Gestaltfestigkeit gehärteter Passfederverbindungen
Die Passfederverbindung (PFV) zählt nach wie vor zu den gebräuchlichsten formschlüssigen Verbindungen im Bereich der Antriebstechnik. Insbesondere die einfache Montage und Demontage sowie die relativ einfache Fertigung begründen den häufigen Einsatz dieser Verbindung. Darüber hinaus wird aus Sicherheitsgründen vielfach der Formschluss als redundante Maßnahme zum Kraftschluss gefordert. PFV mit „weicher“ Welle wurden in den letzten 20 Jahren umfassend hinsichtlich der Gestaltfestigkeit untersucht [1-3]. Die nunmehr in DIN 743 [4] enthaltenen und ursprünglich pragmatisch aus Praxisbeispielen abgeleiteten Kerbwirkungszahlen gelten damit als validiert. Gleichwohl ist festzustellen, dass nicht alle maßgebenden Einfluss- parameter (z. B. bezogenes Übermaß x, Verhältnis tm/sba) von den Kennwerten in DIN 743 explizit erfasst werden. Dies gilt auch für PFV mit gehärteter Welle, für die bisher keine gesicherten Versuchswerte existieren. Im Rahmen der Forschungsvereinigung Antriebstechnik e.V. (FVA) wurden diesbezüglich umfangreiche Untersuchungen durchgeführt [5], über die nachfolgend auszugsweise berichtet wird.
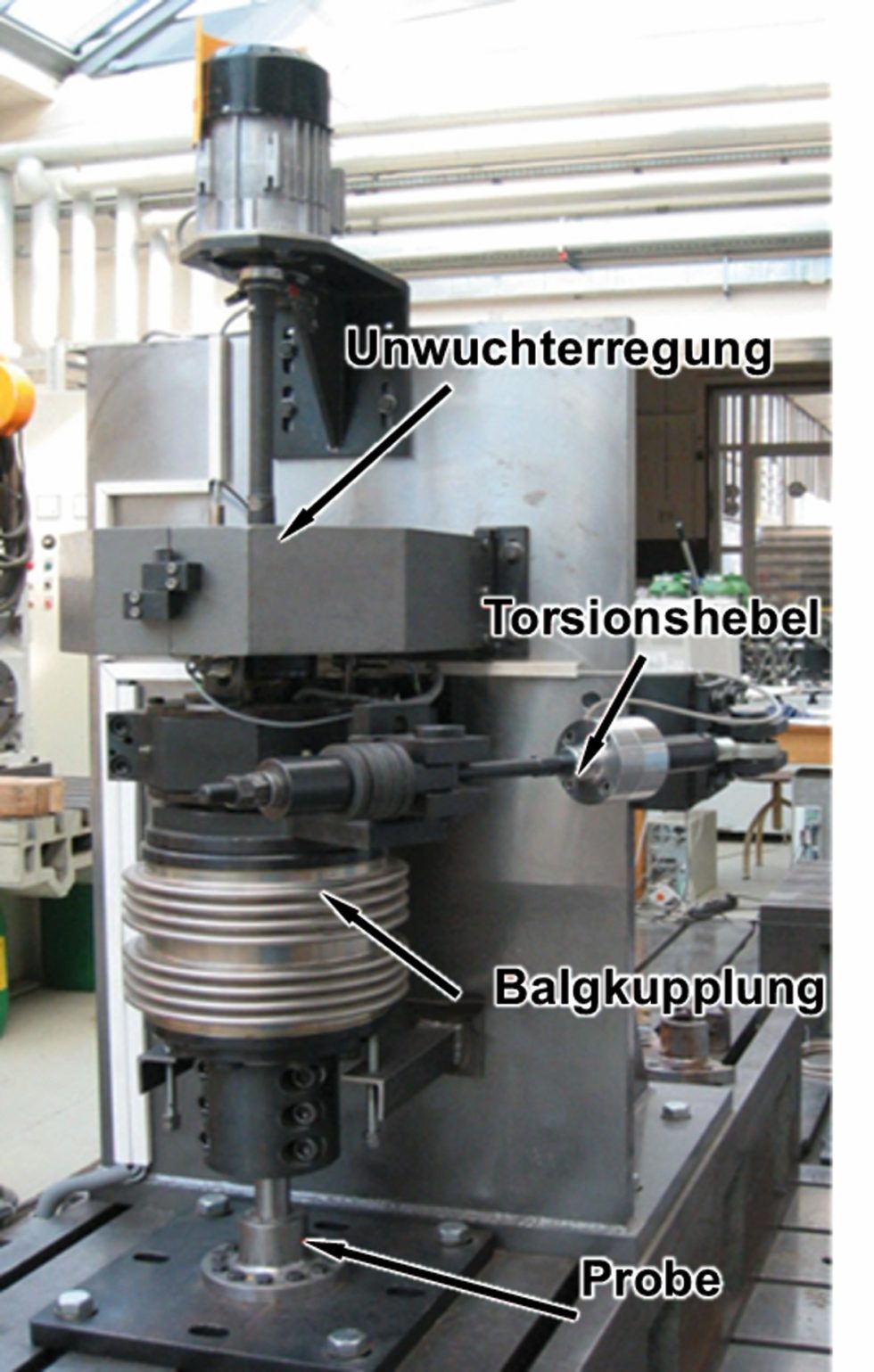
Bild 1 Unwuchtprüfstand zur Erzeugung der Umlaufbiegung. Bild: Verfasser
1 Einleitung und Zielstellung
Ein typisches Beispiel für eine PFV mit gehärteter Welle ist die Ritzelwelle. Da Verzahnungen generell randschichtgehärtet werden, erfährt eine in die Welle eingebrachte Passfedernut die gleiche Wärmebehandlung. Zwar wäre ein Abdecken der Nut zur Vermeidung der Aufkohlung möglich. Dies verursacht aber zusätzliche Kosten und zudem besteht die Gefahr einer technologischen Kerbe am Übergang hart/weich.
