Fortgeschrittene Konstruktionstechniken zur Kühlkanalgestaltung in Stranggießkokillen
Dieser Beitrag stellt eine Konstruktionsmethodik vor, die im Bereich der Stranggießtechnik ihre Anwendung findet und insbesondere eine prozessgerechte Gestaltung der Kokillen unter Beachtung fertigungstechnischer Restriktionen absichert. Fortgeschrittene Modellierungstechniken auf Basis leistungsfähiger 3D-CAD-Systeme erlauben eine flexible konstruktive Gestaltung der Kühlkanalgeo-metrie von Kokillenkupferplatten. Zugleich ergeben sich hier Möglichkeiten, gestaltbestimmende Geometrieelemente direkt in das CAM-System zu transferieren bzw. für die NC-Programmierung zu nutzen. Anwendung finden solche Spezialplatten in Kokillen im Maschinenkopf moderner Hochleistungs-Brammenstranggießanlagen.
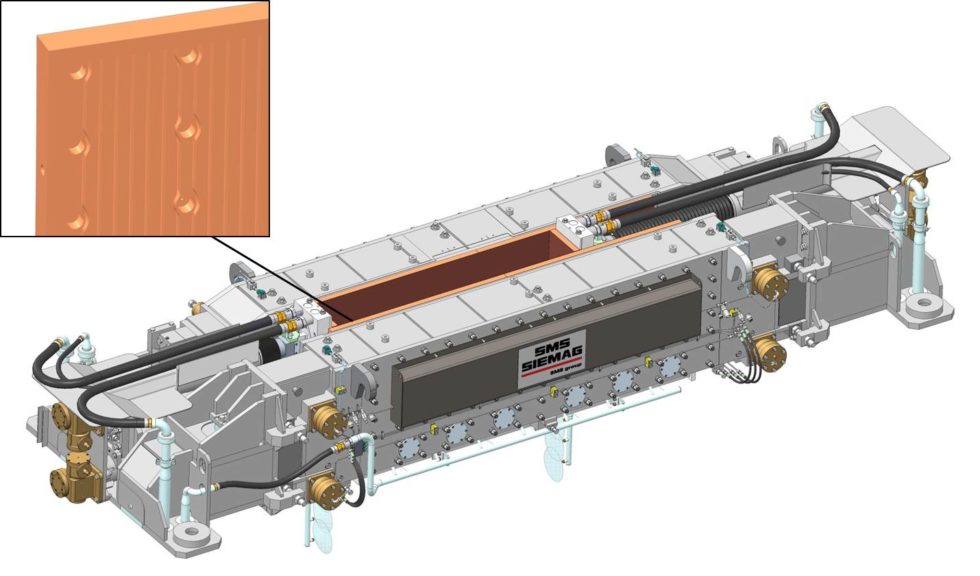
Bild 1: 3D-Modell einer Stranggießkokille mit Kupferplatten. (Bild: SMS Siemag)
1 Problemstellung
Wasserdurchströmte Kupferplatten der Kokille sind in Stranggießanlagen das zentrale Element für den Wärmeentzug aus dem Flüssigstahl. Sie leiten die primäre Erstarrung ein und bilden die Grundlage für die Formgebung der späteren Stahlbramme. Da in der Kokille die erste Strangschale gebildet wird und damit, neben der Form, auch die innere und äußere Qualität der Bramme maßgeblich beeinflusst wird, kommt einer guten Kühlwirkung eine besondere Bedeutung zu (Bild 1).
Mit der Weiterentwicklung der Technologie des Stranggießens und der Gießpulver sowie der Entwicklung von Sonderstählen steigen die Anforderungen an die Kokillengestaltung. Auf der einen Seite wird eine hohe Produktivität der Anlage gefordert, auf der anderen Seite sind höchste Qualitätsanforderungen an das stranggegossene Produkt gestellt. Hochfeste Stähle und insbesondere sogenannte peritektische Stähle lassen sich schwerer vergießen als einfache Kohlenstoffstähle. Es kann zu Rissbildungen und lokalen Einziehungen kommen oder die Einhaltung der Form nach dem Austritt aus der Kokille ist aufgrund von Ausbauchungen der Strangschale schwieriger. Mit zunehmender Gießgeschwindigkeit steigen auch die Temperaturbelastungen der Kupferplatten. Im Zuge konstruk-tiver Umbauten wurden zwar häufig die Randparameter wie Kokillenlänge, Gießpulver und Gießgeschwindigkeit geändert und damit die Anforderungen an die Kokille erhöht, nicht jedoch das Design der Kupferplatten angepasst. Da die Platten einer starken chemischen und thermischen Beanspruchung im Bereich des Flüssigstahlspiegels unterliegen und durch die hohe Reibung der Strangschale in Verbindung mit dem inneren Druck der Flüssigstahlsäule im Bereich des Kokillenaustritts stark abrasiv abgenutzt werden, muss eine regelmäßige mechanische spanende Überarbeitung der mit dem Flüssigstahl und der Strangschale in Kontakt stehenden Heißseite der Kupferplatte erfolgen.
