Antriebe für die Automation an der Presse
Wenn man den FeederPlus 6neo von Strothmann Machines & Handling in Aktion sieht, weiß man, was Präzision bedeutet. Bis zu 16 umgeformte Bleche für Fahrzeugkarossen – jedes bis zu 60 kg schwer – werden von diesem Verkettungssystem pro Minute millimetergenau und zugleich hochdynamisch von einer Presse zur nächsten transportiert. Ermöglicht wird diese Performance durch Getriebe, Servoaktuatoren und Ritzel-Zahnstangen-Systeme von Wittenstein alpha. Aufgrund ihrer Leistungsdichte meistern sie auch hohe Antriebsleistungen und Lagerkräfte bei gleichzeitig kompakter Baugröße.
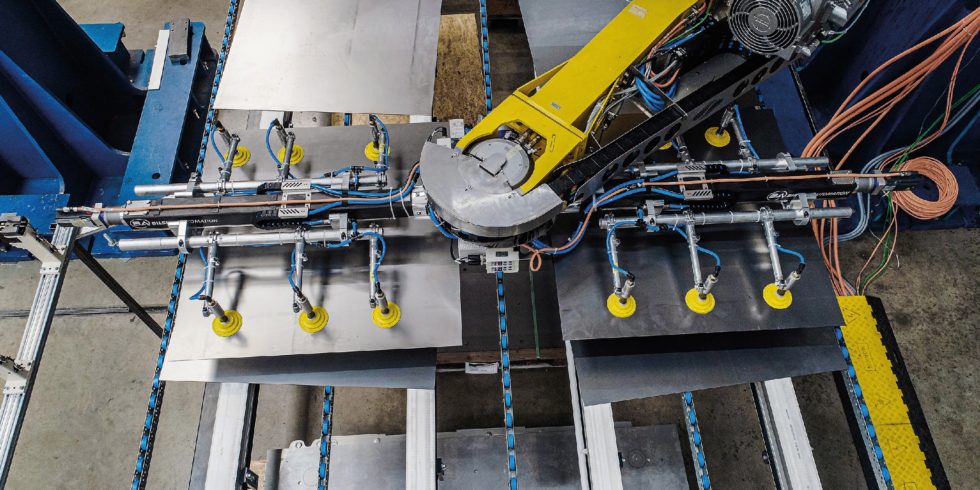
Der FeederPlus 6neo transportiert pro Minute bis zu 16 umgeformte Bleche für Fahrzeugkarossen von einer Presse zur nächsten. Bild: Strothmann Machines & Handling
Die erste Generation des Single-Arm-Verkettungssystems, der „FeederPlus6“, hat sich über mehr als zehn Jahre zur Automatisierung von Pressenlinien vornehmlich in der Automobilindustrie etabliert.
„Damals wie heute verbauen wir in unseren Anlagen nur Komponenten von Qualitätsanbietern“, sagt Andreas Senge. Er ist bei der Strothmann Machines & Handling GmbH in Schloss Holte-Stukenbrock als Leiter der Produktgruppe Pressenautomation und Handlingssysteme zuständig für die Konstruktion und Entwicklung von Automatisierungslösungen.

Andreas Senge, Leiter Produktgruppe Pressenautomation und Handlingsysteme bei Strothmann: „In Wittenstein aber nur einen Komponentenlieferanten zu sehen, würde unserer langjährigen, vertrauensvollen Zusammenarbeit nicht gerecht werden.“ (Bild: Wittenstein)
„Wenn diese Hersteller dann wie Wittenstein ein Portfolio bieten, mit dem wir die Anforderungen der verschiedenen Maschinenachsen vollständig abbilden können, ist das natürlich optimal. Die Antriebsauslegung kann schnell und komfortabel mit dem Auslegungstool cymex 5 erfolgen. Auch die Konstruktion, die Montage, die Inbetriebnahme und der Service werden wesentlich erleichtert.“ Folgerichtig ist Wittenstein auch im neuen FeederPlus 6neo in allen Achsen vertreten: mit kompakten und spielarmen Planetengetrieben, mit dauerfesten, spanlos und schnell montierbaren Zahnstangen, mit Planetengetrieben in High-Torque-Ausführung, mit extrem verdrehsteifen, maximal kompakten und spielfreien Galaxie-DF-Getrieben, mit Kegelradgetrieben sowie mit Servoaktuatoren – alles aus einer Hand.
