Aus Giftabfall wird CO2-freier Stahl
Bei der Aluminiumherstellung fallen gigantische Mengen an giftigem Rotschlamm an. Mit Wasserstoff lässt sich daraus in einem Lichtbogenofen sehr reines Eisen gewinnen, das direkt in Stahl umgewandelt werden kann. Kann das profitabel sein?
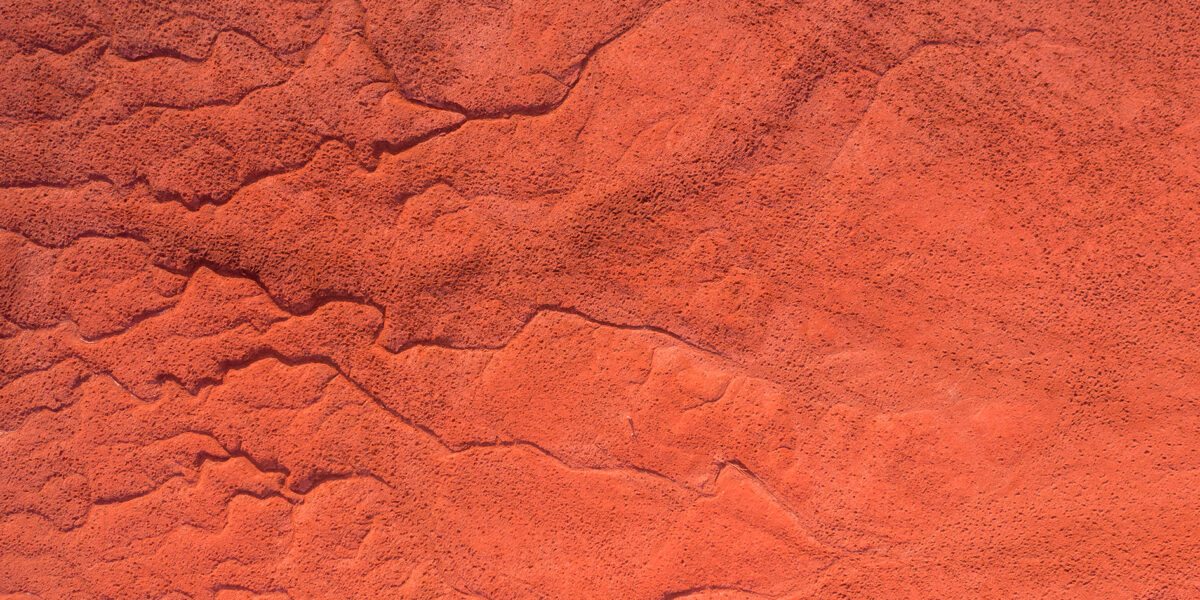
Rotschlamm enthält bis zu 60 % Eisenoxid.
Foto: PantherMedia/airpixel.hu
Aus giftigem Rotschlamm, einem Abfallprodukt aus der Aluminiumherstellung, lässt sich teilweise völlig oder zumindest weitgehend emissionsfrei Eisen gewinnen. Jährlich fallen dort 180 Mio. t Schlamm an, der auf riesigen Deponien gelagert wird. Daraus könnten Schätzungen der Max-Planck-Gesellschaft (MPG) zufolge rund 30 Mio. t Stahl gewonnen werden, und zwar ohne Emissionen von Kohlenstoffdioxid. In Deutschland wurden 2022 knapp 37 Mio. t Stahl erzeugt. Der Prozess würde sich sogar ökonomisch lohnen, sagt Matic Jovičevič-Klug, Materialforscher am Max-Planck-Institut für Eisenforschung in Düsseldorf, der maßgeblich an der Entwicklung des Verfahrens beteiligt war.
