Innovative Lasermikrobearbeitung bewährt sich in der Sensor-Fertigung
In einer Sensor-Fabrik im kalifornischen Santa Clara kommt seit Kurzem moderne Anlagentechnik aus Chemnitz zum Einsatz: Ein selektives Laser-Annealing-System erzielt dort beste Resultate hinsichtlich Durchsatz und Präzision in der Fertigung von Magnet-Sensoren.
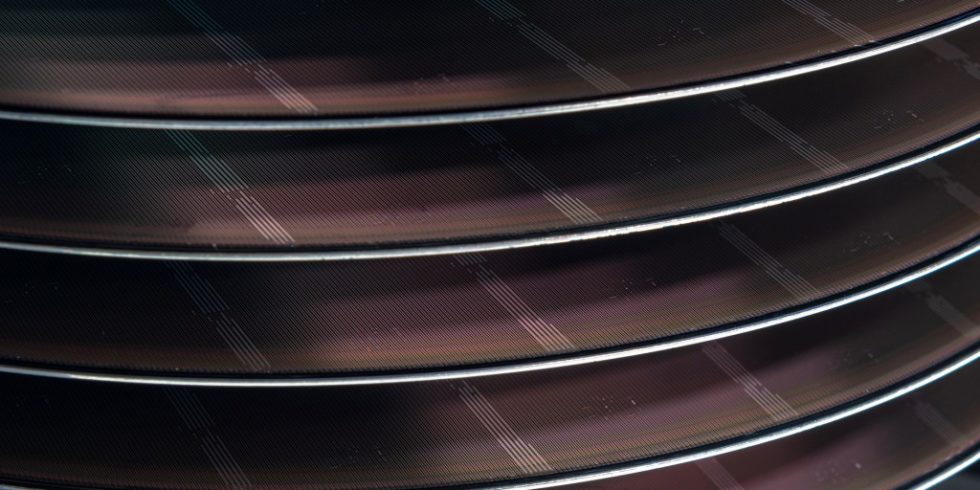
Monolithisch integrierte Sensorchips lassen sich mit neuartiger Anlagentechnik jetzt in nur einem Produktionsschritt kosteneffizient fertigen.
Foto: 3D-Micromac
Wafer, die für Sensoren wichtige Komponenten darstellen, sind aus der Mikroelektronik, Photovoltaik oder Mikrosystemtechnik nicht mehr wegzudenken. Die etwa einen Millimeter dünnen Scheiben werden aus Halbleiter-Rohlingen gefertigt und zumeist mit dem Laser in Form geschnitten. Ein Wafer dient als Grundplatte für elektronische Bauelemente oder für photoelektrische Beschichtungen.
Bei der „Dotierung“ werden geladene Ionen in einem elektrischen Feld beschleunigt und auf die Wafer gelenkt, um die elektrischen Eigenschaften zu beeinflussen. Für die Tiefenaktivierung sorgt dabei inzwischen häufig das Verfahren „Laser Annealing“, das gegenüber herkömmlichen Verfahren wie dem Ofenprozess Vorteile bietet. Die Wärmebelastung ist nur gering und die Tiefenaktivierung gleichmäßig.
Breite Einsatzmöglichkeiten für TMR- und GMR-Sensoren
Mit der neuen Anlage aus Chemnitz lassen sich sowohl GMR (Giant Magneto-Resistance)- als auch TMR (Tunnel Magneto-Resistance)-Magnetfeldsensoren bearbeiten. Beide Sensorenarten haben spezifische Besonderheiten und Vorteile: Der GMR-Effekt ist ein magnetoresistiver Effekt, bei dem sich der Widerstandswert eines metallischen Dünnschichtsystems in Abhängigkeit von der magnetischen Feldstärke ändert. Dabei wird der der Elektronen-Spin-Effekt in einem ultradünnen Schichtsystem ausgenutzt, der die Leitungsmechanismen verändert. Beim TMR-Mechanismus wird ein Tunnel-Effekt genutzt, der auf der Quantenphysik basiert. Dieser Effekt tritt in Schichtensystemen mit mindestens zwei ferromagnetischen Schichten sowie einer dazwischen liegenden Isolationsschicht auf. Diese ändert mit der Ausrichtung des Magnetfelds den Widerstandswert. Der Vorteil dieser Technik liegt in der extrem kleinen Bauweise: TMR-Sensoren haben Kantenlängen, die im Mikrometerbereich liegen.
