Leichtbau-Kosten bewerten am Beispiel eines modularen Batteriekonzepts
Ein modulares Starter-Batteriekonzept bietet die Chance, die Masse eines elektrifizierten Fahrzeugs um 33 kg zu senken. Gleichzeitig gibt sie 10 Liter Bauraum frei. Die stückzahlabhängigen Leichtbaukosten liegen zwischen 16 bis 23 €/kg.

Ein modulares Starter-Batteriekonzept erschließt bei einem Elektrofahrzeug eine Gewichtsreduktion und sorgt gleichzeitig für einen Bauraumgewinn.
Foto: TGM
In der Automobilindustrie erfordern die sich verschärfenden Regularien neue Lösungen zur Senkung des Kraftstoffverbrauchs und der Schadstoffemissionen. Zeitgleich steigen jedoch auch Fahrzeuggewichte insbesondere durch die Elektrifizierung und Komfortverbraucher. Zwischen Gewicht und Kosten bewegt sich der Leichtbau, der auch Bauteile wie die etablierte Blei-Starterbatterie herausfordert.
Was ist der Status Quo?
Bereits 1911 verwendete Cadillac eine Blei-Starterbatterie und setzte damit einen Standard [1], der auch heute in elektrischen Automobilen weiterhin Anwendung findet. Die Batterie wird zum Start des Verbrennungsmotors oder zur Versorgung sicherheitsrelevanter Bauteile und auch zum Abschalten der Traktionsbatterie genutzt. Typischerweise ist das Gehäuse als Blockkasten aus säurebeständigem Polypropylen mit einer genormten Bodenleiste ausgeführt [2]. Der Antriebsstrang eines hybriden „BMW X5“ ist in Bild 1 gezeigt. Erkenntlich sind zwei Starterbatterien im Heck des Fahrzeugs oberhalb der Abgasanlage.
Der letzte wesentliche Technologieschritt war das Binden der Bleisäure, um Ladungsdurchsatz und Zyklenfestigkeit bei Start/Stopp zu gewährleisten [1]. Im Betrieb treten Beschleunigungen bis 3 g am Gehäuse auf, welche von der Batteriehalterung im Fahrzeug aufgenommen werden. Üblicherweise weisen die Starterleitungen Querschnitte bis zu 95 mm2 auf [1] und verlaufen zum Beispiel vom Einbauort der Batterie bis zum Verbrennungsmotor.
Was macht das Leichtbaupotenzial aus?
Aus Leichtbausicht ist die Blei-Technologie aufgrund ihrer geringen Energiedichte zu hinterfragen und entsprechend das Gehäuse sowie die Befestigung zu gestalten. Wie in Bild 2 gezeigt, liegt hinsichtlich der spezifischen Energie das Einsparpotenzial bei circa 46 Prozent und hinsichtlich der spezifischen Leistung bei circa 74 Prozent, wenn auf Lithium umgestellt wird. Neben der direkten Gewichtseinsparung ergeben sich weitere Vorteile. Beispielsweise wird der Halter insbesondere im Betrieb entlastet, die Batterie kann flexibel an anderen Einbauorten montiert werden und so die benötigte Länge der Starterleitung reduziert werden. Darüber hinaus bietet das steifere Gehäuse auch Vorteile bei Crash.
Worauf baut das neue Batteriekonzept & –Gehäuse auf?
Lithium ist das leichteste Feststoffelement und weist das niedrigste Standardpotenzial in der elektrochemischen Spannungsreihe auf [4]. Die davon abgeleiteten Lithium-Zellen können hinsichtlich der positiven Elektrode sowie der Bauform unterschieden werden. Ursprünglich umfasste die DIN SPEC 91252:2011–01 prismatische Zellen, Folien- und Rundzellen. Letztere Bauform ist die Basis des Konzepts, wobei Lithium-Eisen-Phosphat als positive Elektrode vorgesehen ist, da dieses bis 300 °C keine thermischen Effekte zeigt [4]. Neben der Erfüllung der Sicherheitsanforderungen ist für den Gewichtsvorteil entscheidend, dass bei Lithium-Eisen-Phosphat die Spannung über die Kapazität nahezu konstant bleibt [1], sodass die nutzbare Kapazität gesteigert wird. Die Auslegung der Zellen ist von der Firma Liteblox vorgenommen worden.
