Wie Cobots erfolgreich Elektronik-Funktionstests erledigen
Agilität ist für Elektronikhersteller der Schlüssel zum Erfolg. Gezeigt wird, wie ein Dienstleister seine Produktionskapazität mit Hilfe einer kollaborativen Robotik-Lösung verdoppelt hat.
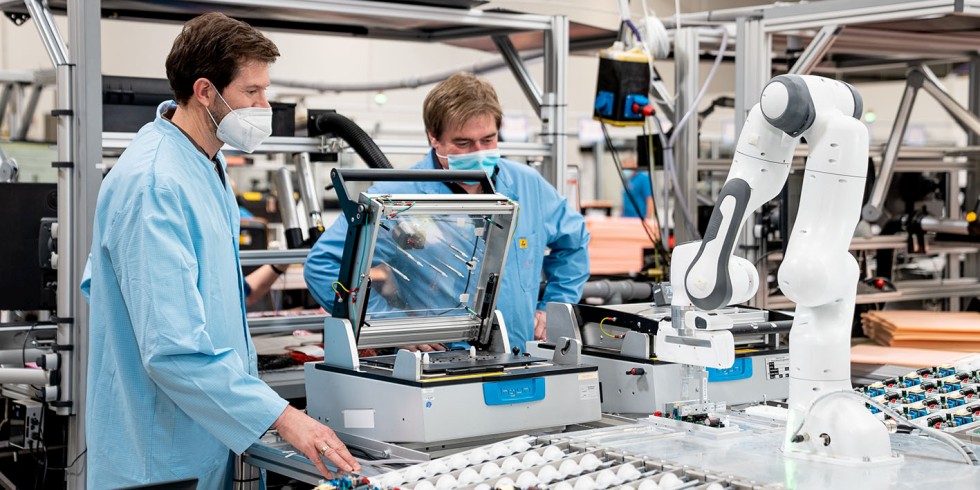
Ein Cobot (kollaborativer Roboter) erzielt unter anderem eine erhebliche Arbeitserleichterung für die Werks-Mitarbeiter, da er ihnen die monotone, manuelle Testtätigkeit abnimmt.
Foto: TQ
Die Elektronikbranche ist von stets steigenden Qualitätsansprüchen sowie einer von Kunden zunehmend gewünschten Individualisierbarkeit der Produkte gekennzeichnet. Hinzu kommt auch noch der wachsende Kostendruck in der Produktion. Alle diese Hürden für den wirtschaftlichen Betrieb eines Unternehmens lassen sich nur mit Hilfe cleverer Prozessautomatisierung bewältigen.
Cobot stellt Profitabilität plus Arbeitserleichterungen sicher
Das hat auch die Firma Frank Elektronik erkannt. Der Elektronik-Dienstleister setzt beim Testen von Flachbaugruppen auf eine kollaborative Robotik-Lösung von TQ und profitiert seither von einem stabilen, hochpräzisen Testprozess sowie der Verdopplung seiner Produktionskapazität. Darüber hinaus sorgt der eingesetzte Cobot (kollaborative Roboter) auch für eine erhebliche Arbeitserleichterung der Werkarbeiter, da er ihnen die monotone, manuelle Testtätigkeit abnimmt und damit Kapazitäten für anspruchsvollere Montagearbeiten schafft.
Frank Elektronik aus dem bayerischen Traunstein ist Teil der Elektronik Gruppe, einem überregionalen Verbund von mittelständischen EMS (Electronic Manufacturing Services)-Dienstleistern. Das Unternehmen ist auf Lichttechnik sowie die Bestückung von Platinen und Baugruppen spezialisiert. Seit Ende 2020 hat der Betrieb jetzt eine Robotik-Lösung von TQ für den automatisieren Funktionstest zweier verschiedener Flachbaugruppen im Einsatz.
