRP Annals – Manufacturing Technology 60 (2011), No. 2, pp. 715–733.
Bauernhansl, T.: Die Vierte Industrielle Revolution – Der Weg in ein wertschaffendes Produktionsparadigma. In: Baurnhansl, T.; ten Hompel, M.; Vogel-Hauser, B. (Hrsg.): Industrie 4.0 in Produktion, Automatisierung und Logistik. Stuttgart: Springer-Vieweg-Verlag, 2014. Umsetzungsempfehlungen für das Zukunftsprojekt Industrie 4.0. acatech – Deutsche Akademie der Technikwissenschaften e.V., München, 2013.
Prof. Dr.-Ing. Achim Kampker M.B.A, Jahrgang 1976, studierte Maschinenbau mit der Vertiefungsrichtung Fertigungstechnik und promovierte 2004 am Lehrstuhl für Produktionssystematik des Werkzeugmaschinenlabors (WZL) der RWTH Aachen. Seit 2014 ist er Leiter des Lehrstuhls Production Engineering of E-Mobility Components (PEM) der RWTH Aachen. // Dr.-Ing. Christoph Deutskens M.Eng., Jahrgang 1982, studierte Maschinenbau an der RWTH Aachen sowie Industrial Engineering an der Tsinghua University in China. Seit Januar 2014 ist er am Lehrstuhl PEM als Oberingenieur tätig. // Dipl.-Ing. Kai Kreisköther, Jahrgang 1985, studierte Maschinenbau an der RWTH Aachen. Seit 2014 ist er Gruppenleiter der Gruppe Electric Powertrain des Lehrstuhls PEM. // Marius Schumacher M.Sc., Jahrgang 1988, studierte Maschinenbau an der RWTH Aachen. Seit 2015 ist er wissenschaftlicher Mitarbeiter am Lehrstuhl PEM.