Leichtbauwerkstoffe für den modernen Automobilbau
Aluminiumlegierungen zählen zu den wichtigsten Leichtbauwerkstoffen im modernen Automobilbau, konnten sich allerdings aufgrund der geringeren Festigkeit und Umformbarkeit noch nicht flächendeckend gegenüber den klassischen Stahlwerkstoffen durchsetzen. Derzeit stellen die tribologischen Bedingungen aktuell noch die größte Herausforderung und somit die Limitierung für den industriellen Einsatz dar, zumal die Voraussetzung für eine wirtschaftliche Fertigung hochfester Aluminiumbauteile die Vermeidung von adhäsivem Verschleiß bedingt, um eine ausreichend hohe Werkzeugstandzeit und Bauteilqualität zu gewährleisten. Der Lehrstuhl für Fertigungstechnologie hat daher in Kooperation mit dem Schmierstoffhersteller Holifa Fröhling GmbH & Co. KG, neuentwickelte, temperaturbeständige Schmierstofflösungen, welche frei von Bornitrid, Graphit und Molybdändisulfid sind, hinsichtlich des Einsatzverhaltens im Rahmen der nicht-isothermen Warmumformung der Aluminiumlegierung AA7075 untersucht.
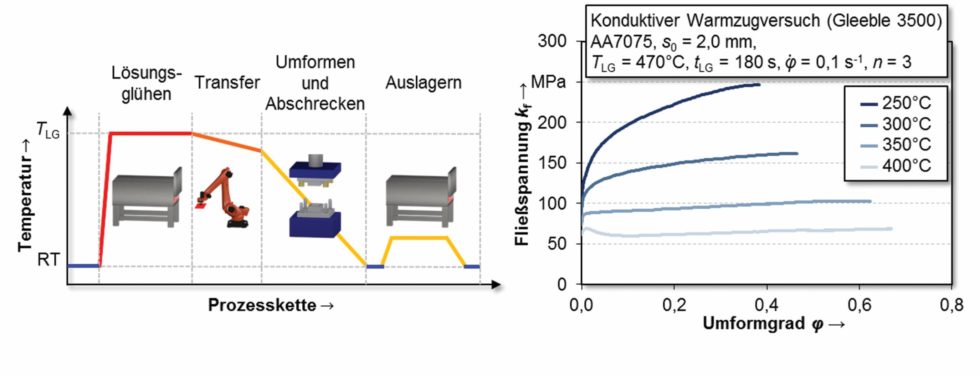
Bild 1: Verfahrensschritte beim Umformen unter Abschreckbedingungen (links) und das Fließverhalten des Werkstoffes AA7075 nach Lösungsglühen und anschließendem Umformen bei erhöhten Temperaturen (rechts). (Bild: FAU Erlangen)
Im Bereich der Karosserieaußenhaut werden Güten der 6000er-Serie bereits erfolgreich verwendet. Für Strukturbauteile ist der Einsatz von 5000er- und 6000er-Legierungen ebenso erfolgreich umgesetzt [1]. Crashrelevante Bauteile mit hohen Anforderungen hinsichtlich Festigkeit und Energieabsorption werden bislang nicht aus dem Leichtmetall hergestellt. Ein vielversprechender Ansatz, um Leichtbauweise auch in sicherheitsrelevanten Bereichen zu implementieren, ist die Verarbeitung hochfester Aluminiumlegierungen wie beispielsweise der 7000er-Serie. Diese zeichnen sich durch eine hohe Festigkeit, sehr gute Energieabsorption und Recyclingfähigkeit aus. Herausforderung beim Einsatz dieser Werkstoffe ist jedoch die eingeschränkte Umformbarkeit, weshalb für die Umformung meist temperaturgestützte Verfahren wie die Halbwarm- oder Warmumformung verwendet werden.