Die formgebende Oberfläche wird durch die Überarbeitung quasi wieder in den Neuzustand versetzt, wobei aber die Platte 1 – 2 mm an Materialdicke verliert. Aus wirtschaftlichen Gründen werden bei einigen Betreibern die Kupferwandstärken vor den Wasserkanälen immer stärker reduziert, woraus sich sehr geringe Restwandstärken vor den Kühlkanälen ergeben. Die Kupferplatten werden also bis an die Grenzen ausgenutzt.
Wenn allerdings dadurch zu geringe Restwandstärken vor den Kühlkanälen auftreten, kann es, bei zusätzlich ungünstig konstruierter Kühlkanal-geometrie, zu lokalen Temperaturerhöhungen insbesondere im Bereich der Befestigungsschrauben kommen.
Wenn dies mit einer geringen Fließgeschwindigkeit des Wassers in den Kühlkanälen einhergeht und eventuell sogar Ablagerungen in den Kanälen vorliegen, beeinflusst dies die Wärmeabfuhr negativ. Das wiederum kann die Bildung von Längsrissen auf dem Produkt begünstigen.
Da die Kupferplatten als Verschleißteil ständig ersetzt werden müssen, muss der Konstrukteur neben der funktionalen Gestaltung auch der Wirtschaftlichkeit der Fertigung ein besonderes Augenmerk schenken.
Das Fertigen von Kühlkanälen mit Hilfe von Scheibenfräsern hat sich als Stand der Technik etabliert. Bis heute können damit ein Großteil der Kokillenanforderungen wirtschaftlich und funktional gut erfüllt werden. Nachteilig ist allerdings, dass sich bedingt durch den Scheibenfräserradius im oberen Endbereich der Kupferplatten und am Austritt die Wandstärke vergrößert und sich damit dort die Kühlwirkung verschlechtert. So kann z. B. im Auslaufbereich der Kokillenkupferplatte durch zu große Wandstärken ein Wiederaufheizen der Strangschale das Durchbruchrisiko erhöhen (Bild 2).
Eine Verkleinerung der Radien kann bei Scheibenfräsern nur begrenzt realisiert werden, bedingt durch die notwendige Tiefe der Nut und den Mindestdurchmesser des Fräskopfes.
2 Lösungsansatz
Eine Möglichkeit zur Vermeidung der vorgenannten Problemstellung ist die spezifische dreidimensionale Gestaltung der Kühlkanäle durch wissensbasierte CAD-Techniken [2]. Für Fräsprozesse sind geeignete Leitkurven, mit denen letztendlich auch die Werkzeugwege beschrieben werden können, von besonderer Bedeutung. Im betrachteten Fall werden Kurven-Projektionstechniken eingesetzt, um eine anforderungsgerechte und flexible Bahnkurvendefinition zu ermöglichen.
Mit Hilfe von Kugelfräsern oder Schaftfräsern kann entlang einer vordefinierten Bahnkurve eine über der Kokillenhöhe angepasste variable Kühlkanaltiefe dw (y) vorgegeben werden. Im Vergleich zur konventionel-len Fertigung mittels Scheibenfräser erlauben Fingerfräser das Umfahren der Befestigungsgewinde oder anderer Bereiche der Platten wie zum Bei- spiel von Bohrlöchern für Thermoelemente.
Gerade im oberen thermisch am höchsten belasteten Primärkühlbereich der Kupferplatten kann dadurch eine Vergleichmäßigung der Kühlkanalanordnung erreicht werden. Durch gleichmäßige horizontale Abstände P von Kühlkanal zu Kühlkanal kann die Ausbildung einer ausgeprägten Ab-weichung vom idealen Isothermenverlauf im Bereich zwischen den Befestigungsbolzen vermieden werden.