In Hinblick auf die Gestaltfestigkeit sollten infolge der Einsatzhärtung im Vergleich zum Vergüten eigentlich Vorteile zu erwarten sein. In DIN 743 wurde diesbezüglich der Verfestigungsfaktor KV eingeführt, für den in Ab-hängigkeit vom Wärmebehandlungsverfahren Wertebereiche angegeben werden. Für Einsatzhärtung und gekerbte Bauteile gilt beispielsweise Kv = 1,2.…2. Gleichung (2) verdeutlicht in Form des Gesamteinflussfaktors K der DIN 743 den linearen Einfluss des Faktors KV auf die Beanspruchbarkeit des gekerbten Bauteils.
b: Kerbwirkungszahl
K1: technol. Größeneinflussfaktor
K2: geom. Größeneinflussfaktor
KF: Rauheitsfaktor
KV: Oberflächenverfestigungsfaktor
sbW: Werkstoff-Wechselfestigkeit
sbWK: Bauteil-Wechselfestigkeit
Die Kerbwirkungszahl b kann für die meisten Welle-Nabe-Verbindungen aufgrund des Bruchortes in der Fuge und der dort vorliegenden Singulari- täten nur experimentell ermittelt werden. Der Oberflächeneinfluss infolge Reibdauerbeanspruchung ist daher in der Kerbwirkungszahl enthalten, weswegen in Gl. (2) KF = 1 gesetzt werden kann.
PFV mit einsatzgehärteter Welle können derzeit mit DIN 743 nicht wirkungskonform berechnet werden. Die darin enthaltenen Kerbwirkungszahlen für Torsion und Umlaufbiegung sind wenig differenziert. Das domi-nante Unterscheidungsmerkmal ist die Zugfestigkeit. Die bereits bei den Vergütungsstählen nachgewiesene Abhängigkeit vom Übermaß und vom Beanspruchungsverhältnis statische Torsion/Umlaufbiegung wird nicht ausgewiesen bzw. nur qualitativ beschrieben.
Da in DIN 743 keine Einschränkung bezüglich der Anwendung des Verfestigungsfaktors KV enthalten ist, wird dieser oftmals auch für gehärtete PFV genutzt. Die dabei entstehenden und bereits in einer Vorstudie [6] nachgewiesenen Fehler können in Abhängigkeit vom Faktor KV bis zu 50 % betragen. Grund dafür ist die Erkenntnis, dass bei PFV die Schwingfestigkeit durch das Härten offenbar nicht gesteigert wird.
Wegen weiterer erkannter Unsicherheiten war das Ziel des IGF/FVA-Vor-habens die statistische Absicherung der punktuell vorliegenden Gestaltfestigkeiten von PFV mit gehärteter Welle. Des Weiteren sollten die Doppelkerbe Freistich/Passfedernut und die Wirkung einer, bezogen auf die Nabenstirnfläche, vorgezogenen oder zurückgesetzten Passfeder untersucht werden. Von den Ergebnissen partizipieren besonders die zahlreichen Getriebehersteller, die weltweit sehr erfolgreich agieren.
2 Experimentelle Untersuchungen
2.1 Prüfstand und Probengeometrie
Die Belastung der PFV erfolgt, wie in der Praxis üblich, mit umlaufender Biegung und überlagerter statischer Torsion. Das Verhältnis von Torsion zur Biegung beträgt, wenn nicht anders angegeben tm/sba = 0,5 bzw. Mt/Mb = 1.
Für die Gestaltfestigkeitsunter- suchungen wurde der in Bild 1 dargestellte Unwuchtprüfstand genutzt.
Die durch einen Servomotor in Rotation versetzte Unwucht erzeugt über die senkrecht stehende Haltewelle ein durch die Drehzahl einstellbares umlaufendes Biegemoment. Das Drehmoment wird über den Torsionshebel und eine biegeweiche Balgkupplung in die Probe eingeleitet. Die Einstellung des Torsionsmomentes erfolgt über einen Kraftaufnehmer. Bild 2 zeigt die Probenform und zugleich eine mit DMS applizierte Welle zur Kalibrierung der Lastregelung.
Für Welle und Nabe wurde der Werkstoff 18CrNiMo7–6 gewählt. Als Härtewert wurde generell 59 + 3 HRC mit einer Einsatzhärtetiefe CHD = 0,5 + 0,2 mm vorgegeben. Alle Versuche wurden trocken gefahren.
Die der Norm [7] entsprechende Passfeder war stets aus dem Werkstoff C45 mit der rundstirnigen Form A. Der Standardprüfdurchmesser betrug 40 mm und entspricht somit dem Bezugsdurchmesser dBK der DIN 743. Die Welle ist immer ohne Absatz (glatt) ausgeführt, wenn nicht anders vermerkt. Weitere Geometrieangaben sind [5] zu entnehmen.
2.2 Werkstoffuntersuchungen
Die Eigenschaften von Stählen werden wesentlich durch den Behandlungszustand beeinflusst. Während des Einsatzhärtens wird auch der Kernbereich der Welle modifiziert. Insofern ergibt sich die Notwendigkeit, den Zustand des Kernmaterials zu überprüfen. Die Zugproben wurden deshalb aus dem Kernbereich der Wellen entnommen. Um den gelegentlich in der Praxis diskutierten Einfluss der Härterei auf die Festigkeit der Welle unter- suchen zu können, wurden diese in drei Härtereien einsatzgehärtet. In den Härtereien 1 und 2 erfolgte die Aufkohlung im Gas, in Härterei 3 im Vakuum (Niederdruckaufkohlen). Die charakteristischen Härteangaben waren immer gleich und sind Kap. 2.1 zu entnehmen.
In Tabelle 1 sind die Ergebnisse aus statischen Zugversuchen nach DIN EN ISO 6892–1 [8] zusammengefasst. Die Angaben zur Streckgrenze und zur Zugfestigkeit stellen Mittelwerte aus jeweils drei Versuchen dar. Insgesamt ist festzustellen, dass die ermittelten Festigkeitswerte den Vorgaben für den Werkstoff 18CrNiMo7–6 (1.6587) entsprechen.