Wasserstoff schnappt sich die Sauerstoffatome auf dem Weg zum Stahl
Rotschlamm bekam seinen Namen von seiner Farbe. Die wiederum kommt von den großen Mengen an Eisenoxid, die darin enthalten sind. Genau auf diesen Rost haben es die Max-Planck-Forschenden abgesehen. Mithilfe von grünem Wasserstoff, der ohne jegliche Emission erzeugt worden ist, entreißen sie dem Rost die Sauerstoffmoleküle. Es entstehen Wasserdampf und Eisen, das mit den üblichen Verfahren in Stahl umgewandelt werden kann.
Schwermetalle werden aus dem Verkehr gezogen
Rotschlamm enthält bis zu 60 % Eisenoxid. In einem Lichtbogenofen, wie er in der Stahlindustrie genutzt wird, um Schrott zu recyceln, wird der Schlamm geschmolzen. Ein sogenanntes Plasma, das Wasserstoff enthält und sich bei der großen Hitze im Lichtbogen bildet, bindet die Sauerstoffatome. Das flüssige Eisen bleibt ebenso zurück wie flüssige anorganische Stoffe (Oxide). Die beiden Fraktionen lassen sich trennen. Die Oxide erstarren zu einem glasähnlichen Material, das etwa im Straßenbau verwendet werden kann. Darin gebunden sind die Schwermetalle, die ebenfalls im Rotschlamm steckten. Sie sind in den glasartigen Kristallen sicher verwahrt, können also nicht mehr ausgewaschen werden. Ein Teil der Metalle wie Chrom, die ebenfalls Bestandteile des Schlamms sind, finden sich zum Schluss im Eisen. Sie können als Veredelung drinbleiben oder im Rahmen der Umwandlung in Stahl abgetrennt und gesondert verwertet werden.
1,5 Milliarden Tonnen CO2 lassen sich einsparen
„Wenn man aus den 4 Mrd. t Rotschlamm, die bei der weltweiten Aluminiumproduktion bislang angefallen sind, mit grünem Wasserstoff Eisen erzeugen würde, könnte die Stahlindustrie fast 1,5 Mrd. t CO2 einsparen“, sagt Isnaldi Souza Filho, Forschungsgruppenleiter am Max-Planck-Institut für Eisenforschung. Dass ist etwa doppelt so viel wie die gesamten CO2-Emissionen Deutschlands pro Jahr.
Wirtschaftlichkeitsschwelle ist schnell erreicht
Eisen mit Wasserstoff aus Rotschlamm erzeugen nützt nicht nur der Umwelt. Der Prozess lohnt sich auch ökonomisch, wie das Forschungsteam in einer Analyse der Kosten nachgewiesen hat. Mit Wasserstoff und einem Strommix für den Lichtbogenofen aus nur teilweise regenerativen Quellen wäre das Verfahren bereits wirtschaftlich, wenn der Rotschlamm 50 % Eisenoxid enthielte. Berücksichtigt man noch die Kosten für Lagerung und Entsorgung des Rotschlamms, reicht bereits ein Anteil von 35 %.
Lichtbogenöfen sind ohnehin vorhanden
Mit makellos grünem Wasserstoff und Ökostrom ist bei den heutigen Kosten – den Aufwand für die Deponierung des Rotschlamms eingerechnet – ein Anteil von 30 bis 40 % Eisenoxid nötig, damit das entstehende Eisen am Markt konkurrenzfähig ist. „Das sind vorsichtige Abschätzungen, weil die Kosten für die Entsorgung des Rotschlamms wahrscheinlich eher niedrig berechnet sind“, sagt Filho. Ein weiter Vorteil aus Sicht der Praxis: Lichtbogenöfen sind in der Metallindustrie – auch in Aluminiumhütten – weit verbreitet. In vielen Fällen müsste die Branche also nur wenig investieren, um umweltverträglicher zu werden. „Uns war es wichtig, auch die ökonomischen Aspekte zu berücksichtigen“, sagt Dierk Raabe, Direktor am Max-Planck-Institut in Düsseldorf. „Jetzt kommt es auf die Industrie an, ob sie die Plasmareduktion von Rotschlamm zu Eisen auch einsetzt.“