Methodik zur Auswahl von Raffungsmodellen für beschleunigte Versuche
Raffungsmodelle beschreiben den Zusammenhang zwischen den Lebensdauern unter Beanspruchung im Versuch und im Feld. Für unterschiedliche Schädigungsmechanismen existiert eine Vielzahl von Modellen, um einen Raffungsfaktor für beschleunigte Versuche zu ermitteln. Ziel dieses Artikels ist es, einen Überblick über die Vielzahl an existierenden Raffungsmodellen zu geben und ein methodisches Vorgehen zur Auswahl des geeigneten Modells für den jeweiligen Anwendungsfall zu liefern.
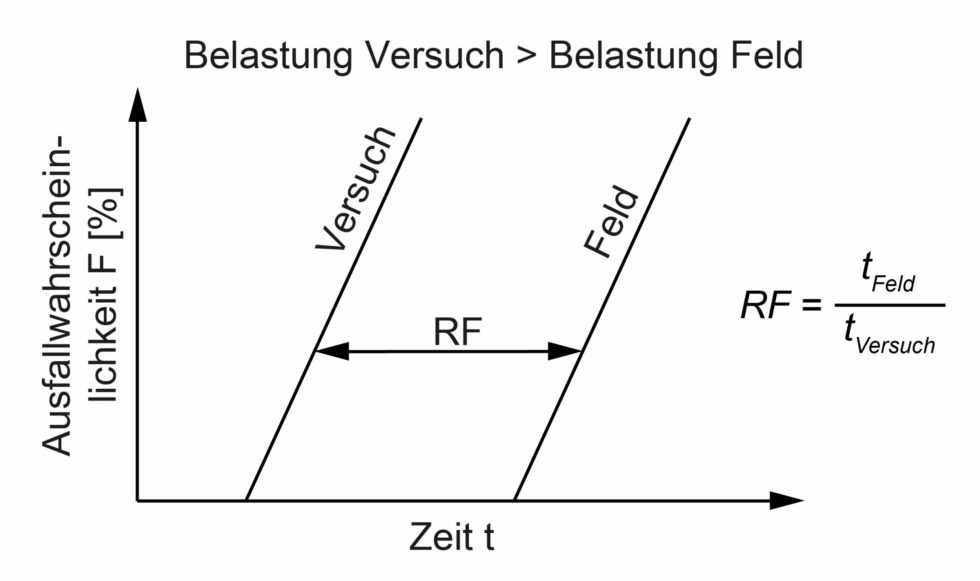
Bild 1 Raffung. Bild: Verfasser
1 Einleitung
Versuche zum Nachweis der Zuverlässigkeit eines Produktes können sehr zeitaufwendig und teuer sein. In der Praxis kommen deshalb oft beschleunigte Versuche zum Einsatz, bei denen die Versuchszeit mit Hilfe eines Raffungsfaktors RF, wie in Bild 1 dargestellt, verkürzt werden kann [1].
Der Zusammenhang zwischen den Beanspruchungen im Versuch und im Feld wird über Raffungsmodelle beschrieben und ermöglicht die Bestimmung eines Raffungsfaktors. Die Voraussetzung für die Anwendung eines Raffungsmodells ist, dass der Schädigungsmechanismus sich zwischen Feld und Versuch nicht ändert und somit auch der Weibull-Formparameter in der Lebensdauerverteilung bei unterschiedlich starken Beanspruchungen konstant bleibt [2].
Raffungsmodelle sind vom auftretenden Schädigungsmechanismus abhängig. Für die jeweiligen Schädigungsmechanismen existiert eine Vielzahl an Modellen um einen Raffungsfaktor zu ermitteln. Verschiedene Raffungsmodelle können dabei auch unterschiedliche Beanspruchungseinflüsse berücksichtigen. Zudem gibt es für manche Schädigungsmechanismen auch mehrere Raffungsmodelle. Der Anwender steht deshalb nicht selten vor dem Problem, das richtige Modell für den eigenen Anwendungsfall auswählen zu müssen. Ziel dieses Artikels ist es, einen Überblick über die Vielzahl an existierenden Raffungsmodellen zu geben und ein methodisches Vorgehen zur Auswahl des geeigneten Modells für den entsprechenden Anwendungsfall zu liefern. Hierbei wird durch die Zerlegung eines Systems in seine einzelnen Systemelemente die Komplexität des Problems verringert und so eine Funktionszuordnung der Elemente vereinfacht. Mit den auftretenden Beanspruchungen werden dann mögliche Schädigungsmechanismen von Wirkflächen bestimmt. Die Schädigungsmechanismen werden dann wiederum über die aufgezeigten Raffungsmodelle beschrieben. Die Auswahl eines geeigneten Modells für den jeweiligen Anwendungsfall wird über die Auswahlmethodik unterstützt.