Die Untersuchungen bezüglich Härte und Gefüge wurden an Querschliffen durchgeführt. Bild 3 zeigt die Härte- tiefenverläufe an der geschliffenen Wellenoberfläche. Die Einsatzhärtetiefe CHD variiert in geringem Maße, entspricht aber immer den Vorgaben. Mit dem Niederdruckaufkohlen (Härterei 3) wurde die größte Härte an der Oberfläche erreicht, wobei der Härte- gradient dem der Härterei 2 entspricht. Bei der Härterei 1 ist der Gradient deutlich flacher. Der Einfluss auf die Gestaltfestigkeit wird in Kap. 2.5 diskutiert.
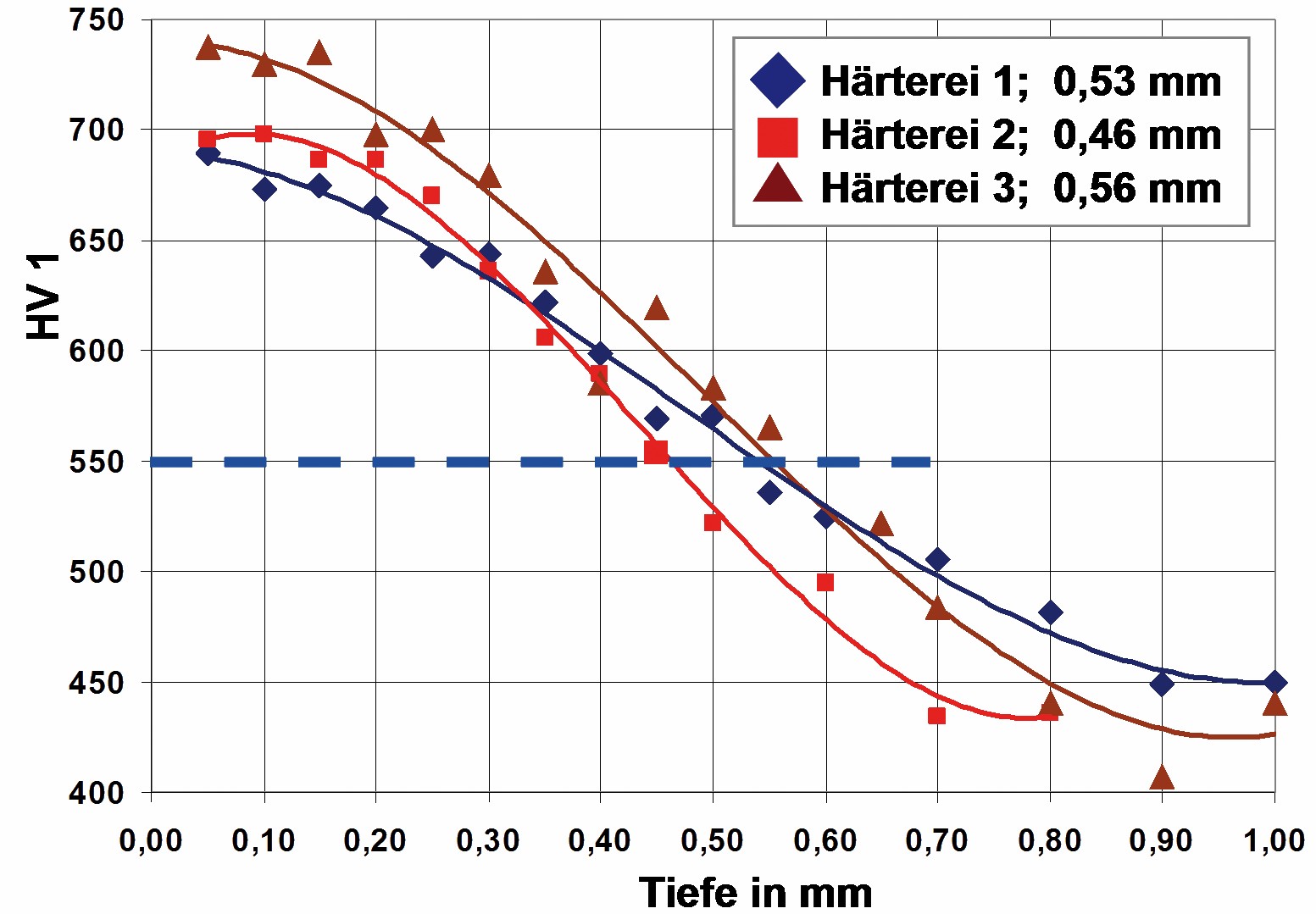
Bild 3 Härtetiefenverläufe und CHD an der geschliffenen Wellenoberfläche für die Härtereien 1, 2 und 3. Bild: Verfasser
Das Gefüge an der Wellenoberfläche stellt bei allen drei Varianten eine Mischung aus Platten- und Lattenmartensit sowie Restaustenit dar (siehe dazu auch [5]). XRD-Messungen ergaben für die Härtereien 1 und 2 Restaustenitanteile von 15 bzw. 17 Gew-% . Für die Härterei 3 wird der Restaustenitanteil etwas geringer eingeschätzt. Erwartungsgemäß nehmen die Anteile des Restaustenits mit zunehmendem Abstand von der Oberfläche ab. Demnach besteht ein Zusammenhang zur Abnahme der Kohlenstoffkonzentration und Härte mit zunehmender Tiefe.
Die Untersuchung auf Mikrorisse gestaltete sich wegen der spezifischen Merkmale des martensitischen Gefüges schwierig. Im Rahmen der Routineuntersuchungen am geätzten Schliff konnten solche Defekte nicht nachgewiesen werden. Daher wurden gezielte Nachuntersuchungen an Wellen im Ausgangszustand und nach den Dauerprüfstandtests durchgeführt. Lediglich bei den von der Härterei 3 behandelten Wellen wurden Mikrorisse im Bereich der Nutkante nachgewiesen. Die festgestellte maximale Tiefe betrug 30 µm und die Längen 10 bis 50 µm. Ein signifikanter Unterschied zwischen dem Ausgangszustand und dem geprüften Zustand war nicht festzustellen. Bild 4 zeigt beispielhaft Mikrorisse in der Nähe der Nutkante einer Welle aus der Härterei 3.