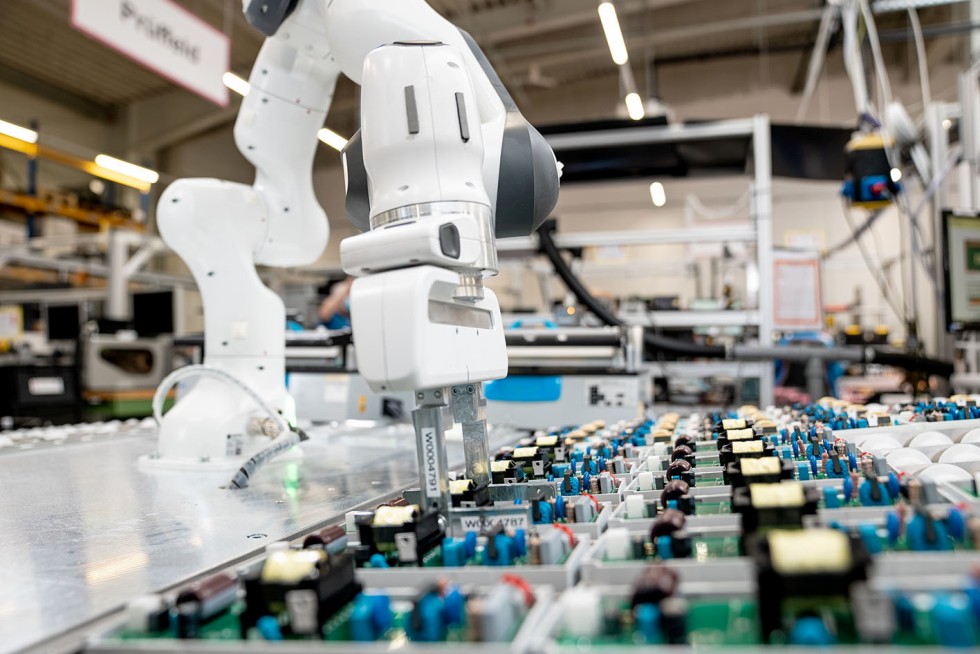
Der Elektronik-Dienstleister setzt beim Testen von Flachbaugruppen mit bestem Erfolg auf eine kollaborative Robotik-Lösung. Im Bild entnimmt der Cobot die Elektronikgruppe aus der Materialrutsche.
Foto: TQ
„Bevor wir den Cobot im Einsatz hatten, haben bei uns dieselben Mitarbeitenden den Testvorgang ausgeführt, die auch die nachfolgende Montage der Leiterplatten übernehmen“, erinnert sich Wolfgang Meyer, verantwortlich für das Prozess-Engineering bei Frank Elektronik. „Pro Schicht haben wir damals zwischen 430 und 450 Geräte gefertigt. Seitdem der Cobot jetzt das Test-Handling übernimmt und die Menschen nur noch montieren, konnten wir unsere Produktionskapazität verdoppeln“, freut sich Meyer.
Gleichzeitiger Test zweier verschiedener Flachbaugruppen
Konkret sieht der Anwendungsfall bei Frank Elektronik so aus: Die zwei verschiedenen zu testenden Gerätevarianten werden in ein Einlaufband gelegt und dann – je nach Variante – in zwei separaten Spuren zum Cobot transportiert. Dieser legt sie in eine Zwischenablage, entnimmt dort die Flachbaugruppe aus dem Gerät und legt sie in den Tester ein. Dann schließt er den Deckel der Testvorrichtung und scannt über einen Barcode die Seriennummer ein, was das Signal für den Testbeginn ist.
Nach Abschluss der Prüfung öffnet er den Deckel und das Testprogramm schickt ein „Gut“- oder „Schlecht“-Signal an die Steuerung. Somit weiß der Cobot, wo er die Einheit ablegen muss: Die als gut bewerteten Geräte in den grünen Bereich des Auslaufbands, die Ausfälle in den roten. Insgesamt dauert ein Testvorgang ungefähr 100 Sekunden. „Wir haben zwei Testeinrichtungen im Einsatz – für jeden Gerätetyp einen“, erläutert Meyer. „Eine der mechanischen Herausforderungen war es daher, dass der Cobot zwei verschiedene Flachbaugruppen gleichzeitig greifen kann“. Diese Anforderung löst der eingesetzte Franka-Emika-Roboter über einen Doppelgreifer, der es ihm ermöglicht, die zwei Varianten ohne Umrüstung zu verarbeiten.
Einfache und selbst-erklärende Bedienbarkeit des Cobots
Generell kann der Cobot verschiedene zu automatisierende Bewegungsabläufe per handgeführter, manueller Vorgabe lernen und lässt sich ganz einfach und intuitiv über ein Touchdisplay bedienen. Er kann im Fertigungsablauf auch noch weitere Aufgaben beim Löten oder beim Montieren übernehmen.