2 Methodische Auswahl von Raffungsmodellen
Im Folgenden wird die Auswahlmethode eines für den entsprechenden Anwendungsfall geeigneten Raffungsmodells vorgestellt. Die Methode untergliedert sich in die in Bild 2 dargestellten fünf Schritte.
Die einzelnen Schritte des metho- dischen Vorgehens zur Auswahl eines geeigneten Raffungsmodells werden im Folgenden ausgeführt und anhand eines Steuergerätes beispielhaft veranschaulicht.
2.1 Schritt 1: Erstellen der Systemstruktur
Analog zur Systemtechnik sollte in einem ersten Schritt eine Systemstruktur für das zu analysierende System erstellt werden. Die Einteilung eines Produktes in Subsysteme kann hierfür zunächst anhand der VDA-Richtlinie für die FMEA [3] durchgeführt werden. Die Systemstruktur sollte jedoch nicht auf der Bauteilebene enden, sondern auf der Ebene der Wirkflächen. Wirk- flächen entsprechen dabei Flächen, die am Energie-, Stoff- und Informationsaustausch des betrachteten Systems beteiligt sind [4].
In Bild 3 ist beispielhaft die Erstellung der Systemstruktur für ein Steuergerät dargestellt (schwarz).
Das Steuergerät selbst stellt hierbei die Systemebene dar, die Ebene darunter (Mitte) zeigt die Bauteilebene und die unterste Ebene (rechts) zeigt die Ebene der Wirk- flächen. Dem Ball Grid Array (BGA) werden hier die Wirkflächen Lotverbindung, Leiterbahnen und Dielektrikum zugeordnet.
2.2 Schritt 2: Erstellen der Funktionsstruktur
Funktionen eines Produktes werden durch die im Produkt vorhandenen Subsysteme erfüllt. Im zweiten Schritt der Auswahlmethodik werden deshalb die Funktionen der Wirkflächen bestimmt. Die Funktionen der Wirk- flächen oder auch deren Fehlfunk- tionen sollen später helfen, die Ausfallmechanismen auf physikalisch-chemischer Ebene zu identifizieren.
Zur Bestimmung der Funktionen der Wirkflächen ist es hilfreich eine Funktionsstruktur des Produktes zu erstellen. Die Ermittlung der Funktionsstruktur sollte anhand der in Schritt 1 erstellten Systemstruktur erfolgen und die Funktionen den entsprechenden Subsystemen bzw. Wirkflächen zugeordnet werden. Dies entspricht dem Vorgehen der FMEA [1]. Leitlinien können hierfür als Hilfestellung dienen um alle Funktionen zu berücksichtigen [1], [5].
Für das Beispiel Steuergerät ist die Funktionsstruktur in Bild 3 grün dargestellt. Aus der Funktionsstruktur kann die Funktion der einzelnen Wirkflächen entnommen werden. Die Funktion der Lotverbindung des BGA ist hierbei beispielsweise die Verbindung von Bauteilkontakten zur Leiterplatte.
2.3 Schritt 3: Klärung der Betriebsbedingungen
Um mit Raffungsmodellen den Zusammenhang zwischen dem Raffungsfaktor und den Beanspruchungen im Versuch und im Feld zu beschreiben, ist es wichtig die im Feld herrschenden Betriebsbedingungen zu kennen. Damit ist es möglich, die Versuchsbedingungen festzulegen und einen Raffungsfaktor zu berechnen. Zu den Betriebsbedingungen zählen zum einen Signale, Energien und Stoffe, die über die Funktion der Wirkflächen verarbeitet werden, zum anderen auch Umgebungsbedingungen. Auftretende Betriebsbedingungen können z. B. Temperatur, Temperaturwechsel, relative Luftfeuchtigkeit, elektrische Spannung, Strom, Ionenfluss, mechanische Kräfte oder Spannungen usw. sein.