Hierbei können Fräser mit Durchmessern von 5 – 8 mm zum Einsatz kommen. Der Konstrukteur muss bei der Dimensionierung und Auslegung die verfahrenstechnischen Anforderungen kennen. Diese Eckdaten wie Strömungsgeschwindigkeit in den Kühlkanälen oder die spezifische Wasserbeaufschlagungsdichte und Wasser- bedeckung können in Auslegungs- dateien hinterlegt sein und mit dem CAD-System verknüpft werden [3]. Moderne 3D-CAD Programme erlauben eine flexible Konstruktion der Kanalverläufe und das Ein- und Auslesen von Parametern. Zur Definition der Nutgrundtiefe wird zunächst eine Nutgrundkonturfläche generiert, die aus einer flexibel anpassbaren Nutgrundkonturkurve erzeugt wird (Bild 4). Im einfachsten Fall ist es eine Profilfläche, die rechnerintern letztendlich durch die Parallelverschiebung der Konturkurve erzeugt wird.
Die Konturkurve kann gezielt den metallurgischen Anforderungen an die Kühlwirkung lokal und über der Plattenhöhe angepasst werden. Entsprechende Möglichkeiten sind in dem Patent [4] beschrieben.
Im zweiten Schritt definiert der Konstrukteur die Kühlnutanordnung über der Plattenbreite. Dabei wird er die kühltechnischen Grundanforderungen wie spezifische Wasserbeaufschlagung und Wassergeschwindigkeit berücksichtigen. Die Eingangsdaten können dem Konfigurationsmodell in Form von Layoutparametern übergeben werden. Ebenso können die Input-Parameter mit einer externen Excel-Analyse verarbeitet werden oder implizit im CAD-System über Parameterbeziehungen umgesetzt und angekoppelt werden. Aus der nominellen Brammenbreite Bnom und den eingeplanten bzw. vorhandenen Wasservolumenströmen je Kühlplatte sowie den Geometrieparametern des Modells lassen sich wesentliche Auslegungs-Kontrollwerte für den Konstrukteur ermitteln und rechnerunterstützt ausgeben. Die erforderliche Kühlwassermenge kann über die spezifische Wasserbeaufschlagungsdichte w in [l/mm . min] kontrolliert werden.
Die am Wärmeaustausch beteiligte Umfangslänge Uakt der Breitseitenkupferplatte kann aus den Dicken der Schmalseitenplatten dcu,mech,ss und des maximalen Kokillenöffnungsmaßes in Breitenrichtung ermittelt werden. Der Faktor K berücksichtigt das Schrumpfverhalten der Bramme auf dem Weg von der Kokille bis zum Endprodukt, der fertigen Stahlbramme.
und
Uakt = Bo,max + 2dcu,mech,ss
Typische Werte für w liegen bei 2.0 – 2.2 [l/mm . min].
Aus der Anzahl der Kühlkanäle Nw,BS, deren Breite bw,BS und der aktiven Umfanglänge der Breitseitenplatte Uakt kann man die sogenannte Umfangs-bedeckung Z als Bewertungsgröße ermitteln.
Die Umfangsbedeckung Z [%] sollte zwischen 20 und 25 % liegen. Sie ergibt sich zu
Weiterhin wird die Wassergeschwindigkeit in den Kühlkanälen kontrolliert.
Die erforderlichen Werte liegen im Erfahrungswissen des Konstrukteurs und Verfahrensingenieurs. Sie sollten 6 m/s nicht unterschreiten.
Die Heißseitentemperatur der Platte lässt sich dann berechnen, wenn die lokale Wärmestromdichte bekannt ist. Sie kann auf der Messung des Temperaturgradienten innerhalb der Platte mit Hilfe von mindestens zwei hintereinander angeordneten Thermoelementen basieren oder wird unter Zuhilfenahme verschiedener Formelansätze, die sich in der praktischen Anwendung als gute Näherung herausgestellt haben [5], abgeschätzt:
oder nach [6]:
Vor allem wird die Temperaturbelastung der Platten durch die Gießgeschwindigkeit, die Stahlsorte und auch durch die Schichtdicken und Leitfähigkeiten der aus den eingesetzten Gießpulvern entstehenden Gießschlackenfilmen und Luftspalten bestimmt.