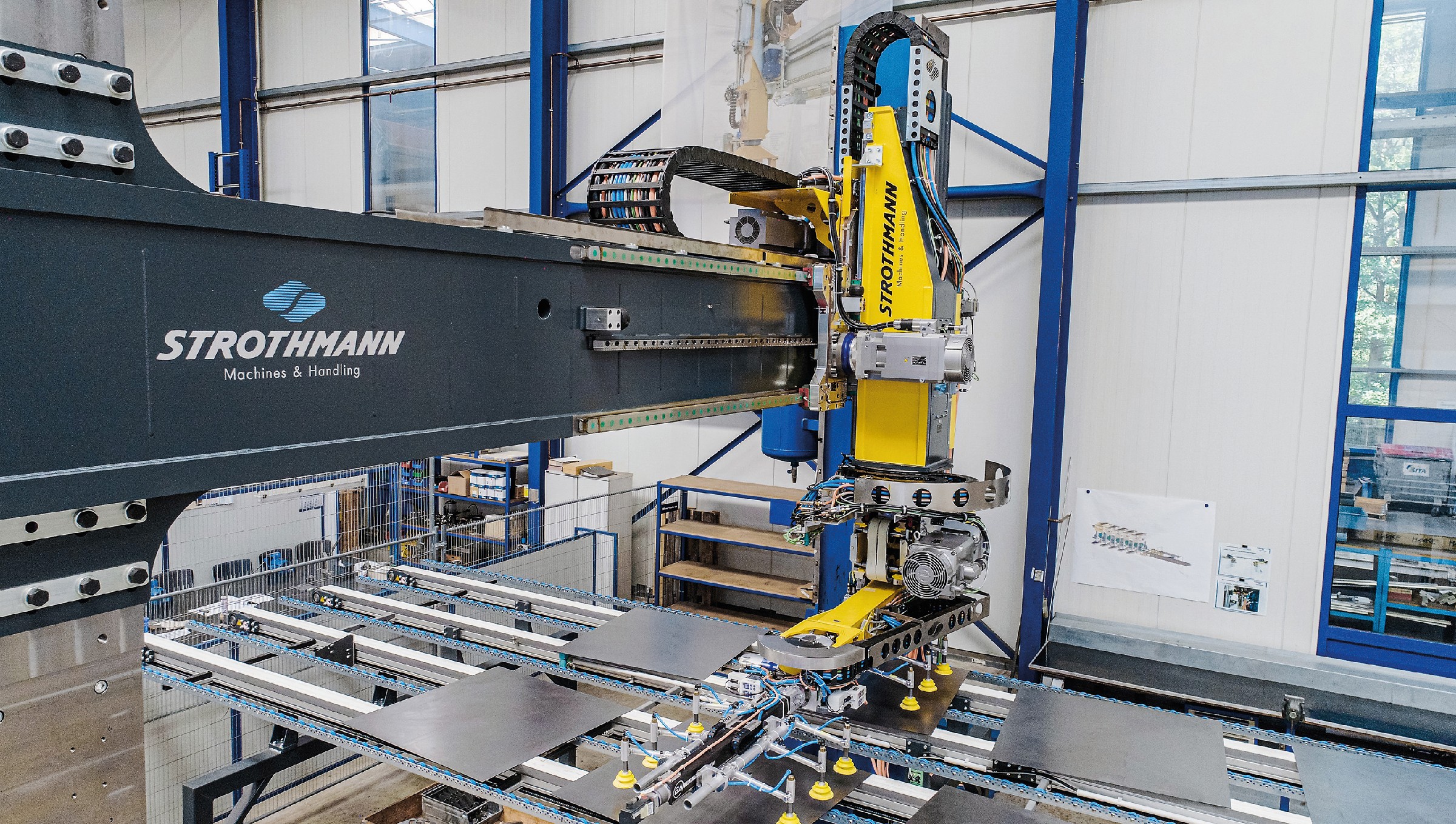
Antriebstechnik von Wittenstein kommt in allen Achsen des FeederPlus 6neo zum Einsatz. (Bild: Strothmann Machines & Handling)
„In Wittenstein aber nur einen Komponentenlieferanten zu sehen, würde unserer langjährigen, vertrauensvollen Zusammenarbeit nicht gerecht werden“, erklärt Senge und betont die fachkundige Unterstützung beim Projektieren und Auslegen von antriebstechnischen Lösungen, wie sie auch im FeederPlus 6neo umgesetzt sind.