Die Betriebsbedingungen können entweder direkt für die zuvor bestimmten Wirkflächen des Produktes ermittelt werden oder über den bereits erstellten Funktionsbaum in der Top-down-Methode.
An der in Kapitel 2.2 angesprochenen Wirkfläche, der Lotverbindung, sollen hier beispielhaft die Betriebsbedingungen aufgeführt werden. Zunächst ist die Lotverbindung des BGA einer äußeren Temperatur ausgesetzt, welche statisch oder dynamisch wirkt. Weiter fließt ein Strom über die Lotverbindung. Dieser ist abhängig vom Schaltzustand und kann zu einer zusätzlichen dynamischen Erwärmung (Temperaturwechsel) der Wirkfläche führen. Die unterschiedliche thermische Ausdehnung von BGA und Leiterplatte kann außerdem zu mechanischen Spannungen in der Lotverbindung führen.
2.4 Schritt 4: Bestimmung der auftretenden Schädigungs- mechanismen
Die auftretenden Schädigungsmechanismen an den Wirkflächen sind physikalisch oder chemisch begründet. Mit der Kenntnis der auftretenden Beanspruchungen kann eine Hilfestellung zur Bestimmung der auftretenden Schädigungsmechanismen gegeben werden. Berücksichtigt sind die Schädigungsmechanismen Hot Carrier Injection, Oxidation, Surface Inversion, Migration, Ermüdung, Korrosion, Filamentwachstum und Zeitabhängiger Dielektrischer Durchbruch (engl. Time Dependent Dielectric Breakdown). In Bild 4 sind damit die Betriebsbedingungen und Schädigungsmechanismen berücksichtigt, die eine Auswahl aus den betrachteten und in Bild 5 dargestellten Raffungsmodellen erlaubt.
Mit Hilfe der zuvor ermittelten Betriebsbedingungen als auftretende Beanspruchungen können die potenziell eintretenden Schädigungsmechanismen identifiziert werden. Die Schädigungsmechanismen sind in Bild 4 in ovaler Form dargestellt. In Bild 4 ist außerdem zu sehen, dass einzelne Beanspruchungsarten alleine bereits einen Schädigungsmechanismus verursachen können, andere Schädigungsmechanismen jedoch verlangen mehrere definierte Beanspruchungsarten (gekennzeichnet mit &) oder eine von mehreren Beanspruchungsarten (gekennzeichnet mit ≥ 1). Die Temperatur hat bei fast allen Schädigungsmechanismen einen Einfluss.
Die genaue Identifizierung der auf-tretenden Schädigungsmechanismen sollte schließlich über eine Befundung des Produktes nach Schädigungseintritt erfolgen. Jedoch kann das bis- her vorgestellte Vorgehen helfen, die möglichen Schädigungsmechanismen einzugrenzen und schneller zu identifizieren.
Für das Beispiel der Lotverbindung lassen die dynamische Temperaturbeanspruchung und die, durch die Temperatur verursachten, mechanischen Spannungen nach Bild 4 auf den Schädigungsmechanismus der Ermüdung schließen.
2.5 Schritt 5: Auswahl der Raffungsmodelle
Für die im vorherigen Schritt ermittelten Schädigungsmechanismen der Wirkflächen können nun die passenden Raffungsmodelle ausgewählt werden, um den Zusammenhang zwischen den Beanspruchungen im Feld und im Versuch sowie dem Raffungsfaktor beschreiben zu können. Als Hilfe hierzu dient Bild 5, in dem die erste Spalte die auftretenden Schädigungsmechanismen zeigt. Nachdem hier der für den entsprechenden Anwendungsfall relevante Schädigungsmechanismus ausgewählt wurde, sind in Spalte zwei die von dem jeweiligen Raffungsmodell berücksichtigten Einflüsse zu finden. Mit der Kenntnis der in Schritt 3 geklärten Betriebsbedingungen und den daraus zu berücksichtigenden Einflüssen kann nun auf ein passendes Raffungsmodell für den jeweiligen Anwendungsfall geschlossen werden. In Spalte 3 ist der Name für das geeignete Raffungsmodell aufgeführt. Mit den Formeln in der vierten Spalte kann unter der Kenntnis der auftretenden Beanspruchungen im Versuch und im Feld sowie den entsprechenden produktabhängigen Modellparametern ein Raffungsfaktor zwischen der Lebensdauer im Feld und der Lebensdauer im Versuch berechnet werden. In den aufgeführten Formeln beschreibt der Index S (engl. stress) die erhöhte Beanspruchung im Versuch und der Index U (engl. use) die Beanspruchung im Feld. Die letzte Spalte von Bild 5 zeigt für alle betrachteten Raffungsmodelle noch eine Quelle. In den Quellen sind weitere Erklärungen zu den Modellen zu finden.