Das modulare Gehäuse ist von TGM Lightweight Solutions aus Berlin als Patent eingereicht und ausgehend von der Zelle so aufgebaut worden, dass die Zellhalter eine hohe Packungsdichte und Luftzirkulation erlauben. Darüber hinaus stützen die Zellhalter das Gehäuse gegen äußere Lasten. Die Formgebung wird zugunsten der Eigensteifigkeit prismatisch gestaltet. Diese Maßnahmen senken das Gewicht der Batterie. Um eine einfache Substitution von bestehenden Blei-Batterie möglich zu machen, kann diese wie die genormten Starterbatterien montiert werden.
Welche Gewichtsreduktion kann erreicht werden?
Als Referenz ist der erste Plugin-Hybrid der Kernmarke BMW, der „F15 Hybrid“, ausgewählt worden [5]. Dieser ist neben der Traktionsbatterie mit zwei Blei-Starterbatterien ausgestattet, welche zusammen eine Kapazität von 140 Ah bieten und ca. 41 kg wiegen [6]. Durch den Technologiewechsel auf Lithium-Eisen-Phosphat und die Konsolidierung der beiden Batteriegehäuse ergibt sich die in Bild 3 prognostizierte Gewichtseinsparung von über 33 kg.
Welche Fertigungsüberlegungen sind eingeflossen?
Bereits 1932 wurden Batteriegehäuse mittels Spritzguss gefertigt [7]. Basierend auf den ersten Konzeptskizzen ist der Fertigungsprozess vorausgewählt worden. Hierbei stand die Möglichkeit der Serienfertigung, der Fertigbarkeit ohne Nachbearbeitung sowie die Effizienz (inkl. Verwendung von Recyclaten) im Vordergrund. Ergebnis dieser Bewertung ist: Infrage kommende Verfahren sind der konventionelle Spritzguss bzw. der Spritzguss mit Gasinjektion oder Schäumen, sowie bei Gehäuseanpassungen auch die Extrusion. Vorteilhaft beim Einsatz von Thermoplasten ist deren Elastizität, die Schnappverbindungen erlaubt [8], was Montage- und Reparaturvorteile erschließt.
Für die Herstellung des Gehäuses ist die Spritzgießmaschine von Engel „victory 1560/140 tech“ aus Effizienzgründen ausgewählt worden. Deren holmlose Schließeinheit gestattet es, verhältnismäßig große und komplexe Werkzeuge auf der Maschine zu nutzen, sodass die Maschinengröße auf die benötigte Schließkraft statt der Werkzeugmaße ausgelegt werden konnte. Dies erlaubt es, zwei- und vierfach Kavitäten zu nutzen. Das bedeutet niedrigere Investitions- und Betriebskosten sowie einen kleinen Anlagenfootprint. Weitere Vorteile der Engel-Holmlostechnik sind schnelle Rüstprozesse sowie effiziente Automatisierungskonzepte, da der Roboter ohne Störkantenumfahrung direkt die Kavität erreichen kann.
In mehreren Iterationen ist unter Einbezug von Experten des National Manufacturing Institute Scotlands und der Firma Koller Formenbau das Gehäusekonzept iterativ hinsichtlich Kosten, Fertigung, Werkzeuggestaltung, Leichtbau und Konstruktion überarbeitet worden. Auch ist die Leichtbaukostenbewertung gegen eine Bewertung eines etablierten Zulieferer gemessen worden.
Wie sind die Leichtbaukosten zu bewerten?