Die vielseitige Anlage zur Bearbeitung beider Sensortypen stammt vom sächsischen Spezialisten 3D-Micromac, einem international führenden Anbieter für Systeme in der Lasermikrobearbeitung und der Rolle-zu-Rolle-Laserbearbeitung. Das neue Produktionssystem gewährleistet eine kosteneffiziente Fertigung monolithisch integrierter Sensorchips in nur einem Produktionsschritt.
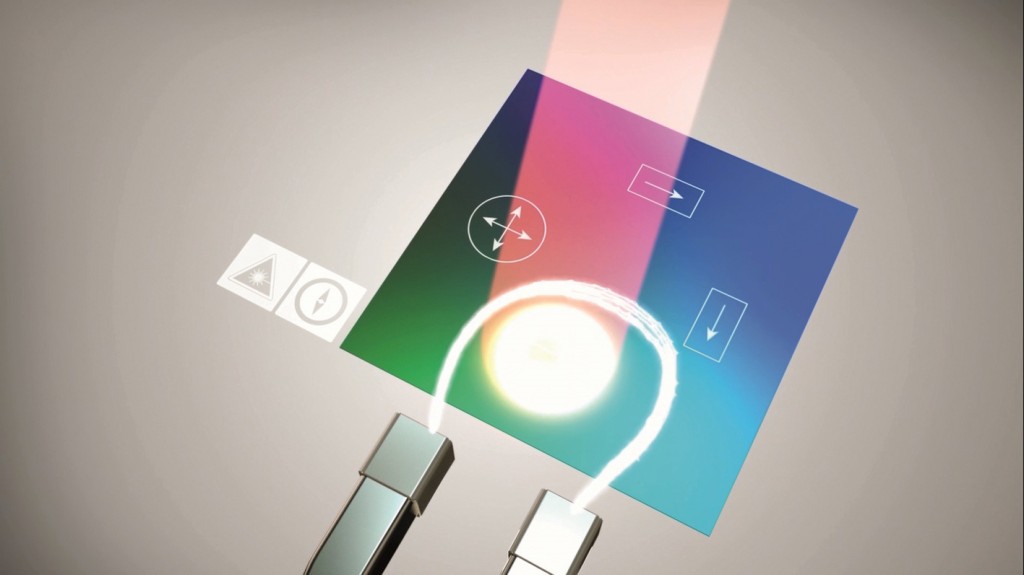
Prozessbild des „xMR“-Verfahrens: Viele Besonderheiten machen das Laser-Pinning-System aus Chemnitz zu einem idealen Werkzeug für die Magnet-Sensor-Bearbeitung.
Foto: 3D-Micromac
Verarbeitung noch kleinerer Strukturen bei hoher Qualität
Bei der Bearbeitung wird ein „On-the-Fly-Laserspot“ genutzt, der sich in Geometrie und Pulsenergie flexibel an diverse Magnetsensoren anpassen lässt. Für die Adaption an verschiedene Sensor-Positionen und Abmessungen sowie Magnetfeldorientierungen ist lediglich die Änderung von „Rezepten“ notwendig. All dies macht das Laser-Pinning-System zu einem gut geeigneten Werkzeug für die Magnet-Sensor-Bearbeitung. Bei Crocus Technology, einem führenden Hersteller von TMR-Sensoren, ist ein microVega xMR-System bereits erfolgreich im Einsatz. Das Unternehmen konnte damit die Produktivität in seiner Fertigung bereits signifikant steigern.
Gegenüber herkömmlichen Annealing-Verfahren in der Magnet-Sensor-Produktion zeichnet sich die in der neuen Anlage genutzte Technologie unter anderem durch eine höhere Präzision aus und erlaubt so die Verarbeitung von kleineren Strukturen. Die besonders gute Selektivität des Kurzpuls-Lasers gestattet eine deutliche Verringerung der Abstände zwischen den Sensoren und zur Auswerteelektronik. Die Anzahl der Bauelemente je Wafer lässt sich dadurch signifikant erhöhen. Hervorzuheben sind zudem die Energie-Homogenität und die Wiederholgenauigkeit. Bei der Ausrichtung der Magnetfeldrichtung beträgt die Präzision ±0,010°. Dies ist ein weiteres wichtiges Kriterium für die Herstellung sensitiver Sensoren.