Für das Beispiel der Lotverbindung kann nun, ausgehend vom Schädigungsmechanismus Ermüdung, mit den Einflüssen Temperaturwechsel und maximale Temperatur, die Anwendung des Norris-Landzberg- Modell empfohlen werden. Hier wird mit DT der Temperaturwechselhub berücksichtigt, mit T die maximale Temperatur und die Temperaturwechselfrequenz mit f. Der jeweilige Einfluss wird über die Modellparameter o, p und Ea beschrieben.
Für das beispielhaft betrachtete Steuergerät konnte mit Hilfe der aufgezeigten Methodik das Norris-Landzberg Modell als geeignetes Raffungsmodell für den Schädigungsmechanismus Ermüdung und die auftretenden Betriebsbedingungen ausgewählt werden. In der Anwendung konnte die Eignung des Modells für den beschriebenen Anwendungsfall bestätigt werden.
3 Zusammenfassung und Ausblick
Das gezeigte Vorgehen erlaubt die methodische Auswahl eines Raffungsmodells für den jeweils vorliegenden Anwendungsfall anhand der fünf vorgestellten Schritte. Mit dem ausgewählten Modell kann nun die zeitliche Raffung bis zum Auftreten eines Ausfalls in Abhängigkeit der Beanspruchungen im Versuch und im Feld beschrieben werden. Hierzu ist jedoch auch die Kenntnis der jeweiligen Modellparameter nötig, die den jeweiligen Einfluss der einzelnen Einflussfaktoren beschreiben. Beim Basquin-Modell ist dies beispielsweise der Parameter y. Die Modellparameter sind produktabhängig und sollten zunächst über Versuche ermittelt werden. In manchen Fällen ist es jedoch auch möglich die Modellparameter aus der Literatur zu übernehmen.
Literatur:
[1] Bertsche, B.; Lechner, G.: Zuverlässigkeit im Fahrzeug- und Maschinenbau : Ermittlung von Bauteil- und System-Zuverlässigkeiten. 3., überarb. u. erw. Aufl. Berlin, Heidelberg: Springer, 2004
[2] Nelson, W.: Accelerated testing: Statistical models, test plans and data analyses. Pbk. ed. Hoboken, N.J.: Wiley-Interscience, 2004
[3] VDA 4.2. 2003: Sicherung der Qualität vor Serieneinsatz
[4] Albers, A.; Matthiesen, S.: Konstruktionsmethodisches Grundmodell zum Zusammenhang von Gestalt und Funktion technischer Systeme. In: Konstruktion (2002), H. 7/8, S. 55–60
[5] Pahl, G.; Beitz, W.; Feldhusen, J.; Grote, K.-H.: Konstruktionslehre: Grundlagen erfolgreicher Produktentwicklung Methoden und Anwendung. 6. Auflage. Berlin, Heidelberg: Springer, 2005
[6] Jedec Solid State Technology Association JEP122G. 10–2011. Failure Mechanisms and Models for Semiconductor Devices
[7] Gale, R. J.: Epoxy Degradation Induced Au-Al Intermetallic Void Formation in Plastic Encapsulated MOS Memories. In: 22nd International Reliability Physics Symposium, 1984, S. 37–47
[8] Rudra, B.; Pecht, M.; Jennings, D.: Assessing time-to-failure due to conductive filament formation in multi-layer organic laminates. In: IEEE Transactions on Components, Packaging, and Manufacturing Technology: Part B 17 (1994), Nr. 3, S. 269–276
[9] Blattau, N. ; Hillman, C.: A Comparison of the Isothermal Fatigue Behavior of Sn-Ag-Cu to Sn-Pb Solder. In: International Annual Conference on Surface Mount Technology Association (SMTA), 2005
[10] Tebbi, O.; Guérin, F.; Dumon, B.: Statistical Analysis of Accelerated Experiments in Mechanics Using a Mechanical Accelerated Life Model. In: Annual Reliability and Maintainability Symposium, 2003, S. 124–131
