Von A wie Antrieb bis Z wie Zelle: Batterieproduktion in Deutschland entlang der gesamten Wertschöpfungskette
In der Energiewende spielt Strom eine entscheidende Rolle. Egal ob E-Mobility oder mobile technische Gadgets, der Bedarf nach stromspeichernden Medien ist immens. Um der Abhängigkeit vom asiatischen Markt entgegenzutreten und zeitgleich als Innovationsstandort nicht den Anschluss zu verlieren, planen immer mehr Hersteller auch in Deutschland zu produzieren. Damit die Batterieproduktion „Made in Germany“ gelingen wird, muss von der Grundlagenforschung über die Produktion bis hin zum Recycling ganzheitlich gedacht werden. Digitale Lösungen unterstützen Hersteller dabei.
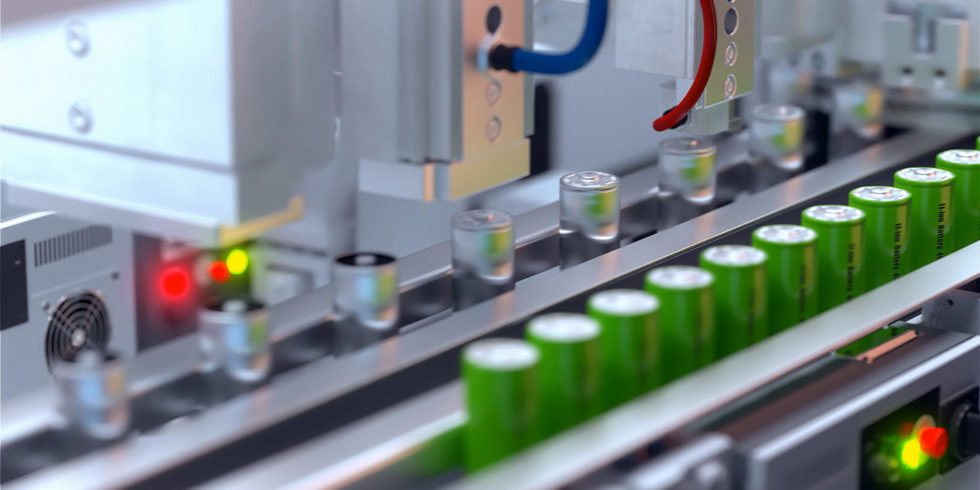
Foto: Dassault Systèmes
Wachstumsmarkt Strom
Mit dem Verzicht von fossilen Brennstoffen und immer mehr elektronischen Devices steigt auch hierzulande der Bedarf nach Strom und entsprechenden Speichermedien. Steigende Energiepreise beschleunigen diese Entwicklung zusätzlich. Gerade im Bereich der Mobilität wird zukünftig kein Weg mehr an E-Autos vorbeiführen. Dies schlägt sich direkt in der Bedeutung von Batterien für die heimische Industrie nieder: Allein im Jahr 2020 wuchs der Markt für Batterien um 35 Prozent auf 5,9 Milliarden Euro an, so der Verband der Elektro- und Digitalindustrie (ZVEI). Doch der hohe Qualitätsanspruch sowie knappe Verfügbarkeiten von Batterien auf dem Weltmarkt führen dazu, dass OEMs die Nachfrage nicht bedienen können.
Die Batterie „Made in Germany“
Um diesem Trend entgegenzuwirken hat in der deutschen Industrie ein Umdenken stattgefunden. Statt sich komplett auf die Lieferung von Batterien aus dem Ausland zu verlassen, wird heute mehr und mehr an der Entwicklung und Produktion in Deutschland gearbeitet. Entscheidend wird dabei sein, in wie weit die gesamte Wertschöpfungskette bedacht wird. Denn zur lieferfähigen Batterie gibt es zahlreiche Einzelschritte, die es zu erfüllen gilt: von der Grundlagenentwicklung in der Forschung, über Prozessoptimierungen und Skalierung der Produktion bis hin zur Logistikplanung.