Abschreckumformen
Ein neuer Ansatz ist die nicht-isotherme Warmumformung hochfester Aluminiumlegierungen, auch Abschreckumformen genannt, ein Verfahren, welches bereits 2005 von Garrett et al. vorgestellt wurde [2], doch erst innerhalb der letzten Jahre beispielsweise am Lehrstuhl für Fertigungstechnologie [3] oder am Institut für Umformtechnik und Umformmaschinen in Hannover [4] verstärkt erforscht wird. In Anlehnung an die Verfahrensweise beim Presshärten hochfester Bor-Mangan-Stähle, wird der Werkstoff nach Wärmebehandlung und Transfer im kalten Werkzeug umgeformt und simultan abgeschreckt. Im Gegensatz zum Presshärten von Stahl werden ausscheidungshärtbare Aluminiumlegierungen während der Wärmebehandlung bei einer legierungsspezifischen Temperatur lösungsgeglüht, um die festigkeitsbedingenden Ausscheidungen im Gitter zu lösen und den Werkstoff dadurch gezielt zu entfestigen. Das anschließende schnelle Abschrecken durch den Werkzeugkontakt während der Umformung bildet dabei die Voraussetzung für eine Festigkeitssteigerung im Rahmen der Wärmebehandlung durch eine Ausscheidungshärtung am Ende der Prozesskette. Im Fall der hochfesten Aluminiumlegierung AA7075 beträgt die Mindestabkühlgeschwindigkeit für eine Ausscheidungshärtung beispielweise 100 K/s [5]. Das Prozessschema der nicht-isothermen Warmumformung kann Bild 1 (links) entnommen werden. Das Lösungsglühen in Kombination mit der direkt nachgeschalteten Umformung bei erhöhten Temperaturen wirkt sich dabei positiv auf das Umformverhalten aus. Konkret zeigt sich mit höherer Umformtemperatur eine signifikante Reduktion der Fließspannungen sowie eine Zunahme der Dehnungen, exemplarisch dargestellt anhand Warmfließkurven der Legierung AA7075 (Bild 1, rechts).
Die Vorteile, die sich daher aus diesem Verfahren ergeben, sind neben einer signifikanten Verbesserung der Formgebung auch eine erhöhte Maßhaltigkeit sowie geringere Bauteileigenspannungen.
Herausforderungen bei der nicht-isothermen Warmumformung
Aufgrund der erhöhten Umformtemperaturen von bis zu 450°C (7xxx Legierungen) werden hohe Anforderungen an die Prozesstechnik gestellt. Neben der Realisierung einer kurzen Transferzeit vom Ofen in das Werkzeug, sowie einer hohen Umform- und dadurch bedingten Abschreck- geschwindigkeit, werden die Werk- zeuge und Schmiersysteme hohen thermischen Belastungen ausgesetzt. Dies führt zu reduzierten Werkzeugstandzeiten, zumal Aluminium bei erhöhten Temperaturen zu Adhäsionen neigt und dies wiederum die Bauteilqualität negativ beeinflusst. Des Weiteren können Schmierstoffe aus dem Bereich der Kaltumformung, welche meist aus einer Öl- oder Silikonbasis bestehen, nur bedingt in diesen Temperaturbereichen eingesetzt werden. Neben einer signifikanten Viskositätsänderung aufgrund der schnellen Temperaturänderungen und einer dadurch verminderten Schmierleistung stellen niedrige Rauchpunkte von meist maximal 200°C sowie die Bildung gesundheitsschädlicher Abbauprodukte die limitierenden Faktoren für den industriellen Einsatz dar. Alternativ werden Schmierstoffsysteme auf Basis von Graphit, Bornitrid oder Molybdändisulfid in der Warmumformung angewendet, zumal diese eine hohe Temperaturbeständigkeit aufweisen, sich allerdings zum einen nur schwer von den hergestellten Bauteilen reinigen lassen und sich zum anderen speziell bei Aluminiumlegierungen negativ auf das Korrosionsverhalten auswirken können. Folglich stellen Schmierstoff- und Beschichtungssysteme einen der aktuellen Forschungsschwerpunkte im Umfeld der nicht-isothermen Warmumformung hochfester Aluminiumlegierungen dar.
Der Lehrstuhl für Fertigungstechnologie hat daher in Kooperation mit dem Schmierstoffhersteller Holifa Fröhling GmbH & Co. KG, neuentwickelte, temperaturbeständige Schmierstofflösungen, welche frei von Bornitrid, Graphit und Molybdändisulfid sind, hinsichtlich des Einsatzverhaltens im Rahmen der nicht-isothermen Warmumformung der Aluminiumlegierung AA7075 untersucht. Neben der Realisierung einer ausreichenden Schmierwirkung zur Herstellung von versagensfreien Bauteilen, stand hierbei auch die Reinigung der Werkzeuge und Bauteile im Fokus.