[11] Held, M.; Jacob, P.; Nicoletti, G.; Scacco, P.; Poech, M.-H.: Fast power cycling test of IGBT modules in traction application. In: Second International Conference on Power Electronics and Drive Systems, 1997, S. 425–430
[12] Norris, K. C.; Landzberg, A. H.: Reliability of Controlled Collapse Interconnections. In: IBM Journal of Research and Development 13 (1969), Nr. 3, S. 266–271
[13] Dauksher, W.: A Second-Level SAC Solder-Joint Fatigue-Life Prediction Methodology. In: IEEE Transactions on Device and Materials Reliability 8 (2008), Nr. 1, S. 168–173
[14] Salmela, O.: Acceleration Factors for Lead-Free Solder Materials. In: IEEE Transactions on Components and Packaging Technologies 30 (2007), Nr. 4, S. 700–707
[15] Matkowski, P.: Acceleration factors of combined reliability tests of lead-free SnAgCu BGA interconnections. In: 18th European Microelectronics and Packaging Conference (EMPC): IEEE, 2001
[16] Osenbach, J. W.; Reynolds, H. L.; Henshall, G.; Parker, R. D.; Peng Su: Tin Whisker Test Development-Temperature and Humidity Effects Part II: Acceleration Model Development. In: IEEE Transactions on Electronics Packaging Manufacturing 33 (2010), Nr. 1, S. 16–24
[17] Welsher, T. L. ; Mitchell, J. P. ; Lando, D. J.: CAF in Composite Printed-Circuit Substrates: Characterization, Modeling and a Resistant Material. In: 18th International Reliability Physics Symposium, 1980, S. 235–237
[18] Takeda, E.; Suzuki, N.: An empirical model for device degradation due to hot-carrier injection. In: IEEE Electron Device Letters 4 (1983), Nr. 4, S. 111–113
[19] Ong, T.-C. ; Ko, P.-K. ; Hu, C.: Hot-carrier current modeling and device degradation in surface-channel p-MOSFETs. In: IEEE Transactions on Electron Devices 37 (1990), Nr. 7, S. 1658–1666
[20] Sim, S. P.; Lawson, R. W.: The Influence of Plastic Encapsulants and Passivation Layers on the Corrosion of Thin Aluminium Films Subjected to Humidity Stress. In: 17th International Reliability Physics Symposium, 1979, S. 103–112
[21] Black, J.: Metallization failures in integrated circuits : MOTOROLA INC PHOENIX AZ SEMICONDUCTOR GROUP, 1968
[22] Weertman, J.: Creep of Aluminum Single Crystals. In: Journal of Applied Physics 27 (1956), Nr. 7, S. 832–834
[23] Chen, F.; Shinosky, M.: Addressing Cu/Low-k Dielectric TDDB-Reliability Challenges for Advanced CMOS Technologies. In: IEEE Transactions on Electron Devices 56 (2009), Nr. 1, S. 2–12
[24] Chen, I. C.; Holland, S.; Hut, C.: A quantitative physical model for time-dependent breakdown in SiO2. In: 23rd International Reliability Physics Symposium, 1985, S. 24–31
[25] Nicollian, P. E.; Hunter, W. R.; Hu, J. C.: Experimental evidence for voltage driven breakdown models in ultrathin gate oxides. In: IEEE International Reliability Physics Symposium Proceedings. 38th Annual, 2000, S. 7–15
[26] Wu, E. Y.; Vayshenker, A.; Nowak, E.; Sune, J.; Vollertsen, R.-P.; Lai, W.; Harmon, D.: Experimental Evidence of T/sub BD/ Power-Law for Voltage Dependence of Oxide Breakdown in Ultrathin Gate Oxides. In: IEEE Transactions on Electron Devices 49 (2002), Nr. 12, S. 2244–2253
AutorenDipl.-Ing. Frank JakobMartin Kimmelmann, M.Sc.Prof. Dr.-Ing. Bernd Bertschealle:Institut für MaschinenelementeUniversität StuttgartPfaffenwaldring 970569 StuttgartTel.: 07 11/6 85-6 99 54E-Mail: jakob@ima.uni-stuttgart.dewww.ima.uni-stuttgart.de