Transport der Bleche im Pressenbetrieb
Der FeederPlus 6neo wird in einer Pressenlinie zur Verkettung von zwei Pressen eingesetzt – je länger die Linie und je mehr Pressen zum Umformen von Blechteilen erforderlich sind, desto mehr Verkettungssysteme werden eingesetzt. Der Single-Arm-Feeder entnimmt ein geformtes Teil aus einer Presse und legt es für den folgenden Bearbeitungsschritt in die nächste Presse ein. „Die Pressen laufen dabei kontinuierlich weiter, während die Bewegungen des FeederPlus 6neo Bahnkurven folgen, die mit den Pressen synchronisiert sind“, beschreibt Senge die Dynamik der Bauteilhandhabung.
Der prozesskritische und zugleich antriebsrelevante Aspekt dabei: die Achsen des Feeders und die Werkzeuge der Presse kommen sich in bestimmten Momenten bis auf wenige Zentimeter nah. „Dies erfordert je nach Achse spielarme oder sogar spielfreie Getriebe mit höchstmöglicher Verdreh- und Kippsteifigkeit, um Kollisionen durch Schwingungen oder Ungenauigkeiten in der Führung und Positionierung zu vermeiden“, bringt es Senge auf den Punkt. Diese Anforderungen durften jedoch nicht zu Lasten der Dynamik gehen, denn der FeederPlus 6neo wurde vor allem entwickelt, um die Ausbringungsleistung von vormals 12 auf jetzt bis zu 16 Teile in der Minute zu steigern.
Die komplexe Kinematik sowie die besonderen Anforderungen an Dynamik und Präzision der antriebstechnischen Komponenten hat Strothmann im frühen Stadium des Entwicklungsprojektes durch Mehrkörpersimulationen analysiert. Verifiziert und optimiert wurden die ermittelten Kraft- und Momentenverläufe sowie die ersten Vorauslegungen von Strothmann durch den Import der Daten in das Auslegungstool cymex 5 von Wittenstein. Die detaillierten Ergebnisse der Mehrkörpersimulation haben eine tiefgreifende und durchgängige Systembetrachtung ermöglicht. „Hierbei wurde nicht nur unsere Berechnung geprüft und validiert, sondern auch grundsätzliche Getriebealternativen hinsichtlich Performance, Bauraum und Kosten bewertet“, blickt Senge zurück. Für jede Getriebeapplikation konnten die Auslegungsgrenzen präzise ausgelotet, gemeinsam das passende Getriebe identifiziert und angemessene Sicherheitsreserven bei der Getriebeauslegung festgelegt werden. „Auch in diesem Projekt konnten wir uns wieder auf die technischen Daten der Getriebe sowie den Support und die Engineering-Kompetenz unseres Partners verlassen.“
Extrem hohe Anforderung an die Achsensteifigkeit
Die Rotationsachsen für den teleskopierbaren Schwenkarm (C1-Achse) und die Bauteilaufnahme (C2-Achse) standen bei der Auslegung besonders im Fokus. Extrem hohe Anforderungen an die Steifigkeit stellte die C1-Achse. Die Herausforderung bestand darin, den Schwenkarm des Feeders ohne eine zusätzliche Lagerung direkt an dem C1-Getriebe zu befestigen. Dies stellte aufgrund des großen Hebelarms und der damit verbundenen Kippmomente besonders hohe Anforderungen an die Getriebelagerung. „Das ausgewählte TP+2000 High Torque von Wittenstein alpha ist eines der wenigen überhaupt am Markt verfügbaren Servogetriebe, die die geforderten Kippmomente aufnehmen können“, erläutert Andreas Senge. Die C2-Achse benötigte eine Getriebelösung mit integriertem Motor, die möglichst flach baut, da dieser Teil des Feeders in den Pressenraum eintaucht. Gleichzeitig sind für das Drehen und Ablegen von Fertigteilen auf Förderbänder am End of Line – eine der noch zu beschreibenden Funktionserweiterungen des FeederPlus 6neo – hohe Drehmomente erforderlich.