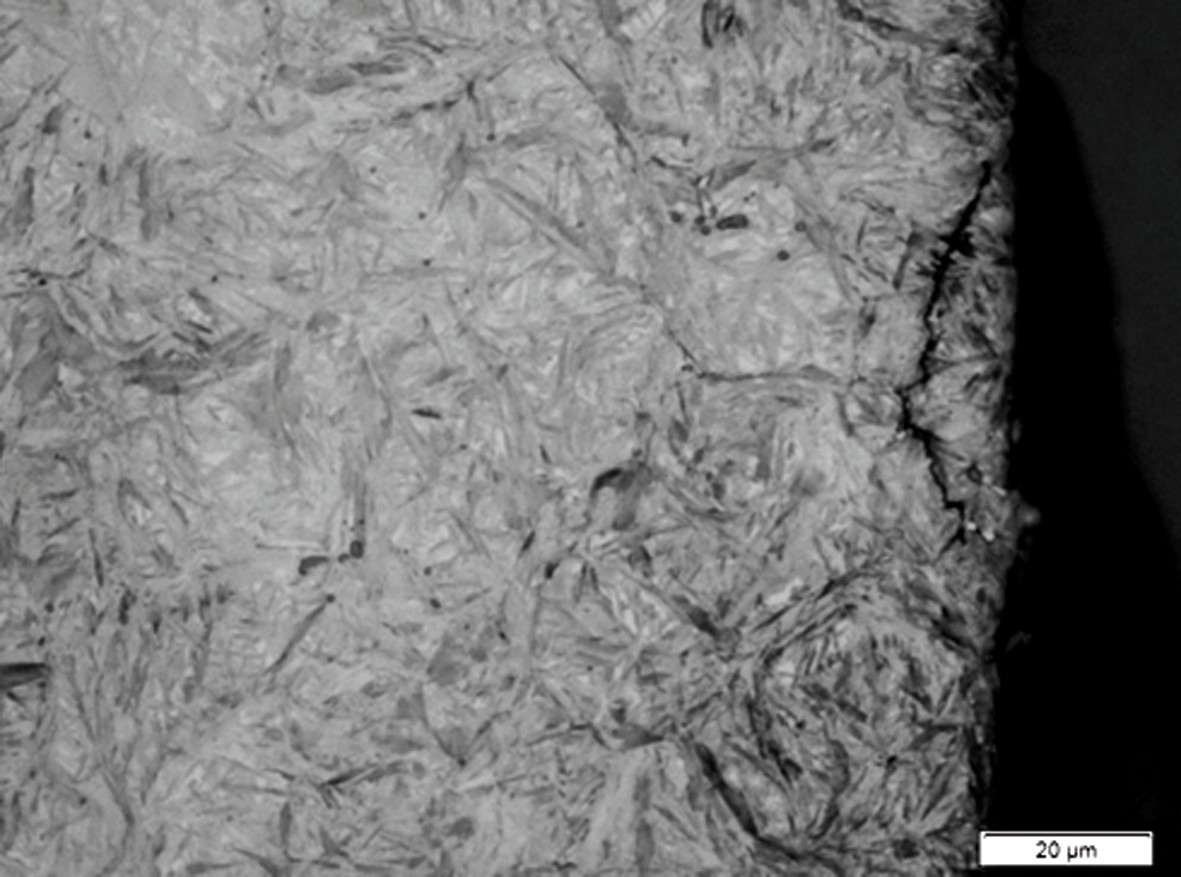
Bild 4 Mikrorisse (dunkle Linien) in der Nähe der Nutkante, Härterei 3; geschliffene Oberfläche (linkes Bild); Nutflanke (rechtes Bild). Bild: Verfasser
Die für das Gasaufkohlen bekannte Randoxidation wurde ebenfalls untersucht. Bei den Härtereien 1 und 2 wurde diese, im Gegensatz zu Härterei 3, bis zu einer Tiefe von maximal 20 µm festgestellt. Da die Wellen vor dem Fügen grundsätzlich geschliffen wurden und der Abtrag ca. 15…20 µm betrug, waren alle Wellen an der Oberfläche frei von kritischen Gefügemerkmalen. Lediglich im gehärteten, nicht nachbehandelten Nutbereich und besonders an der Nutkante bleibt die Randoxidation erhalten.
2.3 Schwingfestigkeitsversuche
Zunächst sollte untersucht werden, ob ähnlich wie bei der Zahnfußfestigkeit auch bei den PFV das Härtever- fahren bzw. unterschiedliche Härtechargen zu nachweisbaren Festigkeitsunterschieden führen können. Die zweifelsfrei geringen Unterschiede im Härtetiefenverlauf führen erwartungsgemäß zu keinen signifikanten Unterschieden bei der Gestaltfestigkeit, wie Bild 5 anschaulich zeigt. Die Schwankungen liegen im Bereich der statistischen Unsicherheiten. Damit kann, unter der Voraussetzung einer „gleichen“ Härteverteilung, eine Abhängigkeit der Beanspruchbarkeit von der Härterei ausgeschlossen werden.
Eine weitere Versuchsvariante orientierte auf die Ermittlung des Verfestigungsfaktors KV bzw. auf den Nachweis der Erhöhung der Übertragungsfähigkeit durch Härten. Dazu wurden stichprobenartig 3 Proben (gleiche Geometrie wie vorher) in der Härterei 1 blindgehärtet, d.h. die Wellen wurden vor der Wärmebehandlung vollständig abgedeckt und damit nicht aufgekohlt (nur vergütet). Bild 6 zeigt das über- raschende Ergebnis, dass bei PFV durch das Härten offenbar keine Festigkeitssteigerung erzielt werden kann. Trotz des nur aus 3 Versuchen resultierenden Schätzwertes bestätigt dies die schon eingangs erwähnte Tendenz aus der Vorstudie. Abschließend sei vermerkt, dass die Bruchorte beider Varianten gleich waren.