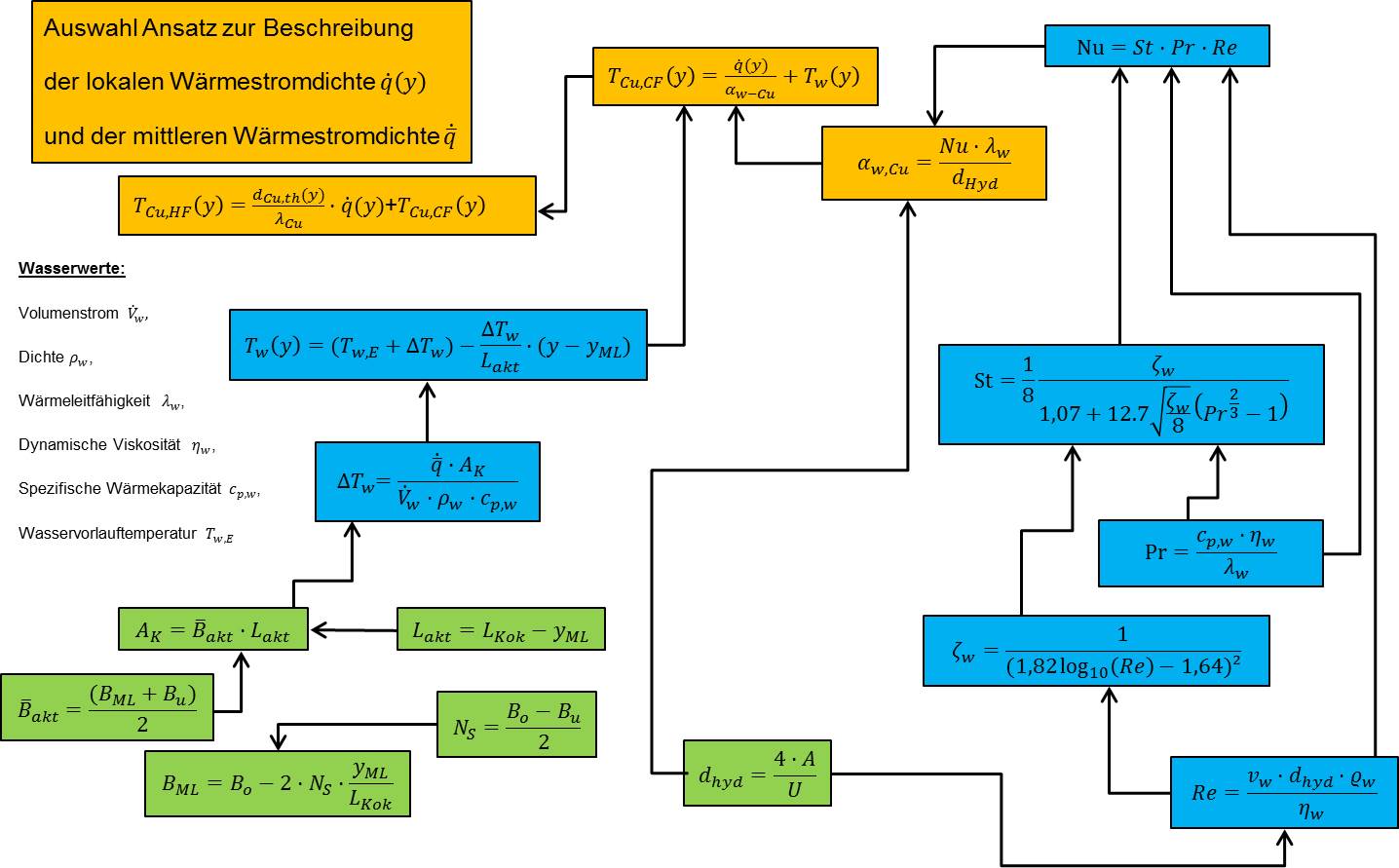
Bild 6: Geometrische Beziehungen und thermisch-fluidtechnische Formelzusammenhänge. (Bild: SMS Siemag)
Die entsprechenden Gleichungen und Beziehungen (siehe Bild 7) können, in Abhängigkeit von den Leistungsmerkmalen des CAD-Systems, direkt im CAD-Datenmodell verankert oder indirekt über einen Parameterabgleich mit einem externen Berechnungswerkzeug in die Modellierung eingebunden werden. Der Konstrukteur bekommt dadurch eine erste Bewertungsgrundlage für seine weitere Detailgestaltung.