Das Antriebssystem Galaxie-DF – das „F“ steht für flat, flach – und spart im Vergleich zum Galaxie-D bis zu 30 % Baulänge ein. (Bild: Wittenstein)
„Das Antriebssystem Galaxie DF110, das wir hier einsetzen, bietet eine so hohe Drehsteifigkeit und Drehmomentdichte auf so kleinem Bauraum, wie sie von keiner anderen Motor-Getriebe-Einheit erreicht werden“, führt Senge aus.
Keine bauteilspezifischen Werkzeuge erforderlich
Über die verkettungstechnische Grundfunktionalität des FeederPlus 6neo hinaus erlaubten es die spielarmen, drehsteifen und hochdynamischen Antriebskomponenten von Wittenstein alpha, den Feeder mit Funktionserweiterungen für den Front-of-Line- und den End-of-Line-Bereich der Pressen auszustatten. „Der FeederPlus 6neo kann jetzt sowohl Platinen mit Positionsabweichungen von der Fördertechnik aufnehmen, diese prozessgerecht zentrieren und in die erste Presse einlegen, als auch Fertigteile aus der letzten Presse entnehmen und ergonomisch vorteilhaft um 90° gedreht auf anschließende Förderbänder verteilen“, erklärt Senge. Diese Funktionserweiterungen, die auch durch die Dynamik und Präzision der Antriebstechnik möglich wurden, sparen dem Kunden mehr als eine Millionen Euro pro Pressenlinie ein. „Möglich ist dies“ erklärt Senge, „weil sowohl am Anfang als auch am Ende der Pressenlinie keine Roboter- und Shuttlesysteme mehr erforderlich sind. Dadurch entfallen zudem bauteilespezifische Greifwerkzeuge und Tooling-Wechselsysteme. Durch die Einsparungen im FoL und EoL wird die Linie insgesamt kürzer, wodurch auch Stahlbau und Schallschutz kürzer und damit günstiger werden. Zu diesen direkten Kosteneinsparungen kommen indirekte hinzu, beispielsweise für Rüstzeiten, für Aufstell- und Lagerflächen oder auch für Wartung und Instandhaltung.“
Im Herbst 2019 hat Strothmann, nach etwa zwei Jahren Weiterentwicklung, den Prototypen des FeederPlus 6neo erstmals auf einer Hausmesse präsentiert. Produktentwicklung und Testphasen sind erfolgreich abgeschlossen – die ersten Feeder der neuen Generation wurden Anfang 2020 ausgeliefert und werden in Kürze in der Pressenlinie eines namhaften Automobilwerkes in Betrieb gehen. Der Fahrzeughersteller kann sich schon jetzt auf „Innovation in Motion“ (Leitspruch von Strothmann) freuen. Und aufgrund der globalen Präsenz auf Wittenstein als ortsnahen Servicepartner für die Antriebstechnik des FeederPlus 6neo vertrauen.
Peter Hempsch
ist Regionalvertriebsleiter bei der Wittenstein alpha GmbH, Technisches Büro Nord-Ost, Bad Pyrmont.
Andreas Grages
ist Applikationsberater bei der Wittenstein alpha GmbH, Technische Büro Nord-Ost, Bad Pyrmont.
Kontakt:
Wittenstein alpha GmbH,
97999 Igersheim,
Tel. (0 79 31) 493 - 0,
info@wittenstein-alpha.de,
www.wittenstein-alpha.de