2.4 Einfluss der Fertigungstechnologie
Mit Blick auf die Werkstoffhärte bietet sich das Fräsen der Nut in die weiche Welle an. Die beim Härten nie gänzlich auszuschließenden Verzüge sind bei kleineren Durchmessern meist vertretbar. Mit zunehmendem Durchmesser nehmen aber zwangsläufig die Vorzüge zu, so dass eine Nacharbeit unumgänglich wird. Um diesen Kostenfaktor zu vermeiden, wird in der Praxis entweder die Nut abgedeckt (ebenfalls aufwändig) oder die Nut erst nach dem Härten eingebracht. Es ist daher folgerichtig, diese Fertigungsvarianten hinsichtlich des Einflusses auf die Gestaltfestigkeit zu untersuchen. Aus DIN 6885 [7] und Forbrig [2] ist bekannt, dass die Nutgeometrie zum Wellendurchmesser nicht geometrisch ähnlich ist. Der Nutquerschnitt nimmt im Verhältnis zum Wellenquerschnitt ab, was eine (geringe) Festigkeitssteigerung vermuten lässt. Deshalb wurde auch diese Konstellation untersucht.
In Tabelle 2 sind die ausgewählten Fertigungstechnologien und Nutgeometrien zusammengestellt.
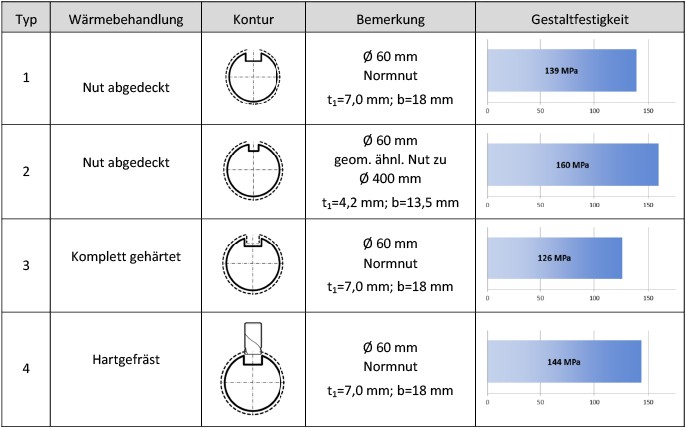
Tabelle 2 Einfluss der Fertigungstechnologie auf die Gestaltfestigkeit; x = 0,5 ‰; tm/sba = 0,25; t1: Nuttiefe, b: Nutbreite; Werkstoff: 18CrNiMo 7-6; —- gasaufgekohlt (Härterei 1), Typen 1, 2 und 4 duktile Nut.
Alle diesbezüglichen Untersuchungen wurden auf einem größeren Unwuchtprüfstand mit dem Wellendurchmesser Ø 60 mm durchgeführt. Die ermittelten Gestaltfestigkeiten sind in Tabelle 2 (rechts) eingetragen. Deutlich wird auch hier wieder der nicht erkennbare Vorteil einer gehärteten Nut und die gute Übereinstimmung vom Typ 1 und Typ 4 mit jeweils weicher Nut. Die leicht niedrigen Gestaltfestigkeiten gegenüber den PFV mit Ø 40 mm sind auf die Unterschiede der Werkstofffestigkeiten (vergl. Tab. 1) und des ungün-stigeren Nut-/Wellenquerschnitt-Verhältnisses zurückzuführen. Die etwas herausragende Gestaltfestigkeit der zu Ø 400 mm geometrisch ähnlichen Nut resultiert dagegen aus dem günstigeren Nut-/Wellenquerschnitts-Verhältnis.
2.5 Einfluss der Passfederlage auf die Gestaltfestigkeit
Mit der Untersuchung einer abgesetzten Welle mit Freistich wurden zwei Ziele verfolgt. Zum einen sollte der Wellenabsatz mit Freistich und Pass- federnut (Doppelkerbe) im Vergleich zur PFV mit „glatter“ Welle untersucht werden. Zum zweiten sollte der Einfluss der Lage der Passfedernut zum Absatz auf die Gestaltfestigkeit ermittelt werden. Hierzu wurden vier unterschiedliche Geometrien, welche alle eine hohe praktische Bedeutung aufweisen, herangezogen. Die Lage der Passfeder wird hier über die Beziehung a1/b definiert, siehe Bild 7, wobei a1/b = 0,5 eine bündig zur Freistichkante liegende Passfedernut kennzeichnet.
Durch eine in den Wellenabsatz verschobene Passfeder (a1/b < 0) lässt sich die tragende Passfederlänge erhöhen, was einem Kompromiss zwischen Bauraum und tragender Länge entspricht. Die zurückgesetzte Passfeder (a1/b > 0,5; Bild 7) führt, wie frühere Versuche an duktilen Verbindungen zeigen, zu einer höheren Gestaltfestigkeit. Die Erklärung hierfür ist die auf dem Formschluss basierende Biegemomentableitung in die Nabe, vgl. Bild 8.
Dies führt zu einer kleineren Beanspruchung am potentiellen Bruchort, der immer im Bereich der Nutausrundung liegt. Die örtliche Beanspruchbarkeit ist zwar zu den anderen drei untersuchten Geometrien gleich, jedoch ist die örtliche Beanspruchung bei gleicher Nennbelastung geringer.
Die Freistichgeometrie wurde wie in früheren Versuchen mit Pressverbindungen [9] ausgeführt. Es wurde ein Freistich nach DIN 509 [10] Form E mit einem Kerbradius 0,6 mm und einer Freistichtiefe von 0,3 mm, gefertigt. Für diesen Freistich im einsatzgehärteten Zustand (18CrNiMo7–6) ergibt sich nach [9] eine Gestaltfestigkeit von etwa 260 MPa. Da die Kerbwirkungszahl der PFV bei C45 etwa gleich der des Freistichs bei C45 entspricht, könnte auf eine ähnliche Festigkeit geschlossen werden.
Die Versuchsdurchführung im Übergangsgebiet zur Dauerfestigkeit erfolgte nach dem Treppenstufenverfahren, die Auswertung nach der IABG-Methode nach Hück [11]. Bild 9 zeigt die ermittelten Gestaltfestigkeiten für eine 50%-Überlebenswahrscheinlichkeit bei 107 Lastwechseln für alle vier Geometrien.