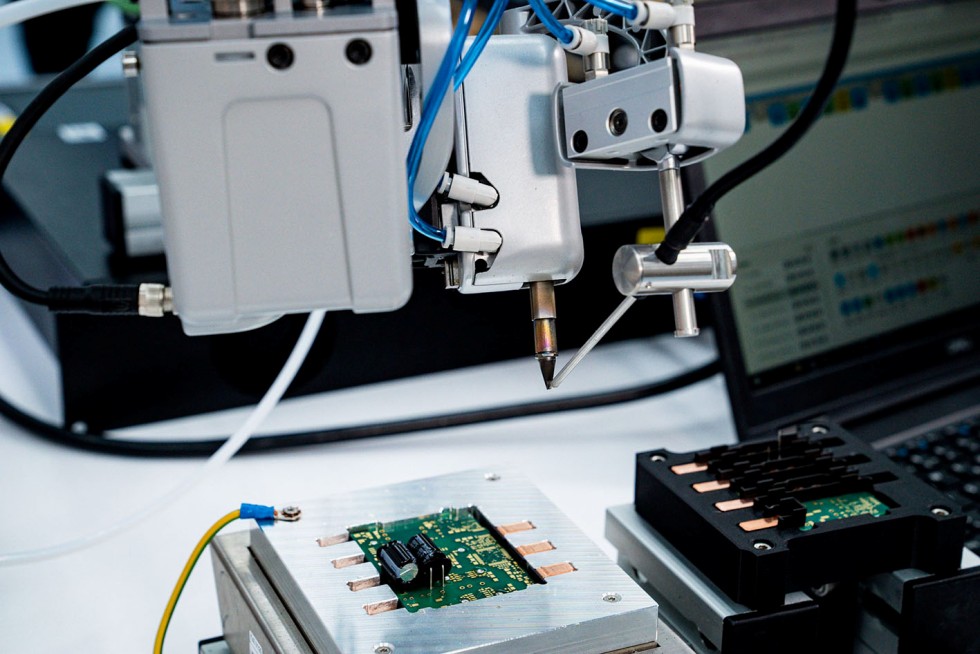
Löten einer Elektronik-Baugruppe: Ganz ohne Robotik-Vorkenntnisse und nur mit einer kleinen Einweisung lassen sich problemlos Programmwechsel durchführen.
Foto: TQ
Für die Programmierung verschiedener Abläufe (z.B. das Greifen eines Gegenstandes) werden aus einem Menü per Drag-and-Drop auf dem Laptop verschiedene Apps ausgewählt, angeordnet, und der Roboter führt sie dann aus. „Mit der richtigen Programmierung der zur Verfügung gestellten Apps konnten wir die komplette Zykluszeit des Testablaufs seit Projektbeginn sukzessive nochmals um 30 Prozent verringern“, freut sich Meyer. Die Bewegungsgeschwindigkeit ist mittlerweile perfekt auf die Dauer des Testprozesses eingestellt, so dass dieser an sich die Performance-Grenze markiert – und nicht der Cobot. „Wir stehen mit unserem Prozess circa bei 80 Prozent von dem, was der Cobot theoretisch verarbeiten könnte“, erläutert Meyer.
Ein großer Vorteil des Cobot-Systems ist, dass die Programmierung selbsterklärend ist. „Ich habe noch nie einen Programmierkurs besucht und bin trotzdem sofort mit der Lösung klargekommen“, so Meyer. „In den ersten zwei Monaten haben wir viel ausprobiert und im Februar 2021 den Umbau auf den zweiten Teststationen vollzogen. Insgesamt hat es dann ungefähr vier Wochen gedauert, bis wir den Prozess so modelliert hatten, wie er jetzt läuft“.
Auch die Mitarbeiter und Mitarbeiterinnen, die die Vorrichtung betreiben, können ganz ohne Robotik-Vorkenntnisse und nur mit einer kleinen Einweisung problemlos einen Programmwechsel durchführen – oder den Cobot nach einem potenziellen Stillstand wieder in Gang bringen. Das scheint jedoch nicht nötig, denn aktuell läuft die Cobot-Lösung bereits seit über sechs Wochen durchgängig und ohne irgendwelche ungeplanten Stillstände. „Im Endeffekt braucht sie mich nicht mehr“, resümiert Meyer.