Die Dynamik des Marktes beherrschen
Kaum ein Markt verändert sich momentan so rasant wie die Batterieindustrie. Zum einen werden in immer kürzeren Abständen neue Möglichkeiten entwickelt, Batterien langlebiger und leistungsstärker zu machen. Zum anderen spielt der benötigte Ressourcenverbrauch eine wichtige Rolle, in wie weit eine Herstellung lohnend ist. Denn vor allem in den erreichten Stückzahlen steckt der Wettbewerbsvorteil, den asiatische Anbieter in den vergangenen Jahren zu nutzen wussten. Diese Entwicklungsschritte sind hochdynamisch und bewirken, dass Prozesse kontinuierlich angepasst werden müssen, um Schritt zu halten.
Vom Piloten bis zur Giga Factory
Die Produktionskapazitäten von Batterien stecken im internationalen Vergleich noch in den Kinderschuhen. Viele Hersteller haben in den vergangenen Monaten Pilotproduktionsstandorte aufgesetzt. Diese dienen dazu, Prozesse einzuführen, die im nächsten Schritt das gezielte Hochfahren der Herstellung ermöglichen. In der Batterieproduktion sind dabei viele Parteien involviert: Das Engineering kümmert sich um die Entwicklung passender Batteriezellen. Fertigungsplaner müssen die Herstellungsprozesse entwickeln. Layout-Planer sind für den Aufbau der Produktionsstandorte verantwortlich. Und letztlich spielt auch die Logistikplanung bei der Beschaffung der benötigten Produktionsmittel eine große Rolle.
Diese Komponenten sind bei der Produktion von Batterien im großen Maße voneinander abhängig und bedingen sich gegenseitig. Entsprechend wichtig ist es, dass alle Beteiligten auf eine gemeinsame „Single Source of Truth“ – sprich eine gemeinsame Datenbasis – zurückgreifen können. Bei der Entwicklung von Prozessen im Pilotwerk wird es daher darauf ankommen, in wie weit ein durchgängiges Core-Modell erreicht wird. Neue Technologien können dort in verbesserte Produktionsprozesse übersetzt und getestet werden, bevor sie im nächsten Schritt in skalierter Form in der Giga Factory zum Einsatz kommen. Erst dann lassen sich Herstellungskapazitäten erreichen, die eine wirtschaftliche Produktion garantieren.
Qualitätsstandards setzen
Ein weiterer erfolgsentscheidender Faktor ist die Qualität der Batteriezellen und der hierfür notwendige stabile Produktionsverlauf an sich. „Made in Germany“ steht weltweit für besonders hohe Qualitätssicherheit, die auch in der Batterieproduktion von Bedeutung ist und somit Produzenten aus Deutschland eine Chance bietet.
Der hohe Qualitätsanspruch fängt bei der Entwicklung der benötigten Batteriezellen an. Selbst kleinste Anomalien oder fehlerhafte Zellen beeinflussen den Lebenszyklus entscheidend. Ist eine Zelle einmal mangelhaft produziert, entsteht ein Dominoeffekt: Ein höherer Innenwiderstand durch eine defekte Zelle beim Stromdurchfluss erwärmt die Batterie und zerstört dabei weitere Zellen. Dieser Effekt potenziert sich, bis schlussendlich die Batterie nicht mehr nutzbar ist.
Doch auch die Qualität der Herstellungsprozesse werden für den Erfolg der Batterien aus deutscher Produktion entscheidend sein. Ausländische Hersteller kämpfen häufig mit hohen Ausschussraten. Auf Grund mangelhafter Fertigungsprozesse kann ein bedeutender Anteil der produzierten Batterien nicht genutzt werden. Die damit verbundenen Kosten schlagen sich direkt in der Wirtschaftlichkeit der Herstellung nieder. Produzenten in Deutschland werden aus diesem Grund besonderes Augenmerk auf einen qualitativ hochwertigen Herstellungsprozess legen müssen, um im internationalen Vergleich bestehen zu können.