Die angegebenen Werte sind Nennspannungen und beziehen sich immer auf den Vollkreisquerschnitt des Fugendurchmessers. Im Mittel wurden pro Geometrie 9 Ermüdungsversuche durchgeführt.
Zunächst ist festzustellen, dass die ermittelten Gestaltfestigkeiten weit unterhalb der Festigkeit des reinen Freistichs liegen. Die kritische Kerbe ist hier in jedem Fall die PFV bzw. die Wellennut. Die Festigkeit beträgt, wenn sich die Passfedernut im Bereich des Freistichs befindet, etwa 150 MPa. Eine etwas höhere Festigkeit weist die zurückgesetzte Verbindung (a1/b = 1,25) auf. Somit bleibt der bereits bei duktilen Verbindungen festgestellte Vorteil auch bei gehärteten PFV er- halten.
Die Anrisspositionen der untersuchten Geometrien sind in Bild 10 zusammengefasst. Als kerbkritische Stelle kann, wie auch bei den duktilen Verbindungen, der Übergangsbereich von der (belasteten) Nutflanke zum Nutradius gesehen werden.
Bei der Geometrievariante a1/b = 0 beginnt der Anriss jedoch im Freistich. Hier fällt der kritische Querschnitt der Nut mit dem Freistich zusammen (Doppelkerbe). Lediglich bei der Variante a1/b = -0,75 findet der Anriss nicht mehr im Übergang zwischen Nutflanke und Nutradius statt, da hier der kritische Bereich in den größeren Durchmesser verschoben ist.
2.6 Bruchflächenanalyse
Fraktografische Untersuchungen nach dem Bruch wurden in [5] an 20 Wellen durchgeführt. Die Charakterisierung von Bruchmerkmalen erfolgte am Rasterelektronenmikroskop (REM) Zeiss NEON40. Beispielhaft zeigt Bild 11 die Bruchflächen von zwei vollständig einsatzgehärteten, gebrochenen Wellen.
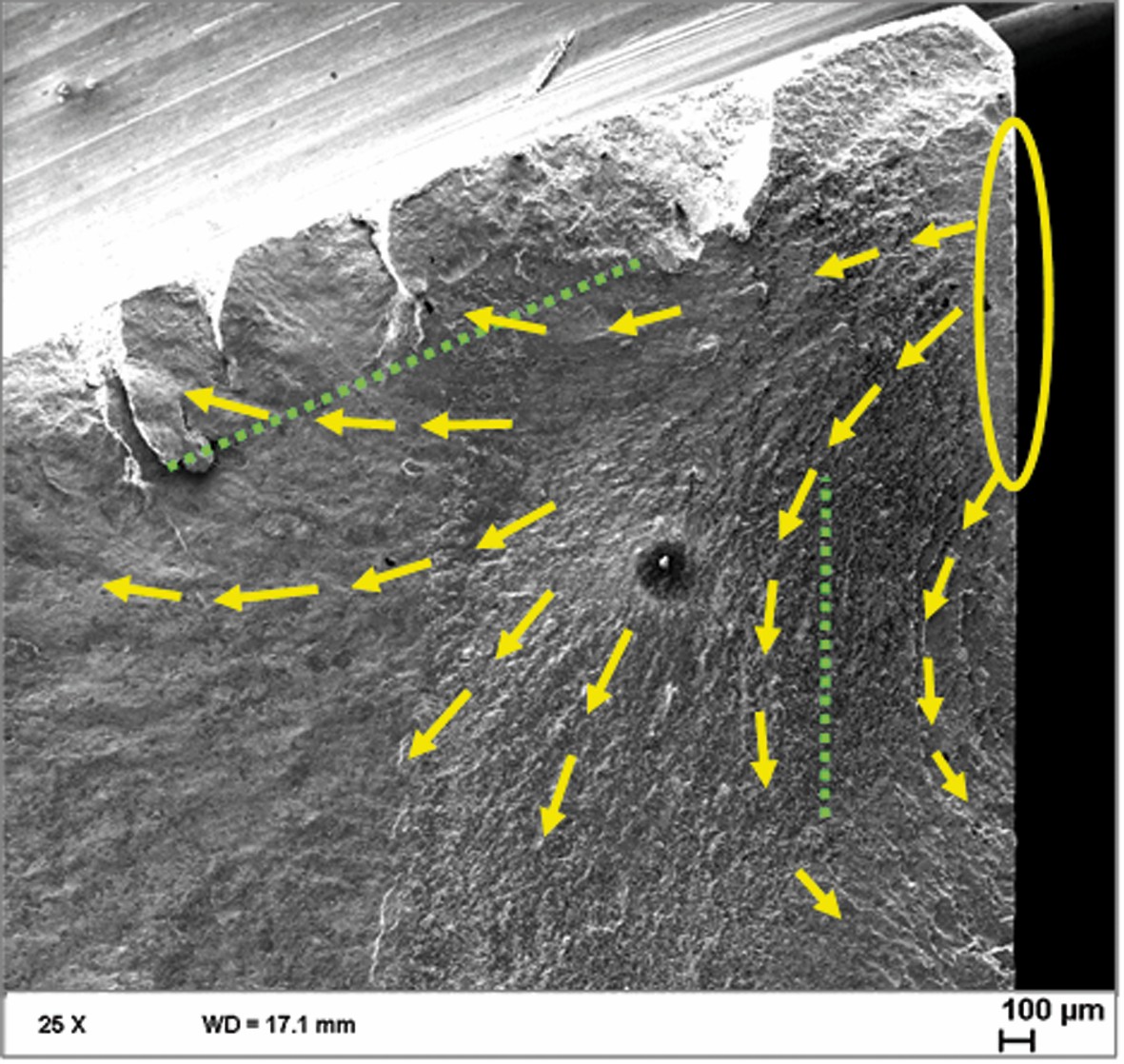
Bild 11 REM-Aufnahmen mit Markierung des Rissausgangsgebietes (Ellipse), des Rissfortschritts (Pfeile) und der Einsatzhärtetiefe (CHD): Rissausgangsgebiet an der Wellenoberfläche nahe der Nutkante (links); Rissaus-gangsgebiet an der Nutflanke nahe der Nutkante (rechts). Bild: Verfasser
Der Anriss beginnt immer im Bereich der belasteten Nutflanke, jedoch nicht immer am gleichen Ort. Wie Bild 11 zeigt, kann der Anriss sowohl an der Wellenoberfläche als auch an der (nicht nachbehandelten) Nutflanke beginnen. Die Pfeile dokumentieren den Rissfortschritt. Wegen des Einstufenversuchs fehlen markante Rissfortschrittslinien. Die Einsatzhärtetiefe (CHD) wird durch die punktierte Linie charakterisiert. Demnach beginnen alle Anrisse in der Härte- zone, wobei der Rissentstehungsort max. 100 µm unterhalb der Oberfläche liegt. Die REM-Untersuchungen ergaben keine Hinweise, dass die Bruchentstehung durch Defekte an der Oberfläche oder im Gefüge initiiert wird (vergl. Kap. 2.2).