Auch die Herstellungskosten lassen sich senken
Mit der neuartigen Anlagentechnik können auf einem einzigen Sensorchip unterschiedliche Referenzmagnetfeld-Richtungen realisiert werden („Pinning Prozess“) – und dies in einem einzigen Fertigungsschritt. Dies ist ein besonders wichtiger Vorteil: Denn der magnetoresistive Effekt wird bei GMR- und TMR-Sensoren durch das gezielte Ausrichten magnetischer Schichten erreicht. Bisher war dazu ein globales Magnetfeld bei gleichzeitiger Erwärmung des gesamten Wafers vonnöten. Dieser Ansatz erfordert jedoch eine aufwendige Prozesskette bis zum fertigen Sensor in einem „Multi-Chip-Package“.
Durch das jetzt mögliche selektive Erwärmen mit dem Laserspot werden im Sub-ms-Takt die Sensoren im monolithischen Chip-Package ausgerichtet. Das neue Annealing-Verfahren ist besonders selektiv und schnell. Bis zu 500.000 Sensoren in der Stunde können bei einem typischen Wafer Design bearbeitet werden. Alle System-Parameter wie Puls-Energie, Sensor-Dimensionen, Abstand zwischen den Sensoren und magnetische Feldstärke lassen sich rein rezeptbasiert einstellen. Entwickler von Sensoren erhalten damit eine viel größere Design-Freiheit.
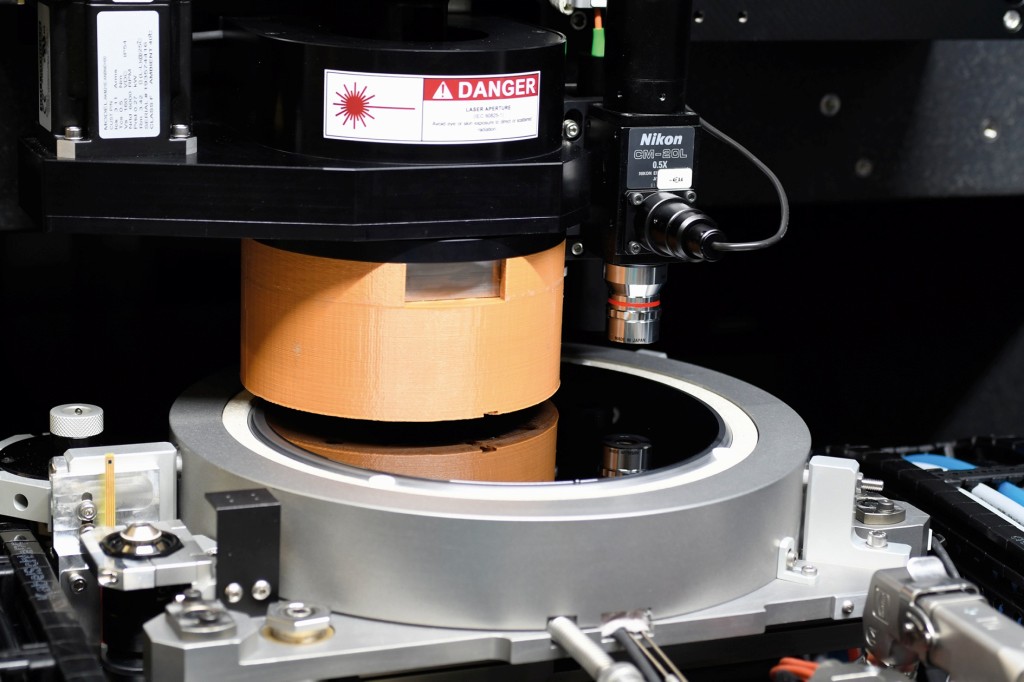
Blick in den Bearbeitungsraum des industriellen Produktionssystems „microVega xMR“ , das selektives Laser-Annealing in der Magnet-Sensor-Fertigung erlaubt.