Mit dem vollständigen Kostenmodell, welches mit der Software „SEER for Manufacturing“ von Galorath für alle entwickelten Konzepte abgebildet wurde, werden die Einflüsse von Werkzeug, Fertigung, Material, Schmelze und Läufersystem, Produktionskapazität und geometriebedingter Komplexität berücksichtigt. Neben der reinen Materialverarbeitung sind auch Montage und Abnahme berücksichtigt. Die Herstellkosten über der Stückzahl sind in Bild 4 für das hier vorgestellte Konzept mit Schnappverbindungen gezeigt. Die Fläche der Kreise symbolisiert die abgeschätzten Leichtbaukosten. Der größte Kostentreiber sind die angesetzten Batteriezellen und die Batterie-Steuerung. Daher ist fortlaufend zu untersuchen, welche Energiespeicher von welchen Herstellern verwendet werden können, um die Wirtschaftlichkeit zu gewährleisten.
Welche weiteren Vorteile sind erschlossen worden?
Mit dem Konzept sind Leichtbaukosten von 16 bis 23 €/kg ausgewiesen worden. Dies resultiert in einer Gewichtsreduktion von über 33 kg. Vor allem ist durch den Entfall der zweiten Batterie ein Bauraumgewinn von 10 Liter erschlossen worden. Das Batteriekonzept grenzt sich durch die bedarfsgerechte Dimensionierung sowie durch die Modularisierung und das zerstörungsfreie Öffnen mittels Schnappverbindungen ab. Weiterhin ist hervorzuheben, dass der Prozess zur Bewertung der Leichtbaukosten, also Abschätzung des Leichtbaupotenzials sowie der Kosten, erfolgreich angewendet werden konnte. Dieser Prozess ist darauf ausgelegt, verschiedene Bauteilkonzepte und Fertigungsverfahren bereits in den Frühphasen zu bewerten, um die Entscheidungsfindung zu unterstützen.
Literatur
- Wallentowitz, H.; Reif, K.: Hrsg. Handbuch Kraftfahrzeugelektronik. Grundlagen, Komponenten, Systeme, Anwendungen. ATZ/MTZ-Fachbuch. Wiesbaden: Vieweg-Verlag, 2006.
- Reif, K.: Batterien, Bordnetze und Vernetzung. Bosch Fachinformation Automobil. Wiesbaden: Vieweg+Teubner Verlag / GWV Fachverlage GmbH, 2010.
- Kable, G.: BMW X5 eDrive prototype first drive review [online], 2014. Internet: https://www.autocar.co.uk/car-review/bmw/x5/first-drives/bmw-x5-edrive-prototype-first-drive-review.
- Rahimzei, E.: Kompendium: Li-Ionen-Batterien. BMWi Förderprogramm IKT für Elektromobilität II: Smart Car – Smart Grid – Smart Traffic. Grundlagen, Bewertungskriterien, Gesetze und Normen, 2015.
- BMW. Der BMW X5 xDrive40e. [online]. Pressemappe, 2015. Internet: https://www.press.bmwgroup.com/deutschland/article/detail/T0207284DE/der-bmw-x5-xdrive40e?language=de.
- A2MAC1. A2Mac1 [Software], 2019. Zugriff am 15. November 2019.
- Laeis, M. E.: Der Spritzguß thermoplastischer Massen. 2. Auflage. München: Carl Hanser Verlag, 1959.
- Ehrlenspiel, K.; A. Kiewert, A.; U. Lindemann, U.; Mörtl, M.: Hrsg. Kostengünstig Entwickeln und Konstruieren. Berlin: Springer-Verlag, 2014.
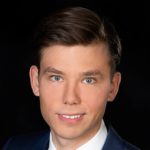
Florian Wätzold, M. Sc., arbeitet als Consultant / Projektleiter bei TGM Lightweight Solutions. Bild: Autor
Graeme McLaughlin, M. Eng., arbeitet als Senior Design Engineer am Advanced Forming Research Centre der Universität Strathclyde.
Dipl.-Ing. (FH) Ralf Utescheny arbeitet als Leiter Innovations-Management und Netzwerkkoordination bei Koller Kunststofftechnik.