Flexibles Umrüsten auf neue Produkte spart Zeit und Geld
Die Station wird es, so wie sie aktuell aufgebaut ist, schon bald nicht mehr geben, da die Produkte durch Nachfolgeprodukte abgelöst werden. Das Set-up wird dann zwar ähnlich, jedoch um einen Schritt erweitert sein, denn die neuen Geräte müssen auch im geschlossenen Zustand nochmals geprüft werden. „Wegen dieses Produktwechsels wäre die aktuelle Station früher nicht mehr brauchbar gewesen bzw. hätten wir sie komplett umbauen und alle Komponenten neu beschaffen müssen“, so Meyer. Mit der Cobot-Lösung profitiert Frank Elektronik jetzt von einer schnellen Umrüstzeit auf das neue Produkt. „Wir müssen lediglich einen neuen Greifer konstruieren und gegebenenfalls andere Schalen besorgen, aber der Rest kann so bleiben, wie er ist – das ist ein riesiger Vorteil“, weiß Meyer.
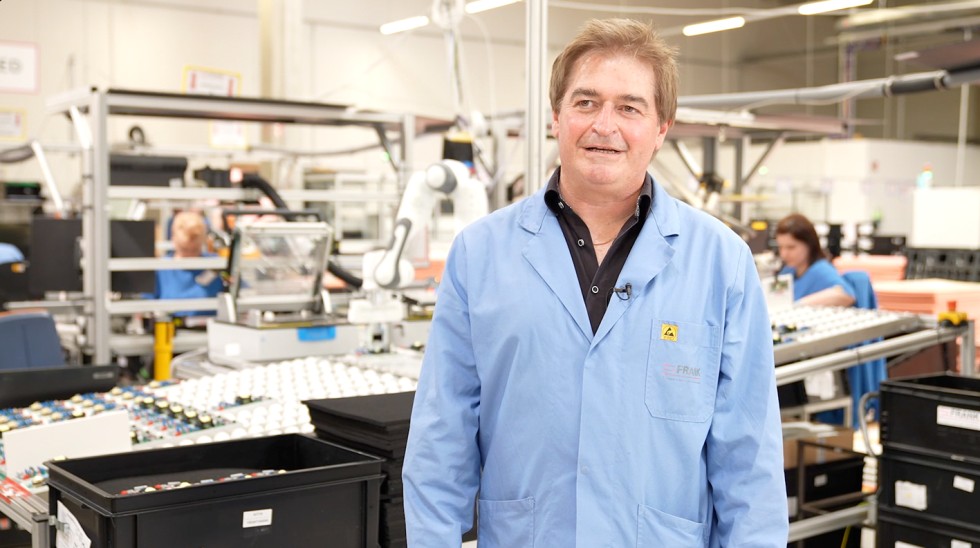
Wolfgang Meyer, Prozessingenieur bei Frank-Elektronik, ist mit der PCBA-Testanlage und dem genutzten Franka-Emika-Roboter vollauf zufrieden.
Foto: TQ
Spürbar optimierte Arbeit und effiziente, stabile Prozesse
Bei Frank Elektronik ist man mit der Lösung so zufrieden, dass für den zweiten Testprozess der neuen Produktlinien jetzt ein weiterer Cobot eingesetzt wird, um die Automatisierung und damit die Produktivitätssteigerung weiter zu erhöhen. „Ich bin sehr positiv gestimmt, dass wir noch weitere Systeme anschaffen werden. Beispielsweise für den zweiten Test beim geschlossenen Gerät. D.h. wir werden ein zweites System anschließen, das nach der Montage dann den zweiten Test durchführen wird.“
Bisher konnte Frank Elektronik mit nur einem Cobot die Produktionskapazität bereits verdoppeln und seine Mitarbeitenden gezielter für die Montage einsetzen. Diese müssen jetzt nicht mehr die Teststation bedienen und die einzelnen Tests abwarten, sondern können durchgehend ihrer Montagetätigkeit folgen. „Der Cobot ist für uns wirklich eine extrem hilfreiche Hand“, so das Fazit von Wolfgang Meyer.
Das könnte Sie auch interessieren:
Der genaueste Roboter der Welt
Tipps für eine sichere Mensch-Roboter-Kollaboration
Roboter programmieren endlich leicht gemacht – dank eines neuartigen Tools
Robert Vogel ist Automatisierungsexperte bei TQ Robotics in Seefeld.