Durch die Anwendung der speziellen rechnerunterstützten Konstruktions- und Fertigungstechnologie kann auf Besonderheiten wie Befestigungsgewinde und Bohrlöcher für Thermoelemente durch das Umfahren mit minimalem Einfluss auf die Kühlwirkung reagiert werden.
Diese Kurven werden dann auf die zuvor anforderungsgerecht definierte Nutgrundfläche projiziert (siehe Bilder 3 und 7).
Es entsteht in dieser Fläche eine neue mitunter komplexe 3-dimensionale Kurve, die als Leitkurve für die weitere Definition der Kühlkanäle genutzt werden kann. Dafür wird am Ende der Leitkurve eine Skizze des Fräswerkzeuges definiert, die dann entlang der Leitkurve als Schnittelement gezogen wird und das Material aus dem Modell entfernt.
Bei Kugelfräsern kann die Generierung einer weiteren äquidistanten Kurve zur Beschreibung seiner Mittelpunktbahn hilfreich sein. Bei zylin- drischen Fräsern kann der obere bzw. untere Scheitelpunkt genutzt werden. Hier ist eine enge Abstimmung mit der NC-Programmierung erforderlich, da es durch Hinterschneidungen zu Abweichungen von der Soll-Geometrie kommen kann, wenn der Fräser nicht senkrecht auf der Mittelpunktbahnkurve fährt. Gegebenenfalls werden die Bahnkurven dann nochmals unterteilt.
Bei schnellgießenden Maschinen darf die Temperatur nicht zu hoch werden. Mit flexibler Anpassung der Kanaltiefe kann dem gezielt entgegen gewirkt werden. Lokale oder kurze Tiefenänderungen lassen sich eher einbringen als dies mit großen Radien der Scheibenfräser möglich ist.
3 Anwendung
Gerade bei älteren Anlagen wie Kreisbogenanlagen lassen sich derart konstruierte Platten sinnvoll einsetzen.
Die traditionellen Ausführungen sind hier zwar in der Regel für die Vielzahl der Standardstähle weiter einsetzbar, jedoch macht die Anwendung spezieller, angepasster Kokillenplattenkonstruktionen mit der Weiterentwicklung der Stahlsorten durchaus Sinn. Außerdem werden die Dicken vor den Kühlkanälen durch die starke Ausnutzung des Kupfermaterials zum Teil unter 10 mm Restwandstärke reduziert. In diesen Fällen kommt es auf eine möglichst homogene Kühlwirkung an.
In der praktischen Anwendung haben sich zwei Kupferlegierungen als Kokillenplattenwerkstoff für Brammenkokillen durchgesetzt. Zum einen ist dies Kupfer-Silber (CuAg) und zum anderen Kupfer-Chrom-Zirkon (CuCrZr). Letzterer Werkstoff ist etwas härter, neigt dadurch aber auch eher zur Rissbildung. Hier bietet sich die konstruktive Gestaltung von gerundeten Kühlkanälen an. Damit kann die Kerbwirkung, die von rechtwinkligen Fräskonturen ausgeht, und damit die Gefahr der Rissentstehung im Kühlkanalgrund, erheblich reduziert werden.
Je nach Schneidwerkzeug ist aber auch eine Rundung der Fräskanten zwischen 0,5 – 2 mm denkbar. Bild 9 zeigt eine derart gefertigte Kupferplatte.
Langsam gießende Maschinen mit risskritischen Stahlsorten erfordern eine sanfte Kühlwirkung. Der Fokus liegt hier darauf, dass die Kupferhauttemperatur nicht zu niedrig wird. Dementsprechend ist in solchen Fällen eine große Wandstärke vor den Wasserkanälen gefordert.
Im Unterschied zu konstruktiven Ausführungen mit großen Scheiben- fräsern, bei denen die dadurch anwachsende Kupferwandstärke im Ein-und Auslaufbereich störend wirkt, kann mit Hilfe einer linearen, leicht gerundeten Bahnkurve in diesen Bereichen eine reduzierte Wandstärke einerseits erzielt werden und zum anderen können damit scharfe 90°-Umlenkungen vermieden werden. Letztlich kann somit ein geringer Druckverlust in den Kühlkanälen erreicht werden. Hierfür wurden entsprechende Optimierungsansätze erarbeitet und in einem CAD-System umgesetzt.