Qualifizierung von Schmierstoffen
Im Speziellen wurden drei unterschiedliche Schmierstoffe anhand von Napfzugversuchen analysiert. Die dabei eingesetzten Schmierstoffe unterscheiden sich grundlegend hinsichtlich ihrer Zusammensetzung. Im Einzelnen wurden eine bei Raumtemperatur pastöse Schmierstoffformulierung auf Basis synthetischer Kohlenwasserstoffe und anorganischer Pigmente (Holifa RVP 55 K) und zwei verschiedene Trockenschmierstoffformulierungen (Holifa HTP 147 und Holifa HTP 16) getestet. Schmierstoff A (Holifa HTP 147) ist dabei eine teilsynthetische Formulierung auf Wachsbasis mit anorganischen Pigmenten, während Schmierstoff B (Holifa HTP 16) ein Trockenschmierstoff auf Basis von Na- und Ca-Stearaten ist (Tabelle 1).
Für die Versuche wurde ein am Lehrstuhl für Fertigungstechnologie vorhandenes Napfzugwerkzeug in Kombination mit einer hydraulischen Tiefziehpresse (Lasco, TSP 100 So) mit einer maximalen Stößelkraft von 1000 kN verwendet. Die entsprechenden Werkzeugabmaße können Bild 2 entnommen werden.
Stempel und Matrize bestehen aus dem Warmarbeitsstahl 1.2367. Ronden des Werkstoffes AA7075-T6 mit einem Durchmesser d0 = 90 mm und einer Blechstärke von s0 = 2 mm wurden zunächst in einem Kammerofen (Rohde ME 87/13) bei der legierungsspezifischen Lösungsglühtemperatur wärmebehandelt, nach einer definierten Haltezeit entnommen und in das Werkzeug transferiert. Um ein vorzeitiges Abkühlen des Flansches durch den Kontakt zum Niederhalter während der Umformung zu vermeiden, wurde ein Distanzring mit einer Blechstärke von sd = 2,5 mm verwendet. Die Stößelgeschwindigkeit betrug 60 mm/s und die Näpfe wurden mit einem Ziehverhältnis von b = 1,8 und einer Ziehtiefe von t = 30 mm tiefgezogen. Die Schmierstoffapplikation fand ausschließlich werkzeugseitig statt, wobei in Abhängigkeit des eingesetzten Schmierstoffes und dessen Bestandteile unterschiedliche Auftragungsverfahren eingesetzt wurden. Neben einer Beölung mittels Pinsel für die Versuche mit der Paste Holifa RVP 55 K wurde für die Auftragung der pulverförmigen Schmierstoffe eine elektrostatische Applikationstechnik eingesetzt, welche die Haftung der Schmierstoffpartikel am Werkzeug sowie eine exakte lokale Dosierung gewährleistet.

Bild 3: Resultierende maximale Kräfte im Napfzugversuch unter Verwendung der Schmierstoffe A, B und C. (Bild: FAU Erlangen)
Zur quantitativen Bewertung der untersuchten Schmierstoffe wurden durch eine in den Stempel integrierte Kraftmessdose die Kraft-Weg-Verläufe während der Umformung aufgezeichnet. Bild 3 zeigt die maximal auftretenden Kräfte im Napfzugversuch bei den verwendeten Schmierstoffen A, B und C, welche signifikante Unterschiede aufweisen. Hierbei wird deutlich, welchen Einfluss der Schmierstoff auf den Tiefziehprozess hat. Neben einer unterschiedlichen Schmierwirkung führen die Schmierstoffbestandteile beziehungsweise die Schmierstoffzusammensetzung und die damit einhergehende Viskosität auch zu einem variierenden Abkühlverhalten des Werkstoffes. Dies wirkt sich wiederum auf das Verfestigungsverhalten und somit auf den Kraftbedarf während des Umformprozesses aus, siehe Bild 1 (rechts). Während pulverförmige Schmierstoffe nur einen lokalen Wärmeübergang von Blech zu Werkzeug zulassen, bilden pastöse Schmierstoffe einen vollständigen Film, welcher je nach Viskosität und Rauheit des Werkzeuges beziehungsweise der Platine einen metallischen Kontakt und dadurch einen höheren Wärmeübergang bedingen. Bei Verwendung der Schmierstoffe A und B konnten Bauteile ohne Versagen hergestellt werden. Der Kraftbedarf bei Schmierstoff A war im Vergleich zu Schmierstoff B doppelt so hoch, was auf eine verminderte Schmierleistung oder ein sehr rasches Abkühlen der Platine hinweist. Zusätzlich fällt auf, dass der verbleibende Flansch bei Schmierstoff A größer ist, was auf ein vermindertes Fließverhalten hindeuten lässt. Der mit Schmierstoff C hergestellte Napf versagte durch Bodenreißer, obgleich hier ein geringerer Kraftbedarf im Vergleich zu Schmierstoff A bereits zum Versagen führt. Bei allen untersuchten Schmierstoffen traten keine Aufschweißungen am Werkzeug auf und die Schmierstoffe ließen sich mit Lösungsmitteln wie Aceton oder leichten alkalischen Lösungen restlos von Werkzeug und Bauteil entfernen. Darüber hinaus durchgeführte Versuche mit bei Raumtemperatur flüssigen Schmierstoffformulierungen im Viskositätsbereich 150 mm2/s bei 40°C führten zu einem Bauteilversagen. Hier trat ein vorzeitiges Versagen der Näpfe durch Bodenreißer auf, die durch ein vorzeitiges Abreißen des Schmierfilms während des Tiefziehens erklärbar sind und daher nicht zusätzlich im Diagramm aufgeführt sind.