3 Kerbwirkungszahlen
Der Sicherheitsnachweis der Welle einer Passfederverbindung unter (Umlauf-)Biegung wird in der Regel nach DIN 743 [4] geführt. Die experimentell ermittelten Kerbwirkungszahlen b fließen in Gl. (2) ein, ebenso der Oberflächenverfestigungsfaktor KV. Bei dieser Vorgehensweise sind alle maßgebenden Parameter (Werkstofffestigkeit, Kerbwirkungszahl, Mittelspannungsempfindlichkeit …) auf den blindgehärteten Zustand zu beziehen.
Die Ableitung von Kerbwirkungszahlen aus experimentellen Ergebnissen im Hinblick auf die spätere Anwendung in Normen bzw. Standards ist nicht immer eindeutig. Für den blindgehärteten Zustand mit Biegung und ohne Torsion kann die Kerbwirkungszahl wie folgt berechnet werden:
Die Dauerfestigkeit sD = 600 MPa wurde an einer glatten Rundprobe ermittelt [5]. Dieses Ergebnis bestätigt näherungsweise die Kerbwirkungszahl in DIN 743 [4] für einen Einsatzstahl (blindgehärtet).
Weniger eindeutig ist die Verfahrensweise bei überlagerter statischer Tor- sion und Einsatzhärtung. Zweckmäßig ist auch hier der direkte Bezug auf die Festigkeit der ungekerbten Probe (blindgehärtet und mittelspannungsfrei).
In dieser modifizierten Kerbwirkungszahl sind alle Einflüsse, also auch der Mittelspannungseinfluss durch Torsion sowie der Oberflächenverfestigungseinfluss beinhaltet. Streng genommen müssten diese Einflüsse, wenn sie in der Norm separat neben der Kerbwirkung berücksichtigt werden, aus der experimentellen Kerbwirkungszahl herausgerechnet werden. Das Separieren der Einflussgrößen kann jedoch, wie bereits beschrieben, nur normspezifisch erfolgen; d.h. die Kerbwirkungszahl in der DIN 743 wäre beispielsweise eine andere als in der FKM-Richtlinie [12], da der Mittelspannungseinfluss insbesondere beim Einsatzhärten unterschiedlich berücksichtigt wird. Diese Vorgehensweise ist deshalb nicht anzustreben.
Weiterhin wird die aktuelle Berücksichtigung der Mittelspannung (statische Torsion) im Festigkeitsnachweis bei PFV kritisch gesehen. Denn auch bei den duktilen PFV wird der Torsionseinfluss im Tragfähigkeitsnachweis nicht ordnungsgemäß berücksichtigt, da hier die Torsion eher neutral bzw. sogar positiv wirken kann. Daher sollten künftig für PFV Basiskerbwirkungszahlen, die unter definierten Bedingungen (stat. Torsion; Übermaß) ermittelt wurden, angegeben werden. Für veränderte Bedingungen sind dann erweiterte Kerbwirkungszahlen abzuleiten, die auch die Mittelspannungen (durch Torsion) einschließen. Im Übrigen wird dies mit dem Rauheitsfaktor bei WNV ebenso gehandhabt. Der Oberflächen-Verfestigungsfaktor KV sollte hingegen für einsatzgehärtete PFV beibehalten werden, da bei reiner Umlaufbiegung eine positive Wirkung der harten Randschicht festgestellt wurde.
Für die Normung wird deshalb empfohlen, eine Basiskerbwirkungszahl, ähnlich wie sie derzeit beim Bezugsdurchmesser dB = 40 mm vorliegt, zu verwenden. Diese ist wie bisher vom Werkstoff bzw. von dessen Zugfestigkeit anhängig und basiert auf einer definierten Kombination aus Übermaß und Mittelspannung (Torsion). Diese Konstellation könnte z. B. die hier im Vorhaben untersuchte Standardvariante (tm/sba = 0,5; x = 0,5 ‰) sein. Liegen andere Verhältnisse vor, können diese mittels einer erweiterten Kerbwirkungszahl b* berücksichtigt werden. Die Vergleichsmittelspannung infolge der Torsion entfällt dann.
Abschließend soll die Einbeziehung des Oberflächen-Verfestigungsfaktors KV diskutiert werden. Aus den in [5] durchgeführten Untersuchungen geht hervor, dass sowohl die Härte (Festigkeit) als auch die Eigenspannungen am Versagensort nach dem Versuch noch vorliegen. Dies spricht für die Beibehaltung des Faktors KV. Gestützt wird diese Erkenntnis durch den für einsatz- gehärtete PFV unter reiner Umlauf- biegung ermittelten Verfestigungsfaktor KV = 1,4 bei Zugrundelegung der Kerbwirkungszahl b = 3,2 nach DIN 743 [4].
Die Folge dieser Verfahrensweise ist allerdings, dass die mit KV = 1,4 aus den Versuchsergebnissen zurück- gerechneten Kerbwirkungszahlen ungewöhnlich groß werden (z. B. b = 6), was aber im Sinne der Wortbedeutung „Kerbwirkung“ durchaus berechtigt ist.