SMS-Siemag setzt solche speziell zugeschnittenen Platten für Hochleistungs-Brammengießmaschinen ein, bei denen es auf ein Höchstmaß an Homo- genität in der Temperaturverteilung auf der Plattenheißseite ankommt. Das ist immer dann der Fall, wenn sehr rissempfindliche Stahlsorten gegossen werden.
Ein weiterer Anwendungsfall sind Kokillen, die mit elektromagnetischen Rühreinrichtungen ausgestattet sind. In diesem Fall müssen die elektrisch leitfähigen Kupferplatten möglichst dünn sein, um die gewünschte Magnetfeldwirkung geringstmöglich zu beeinflussen. Wie eingangs erwähnt kommt es in solchen Fällen dünner Restwandstärken auf eine gleichmäßige Kühlwirkung an. Durch die konstruktiv optimierte Gestaltung kann dem Kunden damit eine höhere Materialausnutzung ermöglicht werden, die die Gesamtlebensdauer des Verschleißteiles Kupferplatte verlängert.
Zusammenfassend ergeben sich durch die optimierte Kühlkanalgestaltung und Verteilung folgende wesent-liche Vorteile:
eine Homogenisierung der Temperaturunterschiede auf der Plattenheißseite,
eine Verbesserung der Kokillenaustrittstemperatur auf der Heißseite, was die Härte der Platte sowie deren Beschichtung und damit die Standzeit positiv beeinflusst,
ein höherer Ausnutzungsgrad, da geringere Restwandstärken vor den Kühlkanälen möglich sind.
Weiterhin erlaubt die Modellierungstechnik eine Anwendung zur Detailoptimierung der Kanalausläufe zur Druckverlustminderung und eine gezielte lokale Anpassung der Kühlnuttiefen mit kurzen Übergangslängen und kleinen Radien. Dies wäre mit konventionellen Scheibenfräsern so nicht möglich (siehe Bild 3).
Literatur:
[1] SMS-Siemag: „Interne Untersuchung Kundenplatte mit CFD,“ Düsseldorf, 2008.
[2] Köhler, P.: Pro/Engineer-Praktikum – Einführende und fortgeschrittene Arbeitstechniken der parame- trischen 3D-Konstruktion mit Wildfire 5.0, Duisburg: Vieweg+Teubner, 2010.
[3] Kesselmanns, C.; Köhler, P.: „Komponentenübergreifende Abhängigkeiten in Gestaltungs- und Berechnungsprozessen; Crosscomponent Dependencies during Design and Computational Processes,“ Konstruktion, pp. 87–90, Nr.10 2013.
[4] Hoffmeister, J.; Letzel, D.: „Stranggießkokille für flüssiges Metall, insbesondere für fluessigen Stahl“. Patent WO 2010015399 A1, 06 08 2009.
[5] Krasilnikov, A.; Lieftucht, D.; Reifferscheid, M.; Hovestädt, E.; Schramm, T.; Kirsch, D.; Scheller, P. R.: „Online shell thickness calculation operating in a new fibre-optical based Mould Monitoring System,“ in 5th International Congress on Science and Technology of Steelmaking, Dresden, 2012.
[6] Schwerdtfeger, K.: „Heat Withdrawal in the Mold in Continuous Casting of Steel. Review and Analysis,“ steel research int.77, 2006 No.12.
LiteraturAutorenDipl.-Ing. Jörn Hoffmeister Leiter Arbeitsgebiet Konstruktion Stranggießtechnik SMS-Siemag AG Eduard-Schloemann Straße 4, 40237 Düsseldorf Tel.: 02 11/8 81-66 75E-Mail: joern.hoffmeister@sms-siemag.com www.sms-group.comProf. Dr.-Ing. Dipl. Math. Peter KöhlerUniversität Duisburg-EssenInstitut für Produkt EngineeringLehrstuhl Rechnereinsatz in der Konstruktion Lotharstraße 1, 47057 Duisburg Tel.: 02 03/3 79-18 20E-Mail: peter.koehler@uni-due.de https://www.uni-due.de/cae