Foto: 3D-Micromac
Flexibler Einsatz in der kalifornischen Fabrik
Die in der TMR-Sensor-Fabrik von Crocus Technology im kalifornischen Santa Clara gefertigten Sensoren kommen unter anderem in IoT (Internet of Things)-Anwendungen zum Einsatz. Ein Aushängeschild des Unternehmens ist die patentierte „XtremeSense“-TMR-Sensor-Technologie: Sie bringt signifikante Verbesserungen für alle Applikationen mit sich, bei denen hohe Genauigkeiten und Auflösungen sowie stabile Temperatur-Eigenschaften und ein geringer elektrischer Verbrauch gefragt sind. Dazu zählen neben IoT-Applikationen und Smart-Devices auch Industrieanwendungen, Konsumgüterelektronik, Medizintechnik sowie Elektroanwendungen im Automotive-Umfeld.
Die Verantwortlichen bei Crocus sind mit der neuen Anlage sehr zufrieden. Zack Deiri, Vorstand und CEO, sagt beispielsweise: „Mit der microVega xMR haben wir eine flexible und trotzdem stabile Technik für die Fertigung von integrierten Magnet-Sensoren erhalten. Das Laser-Annealing-System erlaubt es uns, neue Sensor-Designs zu implementieren, unsere Produktionskosten zu senken und auch den Durchsatz zu erhöhen. Von Anfang an haben die Experten von 3D-Micromac ihre Expertise vorteilhaft in die Prozessentwicklung mit eingebracht. Dank der Lohnfertigung, die bei dem Anbieter möglich ist, konnten wir schon im Vorfeld der Maschinenauslieferung unsere Produktion anlaufen lassen. Wir freuen uns auf die Zusammenarbeit bei zukünftigen Technologieentwicklungen.“
Neue Perspektiven auf dem Magnet-Sensor-Markt erschließen
„Wir sind stolz, dass sich ein so renommierter Hersteller wie Crocus Technology für unser neues System entschieden hat“, äußert Tino Petsch, CEO von 3D-Micromac. „Mit der von uns entwickelten innovativen Anlagentechnik adressieren wir einen Markt mit hohem Wachstumspotenzial.“ Die Verantwortlichen in Chemnitz sind zuversichtlich, dass sie sich mit ihren innovativen Maschinen, der Prozess-Expertise und den Erfahrungen bei Applikationsdienstleistungen auf zukunftsorientierten Märkten platzieren können.
Im unternehmenseigenen Applikationslabor werden die an den Kundenbedürfnissen ausgerichteten technologischen Lösungen entwickelt – von der ersten Idee über Machbarkeitsstudien sowie Prototypenentwicklung bis hin zur Serienreife. Die Systeme kommen weltweit in vielen Hightech-Branchen zum Einsatz, etwa in der Photovoltaik-, Halbleiter-, Glas- und Display-Industrie, in der Mikrodiagnostik und in der Medizintechnik. Als eines der ersten Unternehmen weltweit haben die Chemnitzer Ultrakurzpulslaser zur Materialbearbeitung eingesetzt. Ein weiterer Anwendungsschwerpunkt sind Excimerlaser für die Mikrobearbeitung – mehr als 100 Systeme dieser Art von 3D-Micromac sind bereits im industriellen Einsatz. 2002 gegründet, beschäftigt das Unternehmen heute über 170 Mitarbeiter und hat je ein Tochterunternehmen in China, Taiwan und den USA.
Ausblick auf die Marktentwicklung
Die Nachfrage nach Magnet-Sensoren steigt stetig. In der Unterhaltungselektronik werden sie zum Beispiel als elektronische Kompasse in Smartphones und Wearables eingesetzt. Magnet-Sensoren für die Rotation werden als Winkelsensoren bei bürstenlosen Gleichstrommotoren (BLDC) verbaut. Ein innovatives Anwendungsgebiet dafür ist zudem die Automobilindustrie: Dort werden sie als Lenkwinkelsensoren oder bei elektronischen Gaspedalen genutzt.
Das könnte Sie auch interessieren:
Birgit Etmanski, Dr.-Ing., ist Chefredakteurin der VDI-Z. Mandy Gebhardt ist Teamleiterin Marketing und Öffentlichkeitsarbeit bei 3D-Micromac.