4 Zusammenfassung
Ergänzend zu einer Vorstudie [6] wurden in [5] weitere Ermüdungsversuche an einsatzgehärteten PFV unter Umlaufbiegung und überlagerter sta-tischer Torsion durchgeführt. Ziel war die Ermittlung und Absicherung der Gestaltfestigkeit bei Variation unterschiedlicher Parameter wie Geometrie, Wärmebehandlung, Umgebungsmedium und Fertigungstechnologie. Als Werkstoff für die Wellen und Naben wurde der Einsatzstahl 18CrNiMo 7–6 gewählt.
Analog zu den Ergebnissen aus der Vorstudie, konnten für die einsatz- gehärtete PFV unter Umlaufbiegung und statischer Torsion (häufiger Einsatzfall in der Praxis) praktisch keine Festigkeitsvorteile gegenüber der blindgehärteten Variante (oder auch vergüteten Variante) nachgewiesen werden. Die Gestaltfestigkeit der PFV in der hier geprüften Standardvariante (tm/sba = 0,5, x = 0,5 ‰) liegt etwa bei 150 MPa und ist gegenüber dem gehärteten Freistich die eindeutig kritischere Kerbe. Das Zurücksetzen der Passfedernut in die Verbindung ist ähnlich wie bei der duktilen Verbindung vorteilhaft. Die unterschiedlichen Härte-chargen zeigen, im Gegensatz zu den Werkstoffuntersuchungen, keinen nennenswerten Einfluss auf die Gestaltfestigkeit. Auch das Niederdruckaufkohlen bringt im Gegensatz zu den Erkenntnissen bei Zahnrädern keine Vorteile. Das Abdecken (Blindhärten) sowie das Hartfräsen der Nut führen zu einer geringen Festigkeitssteigerung gegenüber der harten Nut.
Als Ausgangspunkt für das Versagen wurde die durch die Passfeder belastete Wellennutkante im Übergang von der Nutflanke zum Nutradius festgestellt. Bei genauerer Betrachtung mehrerer gebrochener Proben ergaben sich bei starker Vergrößerung Anrissorte an der Wellenoberfläche, an der Nutecke bzw. -kante und an der Nutflanke; jedoch liegen alle Orte sehr nah beieinander. Weiterhin wurde festgestellt, dass die Anrisse oberflächennah, in jedem Fall in der harten Randzone entstehen.
Basierend auf den gewonnenen Erkenntnissen ist für die praktische Anwendung zu empfehlen, bei der Dimensionierung gehärteter PFV nach DIN 743 [4] den Oberflächenverfestigungsfaktor KV = 1 zu setzen und die dort angegebenen Kerbwirkungs- zahlen für ungehärtete Stähle zu verwenden. Für die erforderliche Anpassung des normbasierten Festigkeitsnachweises sollten die hier gegebenen Empfehlungen als Grundlage dienen.
Danksagung: Dieser Bericht ist das wissenschaft-liche Ergebnis einer Forschungsaufgabe, die von der Forschungsvereinigung Antriebstechnik e.V. (FVA, Frankfurt) gestellt und am Institut für Konstruk- tions- und Antriebstechnik (IKAT) der TU Chemnitz unter der Leitung von Herrn Professor Erhard Leidich bearbeitet wurde. Das IGF-Vorhaben 17018 BR wurde über die AiF im Rahmen des Programms zur Förderung der industriellen Gemeinschaftsforschung (IGF) vom Bundesministerium für Wirtschaft und Energie aufgrund eines Beschlusses des deutschen Bundestages gefördert. Die Autoren bedanken sich beim Institut für Werkstoffwissenschaften und Werkstofftechnik der TU Chemnitz für die Werkstoff- und Gefügeuntersuchungen.
Literatur:
[1] Oldendorf, U.: Lastübertragungsmechanismen und Dauerhaltbarkeit von Passfederverbindungen. Dissertation, TH Darmstadt, 1999
[2] Forbrig, F.: Untersuchungen zur Gestaltfestigkeit von Pressverbindungen. Dissertation, TU Chemnitz, 2006
[3] Bruzek, B.; Leidich, E.: Dauerfeste Dimensionierung von Passfederverbindungen. VDI-Fachtagung Welle-Nabe-Verbindungen, VDI-Berichte 2176, 2012
[4] DIN 743: Tragfähigkeitsberechnungen von Wellen und Achsen. Beuth Verlag, Berlin, 2012
[5] Hofmann, S.; Leidich, E.; Podlesak, H.; Wielage, B.: Dauergestaltfestigkeitsuntersuchung an einsatzgehärteten Passfederverbindungen. FVA-Abschlussbericht, Heft 1146, 2015
[6] Leidich, E.; Bruzek, B.: Dauergestaltfestigkeitsuntersuchungen an einsatzgehärteten Passfederverbindungen. FVA-Abschlussbericht, Heft 926, 2010
[7] DIN 6885: Passfedern – Nuten. Beuth Verlag, Berlin, 1968
[8] DIN EN ISO 6892–1: Metallische Werkstoffe-Zugversuche Teil1: Prüfverfahren bei Raumtemperatur, 2009
[9] Leidich, E.; Bruzek, B.; Hofmann, S.: Gestaltfestigkeit von Pressverbindungen II. FKM-Abschlussbericht, Heft 320, 2013
[10] DIN 509, Freistiche. Beuth Verlag, Berlin, 2006
[11] Hück, M.: Ein verbessertes Verfahren für die Auswertung von Treppenstufenversuchen. Zeitschrift Materialwissenschaft und Werkstofftechnik, 14 (1983), S. 406–417
[12] FKM-Richtlinie: Rechnerischer Festigkeitsnachweis für Maschinenbauteile. VDMA Verlag, 6. Ausgabe, 2012
AutorenProf. Dr.-Ing. Erhard Leidich InstitutsleiterStefan Hofmann Wissenschaftlicher Mitarbeiterbeide: TU Chemnitz Fakultät für Maschinenbau Institut für Konstruktions- und Antriebstechnik 09107 Chemnitz Tel.: 03 71/5 31-2 33 10 Fax: 03 71/5 31-2 33 19 E-Mail: e.leidich@mb.tu-chemnitz.de