Mit digitalen Tools zum Erfolg
All diese Anforderungen zu erfüllen, kann für Batterieproduzenten eine enorme Hürde darstellen. Eine enge Abstimmung mit relevanten Fachexperten – und das sind nicht wenige – ist beispielsweise unverzichtbar. Wie können also Batterien, die den Qualitätskriterien und dem Gütesiegel “Made in Germany“ entsprechen, hergestellt werden? Die entscheidende Entwicklungsgrundlage – und zugleich Entwicklungsfortschritt – kann mit Hilfe digitaler Lösungen geschaffen werden, die für Vernetzung und Wissenstransfer sorgen, wo sonst durch mangelhaften Austausch Wissens- und Datensilos entstehen und Potenzial ungenutzt bleibt. Dassault Systèmes bietet Software Tools entlang der gesamten Wertschöpfungskette – wovon Forschung & Entwicklung, über Konstruktion und Fertigung hinzu Ablauf- und Logistikplanung maßgeblich profitieren.
Die Basis bildet eine gemeinsame, durchgängige Datenplattform wie die 3DEXPERIENCE Plattform. Dort sind alle relevanten Informationen entlang der Wertschöpfungskette hinterlegt und für alle Beteiligten jederzeit greifbar. Dies vereinfacht den Zugang zu benötigten Daten an allen Stellen des Prozesses und lässt Aus- und Wechselwirkungen bei Veränderungen frühzeitig erkennen. Die dabei gewonnene Flexibilität ist eine der wichtigsten Faktoren, um eine skalierbare Produktionsplanung und -vorbereitung zu entwickeln.
Ein zweites wichtiges Hilfsmittel ist die Nutzung von virtuellen Zwillingen. Diese können etwa in der Forschung und Entwicklung zum Einsatz kommen, wenn es darum geht, in kürzester Zeit neue und verbesserte Batteriezellen zu entwickeln. Die digitale Simulation ermöglich genauere Einblicke in die Zellabläufe und reduziert damit physisches Prototyping. Aus der Produktion und Qualitätssicherung können beispielsweise Daten wie Trockenzeiten und -temperaturen sowie konkrete Informationen der einzelnen Fertigungsschritte wie beispielsweise die Mischzeit zweier Stoffe erfasst werden, die direkt in den virtuellen Zwilling einfließen. Das Monitoring der Batterie kann aber auch im Einsatz beim Verbraucher fortgeführt werden, gegebenenfalls bis hin zum Ausfall der Zelle. So werden Daten während der Nutzung erhoben, die via Cloud zur Verfügung stehen und wichtige Anhaltspunkte hinsichtlich Verschleißfortschritt liefern. Was nicht beobachtet werden kann, wird aus den Messdaten simuliert. Aus der Gesamtheit der Daten lassen sich langfristig verschiedenste Zusammenhänge im Leben einer Batterie feststellen und so die Produktion optimieren bzw. die Qualität weiter verbessern. Eine Datenplattform wie die 3DEXPERIENCE Plattform kann mit ihren Möglichkeiten entlang der Wertschöpfungskette letztlich dem Produktions- und Qualitätsniveau zum entscheidenden Fortschritt verhelfen. Aber auch in der Logistikplanung spielen virtuelle Zwillinge heute eine immer größere Rolle. Transparente Lieferketten können am Computer simuliert und optimiert werden, um den weiten Zeithorizont von Liefer- und Absatzaussichten besser zu planen.
Sind wir schon so weit?
Die Batterieproduktion in Deutschland nimmt heute richtig Fahrt auf. Der Industrie- und Wissensstandort Deutschland erfindet sich gerade neu und kann zukünftig als Hersteller von Batterien ein wichtiger Player auf dem internationalen Markt sein. Entscheidend wird sein, ob es auch gelingt, in relativ kurzer Zeit die benötigten Kapazitäten und die gewünschten Qualitätsstandards zu schaffen. Digitale Lösungen unterstützen Unternehmen dabei, Innovationen der Zukunft zu entwickeln und umzusetzen. Und darauf wird es auch letztlich ankommen: den Pioniergeist deutscher Unternehmen zu unterstützen, um auch morgen als attraktiver Industriepartner auf dem Weltmarkt auftreten zu können.