Fazit
Die nicht-isotherme Warmumformung ermöglicht die Fertigung hoch-fester Bauteile aus Aluminium, welche speziell für den Strukturleichtbau ein- gesetzt werden und somit einen Beitrag zur Senkung des Fahrzeuggewichts leisten können. Während die Grundlagen zur Umformbarkeit und zur Mikrostruktur bereits im Rahmen unterschiedlicher AiF-Projekte wie beispielsweise am Lehrstuhl für Fertigungstechnologie (18945 N „Fertigung hochfester Aluminiumbauteile durch Umformen unter Abschreckbedingungen“) oder am Institut für Umformtechnik und Umformmaschinen (18994 BR „Warmumformung von 7xxx Aluminiumlegierungen“) erforscht wurden und werden, stellen die tribologischen Bedingungen aktuell noch die größte Herausforderung und somit die Limitierung für den industriellen Einsatz dar, zumal die Voraussetzung für eine wirtschaftliche Fertigung hochfester Aluminiumbauteile die Vermeidung von adhäsivem Verschleiß voraussetzt, um eine ausreichend hohe Werkzeugstandzeit und Bauteilqualität zu gewährleisten. Da Maßnahmen zur Erhöhung der Werkzeugstandzeit wie beispielsweise durch Schmierstoffe oder Werkzeug- beschichtungen einen signifikanten Einfluss auf den Wärmeübergang und somit auf das Umformvermögen respektive die spätere Ausscheidungshärtung hat, sollten die tribologischen Bedingungen für eine ganzheitliche Prozessauslegung berücksichtigt und in Zukunft gezielt erforscht werden.
Literatur:
[1] Hirsch, J.: Aluminium in Innovative Light-Weight Car Design. Materials Transactions, 52 (5) 2011, S. 818–824
[2] Garrett, R.; Lin, J.; Dean, T.: Solution Heat Treatment and Cold Die Quenching in Forming AA6xxx Sheet Components: Feasability Study. Advanced Materials Research 6–8, pp. 673–680, 2005
[3] Degner, J.; Horn, A.; Merklein, M.: Experimental study on the warm forming and quenching behaviour for hot stamping of high-strength aluminum alloys. Journal of Physics: Conference Series 896 (1), 2017
[4] Behrens, B.-A.; et al.: Influences of the formability and mechanical properties of 7000-aluminum alloys in hot and warm forming. Journal of Physics: Conference Series 896 (1), 2017
[5] Ostermann, F.: Anwendungstechnologie Aluminium. Springer Vieweg, Berlin, Heidelberg 2014
Julia Degner, M.Sc., Gruppenleiterin Maßgeschneiderte Halbzeuge, Lehrstuhl für Fertigungstechnologie
Jürgen Herrmann, M.Sc., Gruppenleiter Werkstoffcharakterisierung und -Modellierung, Lehrstuhl für Fertigungstechnologie
Dr. rer. nat. Friedhelm Junker, Geschäftsführer, Holifa
Erik Berendt, Vertrieb und technische Beratung, Holifa
Prof. Dr.-Ing. habil. Marion Merklein Ordinaria, Lehrstuhl für Fertigungstechnologie
Kontakt: Lehrstuhl für Fertigungstechnologie Friedrich-Alexander-Universität Erlangen-Nürnberg, Egerlandstraße 13, 91058 Erlangen
Holifa Fröhling GmbH & Co. KG, Elseyer Straße 8, 58119 Hagen